Технология переработки нефти и газа. Часть 1Производство ароматических углеводородов
Традиционным сырьем для получения индивидуальных ароматических угле-водородов (бензол, толуол, параксилол, метаксилол, ортоксилол и этилбен-зол) является катализат процесса риформинга (риформат). Обычно для полу-чения бензола и толуола риформингу подвергается узкая бензиновая фрак-ция, выкипающая в пределах 70-105оС, а при производстве ксилолов и этил-бензола – 105-140оС. При этом в состав установки риформинга, как правило, входят специальные блоки: догидриро вания продуктов (с целью удалени я алкенов) и экстракции ароматических углеводородов. Если назначением ус-тановки риформинга является получение высокооктанового компонента бен-зина, то в качестве сырья используются бензиновые фракции 85-180оС и вы-деление ароматических углеводородов не предусматривается.
При наличии на НПЗ блока производства ароматических углеводородов его структуру определяет необ ходимос ть получения конкретных продуктов. В настоящее время наибольшим спросом на рынке пользуются бензол и пара-ксилол. Использование бензола при производстве ряда продуктов показано в таблице 8.1.
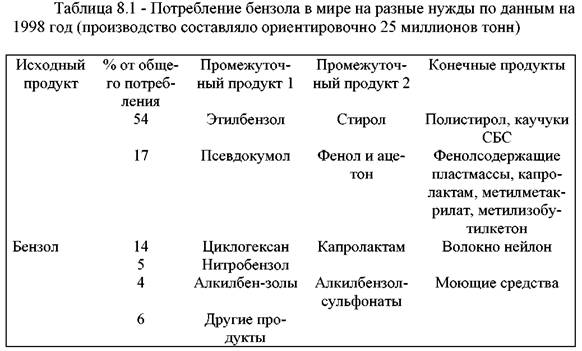
Потребность в толуоле за последние 50 лет резко упала. Из выделяемых при экстракции суммарных ксилолов на сегодняшний день в среднем на мировом рынке потребность в индивидуальных продуктах распределяется следующим образом: этилбензол –1%, параксилол –86%, метаксилол –3% и ортоксилол – 10%.
Современные комплексы производства ароматических углеводородов
В связи с вышесказанным, состав комплексов по получению ароматических углеводородов на различных НПЗ приобрел общие черты и может быть пред-ставлен следующим образом (рис. 8.1). Аналогичный состав имеет производ-ство ароматических углеводородов в ОАО Нафтан.
В начале технологической цепочки находится одна или две установки ри-форминга. При переработке более узких фракций удается лучше оптимизи-ровать режим установок, поэтому чаще предпочтение отдается раздельному получению риформатов, содержащих бензол-толуольную и ксилольную фракции. Во время жидкофазной экстракции от них отделяют рафинаты (практически не содержащие ароматических углеводородов бензиновые фракции), в экстрактах же содержатся только ароматические углеводороды. Бензол-толуольная и ксилольная фракции на первом этапе перерабатываются раздельно. Первая из них подвергается четкой ректификации и разделяется на чистые бензол и толуол. Кроме того, на этом этапе из бензол-толуольной фракции выделяются содержащиеся в небольшом количестве суммарные ксилолы, ароматика С9 и выше (С9+). В связи с низкой потребностью в то-луоле и высоким спросом на бензол первый их них подвергается гидродеал-килированию (отрыв метильной группы от бензольного кольца) по техноло-гии Детол. В результате из толуола в основном получается бензол и угле-водородные газы.
Изменение требований в развитых странах к содержанию ароматических уг-леводородов и особенно бензола в товарных бензинах принуждает их произ-водителей искать способы извлечения и получения чистых аренов из продук-тов бензинового риформинга.
