Кузнечно-штамповочное оборудованиеПадающие части
Номинальная МПЧ - главный размерный параметр - складывается из масс поршня, штока, бабы. Верхний боек, или штамп, не является деталью молота, регламентация его массы необходима для того, чтобы предупредить при эксплуатации утяжеление падающих частей сверх меры, приводящее к значительному изменению параметров молота. Так, ГОСТ 9752 на ковочные молоты допускает превышение номинала всего на 5 %. По ГОСТ 7024 на штамповочные молоты допускается увеличение фактической МПЧ относительно номинальной не более чем на 15 % без учета массы верхнего штампа. Масса же верхнего штампа не должна превышать 30 % от номинальной МПЧ.
Типовой узел падающих частей (рис. 16.8) состоит из раздельно выполненных поршня 2, штока 3, бабы 6 и более мелких соединительных деталей.
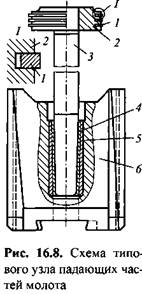
Длительный опыт эксплуатации штамповочных молотов показал целесообразность заклиненного конусного крепления поршня на штоке и штока в бабе. Прочность такого крепления обеспечивается достаточными нормальными напряжениями на поверхности контакта и соответствующим углом конусности а сопряжений (а= 1,25...2,30°). В результате значительные касательные силы, действующие в контакте, располагаются внутри конуса трения, наглухо заклинивая соединяемые детали.
Нормальные напряжения при посадке поршня на шток создаются вследствие линейной усадки по диаметру отверстия при охлаждении поршня, предварительно подогретого до 400...450°С. Расклепка верхнего торца штока не рекомендуется, так как она опасна в связи с ослаблением посадочного натяга. Шток с поршнем монтируют в рабочем цилиндре, выверяют установку бабы и сильным ударом с разгона забивают шток в бабу.
Крепление штока в бабе предусматривает установку в цилиндрическом гнезде бабы промежуточного разрезного стального стакана-сухаря 5. Поверхностная твердость материала стакана ниже твердостей материалов бабы и штока. Поэтому стакан воспринимает весь износ и при необходимости его заменяют. При сильных ударах нормальные напряжения становятся значительными и в конусном соединении при контакте стали со сталью может начаться необратимый диффузионный процесс. Выбить шток из бабы тогда трудно. Для предупреждения этого между штоком и стаканом кладут латунные или медные прокладки 4 толщиной 1 ...2 мм.
Для унификации у ковочных и штамповочных молотов применяют одинаковую конструкцию узла падающих частей.
Поршни молотов изготовляют коваными из стали 45 или 40ХН. Диаметр поршня в зависимости от его размера на 0,7...3 мм меньше внутреннего диаметра втулки рабочего цилиндра. Зазор необходим из-за различной степени теплового расширения сопрягающихся деталей. Для уплотнения служат разрезные кольца 1 из стали 20 или 30, устанавливаемые в 2-4 канавки поршня. Замок кольца обычно косой и плоский, реже - ступенчатый с лучшей герметизацией, но более трудный в изготовлении. Зазор в канавке между поршнем и кольцом должен быть таким, чтобы при монтаже обеспечить посадку поршня в рабочий цилиндр.
Бабы молотов с МПЧ до 5000 кг выполняют коваными, а при большей МПЧ -литыми из стали 45, 35Х, 40ХН или даже 40ХНА в зависимости от условий работы молота.
Шток элементарен по форме, но условия его работы чрезвычайно сложны, а поломка - частое явление в кузнечных цехах. Почти все исследователи указывают, что штоки ломаются заподлицо с бабой или в ее конусе. Это обусловливается характером напряженного состояния металла штока в месте поломок: продольными напряжениями от действия массовых сил при резком торможении падающих частей, напряжениями изгиба вследствие разворота бабы при эксцентричном ударе и постоянно действующими поперечными напряжениями сжатия от посадки штока с натягом. При осмотре места излома обнаруживается усталостный характер разрушения: внешняя кольцевая темная поверхность свидетельствует о появлении поперечной усталостной трещины, а блестящая шероховатая внутренняя часть -об остаточном межкристаллическом изломе. Факторы, определяющие прочность и стойкость штока, можно разделить на две категории: свойства металла, из которого изготовлен шток, и условия нагружения штока.
Чем выше способность металла сопротивляться динамическим нагрузкам, тем дольше служит шток. Поэтому наиболее желательно изготавливать его из хромоникелемолибденовой стали, например ХНЗМ или 40ХНМА. Однако молибден дефицитен, и приходится использовать стали хромоникелевого класса (30ХНЗА, 40ХН, 18ХНВА и т. п.). При облегченных условиях штамповки можно применять даже сталь 45 и, наоборот, при ковке высоколегированных сталей с жестким ударом шток даже ковочного молота должен быть изготовлен из высококачественного металла.
Стойкость штока будет в десятки раз ниже, если заготовка имеет металлургические дефекты, вроде флокенов, расслоений, пор и т. п. Штоки из такого металла ломаются в любом месте по его длине.

