Обмотока машин постоянного и переменного токаИзготовление деталей соединения роторной обмотки
Для изготовления деталей соединения применяется главным образом плоская медь прямоугольного сечения. Нарезка основных полос производится согласно чертежам. Нарезанные полосы рихтуются на стальной плите.
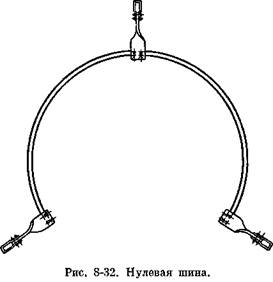
Звезда или нулевая шина (рис. 8-32), соединяющая три фазных конца обмотки ротора, представляет собой полосу плоской меди, согнутой дугообразно на 240°. К концам шины и к ее середине приклепываются токоотводы, изготовляемые из полос меди, сечение которых должно быть не меньше сечения стержня.
На рисунке видно, что к токоотводам в верхней части приклепаны при помощи медных заклепок хомутики, изготовляемые из меди меньшего сечения. Хомутики и места заклепок обслуживаются в оловянной ванне, после чего звезда считается готовой. Соединительные вилки или поперечки (рис. 8-33) изготовляются примерно так же, как и звезда, с той лишь разницей, что у них
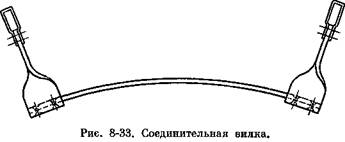
имеется только два токоотвода для соединения со стержнями. Размеры поперечен много короче, чем заезды.
Головка лежит
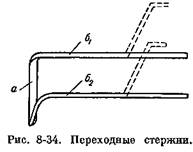
всегда снаружи и помещается на обмоткодержателе. Ножки средней своей частью лежат в пазах ротора, а концы их выходят наружу на другую сторону, где и изгибаются так же, как и концы роторных стержней.
Звезда и соединительные вилки изолируются одинаково — один раз вполнахлестки лентой из лако-ткани толщиной 0,15—0,20 мм, а в местах изгибов — в три четверти нахлестки. Изолировку начинают от наружного края, т. е. от одного хомутика до другого. Наложив лакотканевую ленту со всех четырех сторон, как звезду, так и поперечки покрывают полосками электрокартона и изолируют хлопчатобумажной лентой вполнахлестки, а в местах изгибов в три четверти нахлестки. Покрытие полосками электрокартона деталей соединения предохраняет последние от механических повреждений, могущих произойти при соприкосновении с неровностями металлических частей обмоткодержателя во время работы машины.
изолируются, так же как и пазовая часть стержней ротора, в зависимости от рабочего напряжения.
Изготовление катушек шаблонной однослойной обмотки крупных машин
Изготовление катушек однослойной обмотки может производиться двумя способами. По первому способу намотка катушки производится на так называемом макете — деревянной модели статорной стали. При этом способе вся работа производится вручную таким же порядком, как и при выполнении обмоток — способом протяжки (см. гл. 12). Разница заключается в том, что изготовленная в макете катушка вынимается из него и затем вкладывается в пазы статорной стали, в то время как катушки протяжной обмотки наматываются непосредственно в пазах статорной стали.
По второму способу намотка катушек производится не вручную, а на станках — с помощью специальных шаблонов. Этот способ является значительно более производительным и не требует такой высокой квалификации, как намотка катушек на макете. Ниже дается описание обоих способов.
Заготовка катушек на макете
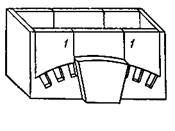
Макет для намотки нижних катушек представлен на рис. 9.1. Наверху над пазами установлены запоры 1 для укрепления гильзы в пазах. В гильзы вкладываются деревянные шпильки и крючки, между которыми протаскивается проводник. Перед намоткой второй и третьей катушек между ними для сохранения расстояния ставятся деревянные прокладки. До изготовления макета должны быть определены все размеры катушек так, как это описано в гл. 5, ибо согласно им изготовляется макет. После намотки всех катушек катушечной группы они вынимаются из макета Рис. 9-1. Деревянный макет. и поступают на изолировку. Намотка катушек в макете имеет целый ряд преимуществ перед намоткой их непосредственно в статоре, а именно:
заготовка катушек может производиться заранее, параллельно со сборкой статорной стали, что ускоряет процесс изготовления машины;
размеры всех катушек получаются строго выдержанными;
укладка проводников производится сверху и видна обмотчику;
при намотке катушек непосредственно в статоре его пришлось бы несколько раз поворачивать, так как производить намотку катушек в пазах, расположенных сверху и сбоку, неудобно.