Фирмой Джи-Ти-Си разработана и внедрена в промышленном масшта-бе технология выделения бензол-толуол-ксилольных (БТК) фракций из различ-ных сырьевых компонентов, в том числе и из продуктов процесса бензинового риформинга. Отличительной ее особенностью является осуществление выделе-ния ароматических углеводородов в режиме экстракционной дистилляции. Принципиальная технологическая схема этой технологии (фирменное название GT-BTXSM ) приведена на рисунке 8.2. В соответствии с ней сырье, выделенное из продуктов риформинга в стабилизационной колонне, подается в паровой фа-зе в середину абсорбера, а в его верхнюю часть поступает тощий абсорбент. Снизу этого аппарата выводится насыщенный
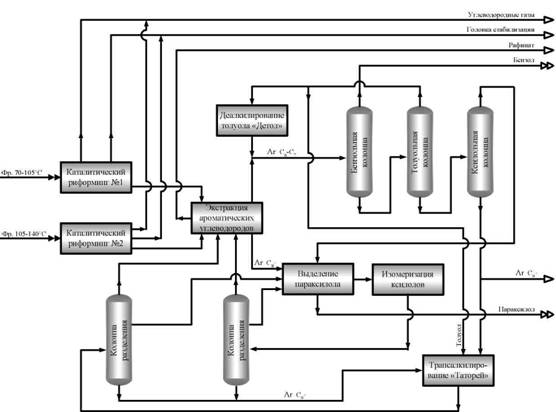
Рис. 8.1 – Принципиальная блочная схема типового комплекса по производству бензола и параксилола
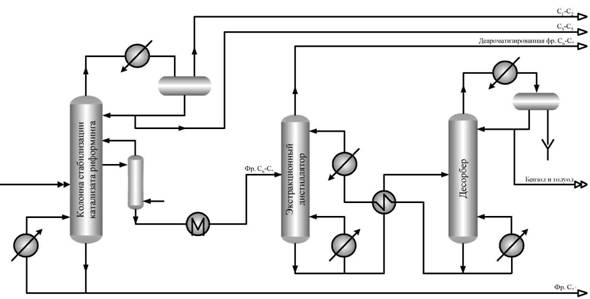
Рис. 8.2 – Принципиальная схема получения ароматических углеводородов по технологии GTC из катализата бензинового риформинга абсорбент, содержащий ароматические углеводороды, деароматизированные же углеводороды выходят сверху. Hoy-xay фирмы - используемый абсорбент (экстрагент) и способ его подготовки. Ароматические углеводороды отпарива-ются от экстрагента в десорбере. Регенерированный абсорбент возвращается после прохождения теплообменника в абсорбер. Однако часть его забирается на очистку от продуктов термической деструкции. Выделенные ароматические уг-леводороды разделяю тся с помощью четкой ректификации на высокочистые бензол (99,99%), толуол (99,99%) и суммарные ксилолы. Потери абсорбента на продукты составляет не более 1 ppm.
Такая технология может быть использована на предприятиях Республики Беларусь для увеличения производства не только бензола и толуола, но и сум-марных ксилолов.
По данным фирмы Джи-Ти-Си ориентировочная стоимость строитель-ства такой установки (блока), мощностью около 100 м3 сырья/час составляет 12-15 млн. долларов США. Кроме того, даются гарантии возможности работы описанной технологии на самом различном сырье, в том числе, богатом непре-дельными углеводородами. В случае необходимости специалисты ПГУ, имею-щие контакты с представителями вышеназванной фирмы, могут получить более конкретную информацию по данному процессу.
Кроме риформата сырьем для получения параксилола может в потенциале слу-жить фракция бензина пиролиза. Содержание изомеров в продуктах экстракции этих двух источников сырья приведено в таблице 8.2.
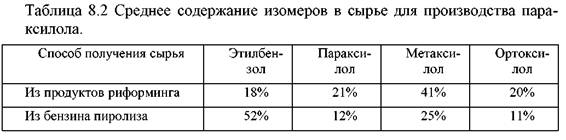
В отличие от бензола выделить чистый параксилол из его смеси с изомерами более сложно. В таблице 8.3 приведены температуры кипения и кристаллиза-ции изомеров ксилола.
