Технология переработки нефти и газа. Часть 1Блок стабилизации
Нестабильный катализат из сепаратора B-212N поступает в теплообменник E-206, где нагревается за счет тепла нижнего продукта колонны стабилизации и поступает в колонну стабилизации C-202.
Из верхней части колонны выводится газ стабилизации и пары верхнего продукта. После конденсации в аппарате воздушного охлаждения AK-203/2 и охлаждения в водяном холодильнике EK-204 верхний продукт поступает в емкость орошения D-202. Часть углеводородного газа из емкости D-202 направляется на производство водорода в секцию 100 установки ЛГК. Остальной угле-водородный газ из емкости D-202, через клапан регулятор давления в колонне С-202, сбрасывается в топливную сеть, на факел или направляется на абсорбцию в секцию 400. Количество выводимой "нестабильной головки стабилизации" контролируется по показаниям прибора поз. FIRC 2030.
Необходимое для стабилизации количество тепла вводится в колонну циркуляцией стабильного катализата через печь F-204 насосами P-212, P-213. Разрежение до камеры конвекции печи F-204 регулируется шибером, который расположен после камеры конвекции.
Стабильный катализат, выходящий с низа колонны и отводимый в парк, охлаждается в теплообменнике E-206, затем в аппарате воздушного охлаждения AK-203/1 и водяном холодильнике EC-206. Температура продукта на выходе из водяного холодильника EC-206 регулируется путем изменения угла наклона лопастей вентиляторов воздушного холодильника AK-203/1. Стабильный катализат окончательно захолаживается в холодильнике ЕС-206, и направляется в парк.
Для контроля за качеством сырья и продуктов секции 200 на аппаратах и трубопроводах предусмотрены пробоотборные устройства.
Для защиты оборудования от превышения давления на аппаратах и трубопроводах установлены предохранительные клапаны.
Основное оборудование, используемое в процессе
Специфическим оборудованием, используемым в процессе каталитического риформинга являются реакторы, многосекционные печи, теплообменные аппараты.
Особый интерес представляют теплообменники типа Packinox (рис. 5. 12).
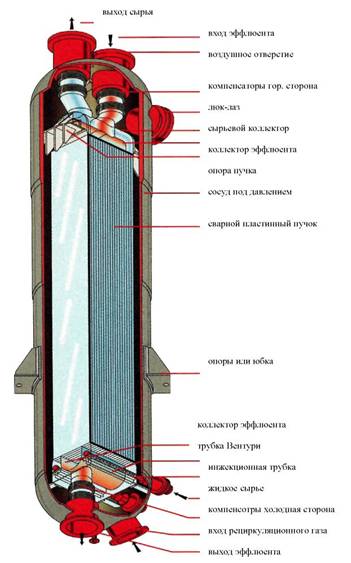
Рис. 5.12 Теплообменник типа Packinox
Packinox – это пластинчатый вертикальный теплообменник, состоящий из сварного пластинчатого теплообменного элемента и сосуда под давлением.
В рабочем режиме пластинчатая часть защищена от разрушения наружным давлением за счет большего потока водородсодержащего газа, подаваемого прямо в сосуд.
Другими составными частями теплообменника являются :
коллекторы для распределения потоко в внутри сварного пластинча того элемента,
компенсаторы, предназначенные для предотвращения разгерметизации аппарата в результате теплового расширение его частей,
инжекционные трубки для впрыска жидкого сырья. Теплообменник Packinox установлен в вертикально и горячий эффлюент из последнего реактора входит в него через верхнюю часть и спускается вниз охлаждаясь (маршрут потока: вход эффлюента, компенсаторы горячей стороны, коллектор эффлюента, пластинчатый элемент, компенсатор холодной стороны, выход эффлюента).
Холодное комбинированное сырье входит в теплообменник через нижнюю часть и движется нагреваясь в верх (маршрут потока: вход водородсодержащего газа + трубка Вентури (пар), жидкое сырье + инжекционные трубки (жидкость), пластинчатый элемент, сырьевой коллектор, компенсаторы горячей стороны, выход сырья).
Пластинча тый элемент изготовлен из штампованны х взрывом гофрированных металлических листов, выполненных из нержавеющей стали, установленных в пакет друг на друга и разделенных по краям распорными втулками, приваренных к листам. Основными компонентами являются длинные тонкие гофрированные листы, которые формуются взрывом под водой (Рис. 5.13).
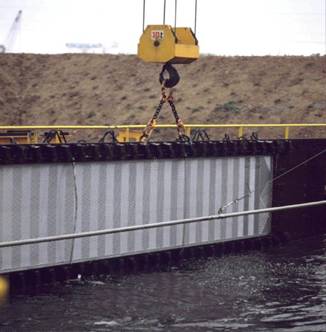
Формовка взрывом обеспечивает очень ровную поверхность и постоянную толщину гофрированных листов которая значительно уменьшает влияние загрязнений.
