Технология переработки нефти и газа. Часть 1Рециркуляция газойля
Рециркуляция – это возврат некоторого количества получаемого в ректификационной колонне легкого газойля или кубового продукта в реактор в смеси со свежим сырьем для повторного крекинга. Для процессов с рециркуляцией вводится понятие "коэффициент рециркуляции", который определяется из выражения:

где К – коэффициент рециркуляции;
– расход свежего сырья в реактор, м3/ч.
Рециркуляция газойля применяется при недостатке сырья для работы установки каталитического крекинга, при этом количество возвращаемого продукта составляет 5 – 10% на сырье (коэффициент рециркуляции 0,050,10). Использование рециркуляции газойля позволяет уменьшить существенное падение производства бензина, однако его октановое число снижается в среднем на 0,5-1 пункт. Это объясняется тем, что рециркулирующий газойль – ароматизированный продукт, при крекинге которого образуется повышенное количество кокса, что приводит к снижению активности катализатора и, как следствие, падению октанового числа бензина. Кроме того, ароматические углеводороды с короткой боковой цепью, содержащиеся в газойле, при крекинге дают большее количество углеводородных газов.
С учетом сказанного, рециркуляция газойля с коэффициентом выше 0,09-0,1 нецелесообразна, так как это осложняет работу реакторнорегенераторного блока из-за повышенного выхода кокса, что приводит к необходимости изменения расхода воздуха в регенератор, кратности циркуляции катализатора, расхода водяного пара и т.п.
Система подачи катализатора и сырья в реактор. На существующих установках с лифтреактором сырье подается в плотный слой движущегося снизу вверх катализатора. Это затрудняет распределение сырья между частицами катализатора, снижает эффективность тепло- и массообмена и увеличива-ет время испарения. При этом, если легкие фракции сырья испаряются достаточно быстро, то его тяжелая часть сравнительно долго остается в жидкой фазе, которая тонкой пленкой покрывает поверхность катализатора и блокирует его активные центры. Результатом неравномерного испарения является снижение активности катализатора, уменьшение количества образующегося бензина, повышенное коксообразование.
Система подачи сырья и катализатора в реактор на установке каталитического крекинга MS выгодно отличается от описанной. Она предусматривает предварительную подготовку потоков катализатора и сырья до начала их взаимного контакта в реакторе (см. рис. 3.14). Плотный поток регенерированного катализатора с насыпной плотностью 800-850 кг/м3, поступающий из напорного стояка, преобразуется с помощью водяного пара (кислой воды) в разрыхленный слой с низкой плотностью до 120-150 кг/м3. Тем самым обеспечивается свободный доступ паров сырья к зернам катализатора. Кроме того, в таком слое достигается высокая равномерность распределения частиц катализатора в объеме реакционной смеси и интенсивный теплои массообмен. Одновременно с подготовкой катализатора производится подготовка сырья в распределительном устройстве, снабженном 16 соплами. Оно предназначено для смешения сырья с водяным паром и преобразования сплошного потока жидкого сырья в 16 струй отдельных распыленных частиц. Такие частицы имеют диаметр 80-150 микрон, мгновенно (90-100 милисекунд) испаряются, их пары перегреваются до температуры реакции под действием водяного пара и теплоты катализатора и вступают в химическое взаимодействие. Для прохождения паров сырья и их равномерного распределения во всей массе катализатора с помощью сопел создается высокая (25-30 м/с) скорость истечения.
Таким образом, система подачи катализатора и сырья в реактор на установке МSСС обеспечивает создание условий для мгновенного испарения сырья и интенсивного его смешения с катализатором и исключает образование зон в реакторе с различным соотношением катализаторсырье.
Оптимальные значения параметров процесса. При производстве бензина на установке каталитического крекинга его выход повышают, изменяя соответствующим образом технологический режим, т.е. параметры процесса, до тех значений, пока затраты на производство бензина растут пропорционально повышению его выхода. Однако при достижении некоторых пределов (при работе установки на данном сырье и катализаторе) рост финансовых расходов начинает превышать рост производства бензина (рис. 3.14). Это объясняется резким увеличением скорости образования кокса и газа, что вызывает дополнительные эксплуатационные затраты (увеличение расхода электроэнергии на подачу воздуха в регенератор и на откачку газа компрессором, расхода воздуха, воды и электроэнергии на конденсацию и охлаждение верхнего продукта ректификационной колонны и т.д.). Кроме того, увеличиваются затраты на подпитку циркулирующего катализатора свежим, так как ускоряется падение его активности. На рис. 3.14 представлен пример определения экономически выгодного выхода бензина (53% на сырье) для фиксированного сырья и катализатора. Экономически выгодный выход бензина при данной производительности установки, сырье и катализаторе – это такое его количество, при превышении которого возрастает затраты на производство.
