Химикаты из древесиныХранение древесины и ее подготовка для производства волокнистых полуфабрикатов
Доставка," выгрузка и учет древесного сырья. Заготовленные в лесу балансы в виде долготья (длина бревен 4,5—6 м) или ко-ротья (длина бревен 1,25—1,5 м), а также технологическая щепа и дрова из соответствующих лесозаготовительных или деревообрабатывающих предприятий, доставляются на целлюлозно-бумажные комбинаты водным, железнодорожным или автомобильным транспортом. Наиболее экономичным видом транспорта является сплав древесины по рекам и озерам в буксируемых плотах или баржах. Технологическая щепа поставляется специальными автощеповозами большой вместимости (от 12 до 40 м3), железнодорожными вагонами-щеповозами (до 150 м3) и водным транспортом в баржах (деревянных 250—300 м3, железных 800— 1000 м3).
Целлюлозно-бумажные комбинаты преимущественно расположены на берегах больших рек или озер, поэтому основную массу сырья они получают сплавом в плотах и баржах и, частично, железнодорожным и автомобильным транспортом. Поскольку возможность водной доставки древесины ограничена навигационным периодом, обычно.4—5 мес в году, создается необходимость хранить на предприятиях большие запасы древесины для обеспечения их работы в течение 8—9 мес. При современных масштабах производства целлюлозно-бумажной продукции потребление древесины крупными предприятиями оценивается сотнями тысяч, а иногда и миллионами кубометров в год. Практически справиться с приемкой такой массы балансов и дров, да еще в течение 120— 140 дней, составляющих продолжительность приплава древесины, можно только лишь при высокой степени механизации всех работ и совершенной организации лесных складов.
Хранение древесного сырья осуществляется на лесных складах, представляющих собой открытую сухую (незатопляемую) площадку, по возможности ровную, расположенную на невысоком берегу реки с прямой береговой линией и примыкающей тихой акваторией. Лесной склад оснащается механизмами для выгрузки, транспортировки и укладки древесного сырья, подачи его в производство, а в некоторых случаях — распиловочным и окорочным оборудованием. Сооружение и устройство лесного склада связано с большими капитальными затратами. Поэтому определяющими факторами при выборе размеров склада, его оснащения механизмами и организации складского хозяйства, являются режим поступления и вид доставки сырья, которые должны обеспечивать хранение минимальных запасов.
На лесной бирже производятся выгрузка сырья из транспортных средств, распределение и укладка его на биржевой площадке, хранение и подача в производство. Для этого используются разнообразные механизмы: поперечные и продольные лесо-транспортеры (производительностью соответственно 100—200 и 30—60 м3/ч) для подъема и выгрузки из воды долготья и коротья отдельными бревнами. Более современна и производительна выгрузка пучков древесины. Для подъема крупных пучков (25— 30 м3) из воды применяют рельсовые выгружатели (бремсберги, Q = 250:300 м3/ч). Универсальными механизмами, широко используемыми на биржах балансов и дров при погрузке и разгрузке барж, вагонов, автотранспорта, подъема пучков из воды, выкладке и разборке штабелей и куч, являются различные типы стреловых и мостовых кранов. Для выгрузки, перемещения и укладки в штабеля преимущественно долготья на крупных предприятиях служат мостовые и кабельные краны. Для беспорядочной укладки коротких балансов (длиной 1,25—1,5 м) в кучи при кучевом методе хранения древесины применяют кучеукладчики (стаккеры). Наиболее эффективным и производительным методом выгрузки коротья из вагонов является применение роторного загоноопрокиды-вателя. Время разгрузки одного вагона составляет около 3 мин (20 вагонов в 1 ч).
Существует четыре метода хранения древесного сырья: в штабелях; в кучах; водный; открытый.
В штабелях могут храниться неокоренные и окоренные балансы в виде долготья (длина бревен 4,5—6 м) и коротья (1,25— 1,5 м). Для выгрузки древесины из воды или железнодорожных вагонов, укладки пучков древесины в штабеля и их разборки широко применяются различные грузоподъемные механизмы.
Древесину, прибывающую сплавом в плотах в виде крупных пучков, объемом 25—30 м3, направляют на лесной рейд, где производятся ее приемка, роспуск плотов и подача пучков к подъемным механизмам. Пучки балансов поднимают из воды и складывают в штабеля. Таким же путем выгружают древесину из барж и платформ, которые подаются под краны по железнодорожным путям.
