Кузнечно-штамповочное оборудованиеЦиклы молотовых установок
Каждая из полостей рабочего цилиндра паровоздушного молота представляет собой термомеханическую систему, в которой в качестве рабочего тела (энергоносителя) используется пар либо сжатый атмосферный воздух. Энергоноситель с требуемыми параметрами необходимо генерировать и транспортировать в пределы термомеханической системы, обеспечив бесперебойное ее действие, а отработавший энергоноситель - удалять. Для выполнения всех этих операций нужна совокупность агрегатов, составляющих энергосиловую установку привода паровоздушного молота. В ее пределах энергоноситель совершает замкнутый цикл.
На рис. 17.3, а приведена простейшая схема паросиловой установки. В котле 1 за счет энергии сгорающего топлива из воды генерируется влажный пар. При необходимости пар подсушивают и перегревают в пароперегревателе 2. Для
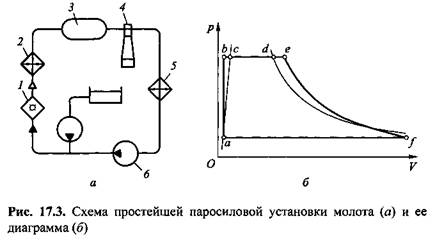
отводится из молота в конденсатор 5, где он,
проходя по охлаждаемым водой трубкам, конденсируется. Насос 6 перекачивает образовавшийся конденсат в котел 1. Цикл энергоносителя завершен.
- полную конденсацию пара.
На экономичность паросиловых установок значительное влияние оказывает правильный выбор начальных и конечных параметров пара.
Для паровых машин непрерывного действия (турбины) и периодического действия с установившимся режимом работы (поршневые двигатели) термический КПД является достаточным показателем экономической эффективности паросиловой установки. Высокое качество изготовления и эксплуатации этих машин позволяет свести до минимума утечки пара во время работы. При остановке же трубопровод свежего пара у них обязательно перекрывают. По этим причинам целесообразно повышать давление пара до 9 МПа и выше, благодаря чему можно снизить общий расход энергоносителя при той же полезной работе.
Эксплуатация и состояние молотов и условия их работы оставляют желать лучшего: утечки энергоносителя чрезвычайно велики. Можно еще как-то примириться с неизбежностью потерь при совершении технологических ходов (ударов) и в цикле качаний падающих частей. Поскольку суммарное время пауз (простоев) у молотов оказывается больше суммарного машинного времени, а трубопроводы при этих паузах не перекрывают, непроизводительные потери энергоносителя оказываются очень большими. В результате полезный расход пара в молотовых установках обычно составляет 15...20% от общего и лишь изредка повышается до 30...40 %.
Работать на паре слишком высокого давления нецелесообразно, потому что получить достаточно низкое давление в конце расширения можно только при очень малом впуске свежего пара, а это усложняет управление молотом. Нельзя забывать и об ограничении по условиям техники безопасности: высокое давление может привести к перетеканию пара из верхней полости в нижнюю и вследствие этого - к самопроизвольному подъему падающих частей в цикле прижима. Однако неприемлемо и заниженное давление свежего пара. Конечно, при давлении в 0,3...0,4 МПа потери на утечки значительно уменьшаются, но для сохранения энергии удара и быстроходности молота приходится увеличивать размеры рабочего цилиндра. Это нежелательно, так как усложняет изготовление и ремонт молота, увеличивает потери вследствие возрастающей конденсации пара при его возросшем объеме, а также потери на трение при движении поршня.
Суммируя все эти противоречивые факторы, приходим к выводу, что оптимальным можно считать давление свежего пара р = 0,7...0,9 МПа.
Несмотря на явную экономию теплоты при работе молотов на перегретом паре, его почти не применяют в кузнечных цехах. Производственники объясняют это эксплуатационными факторами: короблением рабочих элементов органов парораспределения, быстрым рассыханием сальникового уплотнения, утечками пара и увеличением износа цилиндра. Однако передовой опыт показывает, что перегрев пара до 260...280°С не приводит к короблению цилиндрических золотников и дросселей. Два других фактора прямо зависят от ухода за молотом и функционирования системы смазывания. Если смазывание недостаточно, то влажный пар с его обильным конденсатом хоть как-то его восполняет. Поэтому стандарты осторожны в отношении рекомендаций по перегреву, ограничивая его температурой 200 °С.
Объясняется это тем, что давление выпуска помимо
всякий раз задают средним значением на все время выпуска.
КПД молота даже для идеальной паросиловой установки невысок. Это свидетельствует о его несовершенстве как тепловой машины из-за оговоренных выше параметров энергоносителя. Если их улучшать, то идеальный термический КПД будет возрастать, однако реальный КПД будет уменьшаться, так как для небольшого увеличения теплоперепада в систему приходится вносить количество теплоты, непропорционально возрастающее в связи с утечками.
