Технология электрической сварки металлов и сплавов плавлениемСварка под флюсом
Получение равнопрочных сварных соединений при сварке низкоуглеродистой стали под флюсом достигается в основном за счет применения высококремнистых марганцев флюсов АН-348-А, ОСЦ-45 и т. п. и низкоуглеродистой сварочной проволоки Св-08 и Св-08А. При этом достигается высокая стойкость металла шва против образования кристаллизационных трещин и пор. При сварке особо ответственных сварных конструкций эти флюсы пр имен яются в сочетании со сварочной проволокой Св-08 ГА (см. гл. 7). Основной объем работ по автоматической сварке низкоуглеродистой стали выполняется сварочной проволокой диаметром 4 и 5 мм. Для автоматической сварки тонкого металла используется проволока диаметром 0,8—3 мм. Полуавтоматическая сварка выполняется проволокой диаметром 0,8—2 мм.
Сварка стыковых швов. В конструкциях из низкоуглеродистой стали широко применяется сварка стыковых швов без разделки кромок. Увеличение доли основного металла в металле шва, характерное для этого случая, не является препятствием для применения такой технологии, так как содержание углерода в основном металле невелико. Разделка кромок необходима для улучшения формирования шва и в тех случаях, когда толщина основного металла превосходит толщину, которую можно проплавить без разделки кромок.
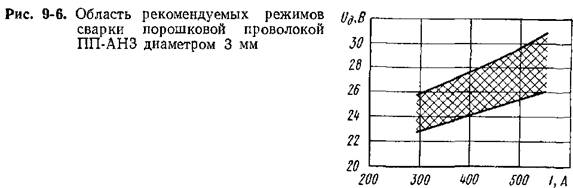
Режим сварки стыковых соединений зависит от типа шва (односторонний, двусторонний, однослойный, многослойный), способа подготовки кромок (без разделки кромок, с разделкой кромок, с обязательным зазором) и от способа удержания сварочной ванны (на флюсовой подушке, на медной прокладке, с ручной подваркой).
При сварке на флюсомедной или стальной подкладке режим сварки двусторонних швов такой же, а режим сварки односторонних швов отличается несколько большей силой тока (табл. 9-9, 9-10, 9-11).
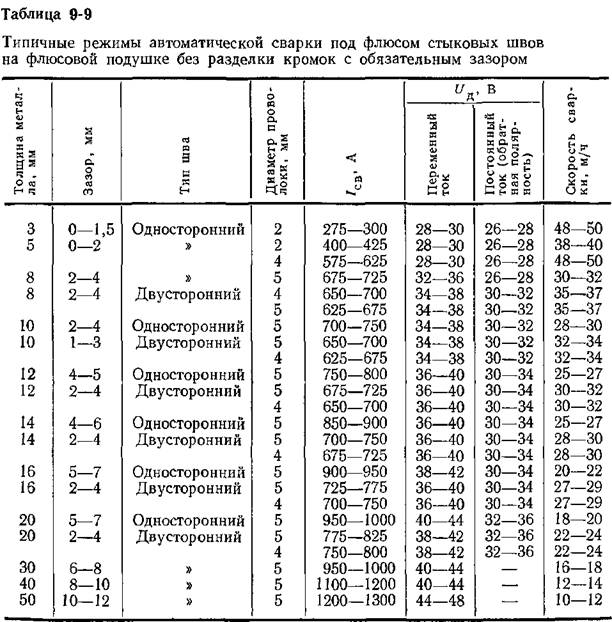
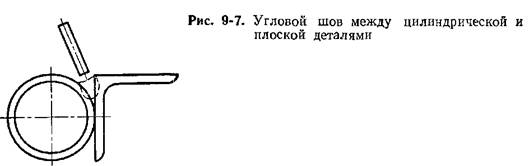
Из табл. 9-12 видно, что металл стыкового шва, сваренного автоматом и полуавтоматом под флюсом, обладает прочностью и пластичностью, равными или превышающими соответствующие свойства основного металла.
