Химикаты из древесиныОбщая схема производства бумаги и приготовление бумажной массы
Технологическая схема производства бумаги (картона) состоит из следующих процессов: приготовления бумажной массы, включающего операции по массному размолу волокон, проклейке, наполнению и крашению массы; аккумулирования бумажной массы; разбавления массы водой до необходимой концентрации; очистки от посторонних включений и узелков; изготовления бумаги (картона) на бумагоделательной (картоноделательной) машине, включающего отлив бумажного (картонного) листа, его прессование, сушку, отделку и намотку в рулон; отделки и переработки бумаги (картона), включающих суперкаландрирование, перемотку, резку и упаковку [1].
Массный размол волокнистых полуфабрикатов. Размолом называется процесс специальной механической обработки растительных волокон в присутствии воды, выполняемый в размалывающих машинах — мельницах. Размол является одним • из важнейших процессов бумажного производства, позволяющих в широком интервале значений изменять многие свойства бумаги. Производится размол волокон в машинах непрерывного действия (в конических, цилиндрических и дисковых мельницах). Общим для размалывающих аппаратов является то, что работа их основана на принципе скрещивающихся ножей и трущихся поверхностей.
Проходя между ножами размалывающих машин, волокна подвергаются воздействию механических и гидродинамических сил, приводящему к протеканию сложных физико-химических и коллоидных процессов в структуре волокон. В результате происходят некоторое укорочение волокон (рубка), поверхностное расщепление и расчесывание в продольном направлении фибриллярной структуры клеточной стенки на фибриллы (поверхностное фибрил-лирование), набухание и гидратация волокон. Волокна становятся более мягкими, повышается их эластичность и пластичность. В процессе фибриллирования ослабляются и разрушаются связи между отдельными фибриллами клеточной стенки волокон. На поверхности фибрилл образуется начес тонкого пухообразного материала, состоящего из целлюлозных молекул. В результате увеличивается удельная поверхность волокон и число свободных гидроксильных групп, способствующих лучшему контакту и соединению отдельных волокон в бумажный лист. Увеличение удельной поверхности волокон и высвобождение гидроксильных групп повышает способность волокон удерживать воду.
В зависимости от режима размола можно получать бумажную массу различной степени помола: от низкой (садкая масса) до высокой (жирная масса). Для получения садкой массы размол ведут в режиме, обеспечивающем преимущественно рубку волокон над поверхностным фибриллированием. В процессе формования листа бумаги масса низкой степени помола (садкая) быстро оседает на сетке, легко обезвоживается и образует рыхлую и пористую структуру листа. Для высокой степени помола массы (жирная масса) характерно преобладание фибриллированных волокон с хорошо разработанной поверхностью, которые труднее обезвоживаются на сетке бумагоделательной машины и образуют плотную, сомкнутую и прочную структуру листа. Характер помола массы выбирают в зависимости от вида и качества вырабатываемой бумаги и картона.
Прочность бумаги характеризуется рядом показателей: сопротивлением разрыву, излому, продавливанию, надрыву и раздиранию, для каждого вида и сорта бумаги имеющим определенное значение, и в общем зависит от прочности волокон, их длины, прочности связи между волокнами и структуры бумажного листа.
Абсолютные значения прочности на разрыв различных видов растительных волокон не уступают прочности железа, чугуна и стали. Так, волокна хлопка выдерживают усилие до 412 МПа, льна — до 745, хвойной сульфатной целлюлозы — до 520; абсолютная прочность на разрыв чугуна составляет 314 МПа, железа — до 392 МПа и различных видов стали от 490 до 1961 МПа. Почему же лист бумаги, изготовленный из растительных волокон, по прочности значительно уступает прочности металлов и почему прочность листа-бумаги намного ниже прочности тех волокон, из которых он Изготовлен?
Лист бумаги при испытании разрывается по наиболее слабому месту. Этим слабым местом в большинстве случаев являются не сами волокна, а связи между ними. При разрыве листа по обе стороны в месте разрыва наблюдается преимущественное вытаскивание волокон из толщи листа, что указывает на разрыв связи между ними. И только часть волокон рвется в поперечном направлении.