Повлиять на КПД всей паросиловой установки все же можно, если полезно утилизировать теплоту отработавшего пара. Одним из эффективных способов повышения экономичности паросиловых установок является теплофикация.
Схема энергосиловой установки привода молота со сжатым воздухом (рис. 17.4, а) построена на базе двух круговых термодинамических процессов: первичного, например цикла Ренкина конденсационной электростанции с турбогенераторами, и вторичного цикла установки, состоящей из компрессора и воздушного двигателя (молота). Состав схемы первичного цикла аналогичен составу схемы, показанной на рис. 17.3, a, но вместо молота здесь установлена паровая турбина 7. Преобразователем, связывающим оба термодинамических цикла, служит система, содержащая электрогенератор 2 и электродвигатель 3. Схема вторичного цикла включает в себя компрессор 4, холодильник 5, нагреватель 6 и молот 7.
Кроме кузнечных цехов сжатый воздух на заводах потребляют и другие производства (для привода пневматического инструмента, приспособлений, в цепях управления и т. д.). Чтобы обеспечить надежную и безопасную работу всех этих потребителей, необходимо подавать сжатый воздух с нормальной температурой (15...20 °С). Теплота у воздуха отбирается непосредственно через стенки компрессорного цилиндра либо в холодильнике 5.
Идеальным случаем является полный отбор теплоты при сжатии по изотерме. Если компрессорный цилиндр теплоизолирован, то процесс сжатия носит адиабатический характер. В реальных условиях компрессор работает по политропе с показателем п = 1,15... 1,25.
Забиваем Сайты В ТОП КУВАЛДОЙ - Уникальные возможности от SeoHammer
Каждая ссылка анализируется по трем пакетам оценки: SEO, Трафик и SMM.
SeoHammer делает продвижение сайта прозрачным и простым занятием.
Ссылки, вечные ссылки, статьи, упоминания, пресс-релизы - используйте по максимуму потенциал SeoHammer для продвижения вашего сайта.
Что умеет делать SeoHammer
— Продвижение в один клик, интеллектуальный подбор запросов, покупка самых лучших ссылок с высокой степенью качества у лучших бирж ссылок.
— Регулярная проверка качества ссылок по более чем 100 показателям и ежедневный пересчет показателей качества проекта.
— Все известные форматы ссылок: арендные ссылки, вечные ссылки, публикации (упоминания, мнения, отзывы, статьи, пресс-релизы).
— SeoHammer покажет, где рост или падение, а также запросы, на которые нужно обратить внимание.
SeoHammer еще предоставляет технологию Буст, она ускоряет продвижение в десятки раз,
а первые результаты появляются уже в течение первых 7 дней.
Зарегистрироваться и Начать продвижение
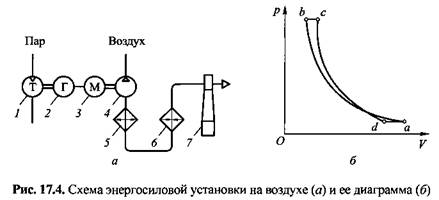

В нагревателе 6 (см. рис. 17.4, а) воздух подогревается по изобаре bc, и в систему поступает теплота. Затем следует адиабатическое расширение в цилиндре воздушного двигателя согласно кривой cd. Как известно, располагаемый теплоперепад в пределах заданного адиабатического расширения рабочего тела определяет полезную работу, отданную системой. При движении по изобаре от d к а объем газа увеличивается и, следовательно, теплота передается отработавшему воздуху в естественном теплообменнике или, попросту, в атмосфере.
При подаче воздуха без промежуточного подогрева точка с сливается с точкой Ъ и параметры воздуха перед расширением соответствуют его параметрам после изотермического сжатия. Начальное давление сжатого воздуха на входе в молот выбирают из тех же соображений, что и для пара.
Перевод молота на подогретый до 200 °С сжатый воздух значительно повышает термический КПД: от 40,6 % до 52,4 %. Это происходит потому, что с повышением температуры подогрева располагаемый теплоперепад возрастает при неизменной работе сжатия.
оказывается столь же выгодной, как и на неподогретом воздухе.
= 0,0754. При более коротких трубопроводах показатели работы молота на паре улучшаются, а при длинных -ухудшаются: сказываются возрастающие потери на конденсацию и утечки, а также термокинетические потери.
Для кузнечного цеха очень важно влияние вида энергоносителя на производительность. Оказывается, что при переводе молота на сжатый воздух производительность обслуживающей бригады повышается вследствие улучшения условий труда: молот обычно в лучшем состоянии и меньше изношен, утечки не мешают работе и т. п. Эффективная мощность молота при работе на сжатом воздухе в идентичных условиях незначительно повышается.
|