Технология электрической сваркиХимический состав и строение флюса
Чем меньше объемная масса флюса, тем больше объем полости, образующейся вокруг столба дуги, и тем большей подвижностью обладает дуга При этом ширина шва увеличивается, а глубина провара уменьшается. Однако изменения глубины и ширины провара при применении флюсов стандартных марок столь невелики, что не требуют существенных изменений режима сварки и легко нивелируются за счет небольшой корректировки напряжения дуги,
Увеличение толщины электродного покрытия и введение в его состав тугоплавких веществ, способствующих образованию на конце электрода козырька, снижают подвижность столба дуги и, как следствие, уменьшают ширину шва и увеличивают глубину провара Глубина и ширина провара при сварке под флюсом АН-348-А и в углекислом газе, при прочих равных условиях, с достаточной для решения практических задач точностью могут быть признаны одинаковыми.
Изменение начальной температуры. В пределах естественных изменений, связанных со сваркой на морозе или с нагревом металла на солнце, начальная температура свариваемого изделия (—60—+80° С) не оказывает практического влияния на глубину провара и ширину шва Подогрев основного металла до температуры 100—400° С приводит к незначительному увеличению глубины провара и ширины шва Существенные изменения ширины и глубины провара имеют место при температуре предварительного подогрева от 500° С и выше, причем ширина провара увеличивается более интенсивно, чем его глубина С предварительным подогревом связано увеличение ширины последних слоев при сварке многослойных швов и при наплавке
Положение электрода в пространстве. На практике сварку ведут вертикальным электродом и с наклоном электрода вдоль шва углом вперед или назад по отношению к направлению сварки (рис 5-54, а, б, в) При сварке углом назад происходит более интенсивное, чем при сварке вертикальным электродом, вытеснение металла сварочной ванны из-под основания столба дуги, что приводит к некоторому увеличению глубины провара и уменьшению ширины шва. Сварка с наклоном электрода углом назад находит практическое применение главным образом при сварке электродами для глубокого провара
При сварке с наклоном электрода углом вперед столб дуги стремится занять положение, совпадающее с осью электрода При этом столб дуги большей своей частью располагается над поверхностью основного металла. Давление столба на поверхность сварочной ванны уменьшается, что приводит к заметному уменьшению глубины провара и увеличению ширины шва по сравнению со сваркой вертикальным электродом. Сварка электродом с наклоном углом вперед применяется для повышения

скорости сварки при одно- и многодуговой автоматической сварке под флюсом.
Наклон изделия относительно горизонтальной плоскости.
При сварке сверху вниз (на спуск) разность уровней расплавленного металла в головной и задней частях плавильного пространства уменьшается, несмотря на неизменное давление, оказываемое столбом дуги. Это приводит к увеличению толщины слоя жидкого металла, расположенного под основанием дуги, и к уменьшению глубины провара. Блуждание дуги по поверхности сварочной ванны при этом усиливается, что приводит к увеличению ширины шва. Поэтому при сварке на спуск уменьшается глубина провара и увеличивается ширина шва.
При сварке снизу вверх (на подъем) разница уровней расплавленного металла в головной и задней частях плавильного пространства увеличивается, а толщина слоя жидкого металла под основанием столба дуги уменьшается. При этом происходит более глубокое проплавление основного металла, т. е. глубина провара несколько увеличивается. Ширина шва при уменьшении блуждания столба дуги заметно уменьшается.
Нормальное, характерное для сварки в нижнем положении формирование шва достигается при механизированной сварке для угла наклона не более 3—4° и при ручной сварке покрытыми электродами не более 8—10°. При больших углах наклона нарушается нормальное формирование шва из-за подтекания жидкого металла под основание дуги при сварке на спуск и из-за непроваров и подрезов по кромкам при сварке на подъем.
Изменение формы шва путем сварки на спуск или на подъем мало применяется из-за сложности установки изделия под сварку и небольшой эффективности. Практическое применение сварка на спуск находит при выполнении круговых швов труб и сосудов малого диаметра. В этом случае электрод смещается от зенита с таким расчетом, чтобы сварка велась на спуск. При этом уменьшается опасность прожогов, улучшается формирование шва и предотвращается возможность стекания жидкого металла сварочной ванны. Сварку на подъем применяют для увеличения глубины проплавления при ручной сварке с глубоким проваром.