Согласно выдвинутым теориям силы, связывающие волокна в листе бумаги, имеют физико-химическую и электростатическую природу и возникают между свободными поверхностными гидрок-сильными группами целлюлозных волокон при их взаимном сближении. Известная роль отводится также силам трения. Механизм образования сил связи, объединяющих волокна в бумажный лист, сложен. Предпочтительнее выглядит теория водородной связи: в период формования структуры бумажного листа в процессе обезвоживания волокнистой суспензии происходит сближение и уплотнение волокон между собой. При определенной сухости бумажного листа вначале возникает менее прочная связь между волокнами через водяные мостики (рис. 22,6), которая определяет прочность бумажного листа в мокром состоянии и обеспечивает возможность передачи мокрого полотна из сеточной части машины в прессовую. Затем в процессе прессования по мере дальнейшего обезвоживания и сближения волокон наряду с водяными мостиками возникают мостиковые связи через атомы водорода (рис. 22, а) — водородные связи, завершение образования которых происходит в процессе сушки при сближении волокон на расстояние 0,255—0,275 нм. Водородная связь достаточно прочна, она является основной силой сцепления волокон между собой в бумажном и картонном листе.
Исходя из вышеизложенной теории, легко объяснить влияние степени помола на прочность бумаги. Чем выше степень помола,
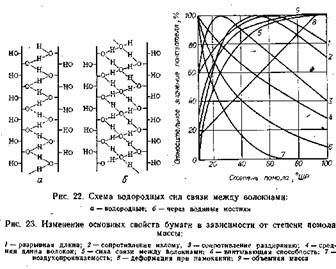
тем больше образуется на поверхности волокон свободных гидрок-силов и тем прочнее связь между волокнами и наоборот. Однако следует иметь в виду, что, повышая степень помола, мы снижаем толщину волокон (разрушаем их структуру) и тем самым снижаем прочность самих волокон. Поэтому повышение прочности бумаги увеличением степени помола можно достигать только до определенной границы, далее которой будет превалировать снижение прочности бумаги за счет потери прочности и укорочения самих волокон.
Забиваем Сайты В ТОП КУВАЛДОЙ - Уникальные возможности от SeoHammer
Каждая ссылка анализируется по трем пакетам оценки: SEO, Трафик и SMM.
SeoHammer делает продвижение сайта прозрачным и простым занятием.
Ссылки, вечные ссылки, статьи, упоминания, пресс-релизы - используйте по максимуму потенциал SeoHammer для продвижения вашего сайта.
Что умеет делать SeoHammer
— Продвижение в один клик, интеллектуальный подбор запросов, покупка самых лучших ссылок с высокой степенью качества у лучших бирж ссылок.
— Регулярная проверка качества ссылок по более чем 100 показателям и ежедневный пересчет показателей качества проекта.
— Все известные форматы ссылок: арендные ссылки, вечные ссылки, публикации (упоминания, мнения, отзывы, статьи, пресс-релизы).
— SeoHammer покажет, где рост или падение, а также запросы, на которые нужно обратить внимание.
SeoHammer еще предоставляет технологию Буст, она ускоряет продвижение в десятки раз,
а первые результаты появляются уже в течение первых 7 дней.
Зарегистрироваться и Начать продвижение
Влияние длины волокон на прочность бумаги также связано с водородными силами. С одной стороны, чем длиннее Волокна, при прочих равных условиях, тем больше водородных связей будет участвовать в сцеплении волокон между собой и тем прочнее будет бумага. С другой стороны, слишком длинноволокнистая масса вызывает хлопьеобразование и ухудшение некоторых печатных свойств. Поэтому для каждого вида бумаги выбирается определенный режим размола, обеспечивающий необходимую длину и фибриллирование волокон.
Кроме водородных сил связи, в бумаге существуют чисто механические силы, обусловленные переплетением волокон и их шероховатостью. Чем плотнее структура, чем лучше прилегают волокна друг к другу, тем более прочным является бумажный лист. Изменение основных свойств бумаги в зависимости от степени помола массы показано на рис. 23.
Основными факторами, влияющими на качество помола целлюлозы, являются: продолжительность размола, удельное давление между ножами мельниц, концентрация массы, тип размалывающей гарнитуры, окружная скорость ротора или барабана, температура массы при размоле. К управляемым факторам относятся продолжительность, удельное давление, концентрация и температура массы.
