Кузнечно-штамповочное оборудованиеВысокоскоростные газовые молоты
К настоящему времени разработано и воплощено в металле довольно много конструктивных схем высокоскоростных газовых молотов. По принципу действия схемы этих молотов можно разделить на двухкамерные и однокамерные.
В двухкамерном молоте (рис. 19.1) помимо рабочей камеры в цилиндре 3 имеется специальная емкость для аккумуляции газа высокого давления - азота с р= 14 МПа. Аккумуляционная камера отделена от рабочей распределительным органом - золотником 4, приводимым в движение от системы управления.
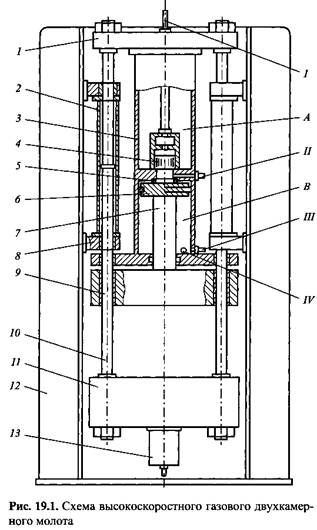
В представленном положении полость В заполнена через отверстие IV газом низкого давления и поршень 6 прижат к торцевому уплотнению 5. Золотник 4 смещен вниз под действием масла, нагнетаемого по трубке I в верхнюю полость золотниковой коробки, и перекрывает сопло из полости А в полость В.
Для пуска молота в сопло по трубке II поступает газ повышенного давления. Несмотря на низкое давление в полости 5, поршень при этом остается неподвижным, так как его площадь под соплом мала по сравнению с кольцевой площадью. Однако давление газа, поступившего по трубке II, все же достаточно велико, чтобы сдвинуть золотник вверх, и поэтому газ высокого давления из полости А через открывшиеся отверстия в золотниковой коробке и сопло врывается в рабочую камеру, отрывая поршень от кольца 5. В результате резко возрастают площадь, на которую действует этот газ, а следовательно, и сила. Подвижные части с большим ускорением начинают перемещаться вниз, достигая максимума скорости в конце хода перед началом штамповки.
Для подъема подвижных частей после удара в полость В под поршнем 6 через трубку III закачивается масло высокого давления. Расширившийся газ из части полости В над поршнем вытесняется в полость А с повторным сжатием (реком-прессией) до начального давления. Когда поршень прижат к кольцу 5 давлением масла, опускается золотник 4, разъединяя полости. После этого давление под поршнем в полости В падает, а газ низкого давления вытесняет масло. Молот вновь в исходном положении и готов к следующему удару.
Конструктивно молот оформлен таким образом. Станина 12 является несущим элементом и предназначена для компоновки всех узлов и деталей, но жестко на ней укреплены только опоры 8 с направляющими втулками. В них установлены две стяжные шпильки-колонны 70, образующие вместе с верхней 1 и нижней 11 базовыми траверсами раму молота. К верхней траверсе прикреплен рабочий цилиндр 3, а на нижней размещена нижняя половина штампа. Подвижные части молота состоят из поршня 6, штока 7 и подвижной траверсы 9 с верхней половиной штампа. Направляется подвижная траверса колоннами 10. На нижней стороне траверсы 11 смонтирован гидравлический цилиндр 13 выталкивателя.
В процессе истечения газа высокого давления через соединительное сопло возникает реактивный импульс, действующий на верхнюю крышку полости А цилиндра 8. В результате вся рама молота движется вверх. После удара вследствие упругого отскока, а затем под влиянием силы тяжести рама смещается вниз. Для того чтобы предупредить удар рамы при посадке на нижние фиксаторы, шпильки-колонны пропущены через демпфирующие гидроцилиндры 2 (гидро-пневмоцилиндры).
Подобное устройство молота обеспечивает благоприятную механику движения соударяющихся масс: подвижные части и рама встречаются в момент удара, обладая соразмерным количеством движения. Поскольку рама плавает относительно станины, гашение импульсной нагрузки происходит практически полностью внутри системы подвижные части - рама. Энергия же упругого восстановления после удара рассеивается в демпфере. Поэтому молот работает устойчиво несмотря на огромный уровень кинетической энергии по отношению ко всей массе машины. Силовая замкнутость и гашение виброколебаний в системе позволяют устанавливать молот на ставнительно небольшом фундаменте.
Процесс удара в высокоскоростном молоте происходит значительно быстрее, чем в паровоздушном. Поэтому удельная мощность рабочего хода на единицу массы высокоскоростной установки несравнимо превосходит таковую для обычного молота. Следовательно, важным отличием высокоскоростных газовых молотов является их очень низкая металлоемкость.