При дуговой сварке и наплавке значение коэффициента формы шва может изменяться от 0,8 до 20. Все изменения элементов режима, вызывающие уменьшение ширины шва и увеличение глубины провара, вызывают уменьшение, а все изменения элементов режима, увеличивающие ширину шва и уменьшающие глубину провара,— увеличение коэффициента формы шва.
Увеличение силы тока приводит к резкому возрастанию глубины провара и практически не отражается на ширине шва, а следовательно, приводит к снижению коэффициента формы шва. Увеличение скорости сварки уменьшает ширину шва и существенно не влияет на глубину провара. Следовательно, увеличение скорости сварки приводит к уменьшению коэффициента формы шва, а уменьшение скорости сварки — к повышению его значения. Увеличение напряжения дуги приводит к заметному увеличению ширины провара, к незначительному изменению глубины провара и, как следствие, к увеличению коэффициента формы шва. Уменьшение диаметра электрода или сварочной проволоки приводит к возрастанию глубины провара и уменьшению ширины шва, а следовательно, к довольно резкому уменьшению коэффициента формы шва. Наклон электрода углом вперед увеличивает коэффициент формы шва вследствие увеличения ширины шва и уменьшения глубины проплавления.
Забиваем Сайты В ТОП КУВАЛДОЙ - Уникальные возможности от SeoHammer
Каждая ссылка анализируется по трем пакетам оценки: SEO, Трафик и SMM.
SeoHammer делает продвижение сайта прозрачным и простым занятием.
Ссылки, вечные ссылки, статьи, упоминания, пресс-релизы - используйте по максимуму потенциал SeoHammer для продвижения вашего сайта.
Что умеет делать SeoHammer
— Продвижение в один клик, интеллектуальный подбор запросов, покупка самых лучших ссылок с высокой степенью качества у лучших бирж ссылок.
— Регулярная проверка качества ссылок по более чем 100 показателям и ежедневный пересчет показателей качества проекта.
— Все известные форматы ссылок: арендные ссылки, вечные ссылки, публикации (упоминания, мнения, отзывы, статьи, пресс-релизы).
— SeoHammer покажет, где рост или падение, а также запросы, на которые нужно обратить внимание.
SeoHammer еще предоставляет технологию Буст, она ускоряет продвижение в десятки раз,
а первые результаты появляются уже в течение первых 7 дней.
Зарегистрироваться и Начать продвижение
На значение коэффициента формы шва оказывают влияние и другие элементы сварочного режима, однако они сказываются в значительно меньшей степени, чем перечисленные выше.
При сварке стыковых однослойных швов, всех слоев многослойного шва, кроме первого и второго, и при наплавочных работах коэффициент формы шва можно изменять в желаемых пределах (рис. 5-55, а, б). При сварке угловых однослойных швов и первого слоя многослойных угловых или стыковых швов коэффициент формы шва или слоя, при котором обеспечивается удовлетворительное формирование, определяется геометрией соединения и может изменяться в весьма узких пределах (рис. 5-55, в, г). Увеличение его значения выше определенной величины приводит в этих условиях к подрезу кромок или к непровару притупления.
Коэффициент формы шва при сварке угловых швов и первого слоя многослойного шва должен находиться в пределах 1,4—2,3. Ограниченные возможности увеличения коэффициента формы шва в значительной степени определяют трудность обеспечения стойкости металла этих швов против кристаллизационных трещин, особенно при сварке основного металла с повышенным содержанием углерода.
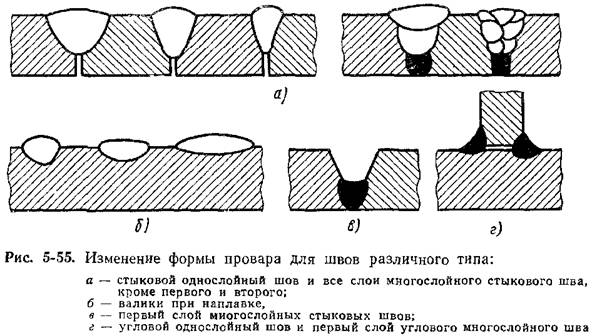
Нормальная форма поверхности шва обеспечивается при коэффициенте формы усиления более 5. При меньшем значении этого коэффициента не достигается плавности перехода от металла шва к основному металлу. Все изменения режима, уменьшающие ширину шва и увеличивающие количество вводимого в шов электродного металла (это прежде всего увеличение силы тока, уменьшение диаметра электрода и напряжения дуги), приводят к уменьшению коэффициента формы усиления (табл. 5-3).
