Технология термической обработки металловИндукционная закалка
Индукционный нагрев для термической обработки, предложенный и разработанный проф. В. П. Вологдиным, является наиболее производительным и прогрессивным способом нагрева. При применении его для поверхностной закалки можно получить разный по глубине закаленный слой и закаливать детали разнообразной конфигурации; можно также полностью автоматизировать процесс закалки. Различают два метода поверхностной индукционной закалки.
При поверхностной закалке (поверхностном нагреве) глубина нагрева до температур закалки примерно равна глубине закаленного слоя. Структура сердцевины при этом остается без изменения, поэтому ее упрочняют предварительной термической обработкой (нормализацией или улучшением). Для поверхностного нагрева детали необходимо сконцентрировать большое количество электрической энергии в небольшом объеме металла (удельная мощность 0,5—1,5 кВт/см2) и проводить нагрев с большими скоростями (30—300° С/с). Время нагрева при этом составляет 1,5— 20 с.
При объемно-поверхностной закалке (глубинном нагреве) глубина нагрева до температур закалки больше слоя с мартен-ситной структурой, который определяется прокаливаемостью стали. Поэтому по данному методу необходимо закаливать стали, прокаливающиеся на меньшую глубину, чем толщина нагретого слоя. В участках детали, лежащих глубже зоны мартенситной структуры, но нагретых до температур закалки, образуются упрочненные зоны со структурой троостита или сорбита закалки.
В связи с нагревом на большую глубину значительно снижаются удельная мощность (до 0,05—0,2 кВт/см2) и скорость нагрева в области фазовых превращений (до 2—10° С/с); время нагрева составляет 20—100 с. Объемно-поверхностную закалку применяют для тяжелонагруженных деталей (шестерен, осей, крестовин и др.). Основное отличие индукционного нагрева от нагрева в печах и других нагревательных устройствах заключается в том, что тепло не подводится к детали от внешних источников (конвекцией или лучеиспусканием), а выделяется непосредственно в самой детали.
Рассмотрим принципиальную схему нагрева (рис. 72). Переменный электрический ток подводится к индуктору 2. Закаливаемую деталь 1 помещают в индуктор. Внутри индуктора возникает переменное магнитное поле, индуктирующее в поверхности детали электродвижущую силу, под действием которой в металле возникают электрические вихревые токи (токи Фуко), вызывающие нагрев детали до высокой температуры. Тепло выделяется на тех участках детали, которые подвергаются воздействию переменного магнитного поля и электрического тока. Это обеспечивает высокую скорость нагрева и позволяет производить местный нагрев.
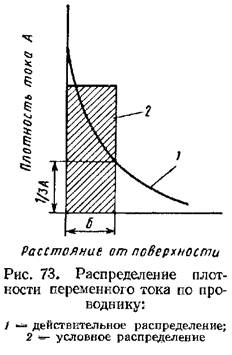
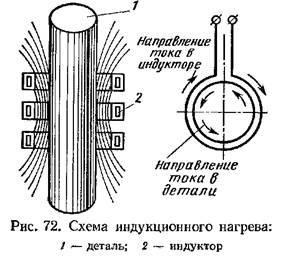
Характерным является распределение токов по сечению проводника (детали). Плотность протекающего переменного тока значительно больше у поверхности, чем во внутренних слоях проводника (рис. 73). Такое неравномерное распределение переменного тока в проводнике называется поверхностным эффектом. Благодаря этому эффекту деталь нагревается на определенную глубину, а сердцевина — незначительно за счет теплопроводности или совсем не нагревается. Плотностью тока в глубоко расположенных слоях детали пренебрегают; считают, что эта часть проводника как бы свободна от тока. Это допущение относится к тем слоям проводника, в которых плотность тока снижается приблизительно в 3 раза по сравнению с плотностью тока на поверхности проводника. Условно считается, что переменный ток идет не с неравномерной, а с одинаковой плотностью по слою проводника определенной глубины. Этот слой называется глубиной проникновения тока. Такое условное распределение плотности тока целесообразно в связи с тем, что на условной глубине проникновения тока выделяется около 87% всего тепла, выделяемого вихревыми токами, Таким образом, распределение тока по кривой заменяется условным распределением по заштрихованному участку.