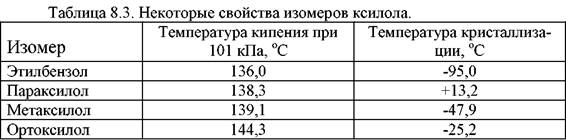
Их температуры кипения очень близки. Наиболее просто с помощью экс-трактивной ректификации можно выделить из смеси ортоксилол. Для того, что-бы из оставшейся смеси отогнать этилбензол требуется сверхчеткая дистилля-ция, причем количество тарелок в ректификационной колонне достигает 200-220 штук. Разделить же пара- и метаизомеры путем ректификации практически невозможно. В то же время отличие температуры кристаллизации параксилола от аналогичного параметра для иных изомеров позволило разработать эффек-тивный способ разделения этих веществ методом низкотемпературной кристал-лизации. Кроме того, путем каталитической изомеризации любой изомер кси-лола может быть превращен в другие, в том числе и в параксилол.
Забиваем Сайты В ТОП КУВАЛДОЙ - Уникальные возможности от SeoHammer
Каждая ссылка анализируется по трем пакетам оценки: SEO, Трафик и SMM.
SeoHammer делает продвижение сайта прозрачным и простым занятием.
Ссылки, вечные ссылки, статьи, упоминания, пресс-релизы - используйте по максимуму потенциал SeoHammer для продвижения вашего сайта.
Что умеет делать SeoHammer
— Продвижение в один клик, интеллектуальный подбор запросов, покупка самых лучших ссылок с высокой степенью качества у лучших бирж ссылок.
— Регулярная проверка качества ссылок по более чем 100 показателям и ежедневный пересчет показателей качества проекта.
— Все известные форматы ссылок: арендные ссылки, вечные ссылки, публикации (упоминания, мнения, отзывы, статьи, пресс-релизы).
— SeoHammer покажет, где рост или падение, а также запросы, на которые нужно обратить внимание.
SeoHammer еще предоставляет технологию Буст, она ускоряет продвижение в десятки раз,
а первые результаты появляются уже в течение первых 7 дней.
Зарегистрироваться и Начать продвижение
С начала 80-х годов прошлого века в технологии производства паракси-лола произошло коренное изменение. На смену его выделения методом низко-температурной кристаллизации пришел адсорбционный способ разделения. В нем использован молекулярно-ситовой эффект. Молекулы параксилола имеют наименьший диаметр, по сравнению с остальными изомерами, но соизмеримый с диаметром входных окон в адсорбционные полости цеолитов типа BaX. По-этому из смеси изомеров только молекулы параксилола могут проникнуть в по-ры вышеназванного адсорбента и адсорбироваться в них. В промышленных масштабах нашла распространение жидкофазная адсорбционная технология фирмы UOP, получившая название Parex (рис. 8.1). Пока эта технология счи-тается наиболее эффективной.
Увеличить производство параксилола можно путем включения в состав блока получения ароматических углеводородов установки трансалкилирования и диспропорционирования толуола и ароматики С9+ (технология Таторей). Сущность данного процесса заключается в том, что ароматческие углеводоро-ды С9+ и толуол под действием высоких температур в присутствии катализато-ра и водорода превращаются в ксилолы (в большей степени параксилол) и бен-зол. Причем выход ксилолов максимален (до 70%) при переработке сырья со-стоящего из 20-40 % толуола и 60-80 % С9+.
Приведенный на рисунке 8.1 набор процессов при производстве паракси-лола сложился в 1980-1990 годах и подавляющее количество нефтеперерабаты-вающих заводов в настоящее время использует их.
Однако в последние 2-3 года фирма Джи-Ти-Си, используя новые под-ходы, предложила более оптимальную (перспективную) схему комплекса полу-чения бензола и параксилола, принципиальная блочная схема которого приве-дена на рисунке 8.3. Наибольший интерес в нем представляют установки алки-лирования толуола метанолом (GT-TolAlk) и новая технология выделения па-раксилола методом кристаллизации (CrystPX).
В процессе GT-TolAlk реакция алкилирования толуола метанолом осуще-ствляется на цеолитсодержащем катализаторе. При этом образуются вода и смесь ксилолов, в основном, параксилол. Следует отметить, что бензол в этом процессе практически не образуется.