Намотка катушек на станке
Здесь мы опишем заготовку катушек на деревянных шаблонах укрепляемых на обыкновенных лобовых станках. Размеры шаблонов устанавливаются согласно вычисленным размерам катушек. Если, например, катушечная группа состоит из четырех катушек, то для каждой катушки должен быть свой шаблон. На рис. 9-2, а показан шаблон для катушек с отогнутой лобовой частью (внутренний ряд катушек на рис. 5-6). На рис. 9-2, б изображен шаблон для катушек с прямой лобовой частью (внешний ряд на рис. 5-6).
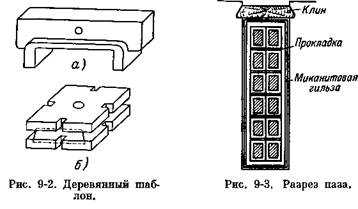
При напряжении между соседними витками свыше 50 в применяют прокладки между рядами витков. Прокладкой служит пропитанный в масле электрокартон или гибкий миканит толщиной 0,2— 0,3 мм. На рис. 9-3 показан разрез паза с поперечной укладкой проводников, между слоями которых проложены горизонтальные прокладки. Статорная обмотка для машин небольшого напряжения выполняется с вертикальными прокладками между рядами.
Намотка нижних катушек производится следующим образом. Бухта с проводником кладется на вертящийся барабан, откуда проводник идет через зажим, сделанный из двух планок, стянутых болтами, между которыми укладываются два слоя фибры.
Проводник проходит к станку. Посредством зажима создается известное натяжение и выравнивание проводника. Начальный конец длиной около 0,5 м, служащий в дальнейшем для вывода, укрепляется в планшайбе.
В процессе намотки для лучшего прилегания витков к шаблону их все время осаживают при помощи фибрового клина и ручника. Пусть обмотка катушек должна быть выполнена поперечной укладкой, согласно рис. 9-3, и между горизонтальными рядами должна быть проложена изоляционная прокладка. В этом случае первые два витка, составляющие один ряд со стороны выходных концов, укладываются на шаблон нормально.Третий виток укладывается с переходом во второй ряд, причем переход делается на отложной лобовой части катушки. Затем либо под переход подкла-дывают электрокартонную прокладку, либо это место изолируют лентой из лакоткани. Четвертый виток укладывается на место временно проложенной прокладки из проводника того же сечения. Пятый и шестой витки наматываются нормально, без переходов,
Забиваем Сайты В ТОП КУВАЛДОЙ - Уникальные возможности от SeoHammer
Каждая ссылка анализируется по трем пакетам оценки: SEO, Трафик и SMM.
SeoHammer делает продвижение сайта прозрачным и простым занятием.
Ссылки, вечные ссылки, статьи, упоминания, пресс-релизы - используйте по максимуму потенциал SeoHammer для продвижения вашего сайта.
Что умеет делать SeoHammer
— Продвижение в один клик, интеллектуальный подбор запросов, покупка самых лучших ссылок с высокой степенью качества у лучших бирж ссылок.
— Регулярная проверка качества ссылок по более чем 100 показателям и ежедневный пересчет показателей качества проекта.
— Все известные форматы ссылок: арендные ссылки, вечные ссылки, публикации (упоминания, мнения, отзывы, статьи, пресс-релизы).
— SeoHammer покажет, где рост или падение, а также запросы, на которые нужно обратить внимание.
SeoHammer еще предоставляет технологию Буст, она ускоряет продвижение в десятки раз,
а первые результаты появляются уже в течение первых 7 дней.
Зарегистрироваться и Начать продвижение
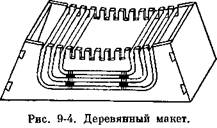
а седьмой и восьмой опять с переходами и т. д.
Между горизонтальными витками, как было указано выше, ставятся в прямой пазовой и лобовой частях изоляционные прокладки из электрокартона толщиной 0,3 мм, которые после намотки катушки заменяются прокладками из гибкого миканита той же толщины. Прокладки из гибкого миканита не ставятся сразу, так как они слишком хрупки и могут быть повреждены при осадке. После намотки необходимого числа витков (в данном случае 12) катушку связывают в 6—8 местах хлопчатобумажной лентой, положенной перед намоткой на шаблон под первые витки катушки. Это необходимо для крепления витков и сохранения необходимой формы катушки. Затем конец проводника отрезают от бухты меди и катушку снимают с шаблона. Таким же образом наматывают остальные катушки нижней катушечной группы.