Организации хранения балансов и технологических дров в кучах отдают предпочтение при строительстве современных целлюлозно-бумажных предприятий, так как этот метод обеспечивает лучшее использование складских помещений и высокую степень механизации. Балансы хранятся только в окоренном виде в свободно насыпаемых кучах высотой до 30 м и шириной в основании до 100 м.
Выгружаемые из воды или железнодорожных платформ пучки древесины поступают на раскатный стол и далее на лесотранс-портер многопильного станка (слешера), где распиливаются на чураки длиной 1,25—1,5 м. Распиленные балансы направляются на окорку. Окоренные балансы попадают на ленточный лесо-транспортер, а с него — на главный кабельный конвейер, транспортирующий их к кучеукладчику (стаккеру). Кучеукладчик состоит из платформы, передвигающейся вдоль и над конвейером по рель-совым-путям, к нижней части опор которой прикреплена металлическая ферма с изменяющимся углом наклона к горизонту (от О до 30°). На ферме смонтирован пластинчатый цепной транспортер. С главного конвейера балансы поступают в приемный лесонако-питель кучеукладчика, затем захватываются наклонным транспортером фермы, поднимаются на установленную высоту и, свободно падая, образуют кучу. По мере роста кучи, постепенно увеличивают угол наклона фермы кучеукладчика. Это предотвращает падение чураков с большой высоты (около 30 м при стационарном устройстве фермы), обусловливающее размочаливание торцов и их забивание землей, песком и другим сором. Передвигаясь, кучеукладчики могут укладывать балансы в кучи длиной до 500 м. Вместимость куч достигает 250 тыс. м3 древесины; производительность кучеукладчика свыше 200 м3/ч. Современные сдвоенные кучеукладчики могут укладывать кучи по обе стороны рельсового пути. При необходимости биржа оборудуется несколькими куче-укладчиками .
Забиваем Сайты В ТОП КУВАЛДОЙ - Уникальные возможности от SeoHammer
Каждая ссылка анализируется по трем пакетам оценки: SEO, Трафик и SMM.
SeoHammer делает продвижение сайта прозрачным и простым занятием.
Ссылки, вечные ссылки, статьи, упоминания, пресс-релизы - используйте по максимуму потенциал SeoHammer для продвижения вашего сайта.
Что умеет делать SeoHammer
— Продвижение в один клик, интеллектуальный подбор запросов, покупка самых лучших ссылок с высокой степенью качества у лучших бирж ссылок.
— Регулярная проверка качества ссылок по более чем 100 показателям и ежедневный пересчет показателей качества проекта.
— Все известные форматы ссылок: арендные ссылки, вечные ссылки, публикации (упоминания, мнения, отзывы, статьи, пресс-релизы).
— SeoHammer покажет, где рост или падение, а также запросы, на которые нужно обратить внимание.
SeoHammer еще предоставляет технологию Буст, она ускоряет продвижение в десятки раз,
а первые результаты появляются уже в течение первых 7 дней.
Зарегистрироваться и Начать продвижение
Для подачи балансов из куч в производство используют тот же цепной конвейер кучеукладчика, для чего снабжают его реверсом, транспортирующим балансы на обратную ветвь главного конвейера, доставляющего их к промывным барабанам в древес-ноподготовительном цехе. Для разгрузки куч используют стреловые краны с многолопастными грейферными захватами вместимостью 3—5 м3 древесины.
При водном методе хранение древесины в зимнее время осуществляют в специально устроенных незамерзающих рейдах.
На открытых складах хранятся технологическая щепа (на открытых площадках в кучах большой вместимости) и щепа собственного изготовления. Этот метод требует значительно меньших капитальных и эксплуатационных затрат, чем хранение балансов в штабелях и кучах, и поэтому является экономически более выгодным.
Технологическая щепа, поступающая в железнодорожных вагонах или автощеповозах, разгружается в траншеи, оборудованные скребковыми транспортерами, откуда подается в производство или насклад хранения. Разгрузку барж осуществляют стреловыми, грейферными кранами или пневматическими установками.
