Технология электрической сварки металлов и сплавов плавлениемОсобенности сварки высоколегированных сталей и сплавов
Металлургические особенности сварки высоколегированных сталей и сплавов. Высоколегированные стали и сплавы составляют наиболее многочисленную группу конструкционных материалов. Только в СССР в эту группу входит более 1500 марок сталей и сплавов. При таком их многообразии задачи сварки и термообработки высоколегированных сталей и сплавов представляют значительные трудности. Весьма важно поэтому научиться распознавать, к какому структурному классу относится сталь или сплав, и при помощи соответствующих диаграмм проследить возможные изменения структуры и образования фаз в околошовной зоне при сварке или в самой стали при термообработке. Это позволит более правильно назначать технологию сварки и термообработки узлов и конструкций.
Структура хромоникелевых сталей, сплавов и сварных швов определяется соотношением эквивалентного содержания ферри-тизирующих (Сг, Si, Mo, Ti, Al, Nb, W, V) и аустенитизирующих (Ni, Co, C, N, Си, Мп, В) элементов. Для определения структуры хромоникелевых швов пользуются диаграммой Шеффлера (рис. 10-24). Эта диаграмма может быть также применена для ориентировочного определения структуры сталей.
Структура и свойства хромистых сталей и сварных швов зависят от содержания хрома и углерода, а также от степени легирования их другими элементами. Рассмотрим влияние легирующих элементов на структуру высоколегированных сталей, сплавов и сварных швов.

никеля [Ni] может быть подсчитана по формулам
В правой части уравнения химические символы означают процентное содержание данных элементов в металле шва. Эти эмпирические формулы являются приближенными. Например, в некоторых источниках коэффициент ферритизирующего действия молибдена оценивается 1, в других— 1,5, в третьих — 3. Различные коэффициенты также приведены для вольфрама, ниобия, титана и марганца. Несовпадение данных объясняется тем, что влияние элементов на смещение границы у-области зависит не только от абсолютного их содержания, но и от содержания других элементов, термообработки и ряда других факторов.
Тем не менее этими формулами можно пользоваться с достаточной для практики точностью. Для примера на диаграмме Шеффлера (см. рис. 10-24) показаны структурное положение 1 металла, наплавленного электродами ОЗЛ-14 (06Х20Н9), и возможное положение 2 при сварке проволокой Св-10Х16Н25АМ6 без учета угара элементов, имеющего место при сварке. Структура металла, наплавленного проволокой Св-10Х16Н25АМ6, является чистоаустенитной; в металле, наплавленном электродами ОЗЛ-14, содержится около 8% феррита.
На величину эквивалентов [Сг] и [Ni] для сталей и сплавов оказывают влияние не только соотношение содержаний элементов и режим термообработки, но и состояние стали (прокат, литье), величина зерна и др. Для катаных сталей эквиваленты хрома и никеля выражаются следующими формулами:

Эти формулы еще более приближенные, чем формулы для сварных швов.
Исходя из условий эксплуатации стали назначают технологию ее сварки. Если сталь Х18Н10Т используют в качестве коррози-онностойкого материала, для сварки следует применитьэлектроды, обеспечивающие получение швов с аустенитно-ферритной структурой например ОЗЛ-14). Если же сталь используют для изготовления хладостойкой аппаратуры, предпочтение следует отдать чистоаустенитным электродам или электродам с ограниченным содержанием феррита, например ЗИФ-1 (08Х18Н9Г6) типаЭА-1Г6. Естественно, что при выборе технологии сварки учитывают и другие факторы: стойкость наплавленного металла против образования трещин, прочность, коррозионную стойкость и др.
К числу основных трудностей, которые приходится преодолевать при сварке высоколегированных сталей и сплавов, относятся: обеспечение стойкости металла шва и околошовной зоны против образования трещин; обеспечение коррозионной стойкости сварных соединений; получение и сохранение в процессе эксплуатации требуемых свойств сварного соединения; получение плотных швов.
Обеспечение стойкости металла шва и околошовной зоны против образования трещин. При сварке высоколегированных сталей и сплавов возможно образование горячих и холодных трещин. Горячим трещинам подвержены в основном аустенитные стали и сплавы, холодным — закаливающиеся стали мартенситного и мартенситно-ферритного классов.
Кристаллизационные и горячие трещины при сварке высоколегированных сталей и сплавов могут образовываться в шве и околошовной зоне (рис. 10-25, 10-26). Механизм их образования такой же, как и при сварке обычных углеродистых конструкционных сталей (см. § 33). Однако высоколегированные стали и сплавы более подвержены кристаллизационным трещинам при сварке, чем углеродистые конструкционные стали.
Это объясняется следующими специфическими особенностями строения и условий кристаллизации высоколегированных швов* сильно развитой транскристаллитной направленной первичной микроструктурой; увеличенной литейной усадкой кристаллизующегося металла; значительными растягивающими напряжениями, действующими на сварочную ванну в процессе ее затвердевания; многокомпонентным легированием, усиливающим вероят-ность появления малых количеств легкоплавкой эвтектической составляющей на границах дендритов в момент завершения кристаллизации сварочной ванны.