Глубина проникновения тока при температуре 20° С
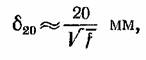

Приближенно такая глубина проникновения тока
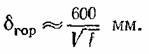
Учитывая изменение глубины проникновения тока при разной температуре, процесс индукционного нагрева можно представить в такой последовательности. Сначала быстро нагревается слой определенной глубины, равный глубине проникновения тока в холодный металл. После потери этим слоем магнитных свойств глубина проникновения тока увеличивается и начинает быстро нагреваться следующий слой, расположенный глубже, а повышение температуры в уже нагретом слое замедляется. После потери магнитных свойств вторым слоем начинает быстро нагреваться третий слой и т. д. Такая последовательность нагрева указывает на то, что при индукционном нагреве тепло быстро распространяется в связи с изменением магнитых свойств (рис. 75). Нагрев в пределах глубины проникновения тока в горячий металл протекает активно и осуществляется за счет преобразования электрической энергии в тепловую. Такой нагрев называется активным нагревом с помощью тока. Нагрев металла в пределах глубины проникновения тока в горячий метал я происходит быстро (за секунды).
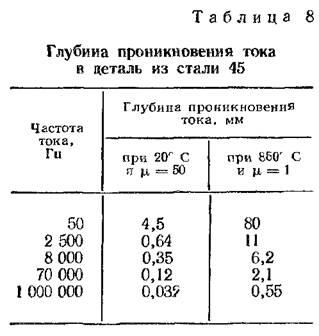
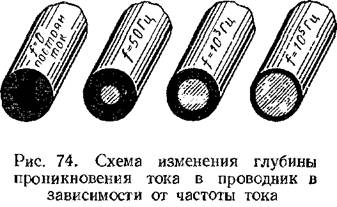
За пределы этой глубины про никновения тока (в глубоко- лежащие слои) тепло может распространяться лишь в результате теплопроводности.
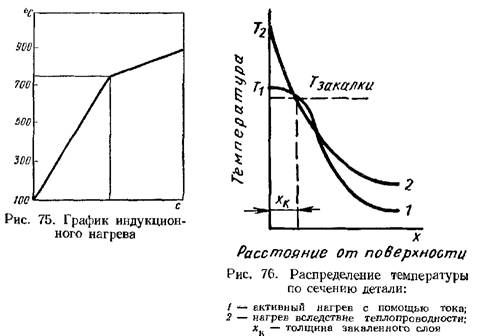
Распределение температуры по сечению детали при активном нагреве с помощью тока или в результате теплопроводности различное (рис. 76). Нагрев с помощью активного тока характеризуется малым перепадом температуры в пределах нагретого слоя и крутым спадом во внутреннем слое, еще не потерявшем маг-нитных свойств (кривая /). При нагреве вследствие теплопроводности перепад температуры большой (перегрев поверхностных слоев детали, кривая 2). Повышение температуры поверхности детали при нагреве вследствие теплопроводности необходимо для ускорения процесса теплопередачи, так как распространение тепла в результате теплопроводности совершается медленно. Чтобы при нагреве вследствие теплопроводности получить заданную глубину закаленного слоя, приходится производить нагрев длительное время, что приводит к переносу значительного количества тепла в сердцевину детали (большие тепловые потери), в связи с чем расход энергии увеличивается. Поэтому если необходимо нагреть поверхность детали на определенную глубину, то нужно применять нагрев заданного слоя с помощью активного тока. Это достигается правильным выбором определенных значений скорости нагрева и частоты тока. Сквозной нагрев детали обеспечивается большим диапазоном параметров нагрева, но и в этом случае необходимо осуществлять быстрый нагрев, чтобы уменьшит тепловые потери излучением с поверхности детали и увеличить производительность нагревательных устройств.