Насыпку куч и их разгрузку для подачи щепы в производство осуществляют с помощью бульдозеров, винтовых конвейеров, пневмотранспортеров и ленточных транспортеров. Наиболее экономичным и удобным для насыпки куч и подачи щепы в производство является пневмотранспорт. Простота обслуживания, высокая производительность и надежность обусловили его широкое применение. Транспорт щепы осуществляется по трубопроводам потоком воздуха, создаваемым воздуходувкой. Скорость переноса щепок составляет 35—45 м/с , а концентрация щепы в потоке воздуха 3,5—6 %• Объем куч равен 150—250 тыс. м3 щепы при высоте 25— 30 м. Фактическая удельная загрузка площади склада достигает 6—8 м3 древесины на 1м
К преимуществам хранения щепы в открытых кучах относится выветривание и окисление смолы, как и при хранении балансов в штабелях и кучах, что снижает в последующем смоляные затруднения в сульфитцеллюлозном и ценообразование в сульфат-целлюлозном производствах. Механические и химические свойства целлюлозы, сваренной из щепы, хранящейся не более 6 мес , мало отличаются от свойств целлюлозы, полученной из балансов. Срок хранения щепы из древесины лиственных пород не более 3 мес. К недостаткам этого метода можно отнести потери древесины (2—5%) от загнивания, некоторое снижение белизны целлюлозы и опасность самовозгорания куч.
Древесина учитывается в объемной мере, выражаемой в кубических метрах. При этом различают кубические метры складочной древесины (скл. м3) и плотной древесины (пл. м3).
В складочных кубометрах древесины выражают общий объем, занимаемый древесиной и пустотами, образованными неплотностью прилегания балансов (из-за округлости, кривизны, сучков и т. п.) или щепок друг к другу, в плотных кубометрах древесины — объем, занимаемый только древесиной. Поэтому между ними существует следующее соотношение: 1 скл. м3 древесины равен 0,72 пл. м3 древесины, или 1 пл. м3 древесины равен 1,4 скл. м3 древесины. Также принимают, что в 1 м3 щепы содержится 0,5 скл. м3 древесины или 0,33 пл. м3 древесины.
Подготовка древесины к переработке. Хранение древесины на лесных складах является одной из главных операций по подготовке древесины к переработке. Дальнейшие операции по подготовке балансов и дров к процессу варки целлюлозы или полуцеллюлозы сводятся к распиловке, окорке, рубке балансов в щепу, сортировке щепы и дополнительному измельчению крупной щепы. Эти операции выполняются в древесноподготовительном цехе (ДПЦ).
Производство различных видов древесной массы может осуществляться как из балансов, так и из щепы. Поэтому в одном случае подготовка древесины ограничивается распиловкой и окоркой, а в другом — аналогична подготовке древесины для целлюлозного производства.
В недалеком прошлом производство волокнистых полуфабрикатов базировалось на традиционном балансовом сырье, подготовка которого осуществлялась непосредственно на целлюлозно-бумажных комбинатах. В последние годы ресурсы древесного сырья существенно возросли за счет вовлечения в переработку низкокачественной древесины, отходов лесозаготовок, шпал о- и таропиления, лесопиления и деревообработки. Экономическая целесообразность подготовки этих видов сырья для использования в местах их непосредственного получения, вызванная более рациональным использованием государственных транспортных средств, привела к образованию широко разветвленной структуры древес-ноподготовительного производства (рис. 1). Основной единицей в этой структуре остается ДПЦ целлюлозно-бумажного предприятия, другими структурными звеньями являются цехи и участки лесозаготовительных, лесопильных и деревообрабатывающих предприятий-поставщиков технологической щепы [7].
Распиловка древесины. На рис. 2 показано устройство и принцип действия многопильного станка (слешера), получившего наибольшее распространение для распиловки балансов. Сле-шер состоит из смонтированного на наклонной деревянной или металлической раме многоцепного транспортера. Цепи транспортера шарнирного типа снабжены мощными захватами и приводятся в движение от привода, расположенного под рамой, через звездочки, закрепленные на валу. Балансы поступают к слешеру лесотранспортером, с которого автоматически сбрасываются на движущийся транспортер. Захваченные балансы с постоянной скоростью (около 0,2 м/с) поочередно надвигаются на вращающиеся дисковые пилы, распиливаются на отрезки определенной длины и поступают на продольный транспортер, которым подаются к окорочным устройствам. Число пил на слешере определяется необходимым числом резов. В целлюлозном производстве 6— 7-метровые балансы обычно распиливаются на отрезки длиной 2—2,5 м. В этом случае достаточно двух пил, как это показано на рис. 2. При распиловке балансов на более короткие отрезки для древесномассного производства число пил на слешере увеличивается до шести-семи. Диаметр пил равен 1500 мм, толщина 6 мм, производительность слешера 150—250 пл. м3 древесины в 1 ч. Потери древесины на опилки составляют 0,3 %. При распиловке балансов для производства древесной массы эти потери больше (до 2—3%), так как часть древесины теряется в виде отпиливаемых торцов бревен.