Однако, во-первых, высокоскоростные газовые молоты имеют усложненный индивидуальный привод. Например, в молоте по рассматриваемой конструктивной схеме в качестве энергоносителя применяют азот высокого и низкого давления, а также масло высокого давления. Азот поступает из баллонов, присоединяемых к цилиндру 3 (см. рис. 19.1) через систему газопроводов с регуляторами давления и прочей арматурой. Для подачи масла предназначается специальный насосный гидропривод. Во-вторых, детали высокоскоростных молотов, работающие в сложных условиях динамических нагрузок, приходится изготавливать из высококачественных сталей и других материалов. Требования к механической и термической обработке деталей также очень высоки. Поэтому стоимость единицы эффективной энергии удара у эквивалентных по мощности высокоскоростных газовых и паровоздушных штамповочных молотов примерно одинакова.
Необходимость совершать различные манипуляции с энергоносителями приводит к тому, что длительность цикла одного двойного хода у высокоскоростного газового молота довольно велика и доходит до 30...60 с в зависимости от размеров машины. Однако штамповка на таких молотах осуществляется за один удар, поэтому часовая производительность составляет 50... 120 поковок.
К настоящему времени выпущены высокоскоростные газовые молоты с энергией удара от 10 до 500 кДж.
В качестве примера однокамерной машины рассмотрим высокоскоростной газовый молот с эффективной энергией удара 160 кДж.
В комплекс установки молота входят: исполнительная машина (собственно молот); аккумуляторная газовая станция; гидропривод; системы газо-, воздухо-и маслопроводов с соответствующей арматурой, регулирующими и распределительными устройствами; пульт управления; электрооборудование и фундамент.
Забиваем Сайты В ТОП КУВАЛДОЙ - Уникальные возможности от SeoHammer
Каждая ссылка анализируется по трем пакетам оценки: SEO, Трафик и SMM.
SeoHammer делает продвижение сайта прозрачным и простым занятием.
Ссылки, вечные ссылки, статьи, упоминания, пресс-релизы - используйте по максимуму потенциал SeoHammer для продвижения вашего сайта.
Что умеет делать SeoHammer
— Продвижение в один клик, интеллектуальный подбор запросов, покупка самых лучших ссылок с высокой степенью качества у лучших бирж ссылок.
— Регулярная проверка качества ссылок по более чем 100 показателям и ежедневный пересчет показателей качества проекта.
— Все известные форматы ссылок: арендные ссылки, вечные ссылки, публикации (упоминания, мнения, отзывы, статьи, пресс-релизы).
— SeoHammer покажет, где рост или падение, а также запросы, на которые нужно обратить внимание.
SeoHammer еще предоставляет технологию Буст, она ускоряет продвижение в десятки раз,
а первые результаты появляются уже в течение первых 7 дней.
Зарегистрироваться и Начать продвижение
Исполнительная машина (рис. 19.2) компонуется из следующих узлов: рамы 3 с подвижными частями 5; станины 6 с ограждениями; цилиндров подъема 2 и выталкивателя 7; фиксаторов 4 и амортизаторов 7; клапана управления и системы смазки. Чтобы обеспечить требуемую прочность и жесткость, раму молота и подвижные части изготовляют цельноковаными из легированной стали 40ХНМА.
Установка рамы в станине допускает вертикальную подвижность. Для этого на боковых стойках рамы имеются направляющие пазы (рис. 19.3), а на станине -соответствующие планки.
В О-образном проеме рамы 1 размещена массивная траверса (баба) 4 подвижных частей. Точность движения траверсы относительно рамы обеспечивается направляющими - базовыми плоскостями у траверсы и регулируемыми планками 8
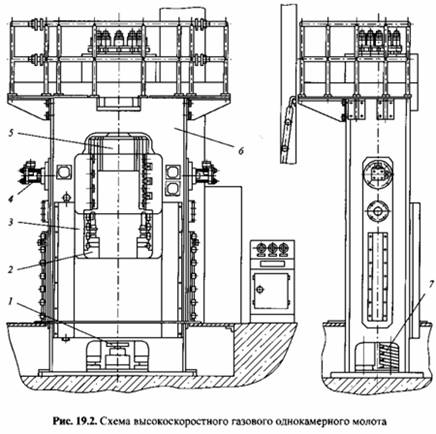
у рамы. В верхней поперечине рамы имеется сквозное отверстие для штока подвижных частей с дополнительным направлением по втулке 2. Снизу шток уплотнен верхней манжетой от утечки газа высокого давления, нижняя манжета предназначена для удержания смазочного слоя масла, поступающего из бачка под низким давлением. Направляющая втулка 2 крепится крышкой 3 буксы.