Забиваем Сайты В ТОП КУВАЛДОЙ - Уникальные возможности от SeoHammer
Каждая ссылка анализируется по трем пакетам оценки: SEO, Трафик и SMM.
SeoHammer делает продвижение сайта прозрачным и простым занятием.
Ссылки, вечные ссылки, статьи, упоминания, пресс-релизы - используйте по максимуму потенциал SeoHammer для продвижения вашего сайта.
Что умеет делать SeoHammer
— Продвижение в один клик, интеллектуальный подбор запросов, покупка самых лучших ссылок с высокой степенью качества у лучших бирж ссылок.
— Регулярная проверка качества ссылок по более чем 100 показателям и ежедневный пересчет показателей качества проекта.
— Все известные форматы ссылок: арендные ссылки, вечные ссылки, публикации (упоминания, мнения, отзывы, статьи, пресс-релизы).
— SeoHammer покажет, где рост или падение, а также запросы, на которые нужно обратить внимание.
SeoHammer еще предоставляет технологию Буст, она ускоряет продвижение в десятки раз,
а первые результаты появляются уже в течение первых 7 дней.
Зарегистрироваться и Начать продвижение
Индукторы. Качество деталей, закаленных при нагреве с помощью т. в. ч., в большой степени зависит от конструкции индуктора, его установки и расстояния между индуктором и нагреваемой деталью. Индукторы изготовляют из медных трубок, по которым для охлаждения пропускают воду. Изготовляют также индукторы, в которых нагревающая часть комбинируется с охлаждающим душевым устройством, через которое на нагретую деталь поступает охлаждающая жидкость. Для равномерного нагрева необходимо, чтобы расстояние от индуктора до детали было во всех точках одинаково. Обычно зазор между индуктором и нагреваемой деталью составляет 1,5—3 мм. Цилиндрические детали равномерно нагреваются благодаря вращению в индукторе. Для деталей каждого типа изготовляют отдельный индуктор, конфигурация которого соответствует форме закаливаемой детали.
Различают индукторы для нагрева: 1) внешней поверхности цилиндрических деталей; 2) внутренней поверхности цилиндрических деталей; 3) плоской и сложной поверхностей деталей. В одном и том же индукторе нельзя нагревать различные по форме и размеру детали.
Наиболее распространены конструкции одно- и многовитковых индукторов (рис. 77). Обычные индукторы имеют низкий к. п. д. (60—70%) вследствие рассеяния электромагнитного поля. Уменьшение потока рассеяния и концентрация электромагнитного поля в нужном направлении достигается применением индукторов с магнитол роводом. При наличии магнито про вода, с трех сторон охватывающего активную часть индуктора, происходит концентрация магнитного поля между индуктором и нагреваемой поверхностью. При этом резко возрастает к. п. д. индуктора. Магннтопроводы в виде пакета, набранного из тонких (0,2 мм), изолированных друг от друга листов трансформаторной стали, пригодны для индукторов, работающих при частотах до 10 000 Гц.