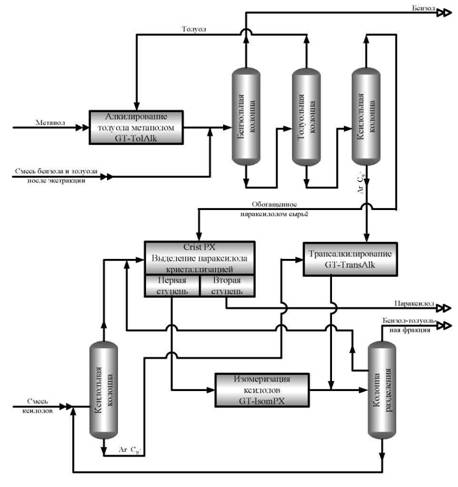
Рис. 8.3 – Современный комплекс по производству ароматических углеводоро-дов (по предложению фирмы GTC Technology Inc.)
В новой технологии низкотемпературной кристаллизации параксилола за счет использования более надежного и высокопроизводительного оборудова-ния, а также оптимизации тепловых и материальных потоков удается сущест-венно повысить эффективность работы установки и превзойти по некоторым показателям установку адсорбционного выделения параксилола.
Дополнительные преимущества перспективного комплекса производства параксилола заключаются в большей его гибкости и возможности переработки всех получаемых компонентов в параксилол.
В таблице 8.4 приведены сравнительные данные по традиционной и пер-спективной технологии выделения параксилола.
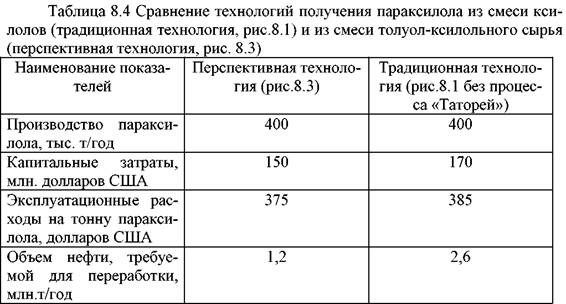
В ОАО Мозырский НПЗ в настоящее время отсутствуют мощности по производству индивидуальных ароматических углеводородов. Однако в его со-ставе имеется установка риформинга бензиновой фракции (секции 200 устано-вок ЛК-6У №1 и 2), производительность которых по сырью составляет 1060 тыс. тонн в год. До пуска комплекса каталитического крекинга риформат (ката-лизат риформинга) являлся главным компонентом для производства высокоок-тановых бензинов. В связи с ограничениями в странах Европы по содержанию ароматических углеводородов (особенно бензола) в бензинах, после ввода в эксплуатацию комплекса каталитического крекинга появилась возможность вывода части катализата риформинга в виде бокового погона в колонне стаби-лизации, с последующим выделением из него бензола методом экстракционной перегонки.
Для выделения ароматики можно применить высокоселективные сольвенты (экстрагенты), сила межмолекулярного взаимодействия которых с молекулами, содержащими ароматическое кольцо, отличается от силы взаимодействия с мо-лекулами неароматических соединений. Применяется два метода разделения:
экстракция жидкостью в жидкой фазе (Ж-Ж) и экстракционная дистилляция (ЭД).
На рисунке 8.4 показано, как влияет присутствие сольвента на разделение угле-водородов различных видов и с различным размером молекул. В состоянии равновесия с сольвентом в жидкой фазе всегда имеется некоторое количество загрязнений, которые должны быть удалены иными способами, чаще всего ― путем экстракционного отпаривания и водной промывки. В методе экстракции Ж-Ж применяется четыре основных технологических блока. Управление про-цессом является довольно сложным, и кроме того, сольвент подвержен загряз-нению более легкими углеводородами. Типовая конфигурация установки, рабо-тающей по процессу сульфолановой экстракции, показана на рисунке 8.5.