(рис. 5-56). В зависимости от режима
сварки ширина шва и глубина металлической ванны, а следовательно, и коэффициент формы могут несколько изменяться по длине сварочной ванны. Однако при правильном выборе режима сварки ширина шва изменяется мало. Глубина металлической ванны может претерпевать более значительные изменения, но, как правило, достигает максимума посредине (по толщине металла). В дальнейшем изложении под шириной шва, глубиной металлической ванны и ее коэффициентом формы мы будем принимать значения этих величин по середине шва,
Форма и размеры металлической ванны оказывают существенное влияние на качество сварного соединения и определяются режимом сварки. Режим электрошлаковой сварки характеризуется величиной тока (или скоростью подачи электрода), напряжением сварки, скоростью сварки и толщиной металла, приходящейся на электрод (частное от деления толщины свариваемого металла на число электродов). На процессе формирования могут сказаться величина зазора, состав флюса, глубина шлаковой ванны, скорость поперечного перемещения электрода, вылет и диаметр сварочной проволоки. Обычно эти параметры режима изменяются мало.
При сварке электродной проволокой глубина шлаковой ванны в зависимости от силы тока составляет 25—70 мм, скорость поперечного перемещения 30—40 м/ч, сухой вылет электрода 60—70 мм и диаметр электрода 4—2 мм. Такие колебания не приводят к изменениям условий формирования шва. Более значительные отклонения указанных параметров, вызванные нарушением режима сварки, могут привести к изменению формы и размеров шва.
При электрошлаковой сварке одной электродной проволокой глубина металлической ванны и ширина шва зависят от всех элементов режима. Наибольшее влияние на этот параметр оказывает величина тока. С увеличением силы тока глубина металлической ванны увеличивается. Это, вероятно, обусловлено изменением погонной энергии сварки. Ток является тем элементом
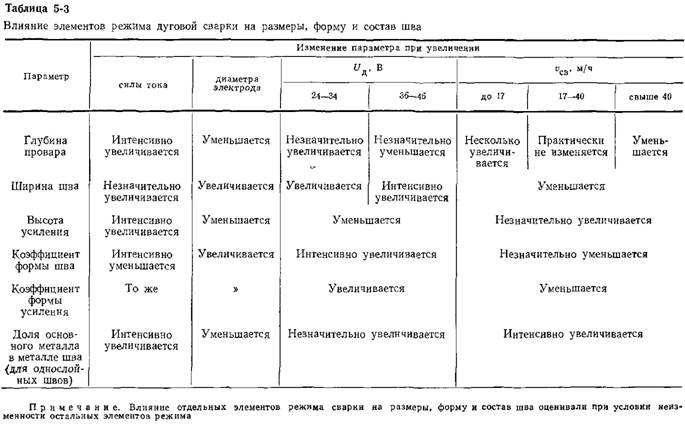
режима, за счет которого в сварочной практике изменяют в желаемом направлении глубину металлической ванны. На ширину шва величина тока влияет мало.
Увеличение напряжения при электрошлаковой сварке приводит к увеличению глубины металлической ванны в связи с повышением погонной энергии. С ростом напряжения в применяемых пределах ширина шва также увеличивается. На практике ширину шва изменяют в желаемом направлении путем изменения напряжения сварки.
При электрошлаковой сварке шов формируется в основном из дополнительного металла. Для заполнения зазора между свариваемыми кромками необходимо ввести строго определенное количество дополнительного металла. Поэтому увеличение скорости сварки достигается за счет повышения силы тока (скорости подачи сварочной проволоки) или увеличения числа электродов и всегда приводит к увеличению глубины металлической ванны. Изменение ширины шва в зависимости от скорости подачи сварочной проволоки (следовательно, и скорости сварки) имеет более сложный характер. Увеличение скорости сварки сначала приводит к увеличению ширины шва, а затем к снижению ее.
Увеличение толщины свариваемого металла, приходящейся на один электрод, приводит к уменьшению ширины шва и глубины металлической ванны, что связано с изменением погонной энергии. Электропроводность флюса заметно влияет на глубину металлической ванны и ширину шва. Снижение электропроводности флюса, при прочих равных условиях, приводит к росту глубины металлической ванны и ширины шва в результате увеличения теплоты, выделяемой в ванне.