При работе на больших частотах такой магнитопровод не пригоден, так как быстро нагревается. Чтобы в процессе нагрева на больших частотах магнитопровод мало нагревался, его изготовляют из материалов, имеющих при таких частотах малые потери на гистерезис и вихревые токи. Такими материалами являются магнитодиэлектрики и новые материалы—оксиферы (ферриты). Магнитодиэлектрики представляют собой порошок магнитомяг-кого материала, смешанный и спрессованный с изолирующим веществом (диэлектриком), например, бакелитом, нитролаками, полистиролом и др. В качестве материала для магнитодиэлектри-
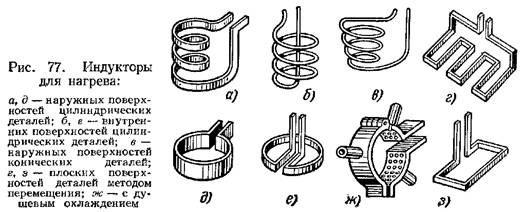
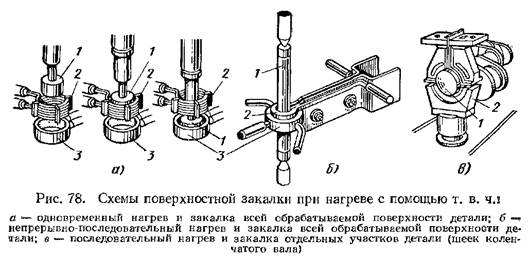
ков применяют карбонильное железо невосстановленное; карбонильное железо восстановленное, например, отожженное в атмосфере водорода; альсиферы — железо-кремний-алюминиевые сплавы; оксиферы (ферриты)1 — порошок оксидов металлов, смешанный, спрессованный и спеченный при 1100—1400° С. В производственных условиях наилучшие результаты получаются при использовании магнптопроводов, изготовленных из карбонильного железа (восстановленного) и из оксиферов.
Способы индукционной закалки. Индукционную закалку проводят различными способами в зависимости от размера и формы деталей и предъявляемых к ней требований. При закалке небольших деталей применяется нагрев и вслед за этим охлаждение всей поверхности. Деталь / (рис. 78, а) помещают в индуктор 2 и сразу нагревают, а затем всю поверхность, подлежащую обработке, охлаждают. Наиболее часто применяют душевое охлаждение. На внутренней поверхности индуктора имеются многочисленные отверстия, через которые после нагрева на поверхность поступает вода или другая закалочная среда. Закалку деталей значительной длины проводят непрерывно-последовательным способом. Деталь 1 (рис. 78, б) устанавливают в центрах и для равномерности нагрева непрерывно вращают с определенной скоростью. Закалка происходит при перемещении индуктора 2 снизу вверх (со скоростью от 0,3 до 3 см/с). При таком перемещении в магнитное поле индуктора 2 последовательно попадают один участок детали за другим. Под индуктором расположено охлаждающее устройство 3, представляющее собой согнутую кольцом трубу с многочисленными отверстиями на внутренней поверхности, через которые на нагретые участки детали поступает вода из душевого устройства. Таким образом, непрерывно-последовательно нагревается и охлаждается вся поверхность детали.
Если необходимо закалить отдельные части детали, то целесообразно применять способ последовательной закалки, при котором обрабатываемая поверхность нагревается и охлаждается по частям, например, последовательная закалка каждой шейки коленчатого вала 1 (рис. 78, в), каждого кулачка распределительного валика, каждого зуба крупномодульного зубчатого колеса и т. п. Для точной установки детали в индукторе и обеспечения определенного и одинакового нагрева и охлаждения каждой нагреваемой детали, от чего зависит качество индукционной закалки, применяют специальные приспособления, установки, автоматы и полуавтоматы различных конструкций.
Режим индукционного нагрева определяется частотой тока, удельной мощностью и временем нагрева. Частота тока определяет экономическую эффективность индукционного нагрева. Наиболее высокий к. п. д. индуктора (0,7—0,8) получается в том случае, когда наименьшая желательная частота тока, необходимая для осуществления индукционного нагрева,
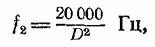
где D — диаметр нагреваемой детали, см.

При выборе частоты тока необходимо учитывать также и толщину закаленного слоя.
Наиболее выгодная толщина закаленного слоя и возможные пределы ее изменения для различных частот приведены в табл. 9.
которые изменяются в зависимости от удельной мощности и времени нагрева.
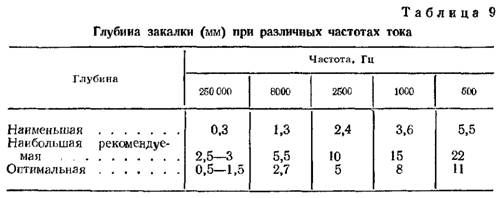
= 0,9 кВт/см2.