Стыковые швы на металле толщиной до 3 мм сваривают проволокой диаметром 0,8—2 мм. Применение тонкой проволоки и постоянного тока позволяет существенно уменьшить силу сварочного тока (7СВ = 8Q— 150 А) без снижения стабильности процесса сварки. Снижение мощности дуги приводит к резкому уменьшению объема сварочной ванны и глубины проплавления основного металла.
Сварка угловых швов под флюсом осуществляется в положении в лодочку и в угол (табл. 9-13, 9-14).
При сварке угловых швов с разделкой кромок или при сварке угловых швов, соединяющих элементы прямоугольной формы с цилиндрическими деталями малого диаметра (рис. 9-7), возможно образование кристаллизационных трещин в швах вследствие неблагоприятных условий их кристаллизации. При необходимости выполнения подобных швов рекомендуется сваривать их двумя дугами в раздельную ванну или в два слоя. При сварке в два слоя первый слой следует выполнять на режиме, обеспечивающем минимальный провар основного металла и максимальное значение коэффициента формы провара.
В зависимости от условий сварки механические свойства металла шва, сваренного под флюсом, изменяются в довольно широких пределах. Если необходимо получить металл шва с пластическими прочностными свойствами, близкими к свойствам основного металла, сечение углового шва или слоя (при многослойной сварке) следует назначать в зависимости от толщины свариваемого металла. Опытным путем установлена зависимость между толщиной основного металла и сечением шва или слоя:

Сварка в защитных газах. Как правило, сварку низкоуглеродистых сталей проводят в углекислом газе, что обусловлено его малой стоимостью. Сварка в аргоне и его смесях находит пока ограниченное применение.
Для автоматической и полуавтоматической сварки плавящимся электродом в углекислом газе металла толщиной 0,8—3 мм и угловых швов с катетами 1—4 мм при любом пространственном поло-
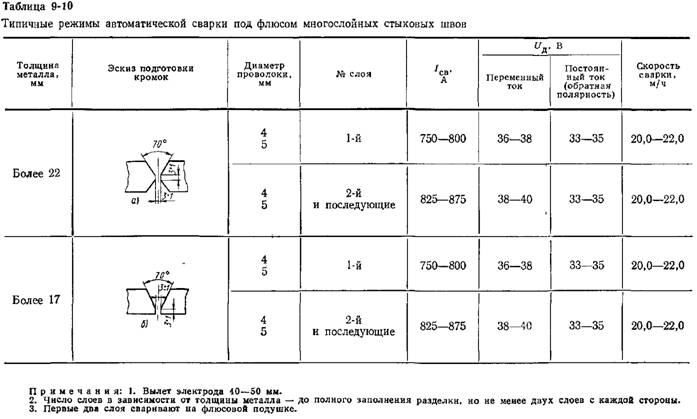
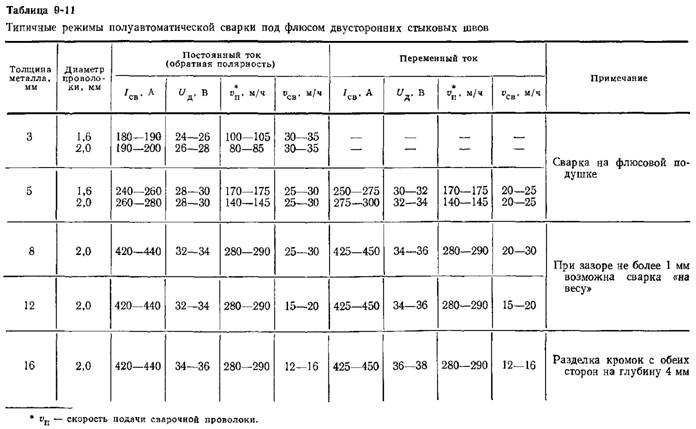
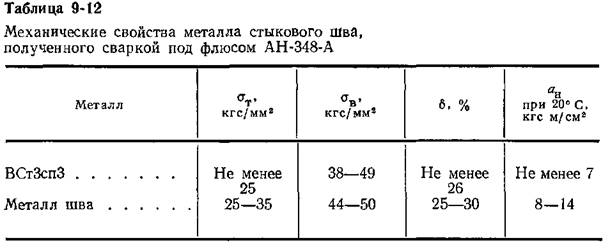
жении шва применяют сварочную проволоку диаметром 0,5— 1,4 мм. Сварку проволокой диаметром 1,4—4 мм ведут в нижнем положении и применяют для металла средних толщин, а также для заварки дефектов литья.