Коэффициент формы металлической ванны находится в обратной зависимости от величины тока и скорости сварки и в прямой зависимости от напряжения на электродах и толщины металла, приходящейся на электрод Общие данные о характере влияния элементов режима сварки на размеры и форму шва при электрошлаковой сварке приведены в табл 5-4
Сварка двумя и более сварочными проволоками и электродной пластиной имеет свои особенности Однако общие закономерности остаются теми же, что при сварке одной сварочной проволокой. Для повышения производительности электрошлаковой сварки процесс стремятся вести при минимальном зазоре между свариваемыми кромками. В металлическую ванну вводят дополнительный металл (порошок, крупку и др.) и увеличивают коэффициент наплавки.
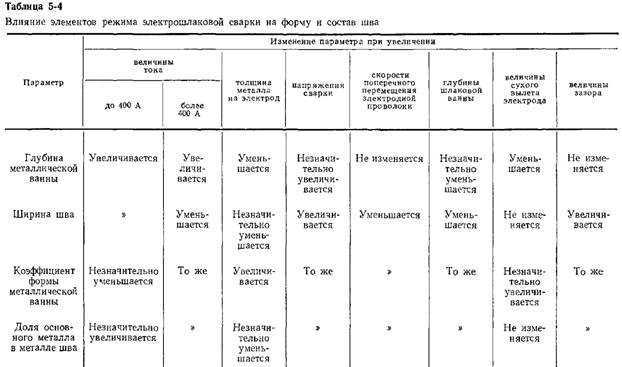
Зависимость между режимом сварки и составом шва при дуговой и электрошлаковой сварке. При сварке неплавящимся электродом без присадочного металла шов полностью состоит из расплавленного основного металла. При сварке плавящимся электродом или неплавящимся электродом с присадочным металлом металл шва представляет собой сплав основного и дополнительного (электродного или присадочного) металлов. Состав шва определяется долями участия того и другого металла в металле шва, зависящими от режима сварки, характера подготовки кромок и изменений, происходящих в составе шва при взаимодействии электродного металла и металла сварочной ванны с газами и шлаком. Долю участия основного и дополнительного металлов определяют обычно по поперечному макрошлифу. При дуговой однослойной сварке долю участия дополнительного металла определяют по формуле
Сервис онлайн-записи на собственном Telegram-боте
Попробуйте сервис онлайн-записи VisitTime на основе вашего собственного Telegram-бота:
— Разгрузит мастера, специалиста или компанию;
— Позволит гибко управлять расписанием и загрузкой;
— Разошлет оповещения о новых услугах или акциях;
— Позволит принять оплату на карту/кошелек/счет;
— Позволит записываться на групповые и персональные посещения;
— Поможет получить от клиента отзывы о визите к вам;
— Включает в себя сервис чаевых.
Для новых пользователей первый месяц бесплатно.
Зарегистрироваться в сервисе

гдедоп-—площадь сечения части шва, образовавшейся за счет электродного и присадочного металла; Fm—общая площадь сечения шва; F0 — площадь сечения части шва, образовавшейся за счет расплавления основного металла.
При ручной сварке FAon определяется как сумма площадей разделки или зазора и усиления шва. При механизированной сварке с постоянной скоростью подачи сварочной проволоки FAon определяют по формуле
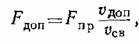
где Fn? — площадь сечения сварочной проволоки; иэл — скорость подачи сварочной проволоки; vCB — скорость сварки.
Общая площадь сечения шва определяется путем замера ее планиметром или подсчета площади фигуры по очертаниям, приближающимся к очертаниям провара.
При дуговой сварке многослойных швов для определения доли дополнительного металла обычно пользуются формулой (5-2), хотя она и не отражает действительного положения, так как в этом случае кроме основного и дополнительного металлов имеется еще и металл нижележащих слоев, который по своему составу отличается и от основного, и от дополнительного металлов.
При электрошлаковой сварке долю электродного металла в металле шва уэл с достаточной для практики точностью определяют по формуле

где s—толщина основного металла; а—ширина зазора; Ъ — ширина шва.