Получаемые данные только ориентировочные: по ним проводится закалка нескольких опытных деталей, после анализа которых режим нагрева может быть установлен более определенно. Индукционную закалку проводят на специальных установках, ток к которым подается от машинных или ламповых генераторов. Машинные генераторы имеют частоты от 1000 до 10 000 Гц при мощности 60—1000 кВт, а ламповые генераторы — частоту до 100 000 Гц и мощность от 5 до 220 кВт.
Сервис онлайн-записи на собственном Telegram-боте
Попробуйте сервис онлайн-записи VisitTime на основе вашего собственного Telegram-бота:
— Разгрузит мастера, специалиста или компанию;
— Позволит гибко управлять расписанием и загрузкой;
— Разошлет оповещения о новых услугах или акциях;
— Позволит принять оплату на карту/кошелек/счет;
— Позволит записываться на групповые и персональные посещения;
— Поможет получить от клиента отзывы о визите к вам;
— Включает в себя сервис чаевых.
Для новых пользователей первый месяц бесплатно.
Зарегистрироваться в сервисе
Свойства стали после индукционной закалки. Результаты индукционной закалки зависят от выбора марки стали, режимов предварительной термической обработки, режимов индукционного нагрева, охлаждения и низкого отпуска. По сравнению с обычной закалкой индукционная закалка придает стали более высокую твердость (на HRC 1—2) и прочность при относительно меньшем понижении вязкости, а также более высокий предел выносливости. Эти преимущества обусловлены измельчением зерен аустенита. С увеличением скорости нагрева (с повышением степени перенагрева) резко возрастает число центров перлито-аустенитного превращения. Поэтому образуется очень мелкое начальное зерно аустенита (из-за отсутствия выдержки при температуре закалки роста зерна не происходит). Измельчение зерна аустенита приводит к уменьшению размеров кристаллов мартенсита. При индукционном нагреве можно получить зерно аустенита 12—15-го балла (при нагреве в печах — 7—10-й балл). Для получения мелкого зерна аустенита при индукционной закалке необходимо применять стали, мало склонные к росту зерна аустенита, а также подвергать закалке детали с мелкодисперсной исходной структурой,
Повышение предела выносливости стали после индукционной закалки связано с распределением остаточных напряжений (рис. 80), В закаленном слое имеются остаточные напряжения сжатия, а за пределами закаленного слоя — напряжения растяжения. Причиной усталостных разрушений являются только растягивающие напряжения. При работе напряжения сжатия будут ослаблять растягивающие (разрушающие) напряжения, возникающие в результате действия внешних сил. Поэтому после индукционной закалки предел выносливости повышается.
Рассмотрим основные факторы, определяющие высокий комплекс свойств при индукционной закалке.