Коробление при термообработке не допускается, поэтому нагрев рекомендуют производить в шахтных печах. Применяют индукционный нагрев штоков.
Определенное влияние на стойкость штока оказывает качество обработки его поверхности: чем меньше параметр шероховатости, тем больше устранено концентраторов в виде микротрещин, надрезов и т. д. Поэтому поверхность штока после чистового точения шлифуют до Rz = 0,63...0,32 мкм. Для повышения стойкости применяют также упрочняющую обкатку роликом, прижатым к штоку силой 30...40 кН.
После того как шток изготовлен, его консервируют, густо смазывая, и передают на хранение. При этом царапины, забоины и тем более ржавчина совершенно недопустимы.
на стержень. Результаты такого решения удовлетворительно подтверждают данные экспериментальных исследований, согласно которым условие прочности штока можно записать в виде

- время прохождения ударной волны по штоку; / - длина штока;
введен здесь для того, чтобы учесть жесткость удара, поскольку в реальных условиях определенная часть эффективной энергии расходуется на уп-ругопластическую деформацию поковки, инструмента, подштамповой плиты и т. п., и тем самым приблизить расчетные значения напряжений к экспериментальным.
В качестве допускаемого напряжения необходимо принимать предел выносливости при сжатии-растяжении с симметричным циклом нагружения:
Забиваем Сайты В ТОП КУВАЛДОЙ - Уникальные возможности от SeoHammer
Каждая ссылка анализируется по трем пакетам оценки: SEO, Трафик и SMM.
SeoHammer делает продвижение сайта прозрачным и простым занятием.
Ссылки, вечные ссылки, статьи, упоминания, пресс-релизы - используйте по максимуму потенциал SeoHammer для продвижения вашего сайта.
Что умеет делать SeoHammer
— Продвижение в один клик, интеллектуальный подбор запросов, покупка самых лучших ссылок с высокой степенью качества у лучших бирж ссылок.
— Регулярная проверка качества ссылок по более чем 100 показателям и ежедневный пересчет показателей качества проекта.
— Все известные форматы ссылок: арендные ссылки, вечные ссылки, публикации (упоминания, мнения, отзывы, статьи, пресс-релизы).
— SeoHammer покажет, где рост или падение, а также запросы, на которые нужно обратить внимание.
SeoHammer еще предоставляет технологию Буст, она ускоряет продвижение в десятки раз,
а первые результаты появляются уже в течение первых 7 дней.
Зарегистрироваться и Начать продвижение

Таким образом, долговечная и надежная работа штока определяется предельно допустимой скоростью падающих частей перед ударом. Деформирование поковки с большей скоростью приведет к быстрой поломке штока.
Если удар наносится с эксцентриситетом, то из-за поворота бабы во фронтальной плоскости вследствие зазоров в направляющих происходит импульсный изгиб штока и в нем возникают поперечные напряжения. Для их снижения нет необходимости в каких-либо конструктивных изменениях молота, достаточно лишь строго выдержать зазоры между бабой и направляющими. В пределах требований на нормы точности для штамповочных молотов эти зазоры должны быть следующими: 0,20...0,35 мм на сторону для мелких и средних молотов и 0,40...0,50 мм - для крупных. Для ковочных молотов допускают зазоры 0,25...0,375 мм на сторону независимо от размеров молота.
Для повышения прочности штоков полезны технологические мероприятия, устраняющие обработку металла в эксцентрично расположенных заготовительных и черновых ручьях в результате применения периодического проката или вальцованных заготовок.
|