Сервис онлайн-записи на собственном Telegram-боте
Попробуйте сервис онлайн-записи VisitTime на основе вашего собственного Telegram-бота:
— Разгрузит мастера, специалиста или компанию;
— Позволит гибко управлять расписанием и загрузкой;
— Разошлет оповещения о новых услугах или акциях;
— Позволит принять оплату на карту/кошелек/счет;
— Позволит записываться на групповые и персональные посещения;
— Поможет получить от клиента отзывы о визите к вам;
— Включает в себя сервис чаевых.
Для новых пользователей первый месяц бесплатно.
Зарегистрироваться в сервисе
Окорка древесины. Балансы перед измельчением в щепу или перед дефибрированием должны быть очищены от коры (окорены), которая плохо проваривается по сульфатному методу и совершенно не проваривается по сульфитному, сильно засоряя целлюлозу. На долю коры приходится значительная часть объема ствола, которая в среднем составляет для еловых балансов 11 %, сосновых 15, осиновых 14, березовых 13 и лиственничных 16%.
В процессе окорки стремятся более полно очистить балансы от коры с минимальными потерями древесины, которые в любом
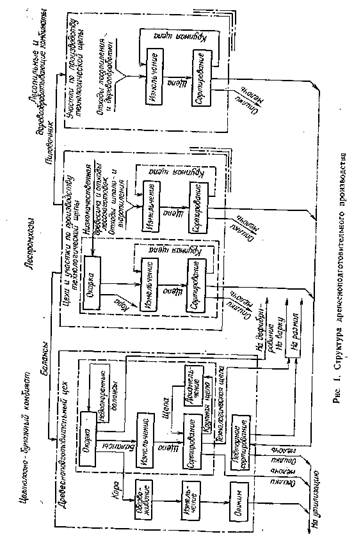
методе окорки неизбежно имеют место. Определяющее значение в процессе отделения коры от древесины принадлежит силам сцепления коры с древесиной, зависящим от влажности и температуры коры. Наиболее желаемым является отделение коры по слою камбия, которое легко осуществляется в свежесрубленной летом древесине. Подсушивание древесины увеличивает силы сцепления коры с древесиной в 2—3 раза, а промораживание при температуре от —5 до —20°С в 8—10 раз. Поэтому подсушенная и промороженная древесина окаривается очень трудно небольшими потерями.
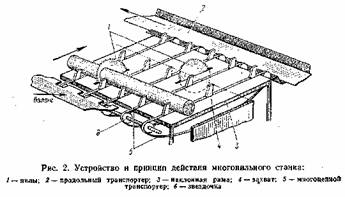
Продолжительное пребывание в воде, пропарка древесины паром или замачивание в горячей воде облегчают окорку. Это учитывается при выборе методов окорки.
В практике применяются в основном механические методы, в которых кора отделяется от ствола различными приемами: срезанием острыми ножами; трением балансов друг о друга; сдиранием по слою камбия и смыванием струей воды под очень высоким давлением. Распространение получили окорочные машины, в основу работы которых положены принципы трения и сдирания. Это окорочные станки трения и роторные окорочные станки. Наиболее широко применяются непрерывно работающие окорочные барабаны, позволяющие окаривать как коротье (барабаны со свободным заполнением), так и длинник (барабаны с параллельной укладкой баланса).
Все шире находят применение двухсекционные барабаны для полусухой и сухой окорки. Устройство и принцип действия такого барабана показаны на рис. 3. Окорочный барабан состоит из двух секций — закрытой, для предварительной обработки баланса, и открытой, окорочной. Закрытая секция представляет собой сплошной стальной цилиндр, к внутренней поверхности которого приварены профильные балки для подрезания и разбивания коры.