Головка рамы выполнена в форме пустотелого цилиндра и служит аккумуляционной газовой камерой. Для увеличения объема камеры внутри штока расточена полость. В шток ввинчивается крышка 77, снабженная сквозными боковыми отверстиями, соединяющими его внутреннюю полость с основной камерой цилиндра.
Сверху цилиндр закрыт крышкой 9, в пазу которой уложено резиновое кольцо 10. В это кольцо упирается острой выступающей кромкой крышка штока, когда он находится в КВП, отсекая тем самым замкнутую полость П очень небольшого объема между крышкой цилиндра и торцом штока.
Станина молота - закрытого типа, сварная (из листового проката). На внутренней стороне боковых листов расположены планки направляющих и стопорные ограничители хода рамы. В переднем и заднем листах имеются проемы, открывающие доступ к штамповому пространству. Для безопасности (на случай поломки инструмента) передний проем перекрывается подвижным ограждением, подъем которого осуществляется при помощи двух пневмоцилиндров. На задний проем ограждение навешивается вручную перед началом работы.
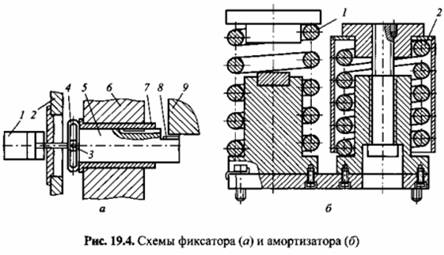
Фундаментная плита станины сделана прочной с ребрами жесткости и служит для крепления цилиндров подъема 5 и выталкивателя 6, а также амортизаторов 7.
Для удержания подвижных частей вверху при аварийном срабатывании системы предназначены два фиксатора (рис. 19.4, а), установленные по боковым сторонам траверсы. Ползушка 5 фиксатора направляется втулкой 7 в раме 6 молота. Приводной пневмоцилиндр 1 фиксатора крепится в прорези боковой стойки 2 станины. Кулисное соединение ползушки со штоком цилиндра сделано так, чтобы она могла перемещаться вместе с рамой молота по вертикали: прямая рамка 4 кулисы закреплена на ползушке, а сухарь 3 - на штоке. Зазор между фиксирующей лыской ползушки и нижней плоскостью траверсы 9 не должен превышать 1 мм, регулируется он при помощи сменной планки 8 на лыске.
Цилиндры подъема и выталкивателя представляют собой обычные гидравлические механизмы двойного действия.
Как и в предыдущей конструкции высокоскоростного газового молота, рама в процессе разгона подвижных частей несколько поднимается, а затем в результате отскока и под действием земного притяжения движется вниз. Для погашения кинетической энергии и плавной посадки на место предусмотрены два пружинных амортизатора, симметрично расположенные относительно оси молота. Каждый из амортизаторов состоит из пружины 1 в свободном состоянии, воспринимающей нагрузку первой, и пружины 2 с предварительной затяжкой, воспринимающей нагрузку второй (рис. 19.4, б). Различие в характеристиках пружин и, следовательно, в частотах колебаний придает амортизаторам некоторые демпфирующие свойства. Амортизаторы одновременно являются и фиксаторами КНП рамы.
В исходном положении (см. рис. 19.3) полости аккумуляционной камеры в цилиндре и штоке заполнены газом высокого давления. Полость сверху штока под крышкой цилиндра соединена с атмосферой, и поскольку на кольцевую часть штока снизу давит сжатый газ, возникающая при этом сила удерживает подвижные части в КВП. Ползушки фиксаторов выдвинуты под траверсу, штоки подъемных цилиндров и выталкивателя находятся внизу, доступ к штампам открыт. Рабочий укладывает заготовку в ручей и нажимает кнопку Удар. Тотчас срабатывает электромагнит воздухораспределителя цилиндров ограждения, впуская сжатый воздух из ресивера пневмосистемы. Двигаясь вверх, ограждение закрывает проем рамы и одновременно нажимает на конечный выключатель, управляющий воздухораспределителем фиксаторов. Ползушка уходит из-под траверсы, освобождая ей путь вниз, и тоже нажимает на конечный выключатель общей системы управления молотом со специальным клапаном управления (рис. 19.5).
В корпусе 5 клапана управления установлена втулка 3, к седлам которой притерты клапаны 2 и 4. Тарелки клапанов упираются в диафрагмы 1 и 6. Диафрагмы защемлены крышками на фланцах корпуса. Со стороны, противоположной тарелкам, диафрагмы поджимаются пружинами и благодаря этому при отсутствии избыточного давления в полостях А и Д клапаны оказываются посаженными на свои седла.
Полости А иДв головках клапана управления соединены с пневмосистемой молота, полость Г системой трубопроводов через входное отверстие Е соединена с аккумуляторной станцией, а через выходное отверстие В - с молотом; полость Б всегда соединена с атмосферой.