Долю участия основного металла ь MefaJHrte ый$& у0 йрй Ыё% методах сварки определяют по формуле
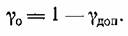
Доля участия основного металла при используемых режимах сварки плавящимся электродом составляет 15—80%. Меньшая цифра относится к вибродуговой наплавке, а большая — к сварке на больших скоростях под флюсом. Доля участия основного и электродного металлов в металле однопроходного шва зависит от элементов режима сварки.
При дуговой сварке повышение силы тока приводит к увеличению количества расплавляемого основного металла и вводимого в шов электродного металла, при этом количество расплавляемого основного металла растет более интенсивно, что приводит к увеличению доли основного металла в металле шва. При электрошлаковой сварке повышение силы тока всегда сопровождается увеличением скорости сварки, что приводит к уменьшению ширины провара и снижению доли основного металла в металле шва.
Увеличение напряжения дуги и напряжения сварки приводит к незначительному уменьшению количества вводимого в шов электродного металла (за счет снижения коэффициента наплавки) и к увеличению количества расплавляемого основного металла. Следовательно, увеличение напряжения приводит к повышению, а уменьшение— к снижению доли основного металла в металле шва.
Увеличение скорости при дуговой сварке приводит к уменьшению количества вводимого в шов электродного и расплавляемого основного металлов. Количество электродного металла снижается более интенсивно, чем количество расплавляемого основного металла, поэтому доля основного металла в металле шва с увеличением скорости сварки увеличивается. При электрошлаковой сварке наблюдается обратная зависимость.
Увеличение диаметра электрода приводит к снижению доли основного металла в металле шва.
Состав сварочной проволоки оказывает существенное влияние на величину коэффициента плавления электрода. Так, высоколегированная проволока обладает более высоким коэффициентом плавления, чем низкоуглеродистая. Низкоуглеродистая проволока, содержащая кремний, имеет несколько более высокий коэффициент плавления, чем такая же проволока без кремния. Увеличение коэффициента плавления проволоки приводит к некоторому возрастанию доли электродного металла в металле шва.
Тип шва и характер подготовки кромок оказывают существенное влияние на долю участия основного металла в металле шва. Характер этого влияния ясен из схемы, приведенной на рис. 5-23. При наплавке валика или сварке стыкового шва без разделки кромок электродный металл используется только для создания усиления. Наличие обязательного зазора или разделки кромок при сварке стыковых или угловых швов Приводит к тому, что электродный металл расходуется на образование расчетного сечения шва и располагается на месте удаленного в процессе разделки кромок основного металла. В результате доля основного металла в металле шва снижается.
При сварке постоянным током прямой полярности несколько уменьшается глубина провара основного металла и увеличивается коэффициент плавления электродного металла. Это приводит к заметному снижению доли основного металла в металле углового шва и в наплавке по сравнению со сваркой переменным током или постоянным током обратной полярности.
Во многих случаях приобретает первостепенный интерес уменьшение доли основного металла в металле шва. Это важно при сварке основного металла, содержащего повышенные количества элементов, снижающих стойкость металла шва против кристаллизационных трещин и ухудшающих другие свойства металла шва (стойкость против перехода в хрупкое состояние, коррозионную стойкость). Особенно это относится к сварке под флюсом, где доля основного металла в металле шва при типичных режимах достигает 70%. Для снижения доли основного металла в металле шва кроме изменения в желаемом направлении перечисленных выше элементов режима прибегают также к многослойной сварке (вместо однослойной), сварке двумя дугами, сварке по присадочной проволоке, сварке с наполнителями и другим технологическим приемам.
Выбор режима сварки
Элементы режима сварки оказывают существенное влияние на форму и состав шва, и путем изменения( их значения можно достичь желаемого результата при различном их сочетании. Основная задача, возникающая перед технологом при выборе режима сварки, сводится к определению такого сочетания элементов режима, при котором обеспечивается требуемое качество сварного соединения при максимальной производительности и минимальной стоимости процесса.
Для данного способа сварки, марки основного металла и типа шва существует оптимальный режим, который в зависимости от конкретных условий может изменяться только в узких пределах. При разработке технологии оптимальный режим подбирают экспериментальным путем или путем расчета на основе приведенных выше уравнений распространения теплоты при сварке. Если из-за отсутствия источников питания необходимой мощности, плохой подготовки под сварку, отсутствия электродов нужного диаметра и других технических причин нельзя применить оптимальный режим сварки, то приемлемый для данных условий режим выбирают опытным путем.
|