На практике нашли применение следующие пути предотвращения кристаллизационных трещин в высоколегированных швах: создание в металле шва двухфазной структуры, ограничение в нем содержания вредных примесей и легирование такими элементами, как молибден, марганец, вольфрам; применение фтористо-кальциевых электродных покрытий и фторидных сварочных флюсов, применение различных технологических приемов.
Остановимся кратко на характеристике этих пугей. Образование в шве двухфазной структуры (аустенит и первичный феррит, аустенит и первичные карбиды, аустенит и боридная фаза эвтектического происхождения, аустенит и хромоникелевая эвтектика) способствует ее измельчению (см. рис. 10-26). В результате удается полностью или частично подавить транскристаллитную первичную структуру. Такие швы несравненно более стойки против образования кристаллизационных трещин, чем однофазные чисто-аустенитные
Чтобы получить двухфазное аустенитно-ферритное строение металла шва, обеспечивают в нем соответствующее соотношение содержания ферритизирующих и аустенитизирующих элементов. Это возможно с помощью структурной диаграммы (рис. 10-24). Удовлетворительная стойкость против образования кристаллизационных трещин достигается при наличии в металле шва 2—3% первичного б-феррита.
Забиваем Сайты В ТОП КУВАЛДОЙ - Уникальные возможности от SeoHammer
Каждая ссылка анализируется по трем пакетам оценки: SEO, Трафик и SMM.
SeoHammer делает продвижение сайта прозрачным и простым занятием.
Ссылки, вечные ссылки, статьи, упоминания, пресс-релизы - используйте по максимуму потенциал SeoHammer для продвижения вашего сайта.
Что умеет делать SeoHammer
— Продвижение в один клик, интеллектуальный подбор запросов, покупка самых лучших ссылок с высокой степенью качества у лучших бирж ссылок.
— Регулярная проверка качества ссылок по более чем 100 показателям и ежедневный пересчет показателей качества проекта.
— Все известные форматы ссылок: арендные ссылки, вечные ссылки, публикации (упоминания, мнения, отзывы, статьи, пресс-релизы).
— SeoHammer покажет, где рост или падение, а также запросы, на которые нужно обратить внимание.
SeoHammer еще предоставляет технологию Буст, она ускоряет продвижение в десятки раз,
а первые результаты появляются уже в течение первых 7 дней.
Зарегистрироваться и Начать продвижение
На этом принципе создано большинство сварочных материалов (электродов и проволок), предназначенных для сварки корро-зионностойких аустенитных сталей Х18Н10Т, Х18Н12Т, Х17Н13М2Т и жаропрочных Х16Н14 (ЭП17), Х16Н16 (ЭП184) и др.
Сварка аустеиутных сталей электродами и проволокой с содержанием феррита до 2—3% связана с определенными трудностями. Так, при чрезмерном проплавлении основного металла возможно образование в шве объемов металла с чистоаустенитной структурой, склонного к кристаллизационным трещинам. Поэтому на практике применяют сварочные материалы, обеспечивающие получение в металле шва свыше 2—3% феррита. Например, электроды ОЗЛ-8 (08Х20Н9) обеспечивают получение в наплавленном металле 3,5—8,5% феррита, электроды ЭА-400/10У (07Х18Н10Г2) — 2—8%, а проволока Св-06Х19Н10МЗТ — до 10%.
Для сварки корневых валиков многопроходных швов, когда доля основного металла в шве значительна, применяют присадочные материалы с более высоким содержанием феррита—порядка 5—10%; например, электроды ЦТ-15-1 (08Х20Н9Г2) дают 5,5— 9,0% феррита; ЦТ-16-1 (08Х20Н9ВБ) — 6,0—9,5% феррита. В некоторых случаях, например при сварке жаростойких аусте-нитных сталей типа 2Х25Н20С2, отличающихся исключительно высокой склонностью к образованию кристаллизационных трещин, для этих целей применяют сварочные электроды со значительно более высоким содержанием феррита. Так, электроды марки ГС-1 (10Х25Н9Г6С2), используемые для сварки корневых валиков этих сталей, дают в наплавленном металле 25—30% феррита.
Швы с повышенным содержанием первичного феррита более стойки против межкристаллитной коррозии. Причиной этого вида коррозии являются фазовые превращения в металле шва, сопровождающиеся обеднением пограничных слоев зерен и кристаллитов хромом в результате встречной диффузии углерода и хрома. Наличие первичного феррита в сварных швах вносит качественные изменения в этот процесс. Фазовые превращения в этом случае локализуются в объемах, занимаемых первычным ферритом, который, как известно, способен растворить больше хрома, чем аустенит. Вследствие этого обеднения пограничных слоев хромом до критических концентраций не происходит и такие швы обладают более высокой сопротивляемостью межкристаллитной коррозии.