При срабатывании конечного выключателя от возвратного движения ползушки сжатый воздух из соответствующего воздухораспределителя поступает в полость Д, смещая клапан 4 вправо. Тогда сжатый газ из баллонов аккумуляторной станции устремляется через открытую полость Г в отсеченную под крышкой
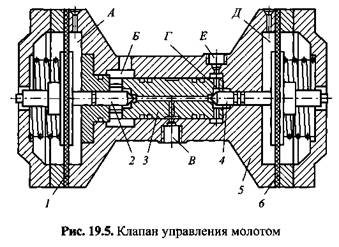
цилиндра полость П (см. рис. 19.3). Давление на шток возрастает настолько, что усилие оказывается достаточным для отрыва его от крышки цилиндра. Тотчас же начинается расширение сжатого газа, и подвижные части, все больше увеличивая скорость, движутся вниз вплоть до удара.
Сервис онлайн-записи на собственном Telegram-боте
Попробуйте сервис онлайн-записи VisitTime на основе вашего собственного Telegram-бота:
— Разгрузит мастера, специалиста или компанию;
— Позволит гибко управлять расписанием и загрузкой;
— Разошлет оповещения о новых услугах или акциях;
— Позволит принять оплату на карту/кошелек/счет;
— Позволит записываться на групповые и персональные посещения;
— Поможет получить от клиента отзывы о визите к вам;
— Включает в себя сервис чаевых.
Для новых пользователей первый месяц бесплатно.
Зарегистрироваться в сервисе
При отходе траверсы от КВП освобождается конечный выключатель, управляющий реверсивным золотником, и масло высокого давления от насоса направляется под поршни цилиндров подъема подвижных частей. Циклограмма молота построена так, что штоки подъемных цилиндров упрутся в траверсу и начнут ее поднимать только после того, как произойдет удар. Такое запаздывание обеспечивается малой скоростью на протяжении небольшого холостого хода штоков вверх. От действия того же конечного выключателя обесточивается электромагнит воздухораспределителя пневмосистемы ограждения и штампы открываются.
В процессе подъема траверса нажимает на конечный выключатель, от которого запитывается электромагнит второго реверсивного золотника гидросистемы. Смещение золотника открывает доступ маслу высокого давления под поршень выталкивателя.
Поскольку ход штоков всех трех гидроцилиндров ограничен (выталкиватель и траверса доходят до упора в КВП), давление в гидросистеме повышается сверх необходимого для извлечения поковки из ручья или подъема подвижных частей. Установленное в гидросистеме реле давления срабатывает и включает электромагнит воздухораспределителя пневмосистемы. Сжатый воздух от ресивера начинает поступать в левую полость А клапана управления (см. рис. 19.5). Клапан 2 сдвигается влево, открывая проход из полости В на выхлоп. В результате давление в полости П между крышкой цилиндра и штоком (см. рис. 19.3) сбрасывается и траверса зависает наверху.
От реле давления срабатывают также упомянутые ранее воздухораспределители фиксаторов, и ползушки выходят под траверсу. Ходом ползушек фиксаторов и толкателя клапана включаются сразу три конечных выключателя, подающие команду на движение в исходное КНП штокам цилиндров подъема и выталкивателя. А они, в свою очередь, блокируют систему управления таким образом, что на пульте загорается сигнальная лампа Готово к удару. Цикл завершен, и после нового нажатия на пусковую кнопку произойдет следующий удар.
Газовая аккумуляторная станция состоит из шести соединенных последовательно баллонов вместимостью 0,04 м каждый, причем давление сжатого азота в баллонах равно 15 МПа. При помощи регулятора давление азота снижается до расчетного р = 11 МПа в аккумуляционной камере молота. Рабочее давление воздуха в пневмосистеме 0,4 МПа.
Большой уровень аккумулированной в приводе энергии, разрядка которой при высоких скоростях движения подвижных частей происходит очень быстро, ставит особые требования к соблюдению правил безопасной эксплуатации высокоскоростных газовых молотов. Совершенно недопустимо проводить какие бы то ни было работы по подналадке штампов или затяжке креплений молота при расположении исполнительных частей в промежуточном положении и наличии при этом сжатого газа в цилиндре. Все это можно делать, когда траверса лежит либо в КВП на фиксаторах, либо в КНП на штампе.
Следовательно, полная работа, совершаемая газом при расширении в цилиндре,