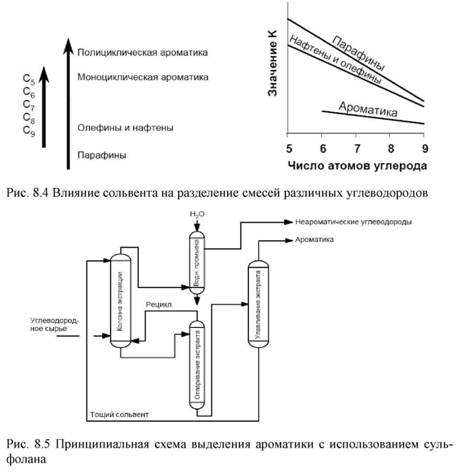
В проекте должно быть предусмотрено удаление легких примесей, экстраги-руемых вместе с ароматикой, путем отпаривания в отпарной колонне. На прак-тике в сольвенте происходит накопление легких и тяжелых углеводородов и неароматических примесей при достаточно большом числе циклов рециркуля-ции. Если в сырье присутствует достаточно много нафтенов или олефинов, этот эффект может быть еще более выражен, следствием чего является значитель-ный рост энергопотребления.
Принцип работы установки экстракционной дистилляции основан на измене-нии относительной летучести компонентов в присутствии высокоселективного сольвента. Этот эффект показан в правой части рисунка 8.4. Обычно считается, что экстракционная дистилляция позволяет перерабатывать только сырье, ком-поненты которого имеют не более двух различных чисел атомов углерода в мо-лекулах, например, С6 и С7. И это действительно так для большинства приме-няемых сегодня технологий экстракционной дистилляции. Однако при удачном выборе сольвента и эффективной конструкции установки ЭД возможно выпол-нить выделение бензола, толуола и ксилолов от прочих присутствующих в сы-рье компонентов с весьма широким диапазоном температур кипения. Эта тех-нология применяется в промышленном масштабе, начиная с 2000 года.
Улавливание БТК методом экстракционной дистилляции производится в двух колоннах, показанных на рисунке 8.6. Первой является колонна экстракцион-ной дистилляции, здесь происходит разделение компонентов сырья. Вторая ко-лонна применяется для регенерации сольвента, в ней сольвент отделяется от целевого продукта. В колонне ЭД в одной операции происходит достаточно полное разделение ароматики и неароматических углеводородов и отделение раствора ароматики в сольвенте от потока рафината. В связи с этим в данной технологии используется меньшее число блоков оборудования и требуются значительно меньшие капиталовложения по сравнению с технологией экстрак-ции Ж-Ж.
Сервис онлайн-записи на собственном Telegram-боте
Попробуйте сервис онлайн-записи VisitTime на основе вашего собственного Telegram-бота:
— Разгрузит мастера, специалиста или компанию;
— Позволит гибко управлять расписанием и загрузкой;
— Разошлет оповещения о новых услугах или акциях;
— Позволит принять оплату на карту/кошелек/счет;
— Позволит записываться на групповые и персональные посещения;
— Поможет получить от клиента отзывы о визите к вам;
— Включает в себя сервис чаевых.
Для новых пользователей первый месяц бесплатно.
Зарегистрироваться в сервисе
Эксплуатация установки ЭД очень проста и понятна, поскольку разделение достигается за счет дистилляции ― процесса, хорошо знакомого инженерам и операторам технологических установок. Регулирование основных параметров технологического процесса очень похоже на регулирование параметров стан-дартной ректификационной колонны.
От типа сольвента, применяемого для экстракционной дистилляции, зависит кратность циркуляции сольвента и число теоретических этапов, требующихся для экстракции. Фирмой Джи-Ти-Си используется сольвент патентованного состава, получивший название Тектив-100, компоненты которого взаимно усиливают действие друг друга и в итоге обеспечивают более высокую селек-тивность и растворяющую способность сольвента, чем любой из его компонен-тов в отдельности. В таблице 8.5 сравниваются некоторые промышленные соль-венты, наиболее часто применяемые для выделения ароматики. Сравнение про-водилось в стандартном эксперименте в условиях равновесия паровой и жидкой фаз для случая разделения бензола и н-гептана.