Вместе с тем не следует забывать, что швы и стали с повышенным содержанием феррита более подвержены сигматизации в интервале температур 450—850° С, а следовательно, и потере пластичности, чем стали и швы с ограниченным содержанием феррита или чистоаустенитные. Поэтому для обеспечения служебных характеристик конструкций и узлов, работающих в интервале критических температур (преимущественно 450—650° С), содержание феррита в шве должно быть ограничено до 2—3%.
Это требование особенно тщательно должно соблюдаться при сварке конструкций, длительно работающих при этих температурах, например контуров атомных станций, высокотемпературных химических реакторов, паропроводов, поверхностей нагрева котлов и др. Для сварки таких конструкций разработаны сварочные проволоки и электроды со строго регламентированным содержанием феррита в пределах 2—5% (например проволоки Св-04Х17Н10М2 и Св-02Х17Н10М2-ВИ и электроды 48А-1 и 48А-2, созданные на базе этих проволок).
Измельчение структуры шва путем создания в нем ферритной фазы нашло широкое применение на практике. Однако этот путь предотвращения образования кристаллизационных трещин не может быть использован при сварке сталей с большим запасом аустенитности и тем более сплавов на железоникелевой и никелевой основах. Чтобы при сварке таких сталей и сплавов получить двухфазные аустенитно-ферритные швы, понадобилось бы ввести в них чрезмерно большое количество ферритизаторов. Это неизбежно повлекло бы за собой значительное изменение свойств твердого раствора и резкое падение пластичности металла шва. Поэтому на практике сварку стабильноаустенитных сталей и сплавов выполняют в основном чистоаустенитными или двухфазными аустенитно-карбидными и аустенитно-боридными швами, отличающимися более высокой стойкостью против охрупчивания при длительной эксплуатации. Представляет также значительный интерес сварка двухфазными швами с хромоникелевой эвтектикой.
Предотвращение образования кристаллизационных трещин в чистоаустенитных швах достигается: ограничением содержания вредных примесей — серы, фосфора, свинца, сурьмы, олова, висмута, а также таких элементов, как кремний, титан, алюминий и ниобий, способствующих образованию по границам кристаллитов легкоплавких прослоек; заменой части никеля марганцем; легированием шва молибденом, вольфрамом, танталом, азотом, рением. Положительное действие этих элементов на стойкость чистоаустенитных швов против образования кристаллизационных трещин широко освещено в специальной литературе.
Перечисленные пути предотвращения образования кристаллизационных трещин в чистоаустенитных швах используют при разработке сварочных материалов. В качестве примера можно привести нашедшие применение на практике сварочные проволоки Св-08Х21Н10Г6, Св-08Х20Н9Г7Т, 1Х16Н14Г7В2Б (ЭП462), Св-10Х16Н25АМ6 с 0,1—0,2% азота, 06Х15Н30Г8В7МЗТ (ЭП235), 08Х25Н55В15Т (ЭИ868), Св-06Х15Н60М15 и созданные на их базе сварочные электроды ЗИФ-1 (13Х20Н9Г6Т), ЦТ-23 (16Х15Н15Г6В2Б), ЭА-395/9 (09Х15Н25АМ6), ЦТ-22 (06Х15Н35В7Г6ТЮ), НИАТ-7 (06Х21Н55М10В12), ЦТ-28 (08Х13Н65М15В4) и др.
Создание в металле шва двухфазной аустенитно-карбидной или аустенитно-боридной структуры как средства борьбы с кристаллизационными трещинами также довольно широко применяется на практике. Чтобы металл шва приобрел двухфазное аустенитно-карбидное строение, его легируют углеродом. Однако углерод оказывает резко отрицательное действие на коррозионную стойкость высоколегированных сталей, сплавов и сварных швов. Поэтому к указанному средству повышения стойкости шва против образования кристаллизационных трещин при сварке нержавеющих сталей можно прибегать только при условии одновременного легирования их такими элементами, как ниобий и титан, способными связать углерод в прочные карбиды.
Сервис онлайн-записи на собственном Telegram-боте
Попробуйте сервис онлайн-записи VisitTime на основе вашего собственного Telegram-бота:
— Разгрузит мастера, специалиста или компанию;
— Позволит гибко управлять расписанием и загрузкой;
— Разошлет оповещения о новых услугах или акциях;
— Позволит принять оплату на карту/кошелек/счет;
— Позволит записываться на групповые и персональные посещения;
— Поможет получить от клиента отзывы о визите к вам;
— Включает в себя сервис чаевых.
Для новых пользователей первый месяц бесплатно.