Рис. 5.13 Гофрированный лист выходящий из формовочного бассейна
Каждый лист снабжен продольными прокладками
вход / выход. Сборка листов дает чередующиеся каналы для комбинирования сырья и эффлюента. Распределе ние среды внутри каналов обеспечивается коробками коллектора и прокладками вход / выход (рис. 5.14).
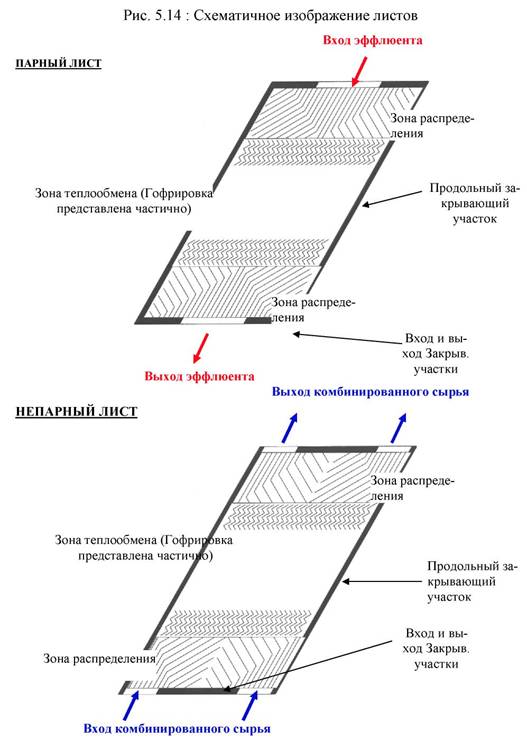
Пластинчатый элемент заключен внутри сосуда под давлением, в котором при рабочем режиме водородсодержащим газом создается соответствующее давление.
При нормальных рабочих условиях перемещения среды внутри сосуда под давлением не происходит, рассчитанного для выдерживания рабочего давления и для защиты пластинчатого элемента. Сосуд под давлением является полностью сварной конструкцией для безопасного проведения операций. Он изготовлен из низколигерованной стали (1.25 Cr. 0.5 Mo. или 2.25 Cr.-1.0 Mo.). Люк – лаз находится в верхней части аппарата, в то время как нижняя часть теплообменника доступна через патрубок циркулирующего водородсодержащего.
Компенсаторы служат для предотвращения разгерметизации отдельных частей аппарата в результате температурного расширения пластинчатого элемента, выполненного из нержавеющей стали, и низколегированным сосудом под давлением. Компенсаторы находятся внутри сосуда под давлением.
Комбинированное сырье состоит из двух потоков, холодный водородсодержащий газ и жидкое сырье. Водородсодержащий газ подается прямо в нижнюю часть сосуда, где он проходит в нижнюю часть пластинчатого элемента через вход трубку Вентури.
Жидкое сырье вводится прямо в пучок через инжекционные трубки (рис. 5.15) обеспечивая равномерное смешивание с водородсодержащим газом и ровное распределение внутри пучка. Инжекционные трубки особенно рекомендуется использовать, когда требуется низкий перепад давления в комбинированном сырьевом теплообменнике.
Забиваем Сайты В ТОП КУВАЛДОЙ - Уникальные возможности от SeoHammer
Каждая ссылка анализируется по трем пакетам оценки: SEO, Трафик и SMM.
SeoHammer делает продвижение сайта прозрачным и простым занятием.
Ссылки, вечные ссылки, статьи, упоминания, пресс-релизы - используйте по максимуму потенциал SeoHammer для продвижения вашего сайта.
Что умеет делать SeoHammer
— Продвижение в один клик, интеллектуальный подбор запросов, покупка самых лучших ссылок с высокой степенью качества у лучших бирж ссылок.
— Регулярная проверка качества ссылок по более чем 100 показателям и ежедневный пересчет показателей качества проекта.
— Все известные форматы ссылок: арендные ссылки, вечные ссылки, публикации (упоминания, мнения, отзывы, статьи, пресс-релизы).
— SeoHammer покажет, где рост или падение, а также запросы, на которые нужно обратить внимание.
SeoHammer еще предоставляет технологию Буст, она ускоряет продвижение в десятки раз,
а первые результаты появляются уже в течение первых 7 дней.