Для размола волокнистых полуфабрикатов на предприятиях, вырабатывающих массовые виды бумаги и имеющих большую производительность, применяются дисковые мельницы. Массный размол проводится в однодисковых и сдвоенных мельницах с закрытой камерой, которые обеспечивают производительность до 650 т/сут.
Широкое применение дисковых мельниц обусловлено быстрым развитием производства волокнистых полуфабрикатов высокого выхода. Они вытесняют другие виды размалывающего оборудования (конические мельницы, роллы) благодаря следующим преимуществам: возможности размола при высокой концентрации массы (до 40%); более низкому удельному расходу энергии; большой единичной мощности и производительности, компактности, простоте конструкции; более широкой области применения (размол целлюлозы, полуфабрикатов высокого выхода, древесной щепы, отходов сортирования древесномассного и целлюлозного производств); возможности получения более однородной по структуре массы.
До недавнего времени основным размалывающим оборудованием при непрерывном процессе размола волокнистых полуфабрикатов были конические мельницы. В последнее время интерес к ним значительно уменьшился. Практически во всех новых мощных технологических потоках устанавливаются только дисковые мельницы. Однако конические мельницы еще широко используются на действующих предприятиях и находят применение в потоках небольшой производительности (2—30 т/сут).
Основные рабочие элементы мельницы — статор (корпус) и ротор — выполнены в виде конусов. Внутреннюю поверхность статора и внешнюю поверхность ротора образуют сменные ножевые рубашки. Зазор между ножами статора и ротора регулируется перемещением (присадкой или вылегчиванием) ротора вдоль его оси при помощи присадочного механизма. При работе мельницы движение массы осуществляется в направлении от малого диаметра ротора к большему . Производительность мельницы по воздущ-носухому волокну 4—16 т/сут, частота вращения ротора 1000 мин-1, площадь поверхности соприкосновения гарнитуры ротора и статора 0,40 м 2 .
Проклейка. Назначение проклейки — придание бумаге или картону ограниченных впитывающих свойств по отношению к воде, чернилам, типографской краске и другим жидкостям и улучшение многих других физико-механических свойств. При неограниченном впитывании (у неклееной бумаги), например, чернил, они будут впитываться в толщу листа бумаги, расходиться и проходить на его обратную сторону. Полное отсутствие впитывающих свойств будет вызывать стекание чернил с поверхности бумаги. Первое и второе явление делают бумагу непригодной для письма и печати. Поэтому процесс проклейки призван обеспечивать для каждого конкретного вида бумаги и картона свою строго определенную впитывающую способность, которая оценивается степенью проклейки [2].
Различают поверхностную проклейку и проклейку в массе. Поверхностную проклейку осуществляют нанесением крахмального или животного клея на поверхность готовой бумаги. Применяется она для производства некоторых специальных высокосортных видов бумаги — документной, чертежной, картографической и др. Подавляющее большинство видов бумаги и картона проклеивается введением проклеивающих веществ в бумажную массу перед отливом бумажного листа, т. е. проклеивается в массе. Для проклейки в массе применяют гидрофобные (водоотталкивающие) вещества, а процесс проклейки все чаще называют гидрофобизацией бумаги или картона. Основным гидро-фобизующим веществом является канифоль, выделяемая из смолы хвойных древесных пород. Канифольная или смоляная проклейка бумаги была изобретена в 1807 г. Иллигом [1].
Для гидрофобизации бумаги и картона имеется большой выбор гидрофобных веществ, среди которых наиболее широкое применение нашли: различные виды канифоли (живичная, экстракционная и талловая, а также их модификации — талловая модифицированная ТМ и экстракционная модифицированная осветленная ЭМО); укрепленные клен на основе перечисленных канифолей; нефтеполимерные смолы (НПС); парафин; талловый пек; нефтяные остатки и др.
основным компонентом которой является абиетиновая кислота.
Канифольный клей получают в клееварочных котлах (варка клея) обработкой канифоли водными растворами щелочей: едкого натра или кальцинированной соды при температуре 95—105 °С.