Зарегистрироваться в сервисе
На практике аустенитно-карбидные композиции нашли применение преимущественно при сварке жаропрочных и жаростойких
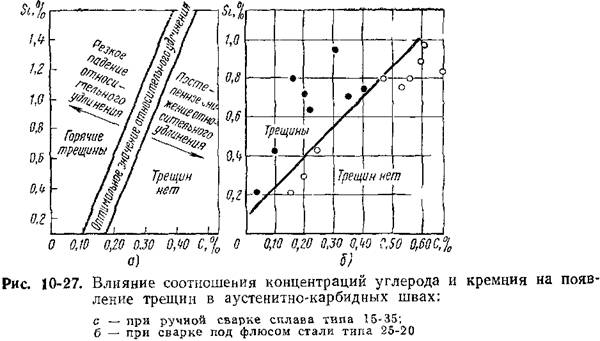
сталей. На этом принципе, например, построены электроды КТИ-7-62 типа ЭА-4ВЗБ2 (наплавленный металл ЗХ15Н35ВЗБ2 с 0,25—0,32% С) для сварки жаропрочного сплава ХН35ВТ (ЭИ612), электроды ОЗЛ-9-1 (наплавленный металл ЗХ25Н18 с 0,15—0,25% С) и сварочная проволока Св-30Х25Н16Г7 для сварки жаростойких сталей типа 25-20.
В аустенитно-карбидных швах, так же как в чистоаустенит-ных, для повышения их стойкости против образования кристаллизационных трещин ограничивают содержание кремния до 0,3— 0,4%, а также снижают содержание серы и фосфора. Содержания углерода и кремния при этом рекомендуется поддерживать в определенных соотношениях (рис. 10-27).
Для создания в шве двухфазной аустенитпо-боридной структуры достаточно легировать его бором в количестве более 0,2%. Важным преимуществом аустенитно-боридных швов является возможность повышения в них содержания кремния без боязни образования в них кристаллизационных трещин. Например, в чистоаустенитных швах типа Х14Н18В2Б кристаллизационные трещины обычно образуются уже при содержании 0,3—0,35% Si. Легирование этих швов бором в количестве 0,32—0,36% позволило повысить в них содержание кремния до 0,56%, и трещины при этом не образовывались. Критическая скорость деформации швов первого состава при испытании их по методике ИМЕТ-П оказалась равной нулю, а второго — возросла до 3,5 мм/мин. Чем больше кремния в шве, тем выше должна быть концентрация бора. Так, для предотвращения образования кристаллизационных трещин в швах типа Х25Н20С2 с 2,5—3% Si содержание бора должно быть в пределах 0,4—0,7%.
На этом принципе созданы сварочная проволока 08Х25Н20СЗР1 (ЭП532) и электроды ОЗЛ/АНЖ-16, дающие наплавленный металл
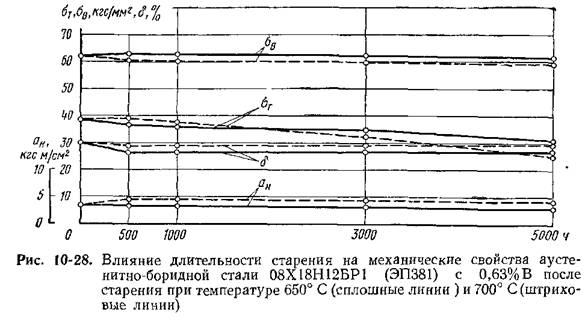
типа 08Х25Н20С2Р1 с 0,4—0,60% В для сварки жаростойких сталей типов Х25Н20С2, 4Х18Н25С2 и сплавов типа ЗХ18Н35СЗ.
При содержании выше 0,8—1,0% В в швах и околошовной зоне возможно образование холодных трещин. Устранение их достигается предварительным и сопутствующим подогревом сварного соединения до температуры выше 250—300° С.
Бор в указанных концентрациях повышает прочность и жаропрочность аустенитных сталей и сварных швов при сохранении достаточно высокой и, что очень важно, стабильной во времени длительной пластичности (рис. 10-28, 10-29).
Ауетенитно-боридные стали и сплавы применяют преимущественно в качестве жаропрочных и жаростойких конструкционных материалов. Возможно их применение также и в качестве корро-зионностойких материалов. Выявлено положительное влияние боридной фазы на стойкость аустенитных сталей и сварных швов против коррозионного растрескивания в некоторых хлоридосодер-жащих средах, в частности в хлористом магнии и морской воде.
Наличие хромоникелевой эвтектики в металле шва способствует измельчению его структуры и повышению стойкости против образования кристаллизационных трещин.
В бинарной системе Cr—Ni хромоникелевая эвтектика образуется при 49% Ni. Однако в реальных сплавах, содержащих в качестве примесей или легирующих элементов марганец, кремний, вольфрам, молибден и другие элементы, хромоникелевая эвтектика образуется и при меньших содержаниях никеля. Естественно, что это не чистая хромоникелевая фаза, она, подобно боридной фазе, содержит в себе значительные количества примесей и легирующих элементов. Известен ряд хорошо сваривающихся зарубежных и советских сплавов этого типа ХН50 (ЭП668), ХН35В (ЭП468) и др.