Для обеспечения необходимых механических свойств металла шва и высокой стойкости его против кристаллизационных трещин и пор при сварке кипящей и спокойной низкоуглеродистых сталей в углекислом газе применяют сварочные проволоки Св-08ГС
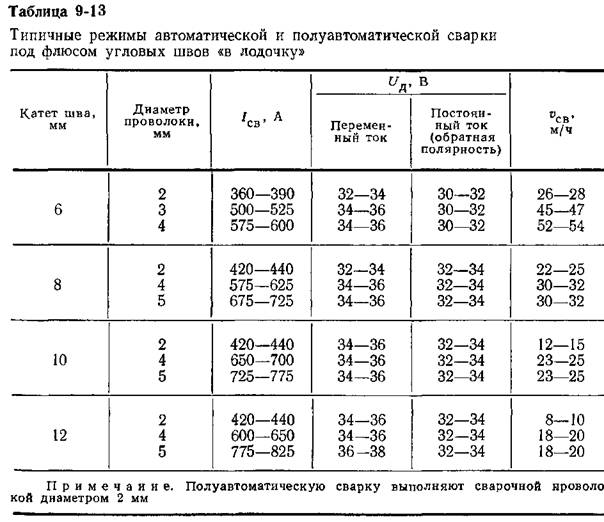
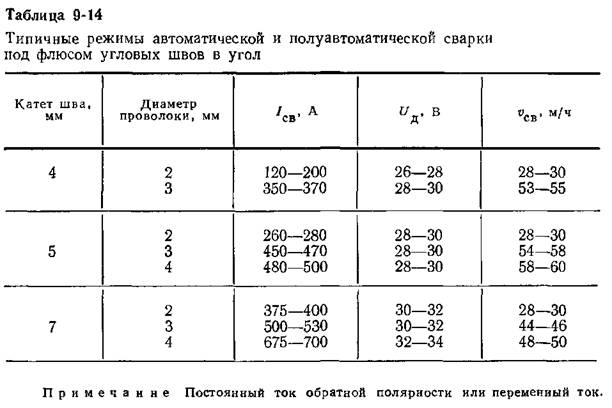
или Св-08Г2С, легированные кремнием и марганцем. При сварке спокойной низкоуглеродистой стали применяют также проволоку Св-12ГС (см. §7-1). При сварке низкоуглеродистых сталей с содержанием углерода, приближающимся к верхнему пределу (0,21—0,25%), следует применять сварочную проволоку Св-08ГС или Св-08Г2С. При сварке проволокой Св-12ГС в этих условиях не обеспечивается необходимая стойкость шва против кристаллизационных трещин.
Серьезное влияние на свойства металла шва оказывает качество углекислого газа. Повышенное содержание в нем водяных паров и воды способствует образованию пор даже при хорошей защите дуги от воздуха и надлежащем количестве кремния и марганца в сварочной ванне (см. §6-4). При применении углекислого газа и сварочной проволоки соответствующего состава поры в швах не образуются. В этом случае отрицательное влияние ржавчины проявляется меньше, чем при сварке под флюсом. При сварке проволокой диаметром 0,5—1,4 мм металл капель в сварочной ванне окисляется в меньшей степени, чем при сварке проволокой диаметром 1,6—3 мм. Поэтому содержание кремния и марганца в шве при проволоке диаметром 0,5—1,4 мм может быть несколько меньшим, чем при проволоке большего диаметра.