- объемы, которые занимает газ соответственно в начале и в конце расширения.

имеют вид

Функцию Р определяем по адиабатическому соотношению

- площадь поперечного сечения штока.
Подстановка выражения (19.3) в систему (19.2) приводит к системе двух нелинейных уравнений.
Причем конечный эффект будет тот же, если переменную силу от расширяющегося газа заменить ее средним значением

- полный встречный ход исполнительных частей и рамы.
от ее начального и конечного значений:
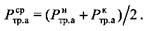
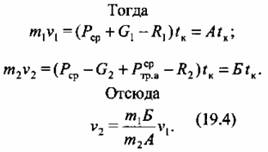
Работа всех внешних сил, действующих на подвижные массы, преобразуется в кинетическую энергию движения, и поэтому эффективная энергия удара

соответственно навстречу друг
другу. Иначе

Для определения перемещения масс из первого уравнения системы (19.2) вычтем второе и полученное уравнение дважды проинтегрируем, заменив силу ее средним значением. Тогда можно записать

Выражение (19.7) в конце хода будет иметь вид


Преобразуем уравнение (19.8) к виду

Дополнительным к нему уравнением служит выражение


Время движения масс от начала хода до удара рассчитываем по формуле

), при непрерывной работе молота запас сжатого газа в баллонах аккумуляторной станции исчерпывается. Число ходов п, на которое его хватит,
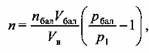
- давление сжатого газа в баллонах.
|