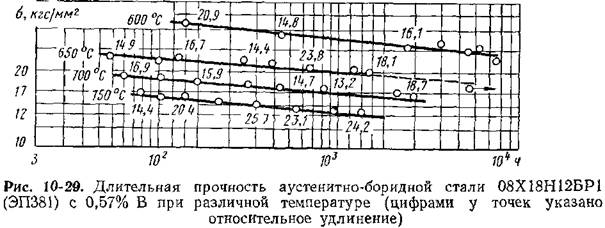
Сварочная проволока из сплава ЭП668 обеспечивает получение двухфазных (аустенит и хромоникелевая эвтектика) швов, стойких против образования кристаллизационных трещин.
Высокохромистые сплавы и сварные швы коррозионностойки при высоких температурах вплоть до 1000—1200° С в серосодержащих (H2S, S02 и др.) средах, в топочных газах, имеющих в своем составе V205 (вызывает так называемую ванадиевую коррозию), и в некоторых средах, содержащих активные азот или хлор, например, в хлористом нитрозиле NOC1.
Применение фтористо-кальциевых электродных покрытий и фторидных сварочных флюсов способствует измельчению структуры металла шва и повышению в результате этого его стойкости против образования кристаллизационных трещин. Электроды с основным покрытием и фторидные флюсы по этой причине нашли преимущественное применение при сварке высоколегированных сталей и сплавов.
Помимо перечисленных чисто металлургических средств находят применение некоторые технологические приемы повышения стойкости высоколегированных швов против образования кристаллизационных трещин. Эти приемы в основном рассчитаны на изменение формы шва и характера кристаллизации металла.
Особенность дуговой сварки высоколегированных сталей заключается в том, что в ряде случаев стойкость металла шва против образования кристаллизационных трещин падает с увеличением коэффициента формы шва (рис. 10-30). При электрошлаковой сварке пластинчатым электродом некоторых высоконикелевых
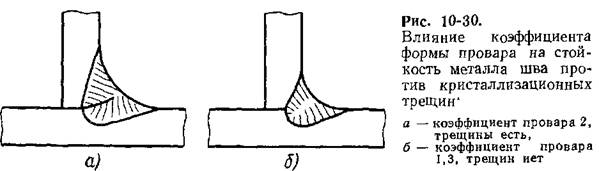
сплавов (ЭИ435 и др.), наоборот, уменьшение коэффициента формы шва приводит к образованию кристаллизационных трещин, аналогично тому, что наблюдается при сварке углеродистых и низколегированных сталей. Металл шва в этом случае кристаллизуется в виде елочки и кристаллиты в осевой его части соприкасаются торцами. В этом месте чаще всего образуются кристаллизационные трещины. При большом коэффициенте формы шва (порядка 2,5—3,5) кристаллиты растут в перпендикулярноосевом направлении и трещины в таком шве не образуются.
При дуговой сварке тавровых соединений из высоколегированных сталей и сплавов увеличение зазора при сборке до 1,5—2 мм благоприятно влияет на характер кристаллизации металла в корне шва. В результате образования кристаллизационных трещин в корне шва не происходит (рис. 10-31). Аналогичное явление наблюдается при сварке соединений типа клавишной пробы. Например, увеличение зазора между лопатками газотурбинного ротора позволяет повысить стойкость шва против образования поперечных трещин, идущих от зазора. Узкий зазор в этих случаях играет роль острого надреза, инициирующего трещину.
Опыт показывает, что влияние предварительного и сопутствующего подогревов сварного соединения высоколегированных сталей и сплавов может быть различным и зависит от их состава и свойств. В общем можно признать, что подогрев не оказывает сколько-нибудь заметного влияния на стойкость высоколегированных швов против образования кристаллизационных трещин.
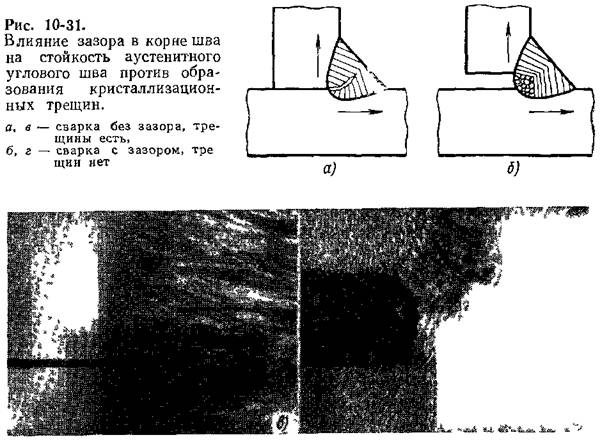
Более того, в ряде случаев он вреден вследстве увеличения провара основного металла и повышения в шве (в результате разбавления его основным металлом) концентрации кремния, серы, фосфора, ниобия и других элементов, вызывающих образование кристаллизационных трещин.
Подогрев полезен при сварке низкопластичных и литых высоколегированных сталей для предотвращения образования в сварных соединениях холодных трещин.
Большое влияние на образование кристаллизационных трещин в высоколегированных швах оказывает режим сварки. Швы, выполненные тонкой проволокой диаметром 1,2—2 мм на умеренных режимах при минимально возможных значениях погонной энергии сварки, обладают повышенной стойкостью против образования кристаллизационных трещин.