Дополнительное легирование проволок для сварки в углекислом газе сильными элементами-раскислителями (титаном, алюминием, цирконием и др.) приводит к уменьшению разбрызгивания при сварке. В настоящее время ведется разработка таких проволок.
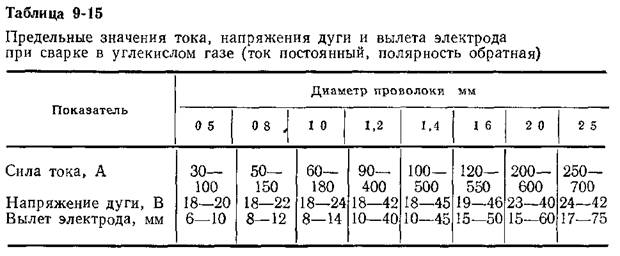
Устойчивое горение дуги при сварке плавящимся электродом в углекислом газе достигается при плотности тока свыше 100 А/мм2 (табл. 9-15).
При сварке в положениях, отличных от нижнего, применяют только электродную проволоку диаметром 0,5—1,4 мм Значения тока и напряжения дуги должны быть минимальными (17—21 В), однако обеспечивающими устойчивое горение дуги Увеличение напряжения дуги приводит к резкому возрастанию разбрызгивания и нарушению процесса, особенно при сварке горизонтальных швов
Забиваем Сайты В ТОП КУВАЛДОЙ - Уникальные возможности от SeoHammer
Каждая ссылка анализируется по трем пакетам оценки: SEO, Трафик и SMM.
SeoHammer делает продвижение сайта прозрачным и простым занятием.
Ссылки, вечные ссылки, статьи, упоминания, пресс-релизы - используйте по максимуму потенциал SeoHammer для продвижения вашего сайта.
Что умеет делать SeoHammer
— Продвижение в один клик, интеллектуальный подбор запросов, покупка самых лучших ссылок с высокой степенью качества у лучших бирж ссылок.
— Регулярная проверка качества ссылок по более чем 100 показателям и ежедневный пересчет показателей качества проекта.
— Все известные форматы ссылок: арендные ссылки, вечные ссылки, публикации (упоминания, мнения, отзывы, статьи, пресс-релизы).
— SeoHammer покажет, где рост или падение, а также запросы, на которые нужно обратить внимание.
SeoHammer еще предоставляет технологию Буст, она ускоряет продвижение в десятки раз,
а первые результаты появляются уже в течение первых 7 дней.
Зарегистрироваться и Начать продвижение
Автоматическую сварку в нижнем положении можно выполнять на максимальном токе Полуавтоматическую сварку в нижнем положении выполняют сварочной проволокой диаметром 0,5—2,5 мм при средних значениях тока и минимальном значении
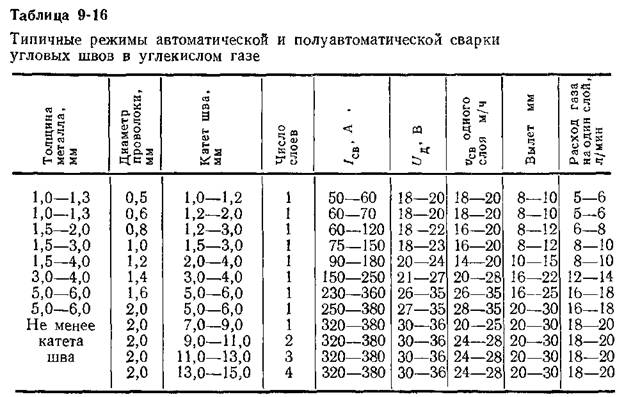
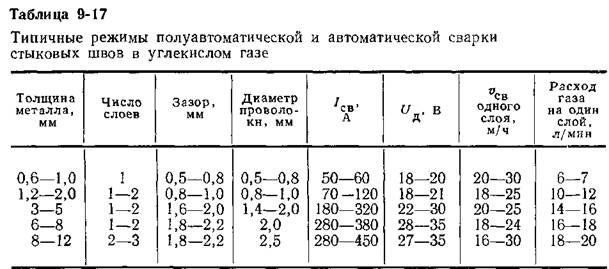
напряжения, указанных в табл. 9-16 и 9-17. При этом обеспечивается минимальное окисление и разбрызгивание металла.