Скорость нагрева при индукционной закалке велика, а время нагрева мало (несколько секунд). Поэтому для завершения превращений стальную деталь нужно нагревать до более высоких температур, чем нормальная температура закалки при нагреве
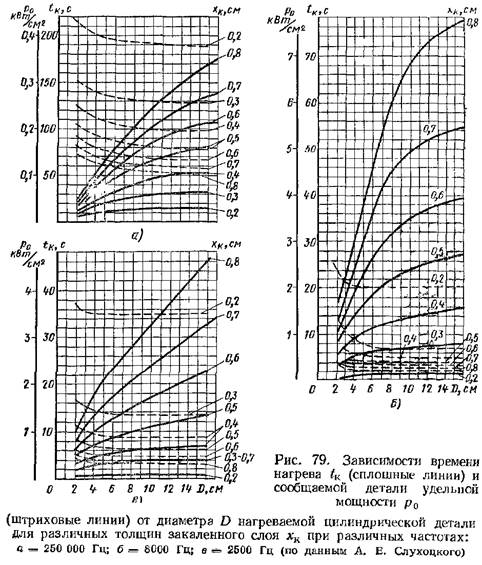

в печах (рис. 81). Чем больше в стали углерода, т. е. чем меньше избыточного феррита, тем меньше влияние скорости нагрева на температуру закалки. Температура индукционной закалки зависит не только от химического состава стали, но и от исходной структуры и скорости нагрева. Исходная структура стали может быть различной: она зависит от того, какой предварительной термической обработке подвергалась сталь: отжигу, нормализации или улучшению. На рис. 82 приведены интервалы оптимальных температур индукционной закалки стали 50 в зависимости от скорости нагрева и исходной структуры. Наиболее узкий интервал оптимальных температур индукционной закалки — для отожженной стали; наиболее широкий — для улучшенной. Этот интервал расширяется главным образом в результате понижения его нижней границы. Это объясняется тем, что исходные структуры отличаются степенью дисперсности фаз. Чем дисперснее исходная структура, тем быстрее протекает превращение при нагреве (превращение перлита в аустенит протекает медленнее, чем сорбита). Таким образом, дисперсность исходной структуры определяет режим нагрева и, следовательно, размер зерна аустенита. При нормализованной структуре доэвтектоидной стали можно получить зерно аустенита 11 —12-го балла; при закалке улучшенных структур получают сверхмелкое зерно аустенита 14—15-го балла. Скорость нагрева в области фазовых превращений определяется глубиной нагрева.

При объемно-поверхностной закалке целесообразно нагревать детали с изотермической выдержкой, чтобы нагреть их на заданную глубину. В результате нарушения режима нагрева в структуре доэвтектоидных сталей остается феррит или получается мартенсит неравномерного строения. Наличие в структуре игольчатого мартенсита является признаком перегрева.
При индукционной закалке необходимо охлаждать быстро, без подстуживания нагретой поверхности и распространения тепла в глубь детали. Можно применять различные способы охлаждения: закалку быстродвижущейся водой или маслом, погружение В воду или масло.
Широко применяют охлаждение душем или потоком воды (быстродвижущейся водой). Этот способ обеспечивает большую интенсивность охлаждения, фиксирует в мартенсите наибольшее количество углерода (если скорость охлаждения в интервале температур мартенситного превращения меньше 600° С/с, происходит отпуск мартенсита), что позволяет получить наиболее высокую твердость. При правильной конструкции охлаждающего устройства обеспечивается большая равномерность охлаждения; это позволяет проводить закалку деталей без образования трещин. При таком способе возможно дозированное охлаждение для проведения самоотпуска. Охлаждение потоком воды по сравнению с душем обеспечивает более равномерную подачу воды на закаливаемую поверхность.
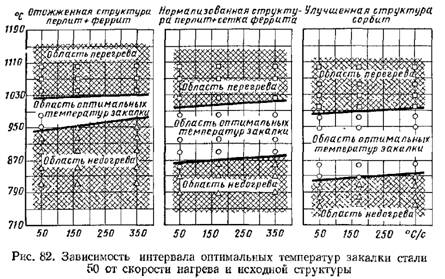
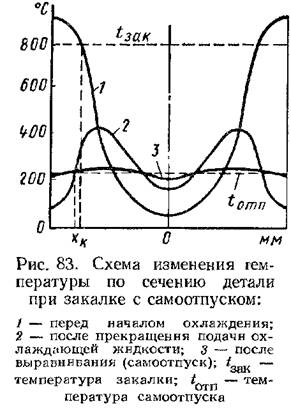
Для получения высокой твердости и предотвращения появления закалочных трещин скорость движения воды относительно детали должна быть в пределах 5—30 м/с. Применение самоотпуска (120—150° С) при интенсивном охлаждении быстродви-жущейся водой практически не снижает твердость (возможно снижение на HRC 1—2) и гарантирует от появления трещин. При индукционной закалке кроме охлаждения водой применяют также закалочную среду аква-пласт.