Во всех случаях сварки, независимо от структурного класса высоколегированных сталей и сплавов, предпочтение следует отдать сварочным материалам (проволокам, электродным стержням и покрытиям, флюсам) повышенной чистоты.
При сварке трудносвариваемых аустенитных сталей и сплавов обязательным является минимальное проплавление основного металла с целью недопущения повышения в шве концентрации кремния, меди, серы, фосфора, бора (речь идет о концентрациях до 0,1%), могущих вызвать в нем кристаллизационные трещины.
Большую опасность для эксплуатационной надежности конструкций представляют околошовные трещины, образующиеся при сварке плавлением высоколегированных сталей и сплавов. Сварщики научились получать качественные швы без трещин при сварке материалов этой группы. Однако значительно труднее предупредить образование околошовных трещин; как будет показано ниже, основная роль в решении этой задачи принадлежит металлургам, а не сварщикам.
При сварке плавлением высоколегированных сталей и сплавов в околошовной зоне возможны горячие строчечные, холодные и локальные трещины.
Горячие трещины (рис. 10-25, 10-32, 10-33, а) появляются в результате частичного расплавления в околошовной зоне по границам зерен или кристаллитов легкоплавких прослоек эвтектического происхождения и воздействия на околошовную зону напряжений, возникающих в результате сварочного нагрева. Таким трещинам особенно подвержены стали и сплавы с повышенным содержанием серы, фосфора, кремния, марганца в сочетании с медью, ниобия, легкоплавких примесей олова, сурьмы, свинца, до 0,1% бора (концентрация, при которой в стали еще не образуется сетка боридной фазы) и других элементов, способствующих образованию на границах зерен легкоплавких прослоек.
Мелкозернистые стали и сплавы менее подвержены околошовным горячим трещинам, чем крупнозернистые (см. рис. 10-32).
Особенно большие трудности в этом отношении встречает сварка крупнозернистых литых аустенитных сталей, например запорной энергетической арматуры из жаропрочных сталей типа 15-15, печных муфелей и катков из высококремнистых жаростойких сталей и сплавов 15Х25Н19С2Л, 20Х21Н46В8Л, ЗХ18Н35СЗ и др. К мерам борьбы с околошовными горячими трещинами относятся:
а) создание в околошовной зоне двухфазной структуры — ау-стенит и первичный феррит, аустенит и боридная фаза (рис. 10-33,6), аустенит и хромоникелевая эвтектика; применение этого способа связано с изменением композиции свариваемой стали и далеко не всегда возможно; б) повышение чистоты сталей и сплавов от вредных примесей (серы, фосфора) и ограничение или исключение в них элементов, инициирующих образование околошовных горячих трещин; в) применение чистых сварочных материалов с ограниченным содержанием элементов, вызывающих горячие трещины; г) применение мелкозернистых (с баллом 7—8 и мельче) сталей и сплавов.
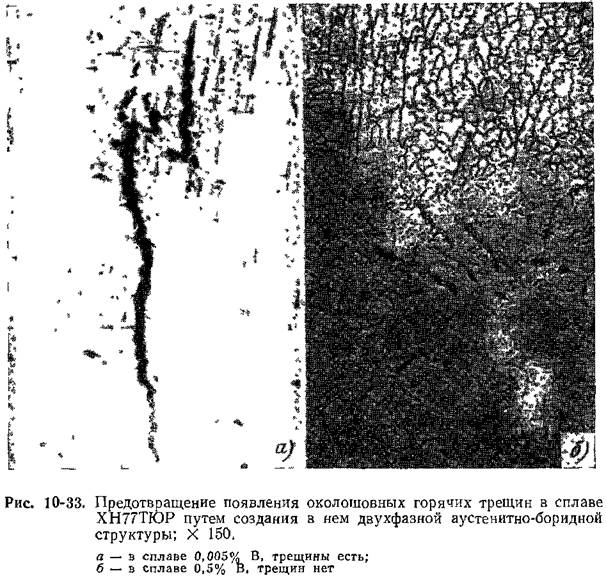
Для создания в околошовной зоне мелкозернистой структуры рекомендуется проковка кромок. Эта операция трудноконтроли-руема и недостаточно эффективна, однако в ряде случаев все-таки может быть использована.
Строчечные околошовные трещины обусловлены повышенной загрязненностью сталей и сплавов неметаллическими включениями и, преимущественно, строчечным их залеганием. Трещины этого типа, по-видимому, могут быть как горячими, так и холодными; носят они в основном межкристаллический характер (рис. 10-34, а, б).