Сварку стыковых и угловых швов обычно выполняют с перемещением конца электрода (рис. 9-8). Амплитуду колебания конца электрода выбирают в зависимости от требуемой ширины валика, толщины металла и формы разделки кромок. При повышенных зазорах между кромками полуавтоматическую сварку тонкого металла можно производить путем периодических кратковременных выключений подачи проволоки. Перерывы процесса обычно составляют 0,25—0,5 с. При сварке с перерывами ванночка подстуживается и не вытекает через зазор. Вследствие легкости возобновления процесса и кратковременности перерывов дефекты в швах не образуются.
При сварке низкоуглеродистой стали в углекислом газе обеспечиваются вполне удовлетворительные свойства металла шва (табл. 9-18).
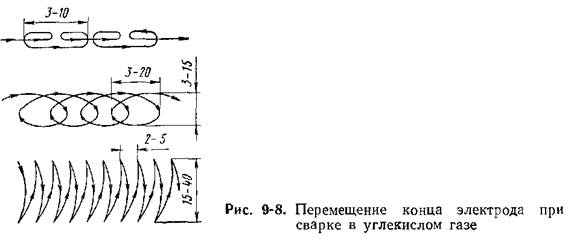
При сварке в среде углекислого газа используют также следующие порошковые проволоки: ПП-АН4 и ПП-АН8 диаметром 2,3; 2 и 3 мм. Сварку выполняют при нижнем, наклонном и горизонтальном расположениях на постоянном токе обратной полярности при питании от источников с жесткой внешней характеристикой (для проволоки диаметром 2 и 2,3 мм /св = 180-500 А, 1?д = 25ч---47 В).
Проволоку ПП-АН8 диаметром 3 мм можно применять при сварке на переменном токе при большой мощности дуги (/св = 400-600 А, £/д = 25-38 В). При сварке в углекислом газе порошковой проволокой обеспечивается более пластичный металл шва, улучшается
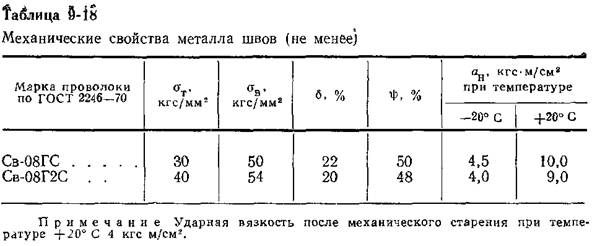
формирование и уменьшается разбрызгивание по сравнению со сваркой проволокой сплошного сечения Св-08Г2С.
Получает также применение сварка без защитного газа проволоками сплошного сечения и порошковыми, содержащими нитридообразующие и редкоземельные элементы (титан, алюминий, церий, цирконий и др.)* Сварочные проволоки этих марок, например Св-20ГСТЮА и Св-15ГСТЮЦА (ГОСТ 2246—70), легированные церием и цирконием, обеспечивают получение механических свойств металла шва на уровне свойств, обеспечиваемых электродами типа Э50. При сварке в углекислом газе проволокой 20ГСТЮА улучшаются технологические показатели процесса по сравнению с проволокой Св-08Г2С: увеличивается стабильность горения дуги, уменьшается разбрызгивание, а свойства металла шва удовлетворяют требованиям, обеспечиваемым электродами типа Э50.
Сварка неплавящимся электродом в углекислом газе находит ограниченное применение при изготовлении конструкций из стали толщиной 0,3—2 мм. Сталь большей толщины этим способом обычно не сваривают, так как с увеличением размеров сварочной ванны затрудняется защита ее от воздуха, возрастает степень окисления металла шва, ухудшаются его механические свойства и снижается стойкость против образования кристаллизационных трещин. Сварку выполняют угольными или графитовыми электродами на постоянном токе прямой полярности. Сварка на обратной полярности недопустима вследствие науглероживания металла шва. Неплавящимся электродом чаще всего сваривают соединения с отбортовкой кромок.