Отпуск и самоотпуск. После индукционной закалки детали подвергают низкотемпературному отпуску с нагревом в печи при температуре 150—250° С. Такой отпуск, незначительно снижая твердость, повышает прочность при изгибе (в 2 раза), снижает внутренние напряжения (на 25—30%) как на поверхности, так и в сердцевине, задерживает самопроизвольный распад мартенсита, приводящий к короблению и изменению размеров. Тонкостенные детали (толщина соизмерима с глубиной проникновения тока) могут подвергаться отпуску с индукционным сквозным нагревом. При индукционной закалке широко применяют самоотпуск. При закалке с самоотпуском охлаждение после нагрева производится не полностью, а прерывается с таким расчетом, чтобы за счет сохранившегося тепла произошел отпуск закаленной детали, аналогичный отпуску в печи.
Процесс закалки с самоотпуском приведен на рис. 83. Кривая 1 характеризует распределение температуры в нагретой детали. После ускоренного охлаждения в закаленном слое образуется структура мартенсита и температура падает до 100° С и ниже. В этот период распределение температуры характеризуется кривой 2. При прекращении охлаждения температура поверхностного слоя повышается (кривая 3) за счет сохранения высокой температуры непосредственно за закаленным слоем, что и приводит к отпуску мартенсита закаленного слоя. Изменяя время охлаждения, регулируют температуру самоотпуска. Для равномерного охлаждения закаливаемой поверхности время охлаждения при закалке должна быть не менее 1—1,5 с.
Основными параметрами режима самоотпуска являются температура и время выдержки. На результаты самоотпуска в основном влияет температура. Поэтому при снижении температуры необходимо увеличить время выдержки. Для получения равной твердости при самоотпуске (по сравнению с отпуском в печи) применяют более высокие температуры, например, Для дета чан из стали 45 на 75—85° С при температуре отпуска до 300" С к из 100—125° С при более высоких температурах.
Для обеспечения стабильных результатов самоотпуск;. процессы индукционного нагрева и охлаждения должны быть антомл тизированы. Вода для закалки должна иметь температуру в пределах 15—35° С, ее подачу регулируют с помощью реле времена. Применение самоотпуска, сокращает длительность обработка (отпуск в печи 1—1,5 ч), предохраняет от появления закалочных трещин, позволяет автоматизировать процесс термической обработки.
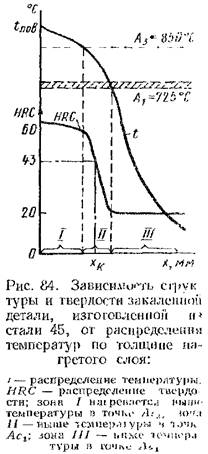
Поверхностная закалка стали (при поверхностном нагреве). При поверхностной закалке мартенентную структуру имеют только поверхностные слои, нагретые до температуры закалки. Большинство деталей, подвергающихся поверхностной индукционной закалке, изготовляют из среднеуглеродистых сталей (марок 40, !П) с суженными пределами по углероду. В автомобилестроении, тракторостроении, сельскохозяйственном машиностроении применяют легированные среднеуглеродастые стали (марок И)Х, 50Г и др.) Для изготовления режущего и измерительного инструмента, проходящего индукционную закалку, используют стали У7, У8, У10, У12, 9Х и др. Поверхностной индукционной закалке подвергают также детали из серых и ковких чугунов (нреимущесг венно с перлитной и перлитно-феррит-ной металлической основой). Толщина закаленного слоя составляет 0,5—8 мм.
Микроструктура доэвтектоидной стали характеризуется следующим распределением структурных составляющих (от периферии к центру): мартенсит (зона I); мартенсит, феррит и троостит (зона II); феррит и перлит (зона III) (рис. 84). Наличие в переходном слое феррита указывает на. более низкую температуру в этой зоне, при которой часть избыточного феррита не превратилась в аустенит.