Радикальным средством предотвращения образования околошовных строчечных трещин является повышение чистоты сталей и сплавов в отношении неметаллических включений. Эффективным средством борьбы с околошовными строчечными, а также и горячими трещинами в основном металле является электрошлаковый переплав (рис. 10-34, в, г). В этом отношении электрошлаковый переплав превосходит вакуумно-дуговой переплав, который не
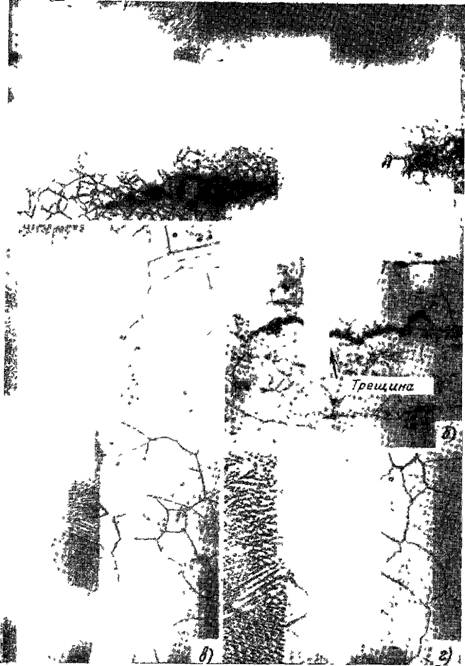
Рис. 10-34. Предотвращение околошовиых горячих и строчечных трещин путем повышения чистоты сплава методом электрошлакового переплава:
а, б — исходное состояние, трещины есть,
в, г, — после электрошлакового переплава, трещин нет,
а, в — сплав ХН77ТЮР (ЭИ437Б), X 70,
б, г — сплав ХН35ВТР (ЭИ725); Х150
позволяет полностью избавиться от строчечного скопления неметаллических включений.
Образование холодных трещин в шве и околошовной зоне возможно при сварке мартенситных и мартенситно-ферритных сталей, а также малопластичных сложнолегированных сталей и сплавов. Предварительный и сопутствующий подогревы до температур свыше 250—300° С предотвращают образование холодных трещин.
Ряд чистоаустенитных сталей (особенно легированных ниобием, титаном или с повышенным содержанием углерода) подвержены так называемым локальным разрушениям. Локальные разрушения — это трещины в околошовной зоне, возникающие в процессе длительной эксплуатации изделий при температурах старения сталей (550—700° С). Одной из причин их возникновения является снижение межзеренной пластичности аустенитной стали в результате воздействия сварочного нагрева.
Предложен ряд способов повышения стойкости аустенитных сталей против локальных разрушений: снижение содержания углерода в стали вплоть до предела его растворимости (0,02— 0,03%); исключение из состава стали ниобия; повышение запаса пластичности стали, например, с помощью электрошлакового переплава; применение присадочных материалов, обеспечивающих получение высокопластичных и менее прочных, чем основной металл, швов.
Обеспечение коррозионной стойкости сварных соединений. В качестве коррозионностойких материалов (табл. 10-16) широко применяют хромоникелевые аустенитные и 13-, 17- и 28%-ные хромистые стали, а также хромомарганцевые аустенитные, хромо-никелевые аустенитно-ферритные, аустенитно-мартенситные и аустенитно-боридные стали.
Оценку коррозионной стойкости металлов по ГОСТ 13819—68 производят по потере массы (пятибалльная шкала) или по глубинному показателю (десятибалльная шкала) (табл. 10-21).
Обладая высокой коррозионной стойкостью, аустенитные и хромистые стали подвержены опасному виду коррозионного разрушения межкристаллитной коррозии.
После воздействия на сталь или шов критических температур (500—800° С) выпадают комплексные карбиды железа и хрома. Выпадение этих карбидов влечет за собой обеднение хромом (ниже 10—12%) пограничных слоев зерен или кристаллитов твердого раствора и соответствующую потерю коррозионной стойкости металла. Существует также предположение, особенно в отношении хромистых сталей, что причиной межкристаллитной коррозии служат не обеднение хромом, а местные напряжения высшего порядка, возникающие на границах зерен в результате выпадения карбидов. Считают также, что карбиды эти богаты скорее железом, чем хромом. Поэтому разрушаются агрессивной жидкостью сами карбиды, а не обедненный хромом твердый раствор.
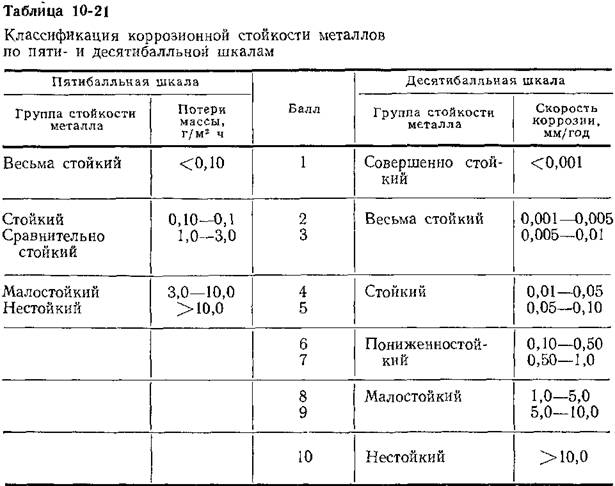
В процессе сварки отдельные участки околошовной зоны подвергаются нагреву до температур, могущих вызвать распад твердого раствора и выпадение карбидов. Впоследствии в этих участках может развиваться межкристаллитная коррозия. Меж-кристаллитная коррозия может поразить также участки шва, подвергавшиеся повторному воздействию сварочного нагрева, а именно места пересечения швов (рис. 10-35, а), места возобновления сварки после смены электродов (рис. 10-35, б), первый шов при двусторонней сварке (рис. 10-35, в, г). Этот вид коррозии может наблюдаться и на гр ани-це шов — основной металл в виде так называемой ножевой коррозии, охватывающей по ширине всего несколько зерен. Ножевая коррозия наблюдается преимущественно в сталях, стабилизированных титаном или ниобием.