Низкое содержание марганца и кремния в составе шва, сваренного неплавящимся электродом в углекислом газе, приводит к тому, что прочность соединения обычно составляет 50—70% прочности основного металла. Однако в ряде случаев такие свойства приемлемы.
Для повышения производительности (скорости) сварки наряду с применением многодуговых процессов (см. гл. 3) в последние годы находят применение способы сварки с поперечными колебаниями электрода, сварка с заполнением разделки металлическими добавками (рубленой проволокой, металлическими окатышами и т. п.) подогрев вылета электрода проходящим током или током от независимого источника, сварка с высокотемпературным подо* гревом изделия и т. д. Все перечисленные методы повышения производительности сварки основаны на уменьшении давления дуги на сварочную ванну и повышении давления жидкого металла ванны.
Электрошлаковая сварка. Электрошлаковую сварку применяют при изготовлении конструкций из низкоуглеродистых сталей большой толщины.
Получение равнопрочного соединения при электрошлаковой сварке низкоуглеродистой стали достигается за счет легирования металла шва через проволоку в основном с повышенным содержанием марганца (Св-10Г2), а иногда также и кремния (Св-08ГС).
Для низкоуглеродистой стали с содержанием до 0,18% С равно прочность металла шва с основным металлом достигается при сварке проволокой Св-08ГА. Можно вести сварку двумя и тремя проволоками разного состава. Обычно применяют флюсы АН-8 или ФЦ-7.
При сварке кипящей низкоуглеродистой стали высокая стойкость металла шва против образования пор достигается при применении проволоки Св-10Г2 или Св-08ГС. Сварка проволоками
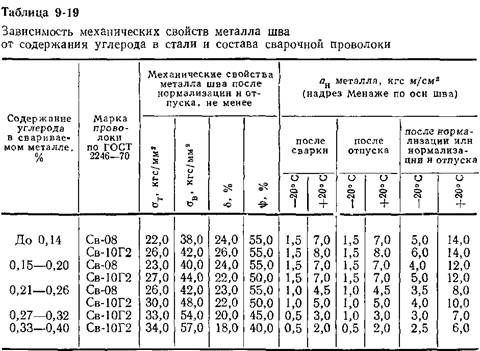

Св-08ГА и Св-08 не обеспечивает необходимого качества металла шва — шов поражен порами. Данные табл. 9-19 (для сравнения приведены результаты для среднеуглеродистой стали) свидетельствуют о том, что при электрошлаковой сварке (толщина металла более 60 мм, флюс АН-8) обеспечивается равнопроч-ность металла шва и сварного соединения в состоянии как после сварки, так и после термообработки. Ударная вязкость металла шва и участка перегрева околошовной зоны в состоянии после сварки при комнатной температуре находится на нижнем уровне требований, предъявляемых к основному металлу, а при температуре ниже комнатной обычно не удовлетворяет требованиям, предъявляемым к основному металлу. Это связано с образованием крупнозернистой видманштеттовой структуры (размер зерен на участке перегрева превышает размеры, предусмотренные шкалой ГОСТ 5639—65). Металл с видманштеттовой структурой обладает пониженной ударной вязкостью и малой стойкостью против перехода в хруцкое состояние.
Образование видманштеттовой структуры зависит от содержания в металле углерода, размера зерна аустенита и скорости остывания металла (рис. 9-9). При средней величине зерна и содержании 0,15—0,35% С образование видманштеттовой структуры происходит при скоростях остывания более 100° С в минуту. При большей величине зерна образование видманштеттовой структуры наблюдается даже при весьма малых скоростях остывания.