. В за-
висимости от количества щелочи, взятой на омыление канифоли, можно получить бурый или белый клей. Для приготовления бурого клея берут такое количество щелочи, чтобы можно было полностью нейтрализовать канифольные кислоты. Сваренный клей легко разводится водой с образованием коллоидного раствора бурого цвета. Концентрацию клея в растворе доводят до 20—40 г/л и применяют для проклейки. Если для варки клея взять щелочи меньше, чем необходимо на омыление всех кислот, то часть канифоли остается в свободном виде (свободная смола). При разведении в воде такого клея, получается дисперсия белого цвета, получившая название белый клей. Содержание свободной смолы в белом клее может достигать 20—40%• П ри более высоком содержании свободной смолы клеи относятся к высокосмоляным и для стабилизации требуют добавки химических диспергаторов. Белый клей разводят водой до концентрации 18—20 г/л и применяют для проклейки.
Сервис онлайн-записи на собственном Telegram-боте
Попробуйте сервис онлайн-записи VisitTime на основе вашего собственного Telegram-бота:
— Разгрузит мастера, специалиста или компанию;
— Позволит гибко управлять расписанием и загрузкой;
— Разошлет оповещения о новых услугах или акциях;
— Позволит принять оплату на карту/кошелек/счет;
— Позволит записываться на групповые и персональные посещения;
— Поможет получить от клиента отзывы о визите к вам;
— Включает в себя сервис чаевых.
Для новых пользователей первый месяц бесплатно.
Зарегистрироваться в сервисе
В настоящее время в С ССР дл я проклейки бумаги готовят в основном бурый и белый клей с содержанием свободной смолы до 20 % на основе обычных и модифицированных канифолей ТМ и ЭМО. Для проклейки картона также широко используются низшие сорта канифоли и талловый пек. Проклейку древесноволокнистых плит осуществляют нефтяными остатками и парафином. Широкое распространение получили композиционные клеи, представляющие собой смесь двух или нескольких гидрофобизующих веществ, например капифольно-парафиновый клей на основе ЭМО и ТМ канифолей с содержанием парафина от 5 до 20 %. Такой клей успешно используется в течение ряда лет на многих предприятиях. Наряду с сокращением расхода клея на проклейку композиционные клеи обеспечивают улучшение некоторых печатных свойств бумаги (снижение деформации в поперечном направлении и др.).
На многие предприятия проклеивающие вещества поступают в виде готового клея — клея-пасты (это сваренный клей, но еще не разведенный водой). После разбавления водой до требуемой концентрации он готов к применению. Это исключает необходимость иметь на предприятии клееварочное отделение, и, что важнее, клей всегда получается стабильным и высококачественным. В перспективе планируется все предприятия перевести на использование клея-пасты, поставляемого централизованно с нескольких клееварочных заводов [2].
Все виды канифольных клеев готовятся по аналогичным схемам, отличающимся только режимами в зависимости от видов канифоли и щелочи. Типовая схема приготовления клея заключается в следующем. В клееварочный котел, снабженный паровой Рубашкой и мешалкой, заливают определенный объем воды, загружают соду (щелочь), включают мешалку и, подогревая содержимое до 70—80°С , растворяют соду. Затем в котел небольшими порциями загружают раздробленную канифоль (смесь канифолсй, парафин). После расплавления канифоли температуру в котле поднимают до 95—105°С и проводят варку. Варка модифицированных видов канифоли завершается в течение 1 —1,5 ч. После окончания варки готовый клей через фильтр, задерживающий кусочки бумаги и другие крупные частицы, перепускают в промежуточную емкость. Сваренный клей разводят водой в горячем виде: при помощи диспергаторов (инжектора или роторно-пульсацион-ного аппарата), назначение которых раздробить, измельчить клей на частички и распределить их равномерно в воде (этот процесс называется эмульгированием). Клей с температурой 70—75°С поступает к инжектору, куда подводятся пар под давлением 0,5— 0,8 МПа и горячая вода температурой 40—60 СС. Пар, захватывая клей и воду, диспергирует его в воде и дисперсия клея поступает в бассейн, куда предварительно набирается некоторый объем холодной воды.. После завершения процесса диспергирования клей хорошо перемешивается, доводится холодной водой до концентрации 20—25 г/л и поступает в один из баков готового клея, откуда подается в производство. Готовый к применению канифольный клей представляет собой коллоидный раствор — раствор частиц клея микроскопических размеров (от 0,3 до 2,5 мкм), равномерно распределенных в объеме воды.