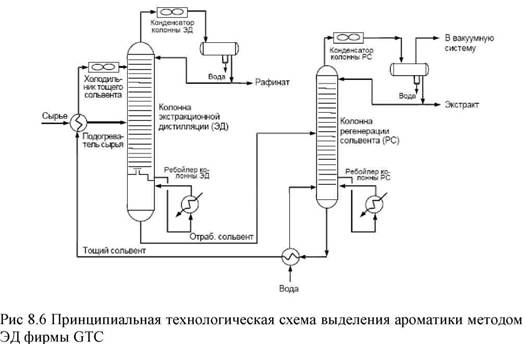
В чистой смеси двух компонентов (в отсутствие сольвента) бензол является бо-лее летучим соединением, чем гептан. Однако при добавлении высокоселек-тивного сольвента летучесть гептана становится выше летучести бензола. Чем больше отношение летучестей α, тем легче протекает разделение.
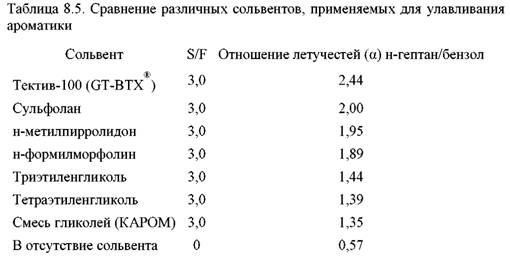
Это, в свою очередь, означает меньшее число ступеней экстракционной дис-тилляции, более полное улавливание ароматики, более высокую чистоту гото-вого продукта и меньшую кратность циркуляции сольвента. На практике менее эффективные сольвенты могут работать только с сырьем, содержащим лишь узкие фракции, что не позволяет применять их для выделения из широких фракций одновременно бензола и толуола либо бензола, толуола и ксилолов.
Принято считать, что сольвенты, имеющие особенно высокую селективность, не могут применяться в системах экстракционной дистилляции потому, что они проявляют тенденцию к образованию двух жидких фаз внутри колонны экс-тракционной дистилляции. Действительно, высокоселективные однокомпо-нентные сольвенты препятствуют перемешиванию и достижению равновесия между жидкими фазами; этот эффект может еще усилиться под влиянием дру-гих факторов. Все это может исказить характеристики традиционного процесса дистилляции. Однако особое сочетание состава применяемого сольвента и кон-струкции внутренних устройств колонны ЭД позволило успешно решить про-блему образования двух жидких фаз.
Все проблемы, связанные с селективностью сольвента, решены фирмой Джи-Ти-Си благодаря разработке системы сольвента патентованного состава, на-званного Тектив. Полезные свойства компонентов сольвента взаимно усили-ваются. Система сольвента имеет более высокую селективность и более высо-кую растворяющую способность по отношению к углеводородам , чем одно-компонентные сольвенты, такие как сульфолан, н-формилмор-фолин или гли-коли. Эффективность экстракции сольвентами Тектив превосходит анало-гичный показатель любой другой промышленно применяемой системы соль-вента.
Другим важнейшим фактором, определяющим эффективность процесса экс-тракционной дистилляции высокоселек тивным сольвентом, является высокая эффективность массообмена внутри колонны экстракционной дистилляции. Фирма Джи-Ти-Си применяет патентованные внутренние устройства колонн, которые обеспечивают тесный контакт и препятствуют нежелательному разде-лению фаз. В результате достигается устойчивая работа установки и исключи-тельно высокая эффективность разделения на каждой тарелке.
Важными факторами в современных системах улавливания и очистки бензола, толуола и ксилолов является обеспечение эксплуатационной технологичности и гибкости в отношении состава сырья. На следующем рисунке показаны сравне-ние показателей систем улавливания ароматики по технологиям Ж-Ж и ЭД.
На рис. 8.7 показан практически достижимый диапазон работы установок экс-тракции Ж-Ж в сравнении с системой экстракционной дистилляции по техно-логии GT-BTX. Системы экстракции Ж-Ж не могут работать с сырьем, содер-жащим менее 6 атомов углерода в молекулах, в связи с нежелательным накоп-лением компонентов С5 в циркулирующем потоке стриппинга. С другой сторо-ны, системы экстракции Ж-Ж не могут использоваться и при слишком большом числе атомов углерода в молекулах сырья в связи с неэффективностью селективного извлечения сольвентом тяжелой ароматики из жидкой фазы. Техноло-гия GT-BTX не имеет этих ограничений. Легкие компоненты легко переходят в поток рафината без необходимости организации внутреннего рецикла благода-ря присущей им меньшей летучести. Тяжелая ароматика, несмотря на меньшую склонность к растворению в сольвенте, полностью улавливается благодаря бо-лее высокой температуре кипения.