Сервис онлайн-записи на собственном Telegram-боте
Попробуйте сервис онлайн-записи VisitTime на основе вашего собственного Telegram-бота:
— Разгрузит мастера, специалиста или компанию;
— Позволит гибко управлять расписанием и загрузкой;
— Разошлет оповещения о новых услугах или акциях;
— Позволит принять оплату на карту/кошелек/счет;
— Позволит записываться на групповые и персональные посещения;
— Поможет получить от клиента отзывы о визите к вам;
— Включает в себя сервис чаевых.
Для новых пользователей первый месяц бесплатно.
Зарегистрироваться в сервисе
При электрошлаковой сварке низкоуглеродистых сталей из-за длительного пребывания металла при температуре аустенизации образуются крупные аустенитные зерна. Это способствует возникновению видманштеттовой структуры даже при малых скоростях охлаждения металла, имеющих место при этом виде сварки. Для видманштеттовой структуры характерно выделение феррита как по границам исходных аустенитных зерен, так и внутри зерна по определенным кристаллографическим плоскостям и направлениям в виде игл-(рис 9-10). Значение ударной вязкости металла электрошлакового шва и участка перегрева околошовной зоны
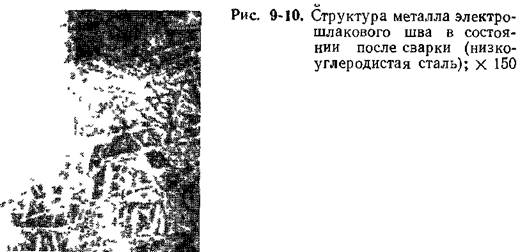
на уровне свойств основного металла в большинстве случаев обеспечивается только после нормализации сварной конструкции, приводящей к устранению видманштеттовой структуры и измельчению зерна.
После термообработки шов имеет структуру феррита и сорбитообразного перлита, распределенного неравномерно и ориентированного по осям столбчатых кристаллитов. Размер зерен соответствует номеру 7-8 по ГОСТ 5639—65.
Высокий отпуск не приводит к повышению значения ударной вязкости металла шва и околошовнои зоны, так как видманштет-товая структура сохраняется и после отпуска. Некоторое повышение ударной вязкости металла электрошлакового шва достигается путем модифицирования, использования ультразвуковых колебаний, электромагнитного перемешивания, механической вибрации ванны и других приемов. Однако при этом остается нерешенной задача повышения ударной вязкости на участке перегрева околошовной зоны. Поэтому в тех случаях, когда по условиям эксплуатации конструкции необходимо обеспечить высокую ударную вязкость металла шва к околошовной зоны при температурах ниже комнатной, ее следует подвергать общей или местной нормализации с последующим общим отпуском для снятия напряжений. В последние годы разработаны и находят применение более экономичные, по сравнению с полной нормализацией, приемы повышения ударной вязкости сварного соединения, выполненного электрошлаковой сваркой. К их числу относится сварка с пониженной погонной энергией и сопутствующей нормализацией металла сравнительно небольшой толщины (до 40 мм). Эта нормализация состоит в том, что на участке сварного соединения, остывшем примерно до температуры 500° С, устанавливают дополнительные нагреватели (горелки, индукторы и др.). Перемещаясь со скоростью сварки, они нагревают металл сварного соединения до температуры нормализации. Находит также применение нормализация сварного соединения в интервале более низких температур (Ас3—Асу).
Для предотвращения образования видманштеттовой структуры при электрошлаковой сварке ведутся также работы по применению основного металла с наследственно мелким аустенитным зерном и по легированию его элементами, снижающими склонность стали к перегреву.
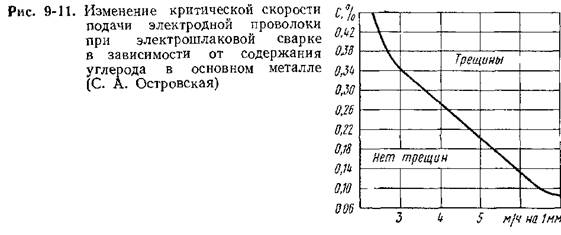
трещины возникают уже при содержании в металле
шва 0,15% С. При i|) = 3 содержание углерода в металле шва при прочих равных условиях может быть повышено до 0,22—0,23% без опасности образования кристаллизационных трещин. Форма сварочной ванны определяется режимом сварки (см. гл. 2). Поэтому для обеспечения высокой стойкости металла шва против образования трещин следует соответствующим образом выбирать режим сварки и в первую очередь скорость подачи электродной проволоки, от которой зависит глубина металлической ванны.