Характеру распределения структур по сечению закаленной детали соответствует распределение твердости. Твердость поверхностного слоя с мартенсит-ной структурой составляет HRC 60—65. Обеспечение высоких твердости, прочности и пластичности детали зависит от глубины закаленного и переходного слоев. Рекомендуемая толщина закаленного слоя хк = (0,1-^-0,15) О, где О — диаметр детали, мм.
Переходный слой должен составлять 25—30% толщины закаленного слоя; чем крупнее деталь, тем больше должна быть толщина закаленного слоя,
Объемно-поверхностная закалка (при глубинном индукционном нагреве) разработана на автозаводе им. Лихачева и широко применяется в производстве для обработки тяжелонагруженных деталей автомобилей. Для получения требуемой толщины закаленного слоя тяжелонагруженных деталей при обычных способах индукционной закалки необходимо изготовлять эти детали из легированных сталей с большой прокаливаемостью. Данный метод поверхностной закалки обеспечивает возможность замены легированных сталей углеродистыми или низколегированными сталями с одновременным получением требуемой прочности и долговечности за счет реализации преимуществ глубинной закалки и поверхностной закалки при индукционном нагреве. Особенности поверхностной закалки при глубинном нагреве следующие: 1) глубина нагрева до температур закалки больше глубины закаленного слоя со структурой мартенсита (не менее, чем в 2 раза); при этом вся деталь или упрочняемая часть детали прогревается насквозь; при охлаждении быстродвижущейся водой закаливается поверхностный слой в соответствии с прокаливаемостью данной стали; в более глубоких слоях, также нагретых до температуры закалки, получается структура троостита или сорбита закалки; упрочнение сердцевины и закалка поверхности осуществляются за одну операцию, обеспечивая повышение конструктивной прочности деталей; 2) необходимость применения сталей с регламентированной (РП) и пониженной (ПП) прокаливаемостью; 3) режим нагрева должен обеспечить получение зерна аустенита не крупнее 11-го балла; скорость нагрева при этом составляет 2—10° С/с, удельная мощность 0,05—0,2 кВт/см2, время нагрева 20—100 с.
При поверхностной закалке с глубинным нагревом обязательно интенсивное охлаждение быстродвижущейся водой для создания перепада скоростей охлаждения по сечению упрочняемой детали. Скорость охлаждения поверхности должна быть не менее чем в 10 раз выше скорости охлаждения сердцевины. В этом случае поверхностный слой имеет твердость HRC 60—65, а более глубокие слои — твердость HRC 30—40.
Метод поверхностной закалки при глубинном нагреве целесообразно и экономически выгодно применять для тяжелонагруженных деталей и деталей сложной формы, для которых обычная поверхностная закалка не может быть осуществлена или не может обеспечить требуемой конструктивной прочности.
Стали для поверхностной закалки с пониженной и регламентированной прокаливаемостью. Стали, применяемые для изготовления деталей, упрочняемых поверхностной закалкой при глубинном нагреве, должны отвечать определенным требованиям. Содержание углерода (от 0,4 до 1,0%) должно обеспечить необходимую твердость поверхности и сердцевины при сохранении достаточной вязкости. Для снижения возможности появления закалочных трещин, повышения сопротивления хрупкому разрушению детали, обеспечения стабильности режимов индукционного нагрева стали должны иметь минимальную склонность к росту аустенитного зерна при нагреве под закалку. Толщина закаленного слоя должна составлять 10—15% рабочей толщины или диаметра и определяться прокаливаемостью стали.
металлургических заводов (химический состав стали 55ПП:
Новый метод поверхностной закалки деталей из стали марки 55ПП позволяет заменить процесс цементации легированных сталей 30ХГТ, 20ХНМ, 12Х2Н4А и др. при обеспечении такой же прочности деталей (HRC 58—63 на поверхности и HRC 30—40 в сердцевине).
|