Открытая секция также имеет вид барабана, собранного из профильных балок, между которыми имеются продольные щели величиной 60 мм. Для повышения эффективной окоркн балки обращены ребрами внутрь барабана. Барабан устанавливается на роликовые опоры и приводится в движение приводом. Внутренний диаметр барабана 3850 мм, длина 20570 мм, частота вращения 6 мин-1.
Балансы длиной от 1 до 2,5 м подаются с торца барабана в закрытую секцию, заполняя барабан на 50—60 % и за счет вращения
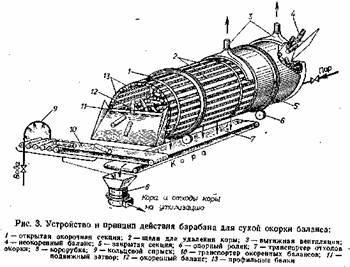
барабана переваливаясь и ударяясь о его стенки и один одругй, медленно продвигаются к противоположному, выгрузочному концу. При таком характере передвижения балансов происходит. и нтенсивное разрушение и сдирание с них коры. Сдирание коры облегчат пропарка и увлажнение древесины паром в закрытой секции, который подается туда под давлением 0,6 МПа. Избыток пара из барабана удаляется вытяжной вентиляцией. Расход пара на окорку 1 пл. м3 древесины 20—25 кг. Основная масса коры с балансов удаляется в открытой окорочной секции. Кора влажностью 40 % проваливается через щели, попадает на транспортер, подающий кору и другие отходы окорки (отколотые щепки, опилки и т. п.) на корорубку. Потери древесины составляют 0,5—2 %.
Время пребывания балансов в барабане зависит от их свойства и состояния (мороженые, лежалые, лиственные) и регулируется подвижным затвором. Пройдя барабан, окоренный баланс поступает на транспортер, с него на рольганг, где прилипшая к нему кора и сор сдуваются сжатым воздухом или смываются водой при помощи спрысков. Далее баланс поступает на измельчение. Производительность барабана 35—50 пл. м3/ч.
К преимуществам сухой окорки относятся: уменьшение расхода воды на окорку в 10 раз (при применении обмыва) или полное отсутствие потребления воды (при обдуве воздухом), позволяющее получить после окорки сухую кору (сухость 60 %); отсутствие надобности применения короотжимных прессов; снижение эксплуатационных расходов.
Рассмотренный принцип работы характерен для всех типов окорочных барабанов. Отечественная промышленность выпускает окорочные барабаны КБС для окорки дров и отходов лесозаготовок и КБ для окорки балансов и дров. Производительность барабанов 50—200 м3/ч. Из другого окорочного оборудования в последние годы широкое применение нашли роторные окорочные станки, позволяющие получать сухую кору, которая после измельчения направляется на сжигание.
Использование отходов окорки. Отходы окорки достигают 15 % объема перерабатываемой древесины. Для предотвращения загрязнения окружающей среды их необходимо утилизировать. Наиболее простым и распространенным способом использования отходов является сжигание их в специальных топках паровых котлов. При мокром способе окорки влажность коры составляет 75—85 %. В этом случае ее нужно обезвоживать до сухости 40—45 %. Воду удаляют при помощи водоотделительных барабанов или короотжимных прессов. Теплота сгорания отжатой коры 6000—7000 кДж/кг, что делает процесс сжигания рациональным. Кору можно использовать для производства строительных плит и картонов, для химической переработки и получения сельскохозяйственных удобрений.
Рубка балансов в щепу. Задачей рубки является измельчение окоренных балансов в щепу, однородную по размерам (длина 16—20 мм, ширина 20—25 мм, толщина 2—3 мм) и с гладким отрубом. Повсеместно на целлюлозных заводах балансы измельчают дисковыми многоножевыми рубительными машинами (рис. 4). Рабочим органом рубительной машины является стальной диск с радиально расположенными ножами. Диск закреплен на горизонтальном стальном валу в трех подшипниках и приво 1 дится в движение приводом. Диаметр диска составляет 2—4 м, число ножей от 8 до 16, частота вращения до 650 мин-1.