Вид шаблона для намотки верхних катушек показан на рис. 9-2, б. Скос пазовых сторон шаблона делается для того, -чтобы стороны катушки не были параллельны, так как они закладываются в пазы по окружности статора, диаметр которого по верху пазов меньше, чем по низу.
Намотанные катушки после снятия с оправки укладываются в пазы деревянного макета (рис. 9-4), выполненного соответственно пазам статора для проверки правильности их изготовления. При примерке катушек в деревянном макете в пазы подкладывают картон. По толщине он должен равняться миканитовой опрессовке (будущей изоляции), которая будет наложена впоследствии на пазовую часть обмотки.
Изготовленные катушки передаются на последующие операции — изолировку, компаундировку, опрессовку и т. д., которые описаны ниже.
Изолировка катушек, намотанных на станке
После снятия катушек со станка временные электрокартонные горизонтальные прокладки заменяются миканитовыми толщиной от 0,20 до 0,30 мм, после чего каждая катушка в пазовой и лобовой частях изолируется хлопчатобумажной лентой шириной от 30 до 50 мм, один раз вполнахлестки. Затем катушки комплектуются по катушечным группам, для чего их укладывают в макет. Между соседними катушками в прямой (пазовой) части прокладывают длинные деревянные планки толщиной, равной длине зуба стали статора плюс двойная толщина стенки миканитовой изоляции катушки, которая будет наложена после компаундировки.
Деревянные планки укрепляются двумя бандажами из шпагата на каждую сторону. В лобовых частях с обеих сторон между отдельными катушками ставят временные картонные прокладки, которые скрепляют временными же веревочными бандажами.
Скрепленные указанным способом скомплектованные катушки поступают на компаундировку.
Компаундировка катушек
Катушки укладываются на металлические стеллажи, прикрепляются к перекладинам киперной лентой и загружаются в компа-ундировочный котел с плотно закрывающейся крышкой, но с открытым краном трубопровода, соединяющего котел с атмосферой в течение 3 ч при температуре 155—165° С. Затем сушка продолжается при этой же температуре, но под вакуумом, не менее 720 мм рт. ст. в течение 2 ч. Из смесительного котла впускают в компаундировочный котел компаундную массу, подогретую до температуры 155—165° С. Когда масса покроет все уложенные катушки (за этим наблюдают через смотровое окно на крышке котла), кран смесительного котла закрывают и нагнетают азот из азотосборника до давления не менее 7 кГ/см2 и держат это давление в течение 3 ч. После этого открывают кран и перегоняют компаундную массу обратно в смесительный котел.
Открывают крышку компаундировочного котла и при помощи крана выгружают стеллажи с катушками и устанавливают их для охлаждения на воздухе или для более интенсивного охлаждения катушки поливают водой из специальной дождевой установки, зимою засыпают снегом. На некоторых заводах имеются баки, куда опускаются кареты с горячей обмоткой и впускается проточная вода для охлаждения.
Разборку компаундированных катушек, во избежание порчи их формы, производят только после полного охлаждения.
Предварительная опрессовка катушек
С остывших катушек снимают все временные бандажи, удаляют деревянные прокладки между катушками, отделяют их друг от друга и снимают картонные прокладки. Затем катушка по всей длине заматывается временной киперной лентой в 1/3 нахлестки и подвергается опрессовке в гидравлическом пароводяном прессе (рис 9-5). Гидравлический пресс состоит из станины 2, на которой установлены два контрфорса 2 и два блока 3 Каждый блок состоит из горизонтального и вертикального цилиндров. Катушка 4 закладывается в прессформу, соответствующую размерам пазовых частей, и помещается между двумя пароводяными плитами 5. Пресс-форма состой! из верхней давящей планки 6, двух боковых щек 7
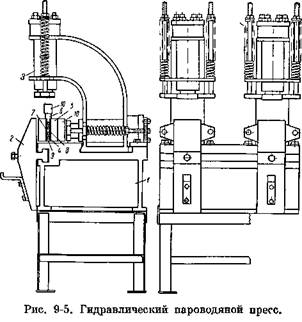
и двух пресспланок 8 и 9. Боковое давление передается через пароводяные плиты и дистанционную прокладку 10 на прессформу. Сверху давление передается непосредственно на верхнюю планку прессформы через дистанционную прокладку.
