Технология термической обработки металловТермическая обработка деталей машин
КОЛЕНЧАТЫЕ ВАЛЫ
Коленчатые валы работают в условиях высоких нагрузок, а шейки вала подвергаются интенсивному износу. Термическая обработка коленчатых валов преследует две цели: повысить их прочность и износостойкость. Изготовляют коленчатые валы из стали и из высокопрочного чугуна. Коленчатые валы автомобильных и тракторных двигателей, компрессоров изготовляют из сталей 45, 50Г, 30ХГ2, 47ГТ, 40ХН и др. (горячей штамповкой). Благодаря штамповке получается хорошая макроструктура — волокна металла не перерезаются, а соответствуют конфигурации вала (рис. 146).
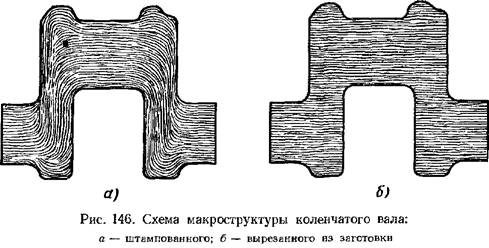
на 40—50° С и последующему
равномерному охлаждению на воздухе. Применяют также нормализацию штампованных заготовок коленчатых валов с использованием тепла после горячей штамповки. Например, штампованные заготовки валов из стали 45 подвергают нормализации в специальной щелевой нормализационной печи с подвесным конвейером. Перед поступлением в рабочую камеру печи, нагретую до 850° С, штампованные заготовки валов проходят через специальный коридор, где охлаждаются с 1050—1100° С до 600—650° С. После нормализации штампованные заготовки проходят через камеру предварительного охлаждения и выдаются на воздух.
Нагрев штампованных заготовок в подвешенном состоянии при нормализации в печи с подвесным конвейером имеет преимущество перед их нагревом в горизонтальном положении в толка-тельных печах, так как исключается неравномерный нагрев излучением пода печи и штампованные заготовки не деформируются от провисания под собственным весом.
После нормализации штампованные заготовки для обработки поступают на металлорежущие станки, а затем шатунные и коренные шейки валов подвергают поверхностной закалке при индукционном нагреве, для чего применяют автоматизированные установки, на которых производят последовательный нагрев и охлаждение каждой шейки. Время нагрева и охлаждения шеек регулирует реле времени. За счет сокращения длительности охлаждения проводится самоотпуск шеек (температура самоотпуска 240—250 С). Для закалки коленчатых валов в поточной линии устанавливают специальные станки. Получают закаленный слой толщиной 3—5 мм, а твердость поверхности шеек HRC 56—62, микроструктура слоя — мелкоигольчатый мартенсит. Если закаленный слой не доходит до переходной поверхности (рис. 147, а), то вредные напряжения растяжения, выходящие
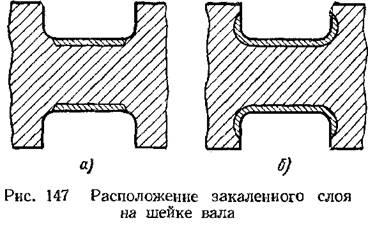
менее 0,005% 3; менее 0,12% Р. Повышенное
содержание марганца в чугуне необходимо для повышения стойкости эвтектоидного цементита, чтобы при термической обработке происходила сфероидизация, а не графитизация эвтектоидного цементита.
Термическая обработка коленчатых валов проводится по следующему режиму: нормализация — нагрев до 950—960° С, выдержка 8 ч, охлаждение со скоростью 30—60° С/мин до 600° С; отпуск — нагрев до 725—740° С, выдержка 8 ч, охлаждение на воздухе. Получаемая структура — зернистый перлит и шаровидный графит, твердость НВ 207—241.
Термическую обработку коленчатых валов целесообразно проводить в печах с защитной атмосферой, и для уменьшения коробления нагревать коленчатые валы на специальных поддонах.
|