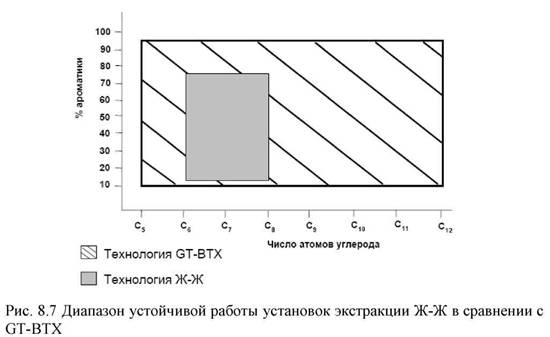
Если рассматривать сырье с точки зрения содержания ароматики, следует отме-тить, что системы экстракции Ж-Ж не подходят для непосредственной перера-ботки сырья с высоким содержанием ароматических углеводородов, так как, если в углеводородной смеси содержится более 75 – 80% ароматики, выделения фазы сольвента из смеси не происходит. Наоборот, при очень низком содержа-нии ароматики кратность циркуляции сольвента в системах Ж-Ж становится слишком большой для того, чтобы такие системы могли оставаться эффектив-ными. В технологии GT-BTX разделения фаз не происходит, и эффективное ве-дение процесса возможно практически во всем диапазоне концентраций арома-тики в сырье.
На рисунке 8.8 показаны области, в которых каждая из двух рассматриваемых технологий имеет преимущества перед другой технологией с точки зрения экс-плуатационных затрат. Легко видеть, что процессы экстракции Ж-Ж по энерго-затратам являются более эффективными, чем процесс GT-BTX, только в очень ограниченном диапазоне условий при весьма нетипичном составе сырья.
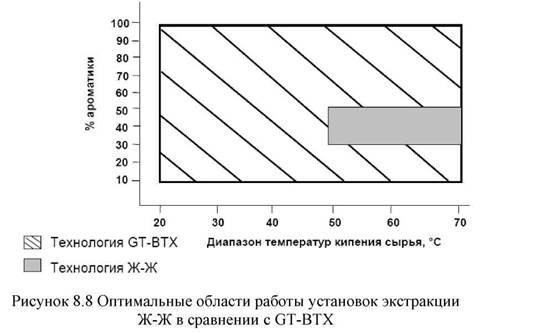
В таблице 8.6 дается общее сравнение технологии GT-BTX с типовым процес-сом экстракции Ж-Ж при переработке риформата типового состава.
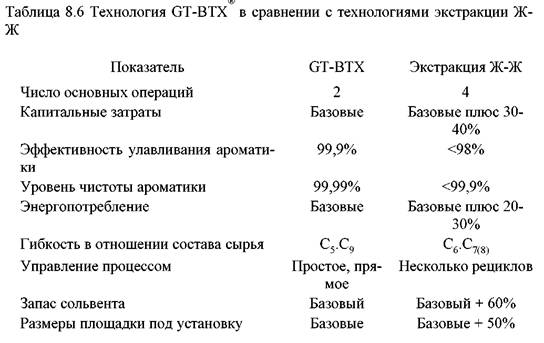
По сравнению с системами экстракции Ж-Ж другие системы экстракционной дистилляции имеют такие же преимущества, как и технология GT-BTX. Однако перечисленные в таблице 8.7 системы, использующие традиционные сольвенты, уступают технологии GT-BTX по следующим показателям:
• Низкая селективность сольвента. Следствием этого фактора являются боль-
шее число этапов разделения, более высокая кратность циркуляции сольвента, более низкая чистота или эффективность улавливания продукта, ограниченный диапазон температур кипения сырья и большие размеры оборудования.