Данные о характере изменения критической скорости подачи электродной проволоки диаметром 3 мм в зависимости от содержания углерода в основном металле при средни значениях напряжения процесса приведены на рис. 9-11. Они относятся к случаю сварки углеродистой конструкционной стали толщиной 60— 200 мм. Содержание марганца, кремния и серы находится в пределах, предусмотренных соответствующими стандартами. Зазор между кромками 25—30 мм. При меньшей толщине металла благодаря особому характеру кристаллизации металла шва (§ 10) величина критической скорости подачи может быть заметно (на 15—25%) повышена. При большей толщине металла скорость подачи должна быть понижена. Степень понижения скорости подачи определяется опытным путем. Для удобства расчета критическая скорость подачи отнесена к 1 мм толщины основного металла.
Выбор режима электрошлаковой сварки обычно ведут по такой схеме. Допустим, необходимо сварить углеродистую сталь с содержанием 0,26% С, толщиной S = 120 мм. Из зависимости, приведенной на рис. 9-11, определяем, что критическая скорость vKp подачи электродной проволоки при таком содержании углерода равна 4,25 м/ч на 1 мм. Суммарную скорость подачи электродной проволоки определяют по уравнению

Сварку металла толщиной 120 мм можно вести двумя или тремя электродами. Скорость подачи каждой электродной проволоки иэл:

где п— число электродов.
Для нашего случая и9л = 255 м/ч при сварке двумя электродами и уэл = 170 м/ч при сварке тремя электродами. Зная критическую скорость подачи электрода, можно определить скорость сварки vCB по уравнению

где Fup — сечение электродной проволоки, мм2; а— ширина зазора, мм.
Для нашего случая при зазоре между свариваемыми кромками, равном 28 мм, и проволоке диаметром 3 мм

Остальные параметры режима сварки выбирают в каждом отдельном случае в зависимости от условий ведения процесса. Приведенные на рис. 9-11 данные могут служить только для ориентировочного выбора режима и в зависимости от конкретных условий сварки изменяются в некоторых пределах. Выбор числа электродов в зависимости от толщины свариваемого металла производится в соответствии с данными, приведенными в §3-5.
Ниже для примера приведен применяемый на практике режим сварки прямолинейных и кольцевых швов конструкций, изготовляемых из низкоуглеродистой стали. Указанный режим относится к сварке погонной части кольцевого шва. Сварку участка шва, замыкающего кольцевой шов, ведут при другом режиме.
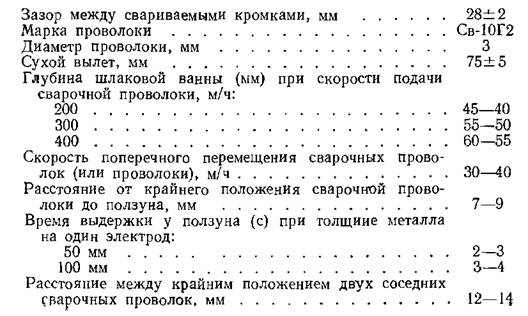
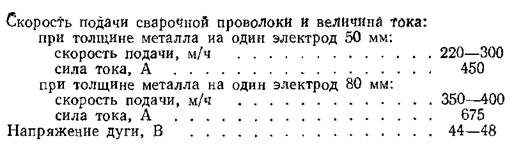
При выборе режима сварки пластиной или плавящимся мундштуком основное внимание уделяют обеспечению стойкости металла шва против кристаллизационных трещин, обеспечивая оптимальное соотношение между формой шва и содержанием в нем углерода.
|