Известны следующие средства борьбы с межкристаллитной коррозией при сварке высоколегированных сталей и сплавов.
Снижение содержания углерода в основном металле и металле шва до 0,02—-0,03%, т. е. до предела его растворимости в аустените. При столь малой концентрации углерод остается в твердом растворе при любой температуре, и выпадение карбидов хрома исключается.
Легирование сталей и швов титаном, ниобием, танталом, цирконием, ванадием. Обладая большим сродством к углероду, чем хром, эти элементы дают устойчивые карбиды. В результате карбиды хрома не образуются, и развитие межкристаллитной коррозии исключается.
Закалка (для сталей типа 18-10 от 1050—1100° С). При нагреве под закалку карбиды хрома растворяются в аустените, а быстрое остывание фиксирует однородное строение стали или сплава. Повторное воздействие критических температур в процессе сварки, естественно, может снова привести металл в состояние склонности к межкристаллитной коррозии.
Стабилизирующий отжиг в течение 2—3 ч при температуре 850—900° С с охлаждением на воздухе (для хромистых сталей отжиг при 760—780° С). Нагрев при указанных температурах приводит к наиболее полному выпадению карбидов и стабилизации их состава. При последующем воздействии более низких критических температур обеднения хромом вследствие выпадения карбидов не произойдет.
5. Повышение в швах содержания феррита до 20—-25% путем дополнительного легирования их хромом и такими элементами, как кремний, алюминий, ванадий, молибден, вольфрам.
Для предупреждения ножевой коррозии применяют также некоторые технологические приемы, направленные на недопущение или уменьшение перегрева металла в околошовной зоне. К ним относятся: сварка короткой дугой на максимальных скоростях; сварка очередного валика после полного остывания предыдущего; сварка слоя, обращенного к агрессивной среде, в последнюю очередь; охлаждение сварного соединения со стороны ранее заваренного шва и др. Термообработка сварных изделий далеко не всегда возможна, поэтому наиболее эффективными средствами предупреждения межкристаллитной коррозии являются снижение содержания в стали и шве углерода и легирование их такими энергичными карбидообразователями, как титан и ниобий.
Общая жидкостная коррозия шва и околошовной зоны возникает в результате воздействия агрессивного реагента на сварное соединение. Основными методами уменьшения этого вида коррозии являются сварка изделий швами идентичного с основным металлом состава и правильный выбор режима термообработки.
Аустенитные стали подвержены еще одному виду коррозии, так называемому коррозионному растрескиванию. Коррозионное растрескивание стали и сварных швов возникает в результате совместного воздействия растягивающих напряжений и агрессивных реагентов, в частности, хлоридных солей (MgCl2, NaCl) морской воды, бидистиллата, некоторых кислот.
Находят применение следующие меры предупреждения коррозионного растрескивания сталей и сварных швов: повышение в них содержания никеля более 40%; создание двухфазной аусте-нитно-ферритной или аустенитно-боридной структуры (содержание не менее 0,5—0,8% В); предупреждение коробления и наклепа сварного изделия, способствующих возникновению растягивающих напряжений в отдельных объемах металла.
Наклеп сварных конструкций и узлов из высоколегированных сталей и сплавов нежелателен. В местах наклепа коррозионная стойкость металла изменяется. Наклеп заметно повышает стойкость металла против межкристаллитной и общей коррозии в окислительных средах (азотная и хромовая кислоты), но может резко снизить ее в неокислительных средах (серная кислота). Избежать наклепа в производственных условиях трудно, поэтому термообработка сварных узлов в этих случаях желательна.
Обеспечение жаростойкости сварных соединений. Способность сталей, сплавов и сварных швов противостоять образованию окалины под действием высоких температур определяется их химическим составом и прежде всего содержанием хрома (см. табл. 10-17 и 10-18). При выборе системы легирования металла шва необходимо иметь в виду, что кремний и алюминий также энергично повышают жаростойкость металла, а ванадий и бор ее снижают. Вольфрам и молибден несколько ослабляют способность металла шва сопротивляться окалинообразованию. Марганец в пределах до 4—6% не оказывает заметного влияния на жаростойкость металла шва.
В общем случае при сварке жаростойких сталей и сплавов нужно стремиться приблизить композицию металла шва к составу основного металла.
|