Зарегистрироваться и Начать продвижение
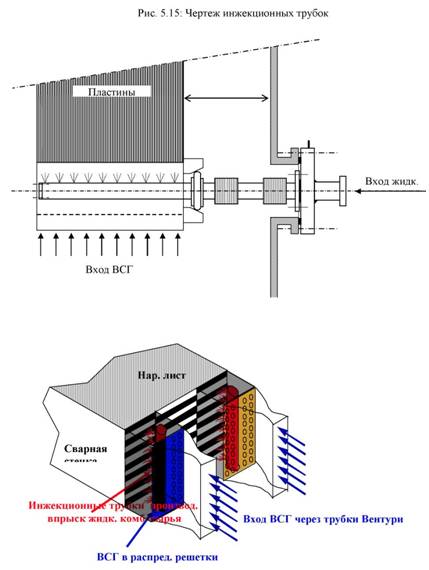
Пути интенсификации процессов каталитического риформинга.
НПЗ на территории бывшего СССР сталкиваются с необходимостью повышения октанового числа риформата, чтобы выпускаемый ими бензин в будущем соответствовал требованиям европейского законодательства по топливам. Следует также учитывать возрастающую потребность в водороде в связи с введением требований, предусматривающих снижение содержания серы в топливе. Поскольку установки каталитического риформинга на многих НПЗ являются основным источником высооктановых бензиновых фракций и водорода, то от них требуют поддержания и даже удлинения существующего межрегенерационного цикла катализатора при работе в более жёстком режиме, направленном на получение более высокоароматизированных продуктов. При наличии на заводе только одной установки риформинга поддержание или удлинение межрегенерационного цикла работы катализатора будет критичным для обеспечения надежности работы НПЗ. Выживание НПЗ малой мощности или НПЗ, занявших на рынке определённую нишу, которые эксплуатируют установки риформинга со стационарным слоем, может зависить от малозатратных решений, направленных на удовлетворение таких потребностей в будущем. ЮОП разработала систему "СайклХ" , включающую в себя новый реактор, регенератор и промежуточную печь, как решение проблем модернизации установок риформинга малой мощности 200 600 тыс. т./г. (33-100 м /час) - со стационарным слоем катализатора и последовательно или соосно установленными реакторами с целью удовлетворения новых требований к установкам риформинга. Ключевыми особенностям этой системы являются следующие:
Низкие капитальные и эксплуатационные затраты.
Увеличение выхода водорода и риформата.
Повышение октанового числа продуктового С5 .
Увеличение продолжительности межрегенерационного цикла катализатора стационарного слоя.
Минимальные сроки внедрения.
Все эти достоинства позволяют эффективно реализовать проект производства чистых топлив при быстрой окупаемости и значительной прибыли на инвестированные средства.
При переходе на европейские стандарты на производство топлив, а также при необходимости в будущем выпускать топлива с ультранизким содержанием серы (10 ппм) НПЗ ясно представляют себе, что для производства реформу лированных видов топлива, отвечающего требованиям предусмотренных к введению новых стандартов, потребуется больше водорода. И такое повышение спроса на водород обусловлено следующими факторами:
Снижением содержания олефинов и серы в бензине с установок каталитического крекинга (FCC).
Снижением содержания бензола и общей ароматики в риформате.
Снижением содержания ароматики и серы в фондовом дизельном топливе.
На большинстве НПЗ основным производителем водорода является каталитический риформинг, поэтому желательно максимально использоватьсуществующее оборудование, чтобы обеспечить наиболее рентабельное решение проблемы. Обессеривание, как и насыщение олефинов требуют значительного увеличения производства водорода на основном источнике его получения на НПЗ. Потребность в риформате, как в высокооктановом компоненте с низкой упругостью паров возрастает, т.к. необходимо скомпенсировать потерю октанового числа при снижении содержания олефинов и бензола. Завод, эксплуатирующий установку риформинга, хотел бы сохранить или повысить октановое число, увеличить выход водорода и продлить межрегенерационный период работы катализатора с тем, чтобы период работы риформинга совпадал с периодом работы установки гидрообессеривания, продолжительностью обычно два года. Не имея источника водорода эти установки гидрообессеривания (HDS) придётся остановить, что отрицательно скажется на рентабельности НПЗ.
Для НПЗ бывшего СССР имеется несколько возможностей повысить октановое число продукта, при сохранении или продлении межрегенерационного цикла работы катализатора, а также удовлетворить будущие потребности в увеличении выпуска водорода:
• Модернизировать существующую установку риформинга традицион ными методами, увеличив общий объем катализатора, использовав ка тализатор большей активности, обеспечивающий больший выход продукта.
• Модернизировать установки риформинга со стационарным слоем ката лизатора на установку Платформинг-НРК с пониженным рабочим давлением для повышения выхода водорода и риформата.
• Реконструировать установку риформинга со стационарным слоем ка тализатора с внедрением схемы Дуалформинг или СайклХ в ка честве эффективного решения с низкими капитальными и эксплуата ционными затратами для повышения выхода водорода и риформата.
|