Балансы по наклонно расположенному (угол наклона от 45 до 50° к горизонту) питательному патрону один за другим подаются к диску и попадают под удары ножей. Режущие кромки ножей, взаимодействующие с упорным ножом, отрубают от бревна шайбы толщиной 15—25 м, которые фасками ножей раскалываются вдоль волокон на отдельные кусочки, проскакивают сквозь прорези диска на его другую сторону и, ударяясь о стенки, кожуха, дробятся в щепки. Толщина отрубаемых шайб регулируется выступом ножа над диском. Лопатками, укрепленными на ободе диска, по патрубку щепа вместе с потоком воздуха выбрасывается в циклон или бункер. Освободившись от щепы в циклоне или бункере, воздух возвращается обратно в кожух рубительной машины по всасывающему воздухопроводу.
Основной особенностью работы многоножевой рубительной машины (в отличие от малоножевой) является непрерывность
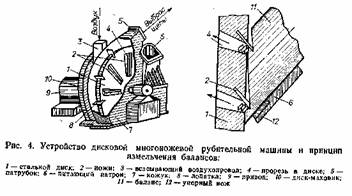
процеса рубки: каждый последующий нож входит в древесину до выхода из нее предыдущего, как показано на рис. 4. Это обеспечивает затягивание балансов в машину и исключает их подпрыгивание. Щепа получается лучшего качества — более мелкая и однородная по размерам [3].
Отечественная промышленность выпускает рубительные машины МРН-100 и МРН-150, МРН-300 производительностью 100, 150 и 300 пл. м3/ч. Расход электроэнергии на рубку балансов 3— 4 кВт-ч на 1 мэ древесины. В результате рубки получается около 90 % нормальной щепы (это щепа указанных выше размеров, применяемая для варки), примерно 8% крупной щепы и 2% отходов в виде опилок и пыли. Крупная щепа поступает на дополнительное измельчение (дезинтегрирование) и возвращается в общий поток. Общий выход нормальной щепы после рубки и дезинтегрирования составляет около 97 %, остальные 3 % —отходы [7]. Для измельчения в щепу долготья в современных рубительных машинах применяют горизонтальную подачу древесины, обеспечивающую получение щепы более высокого качества.
Сортирование, транспортирование и хранение щепы. В процессе рубки наряду с нормальной щепой образуются мелочь и крупные куски, которые отделяются от нее сортированием. Сортирование щепы осуществляется при помощи плоских сортировок. Сортировка (рис. 5) состоит из металлического короба, установленного под углом 20° к горизонту, в котором одно над другим укреплены три сита: верхнее с отверстиями 30X30 мм, среднее с отверстиями 10 X Ю мм и нижнее с отверстиями 5Х Х5 мм. Короб укрепляют на фундаменте или подвешивают так, что он может совершать колебательные движения (до 150 в 1 мин) в горизонтальной плоскости от специального механизма
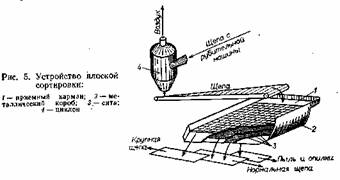
Щепа с рубительной машины выбрасывается в циклон, где, входя по касательной к цилиндрической стенке, теряет скорость и падает в нижнюю часть циклона. Из циклона щепа попадает на ленточный транспортер и направляется на сортировку. Несортированная щепа подается в приемный накопитель и распределяется по поверхности верхнего сита. Благодаря наклону сортировки и ее колебательным движениям щепа, продвигаясь вдоль поверхности сит, просеивается, разделяясь на фракции (крупная щепа, нормальная щепа, мелкая щепа, опилки и пыль), которые задерживаются верхним, средним, нижним ситами и поддоном короба. Нормальная и мелкая щепа объединяются в общий поток и ленточным транспортером подаются в варочный цех. Крупная щепа своим транспортером подается на дезинтегратор, после чего возвращается на сортирование. Опилки и пыль с поддона короба направляются на утилизацию (чаще всего на сжигание в топках паровых котлов).
Производительность сортировок марки СЩ, выпускаемых отечественной промышленностью (СЩ-60, СЩ-120, СЩ-500), от 60 до 900 м3 щепы в 1 ч. Отсортированная щепа из ДПЦ Поступает. в бункера варочного цеха или в промежуточные наземные бункера-силосы, в которых запас обычно обеспечивает суточную работу целлюлозного завода. Щепа в бункера подается ленточными транспортерами, ковшовыми элеваторами или пневматическими установками.
|