Технология переработки нефти и газа. Часть 1Технологическое оборудование секции 2000
Каталитический крекинг является специфическим процессом нефтепереработки, поэтому применяемые аппараты и оборудование имеет свои особенности. Высокая температура, абразивное воздействие движущейся твердой фазы, а также коррозионное влияние некоторых агрессивных веществ предъявляют повышенные требования к конструкции аппаратов и материалам для их изготовления. Особенно это касается реакторнорегенераторного блока, который называют сердцем установки. Рассмотрим более подробно основное технологическое оборудование секции 2000.
Реактор. Реактор представляет собой вертикальный цилиндрический аппарат с переменным диаметром. Схематично он показан на рис.3.18. Внутри корпус аппарата и все детали, соприкасающиеся с движущимся катализатором, защищены изолирующей огнеупорной футеровкой толщиной 125-150 мм, которая защищает металл от эрозии, а также от коррозионного воздействия химически активных веществ при высокой температуре. Для повышения механической прочности слоя футеровки предусмотрена арматура в виде спиральных "усов" (так называемых "анкеров"), выполненных из стальной проволоки диаметром 7-8 мм и длиной 100-150 мм, и приваренных средней частью к внутренней поверхности реактора. На концы "усов" надеваются специальные колпачки, защищающие футеровку при термическом удлинении проволоки. При приготовлении футеровочного раствора в него добавляются тонкие металлические иглы длиной 30-40 мм, что создает дополнительный армирующий эффект и усиливает прочность футеровки.
Реактор установлен на бетонном постаменте высотой примерно 10 м. Высота самого аппарата от внешней кромки нижнего сферического днища (без учета вылета штуцеров подачи пара и вывода отработанного катализатора) до среза верхнего люка (без крышки) составляет 27,95 м. По высоте реактор снизу-вверх условно делится на три зоны:
зона отпарки закоксованного катализатора (стриппер);
зона реакции и первичного отделения продуктов от катализатора;
зона вывода газопаровой продуктовой смеси.
Важное значение имеет работа отпарной зоны, предназначенной для удаления с помощью водяного пара увлеченных углеводородных паров. Катализатор опускается в стриппер через несколько решеток. Пар подается под нижнюю решетку с расходом 1,5-3,0 кг на тонну циркулирующего катализатора. Этого количества пара обычно бывает достаточно для удаления всех унесенных углеводородов. Плохое отпаривание катализатора приводит к увеличению потерь сырья и продуктов, повышению выхода кокса и содержанию в нем водорода. Установлено, что при увеличении концентрации водорода в коксе с 5 до 10% мас. расход воздуха, необходимый для его выжигания возрастает с 12,63 до 13,80 кг на 1 кг. Кроме того, повышенное содержание водорода в коксовых отложениях может привести к местным перегревам катализатора, так как теплота сгорания этих отложений будет выше, чем у "сухого" кокса.
Неблагоприятный режим отпаривания может увеличить закоксованность катализатора в самой отпарной секции за счет углубления реакций уплотнения в десорбируемом слое. Установлено, что основная масса паров, увлеченных катализатором, приходится на свободный объем между его зернами, а доля продуктов уплотнения, адсорбированных в порах и выжигаемых с поверхности, в 10-15 раз меньше. Отсюда следует вывод, что плотность слоя катализатора в отпарной секции (стриппере) должна быть максимальной.
Зона реакции и первичного отделения продуктов от катализатора может быть разделена на две подзоны, что вытекает из ее названия. Как было отмечено выше, реакции каталитического крекинга протекают в весьма короткий промежуток времени. Этому способствует специальное устройство ввода сырья, позволяющее разделить большой поток, предварительно смешанный с водяным паром, на 16 меньших. Другими словами, оно позволяет тонко диспергировать сырье и в результате значительно облегчить его испарение. Сопла для подачи сырья сверху защищены металлической пластиной, предохраняющей от абразивного действия стекающего катализатора.
Практически сразу после встречи с распыленным сырьем катализатор подхватывается парогазовым продуктовым потоком и выносится в райзер. Райзер представляет собой специальную конструкцию, нижняя конусная часть которой полностью перекрывает сечение реактора и служит для сбора и упорядочения движения парогазового потока. В цилиндрическом (разгонном) участке поток увеличивает скорость (за счет уменьшения диаметра) почти в 2,5 раза и попадает в вихревой сепаратор. Принцип действия вихревой системы разделения показан на рис.3.19.
Катализатор отбрасывается к стенкам сепаратора по принципу центрифуги, завихряется и стекает вниз по спирали вдоль стенок корпуса в накопительное пространство, образуемое конусной частью райзера и корпусом реактора. Оттуда он по семи перепускным трубам поступает в зону отпарки. Вихревая система является первой стадией разделения твердой и паровой фаз. Выходящие из сепаратора пары уносят некоторое количество частиц катализатора. Поэтому парогазовая продуктовая смесь направляется в 5 параллельно работающих циклонов диаметром 1,8 м каждый. В них происходит окончательная очистка продуктов реакции от катализатора (остается незначительная часть катализаторной пыли), который из циклонов также стекает в стриппер реактора.