глинозема или квасцов. Осаждение и закрепление частиц происходит при рН равном 4,5—5, создаваемом добавлением коагулянта. Процесс проклейки завершается в сушильной части бумагоделательной машины. При сушке из осажденных частичек смоляного клея удаляется вода, они спекаются и приобретают водоотталкивающие свойства. В готовом листе бумаги эти частички и являются теми гидрофобными преградами, которые ограничивают проникновение воды в толщу листа и ее растекание по поверхности; чем больше таких гидрофобных преград содержится на целлюлозных волокнах, тем выше проклейка бумаги, и наоборот [1].
Расход проклеивающих материалов зависит от требуемой степени проклейки. При выработке сильноклееных видов бумаги расход канифоли составляет от 1,5 до 3,5 %, слабоклееных — от 0,5 до 1 % массы волокна. Расход сульфата алюминия обычно принимают в 2—2,5 раза больше расхода канифоли.
Контроль качества проклейки бумаги осуществляют по показателю степень проклейки, который определяют многими методами. В СССР наиболее, распространен штриховой метод, заключающийся в нанесении на бумагу стандартными чернилами с помощью рейсфедера линий различной толщины, мм : 0,25; 0,5; 0,75; ...; 2. За степень проклейки принимается наиболее широкая линия после высыхания чернил, при которой чернила не расплылись и не прошли на обратную сторону. Степень проклейки бумаги нормируется ГОСТом. Например, писчая бумага № 1, тетрадная № 1 и 2 должны иметь проклейку не менее 1,25 мм, писчая № 2 и 3 — не менее 1 мм, типографская № 1, 2 и 3 — не менее 0,25 мм.
Наполнение. Под наполнением бумаги понимают введение в композицию бумаги минеральных веществ-наполнителей для улучшения ее качества и экономических показателей. Введением наполнителей в композицию бумаги достигаются следующие цели: снижается себестоимость производства бумаги, так как стоимость наполнителя ниже стоимости волокон, часть которых заменяется-наполнителем; повышается белизна бумаги, поскольку почти все наполнители имеют более высокую степень белизны, чем волокна; существенно увеличивается гладкость поверхности бумаги за счет заполнения частичками наполнителя пор и неровностей между волокнами на шероховатой поверхности листа; уменьшается непрозрачность бумаги, что дает возможность писать и печатать с обеих сторон листа; улучшается равномерность просвета; увеличивается мягкость и пластичность — бумага меньше шумит при перелистывании; снижается объемная масса, пористость и, следовательно, впитываемость литографских красок и т. п.
О содержании наполнителя в бумаге судят по показателю зольности бумаги, который определяют по массе прокаленного остатка после сжигания навески бумаги и выражают в % к массе бумаги. Зольность бумаге придает в основном наполнитель, так как естественная зольность волокон менее 1 %.
По зольности бумагу делят на четыре группы:
бумага с естественной зольностью — фильтровальная, электроизоляционная, основа для фибры и пергамента, жиронепроницаемая; наполнители не вводятся;
бумага малозольная (с зольностью до 5 %) — газетная, мундштучная, обойная и др.; в этих видах бумаги важно сохранить, механическую прочность, поэтому повышение содержания наполнителей, существенно снижающих механические показатели бумаги, нецелесообразно;
бумага средней зольности — писчая с зольностью до 6—8%, некоторые виды бумаги для печати, с зольностью до 15%; в эти виды бумаги наполнитель вводится в ограниченных количествах;
бумага высокозольная (зольность свыше 15%)—это типографская, для глубокой печати и др.; для этих бумаг важно иметь хорошие печатные свойства и высокую непрозрачность, поэтому содержание наполнителя в них большое.
Общим недостатком введения наполнителей является заметное снижение механической прочности и степени проклейки бумаги. Кроме того, с увеличением содержания наполнителей в большей степени обнаруживается пылимость бумаги — явление отделения от поверхности бумаги мелких волокон, частиц наполнителя, проклеивающих веществ. Этот эффект резко ухудшает качество печати — бумажная пыль прилипает к печатной форме, забивает набор и клише.