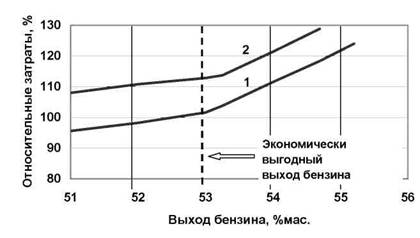
Рисунок 3.14 – Изменение затрат в процессе каталитического крекинга в зависимости от выхода бензина: 1 – эксплуатационные затраты; 2 – общие затраты
Те значения параметров процесса каталитического крекинга (температура, кратность циркуляции катализатора и т.п.), при которых достигается экономически выгодный выход бензина называются оптимальными.
Параметры технологического режима блока "реакторрегенератор". Значения параметров технологического режима реактора и регенератора взаимосвязаны, т.е. находятся в зависимости друг от друга. Изменение значения любого из них в реакторе требует корректировки других в регенераторе и наоборот. Например, при повышении расхода сырья в реактор требуется увеличение подачи воздуха в регенератор, т.к. ускоряется образование кокса на катализаторе. В связи с этим, при эксплуатации установки необходимо все параметры технологического режима блока "реакторрегенератор" поддерживать в определенных пределах их значений (таблицы 3.11 и 3.12).
Забиваем Сайты В ТОП КУВАЛДОЙ - Уникальные возможности от SeoHammer
Каждая ссылка анализируется по трем пакетам оценки: SEO, Трафик и SMM.
SeoHammer делает продвижение сайта прозрачным и простым занятием.
Ссылки, вечные ссылки, статьи, упоминания, пресс-релизы - используйте по максимуму потенциал SeoHammer для продвижения вашего сайта.
Что умеет делать SeoHammer
— Продвижение в один клик, интеллектуальный подбор запросов, покупка самых лучших ссылок с высокой степенью качества у лучших бирж ссылок.
— Регулярная проверка качества ссылок по более чем 100 показателям и ежедневный пересчет показателей качества проекта.
— Все известные форматы ссылок: арендные ссылки, вечные ссылки, публикации (упоминания, мнения, отзывы, статьи, пресс-релизы).
— SeoHammer покажет, где рост или падение, а также запросы, на которые нужно обратить внимание.
SeoHammer еще предоставляет технологию Буст, она ускоряет продвижение в десятки раз,
а первые результаты появляются уже в течение первых 7 дней.
Зарегистрироваться и Начать продвижение
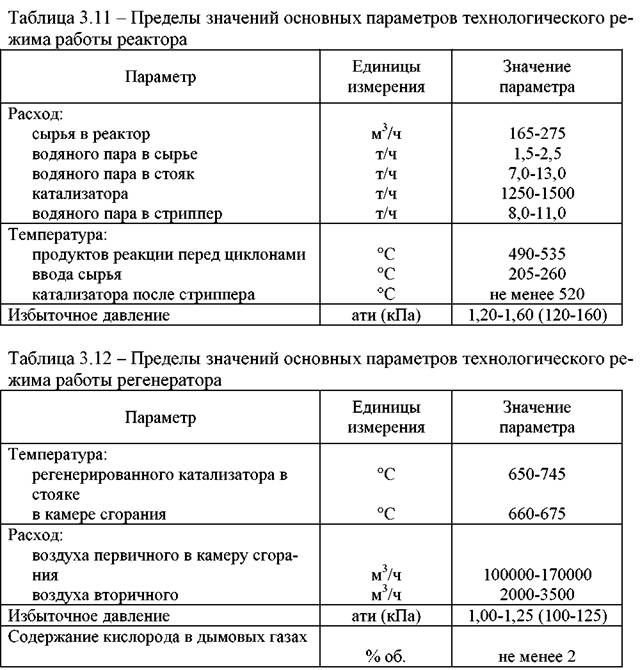
Анализ влияния основных факторов на результаты процесса показывает их большое практическое значение для квалифицированной эксплуатации установки. Эти факторы определяют техникоэкономические показатели, безопасность работы установки и ее экологическую совместимость с окружающей средой. При этом обслуживающий персонал должен хорошо знать, что все эти факторы взаимосвязаны и их необходимо учитывать при изменении значений того или иного параметра процесса.
|