Прессовку можно также производить в ручном прессе. Удельное давление при прессовке составляет около 40 кГ/см2, температура плит 120—130° С. Эта опрессовка необходима для придания катушкам соответствующих размеров по ширине и высоте и для удаления излишков компаундной массы. Доведя ширину и высоту катушки до нужного размера, ее вынимают из пресса, рихтуют в деревянном шаблоне, проверяют шаг обмотки в макете, затем снимают киперную ленту и приступают к наложению корпусной изоляции.
Рекомендуется перед наложением корпусной изоляции проверить электрическую прочность витковой изоляции по существующим нормам для данной конструкции. Этим самым проверяется отсутствие дефектов, которые могли появиться в результате прессовки или других операций.
Наложение гильзовой изоляции на пазовую часть катушки для напряжений выше 500 в. Опрессовка и выпечка
До наложения изоляции от рулона микафолия отрезают кусок требуемого размера, ширина куска должна быть равна длине гильзовой опрессовки, а длина определяется в зависимости от размеров, поперечного сечения катушки. Для чего подсчитывают длину среднего периметра опрессовки и умножают ее на число слоев микафолия.
Сервис онлайн-записи на собственном Telegram-боте
Попробуйте сервис онлайн-записи VisitTime на основе вашего собственного Telegram-бота:
— Разгрузит мастера, специалиста или компанию;
— Позволит гибко управлять расписанием и загрузкой;
— Разошлет оповещения о новых услугах или акциях;
— Позволит принять оплату на карту/кошелек/счет;
— Позволит записываться на групповые и персональные посещения;
— Поможет получить от клиента отзывы о визите к вам;
— Включает в себя сервис чаевых.
Для новых пользователей первый месяц бесплатно.
Зарегистрироваться в сервисе
От рулонного микафолия толщиной 0,25—0,3 мм отрезают кусок соответствующего размера. Нарезанный микафолий наматывают в пять оборотов на пазовую часть катушки. По наложенному первому слою микафолия каждой стороны катушки проводят горячим утюгом, чтобы расплавить лак и приклеить им микафолий к виткам катушки. Обутюженную сторону сразу же притирают тряпкой для удаления возможных морщин и лучшего прилегания микафолия к катушке. Переворачивая катушку, аналогично накладывают последующие обороты микафолия.
На обе стороны катушки поверх микафолия накладывают один слой лакированной телефонной бумаги толщиной 0,05 мм и 1 — 1,5 оборота парафинированной бумаги, которая после опрессовки удаляется. Затем приступают к опрессовке и выпечке изоляции.
Более качественная микафолиевая изоляция в отношении плотности слоев и ровности наложения их получается, когда вместо обутюжки применяется горячая обкатка наложенного микафолия в обкаточном станке. При этом, помимо затяжки слоев изоляции, происходит выпечка, удаление летучих растворителей. Применяя горячую обкатку, можно последующую опрессовку сторон для получения необходимого размера и формы сечения производить в холодном прессе. Обутюженную же изоляцию следует выпекать только в горячем прессе.
В пресс вкладывается одна сторона катушки и сжимается до определенного размера по ширине и высоте пресспланками. Разогревая наложенный микафолий, производят выпечку находящегося в нем лака в течение 30—60 мин и более, смотря по размеру обмотки и толщине изоляции. По истечении указанного времени доступ пара прекращают и катушке дают остыть в прессе, после чего ее оттуда вынимают. То же самое проделывают и со второй стороной катушки.
При опрессовке одной стороны катушки другую сторону необходимо удерживать на специальных подставках, чтобы форма ее не изменилась.
После опрессовки и выпечки перед изолировкой лобовых частей производят отделку опрессованной пазовой части катушки. Снимают парафинированную бумагу. Удаляют излишки выдавленной: компаундной массы и лака на концах гильз ножом или утюгом, после чего накладывают изоляцию на лобовые части.
Изолировка лобовых частей катушек
Изоляция лобовых частей выполняется соответствующим числом слоев лакоткани и одним слоем хлопчатобумажной ленты шириной от 20 до 30 мм вполнахлестки на всей лобовой части и на изгибах. Выводные концы катушек изолируются лакотканью два раза вполнахлестки, причем начало изолировки ведут от края до места выхода из миканитовой гильзы и затем обратно. Изолированные концы подводятся к лобовым частям и поверх них уже накладывается общая изоляция лобовой части. Переходы от катушки к катушке изолируются три раза лакотканью вполнахлестки и поверх—хлопчатобумажной лентой.
После изолировки лобовых частей катушки подвергаются испытанию на корпус и витковое соединение, и выдержавшие его передаются для вкладки в статор.
|