Для наполнения бумаги чаще всего применяют каолин, реже тальк, мел, гипс, двуокись титана. К аолин , или белая глина, это силикат алюминия белого цвета (белизна 77—87%). В бумажную массу каелин вводят в виде водной суспензии, которую готовят разведением каолина водой в специальных мешалках. Каолиновую суспензию очищают от легких примесей во вращающихся ситовых барабанах и других очистных устройствах. Готовую каолиновую суспензию при концентрации 150—200 г/л хранят в бассейнах при постоянном перемешивании. Расход каолина составляет от 60 до 475 кг на 1 т бумаги. Тальк — это минерал пластинчато-чешуйчатого строения, благодаря чему хорошо удерживается в бумаге. Он придает бумаге гладкость и мягкость, меньше снижает прочность бумаги и степень проклейки. Тальк как наполнитель применяется в значительно меньших количествах, чем каолин. Гипс, мел, двуокись титана и другие наполнители применяют только при выработке некоторых видов бумаги специального назначения.
Введение суспензии наполнителя в размолотую бумажную массу производится непрерывно при помощи дозаторов. При наполнении бумаги большое значение приобретает вопрос об удержании в ней наполнителей. Как по экономическим, так и по технологическим соображениям желательно всегда обеспечить максимальную удерживаемость наполнителей в бумаге. Дело в том, что в процессе обезвоживания и формования бумажного полотна значительная часть вводимых минеральных частиц вымывается и удаляется с водой. Эта часть обычно составляет 40—50 % массы введенного наполнителя.
Механизм удержания наполнителей в бумаге очень сложен и включает в себя механические и коллоидно-химические процессы. На удержание наполнителей влияют многие факторы. Так, в бумаге, изготовленной из массы жирного помола, удержание наполнителей выше, чем в бумаге из массы садкого помола. На удержание наполнителей большое влияние оказывает рН волокнистой суспензии, которая регулируется добавлением коагулянтов клея. ; Оптимальным считается рН около 5. Удержание наполнителя во многом зависит от степени использования оборотной воды на бумажной фабрике. Чем полнее используется оборотная вода, тем выше удержание наполнителя и меньше его промой.
В производстве клееной бумаги большое влияние на удержание наполнителей и степень проклейки бумаги оказывает последовательность введения в бумажную массу наполнителя, проклеивающего вещества и сернокислого алюминия. Наибольшее удержание наполнителя обнаруживается в случае введения его первым, а наилучшие результаты проклейки оказываются в той бумаге, где наполнитель был введен последним. Поэтому при выработке высокозольных бумаг рекомендуется перечисленные компоненты вводить в последовательности: наполнитель — клей — сернокислый алюминий, а при выработке сильноклееных бумаг: клей — сернокислый алюминий — наполнитель.
Для повышения удержания наполнителей в бумажную массу непосредственно перед. б умагоделательной машиной вводят вещества, вызывающие хлопьеобразование: животный клей, активированный силикат, полиэтиленимин (ПЭИ) и полиакриламид (ПАА). Наиболее часто применяют ПЭИ и ПАА, представляющие собой синтетические полимеры — длинные макромолекулы, связывающие частички наполнителя между собой в агрегаты (флокулы). Кроме того, эти полимеры повышают удержание мелких волокон, улучшают структуру листа бумаги и повышают его механическую прочность. Применение специальных добавок позволяет повышать удержание наполнителей до 70—85 %.
Крашение и подцветка. С целью придания бумаге приятных эстетических свойств многие ее виды производят цветными, например: афишную, обложечную, писчую цветную, бумагу для спичечных коробков, конвертную, салфеточную, упаковочные виды и др. Различают крашение бумаги и подцветку. В процессе крашения бумаге придается необходимый цвет, а при подцветке — определенный цветовой оттенок, для чего в бумажную массу перед изготовлением бумаги вводят соответствующие красители. Крашение бумаги является сложным процессом, так как окраске подвергается бумажная масса, в большинстве случаев состоящая из нескольких разнохарактерных волокнистых, наполняющих и проклеивающих частиц, которые имеют различную восприимчивость к одному и тому же красителю; поэтому для получения качественно окрашенной бумаги очень важно правильно подобрать краситель.
В бумажной промышленности нашли применение в основном красители органического происхождения: основные, кислотные, прямые, а также некоторые минеральные пигменты. Применяемые красители имеют много различных цветов и оттенков и обладают высокой красящей способностью.
Крашение и подцветка отличаются количеством задаваемого красителя. Расход красителей для подцветки белой бумаги составляет 20—80 г/т, а для выработки цветной бумаги — от 0,2 до 25 кг/т. В бумажную массу красители вводят непрерывно при помощи дозаторов.
|