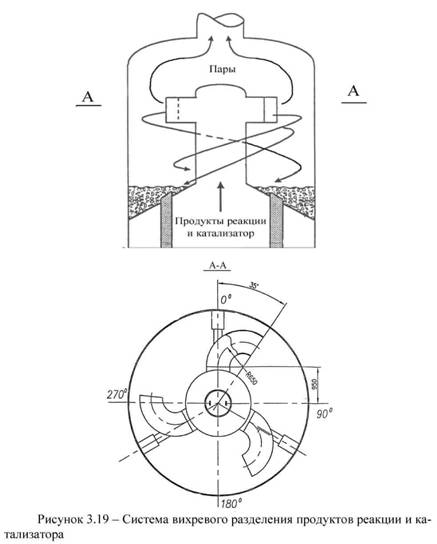
Регенератор. Регенератор конструктивно напоминает реактор, т.е. это такой же вертикальный цилиндрический аппарат с переменным диаметром, однако он больше по объему, т.к. при сгорании кокса образуются довольно большое количество дымовых газов, значительно превышающее объем паров в реакторе. Кроме того, в нем устанавливаются внутренние циклоны, для размещения которых требуется пространство. Огнеупорный слой футеровки накладывается поверх специальной формы якорных болтов. В зависимости от среды выполняются различные уклоны и глубина ее наложения. Специальный слой, устойчивый к истиранию, толщиной 19 мм накладывается в зонах высокой эрозии, таких как: циклоны, устройства распределения воздуха и задвижки катализатора. Высота аппарата 44,7 м, высота постамента 12,5м. Общий вид регенератора приведен на рис.3.18.
Забиваем Сайты В ТОП КУВАЛДОЙ - Уникальные возможности от SeoHammer
Каждая ссылка анализируется по трем пакетам оценки: SEO, Трафик и SMM.
SeoHammer делает продвижение сайта прозрачным и простым занятием.
Ссылки, вечные ссылки, статьи, упоминания, пресс-релизы - используйте по максимуму потенциал SeoHammer для продвижения вашего сайта.
Что умеет делать SeoHammer
— Продвижение в один клик, интеллектуальный подбор запросов, покупка самых лучших ссылок с высокой степенью качества у лучших бирж ссылок.
— Регулярная проверка качества ссылок по более чем 100 показателям и ежедневный пересчет показателей качества проекта.
— Все известные форматы ссылок: арендные ссылки, вечные ссылки, публикации (упоминания, мнения, отзывы, статьи, пресс-релизы).
— SeoHammer покажет, где рост или падение, а также запросы, на которые нужно обратить внимание.
SeoHammer еще предоставляет технологию Буст, она ускоряет продвижение в десятки раз,
а первые результаты появляются уже в течение первых 7 дней.
Зарегистрироваться и Начать продвижение
Регенератор разделен на две секции. В нижней, называемой камерой сгорания, происходит выжиг кокса с отработанного катализатора, поступающего из реактора, который смешивается предварительно с воздухом от главной воздуходувки во внешнем райзере смешения. Смесь поступает через главный коллекторраспределитель, обеспечивающий равномерное ее распределение по объему, в камеру сгорания, где процесс выжига кокса происходит в кипящем слое. Кокс достаточно полно выгорает за 5-7 мин., при этом удельный коксосъем может колебаться в широких пределах – от 20 до 45 кг в час на 1 т катализатора.
Верхняя секция или верхний регенератор создает необходимый объем для отделения регенерированного катализатора от дымовых газов и обеспечивает уравновешенность в системе его циркуляции. Кроме того, здесь размещены 10 двухступенчатых циклонов диаметром 1,38 м, которые подвешены на металлических штангах к крышке регенератора и дополнительно укреплены между собой и стенкой корпуса.
Регенерированный катализатор потоком дымовых газов транспортируется по райзеру в Т-образный разделитель, являющийся его верхней частью. Отделенное здесь основное количество катализатора ссыпается в пространство между стенкой регенератора и райзером, образуя слой, уровень которого регулируется. Сюда же добавляется свежий или равновесный катализатор. Из этого слоя регенерированный катализатор стекает через задвижки в реактор, а также осуществляется его циркуляция в камеру сгорания.
Дело в том, что отработанный катализатор поступает в регенератор с температурой 495-530°С. Эта температура является недостаточно высокой для полного выжига кокса в аппарате большого размера. Поэтому горячий катализатор из верхней секции в количестве приблизительно равном расходу отработанного катализатора постоянно циркулирует в камеру сгорания, что повышает эффективность процесса сгорания кокса. Регулированием расхода горячего регенерированного катализатора можно управлять следующими процессами в камере сгорания: температурой смешения перед сжиганием, плотностью слоя катализатора, а также временем выгорания кокса. Это, в конечном счете, позволяет оптимизировать в целом процесс регенерации катализатора.
Дымовые газы, выходящие из Т-образного разделителя увлекают с собой некоторое количество наиболее мелких частиц катализатора. Унесенная твердая фаза отделяется в 10 параллельно работающих двухступенчатых циклонах и стекает из них в слой регенерированного катализатора. Освобожденные от твердых частиц дымовые газы из каждого циклона собираются в сборной камере, называемой пленумом, и выводятся из регенератора на очистку и использования их теплоты.
|