• Вторичные свойства сольвента. Другие сольвенты, применяемые в процессах
экстракционной дистилляции, имеют более низкую температуру кипения, чем Тектив-100, что затрудняет выделение сольвента из потоков продуктов. Плотность Тектива-100 на 10% выше плотности традиционных сольвентов, поэтому при заданном массовом расходе сольвента его объемный расход будет меньше, с соответствующим уменьшением объема загрузки сольвента и размеров оборудования, работающего по процессу GT-BTX.
• В некоторых других технологиях ЭД применяются сольвенты, компоненты
которых содержат базовый азот. Даже в очень небольших концентрациях базовый азот является каталитическим ядом для катализаторов, применяемых на многих перерабатывающих установках, расположенных после установки экстракционной дистилляции. Сольвент Тектив-100 не содержит этих нежелательных соединений вовсе.
В других процессах ЭД для получения продукта приемлемого качества, не содержащего примесей сольвента, требуется более высокое энергопотребление.
Во многих установках ЭД прежнего поколения эффективность разделения не-
велика в связи с низкой эффективностью контакта несмешивающихся жидкостей, неудачной конструкцией оборудования либо по иным причинам.
Сравнение основных свойств сольвентов экстракционной дистилляции приводится в таблице 8.7.
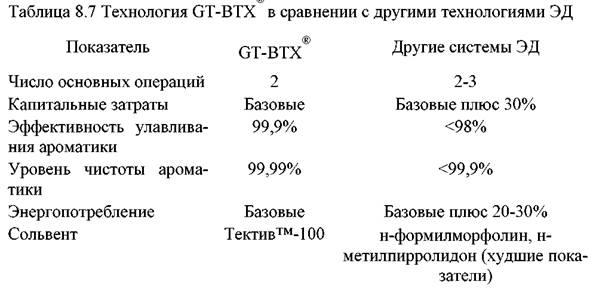
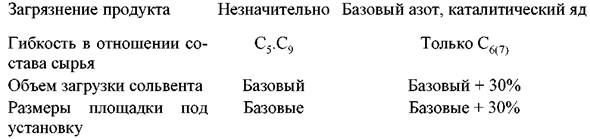
Наглядным примером, демонстрирующим преимущества технологии GT-BTX, является недавно пущенная в эксплуатацию новая установка экстракционной дистилляции фирмы Эль-Джи – Калтекс. Эта установка является крупнейшей в мире и, бесспорно, имеет наиболее высокие эксплуатационные показатели среди всех установок, работающих по технологии экстракционной дистилля-ции. Ее мощность по ароматике составляет 900 000 т/год.
Эксплуатационные характеристики установки с самого момента пуска были ис-ключительно высокими. Некоторые показатели, полученные по результатам первоначального пробного пробега, представлены ниже в таблице 8.8.
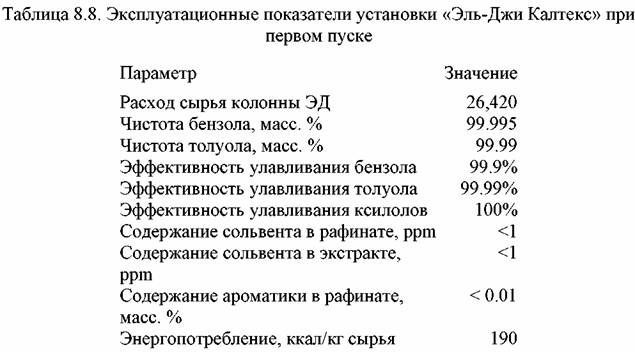
Установка экстракционной дистилляции, работающая по технологии GT-BTX, отличается исключительно высокой эксплуатационной технологичностью, ко-торая сохраняется в течение длительного времени. Свойства сольвента в про-цессе эксплуатации практически не меняются, продувок не требуется. Установ-ка имеет очень короткое время выхода на режим в случае аварийной остановки. Если в более сложных системах экстракции Ж-Ж, где применяется несколько контуров циркуляции, для выхода на режим требуется 24 часа, то операторы Эль-Джи – Калтекс добились вывода своей установки на стационарный ре-жим и производства продукции, отвечающей всем техническим требованиям, всего примерно через 4 часа после подачи сырья на установку.
|