Технология электрической сваркиВлияние растягивающих напряжений
В реальных условиях сварки практически невозможно полностью устранить влияние растягивающих напряжений на кристаллизующийся металл сварочной ванны. Поэтому задача сводится к уменьшению величины этих напряжений, к отдалению момента возрастания их до значения, которое может вызвать пластическую деформацию металла шва, приводящую к его разрушению. Это может быть достигнуто путем рационального конструирования узлов и элементов, уменьшения количества и сосредоточения швов, выбора оптимальной формы разделки кромок, устранения излишней жесткости узлов и других мер.
Уменьшение влияния растягивающих напряжений за счет технологических мер достигается путем предварительного подогрева, рационального порядка наложения швов и выбора способов и режимов сварки, обеспечивающих минимальную величину этих напряжений. Положительное влияние подогрева обусловлено отдалением момента возникновения растягивающих напряжений и снижением скорости их нарастания в период, когда металл шва обладает пониженной пластичностью.
Предварительный подогрев является весьма эффективной мерой повышения стойкости металла шва против кристаллизационных трещин при сварке конструкционных и других сталей. Температура предварительного подогрева, при которой не наблюдается образования трещин, зависит от химического состава металла шва, конструкции и сечения деталей, а также других факторов и обычно изменяется в пределах 150—500° С. Для
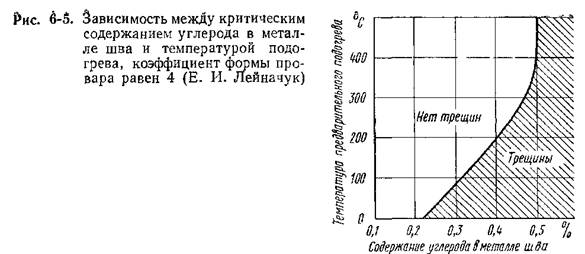
иллюстрации сказанного на рис. 6-5 приведена зависимость между значением температуры подогрева и критическим содержанием углерода в металле шва.
При рациональном порядке наложения швов возможна сварка деталей с оптимальным их закреплением, что приводит к снижению растягивающих напряжений. На практике достаточно часто, особенно при сварке под флюсом низколегированных и среднелегированных сталей, наблюдается образование трещин в участках шва, непосредственно прилегающих к сборочным прихваткам, и у планок, служащих для вывода начала и конца шва за пределы соединения (рис. 6-6).
При расплавлении сборочной прихватки зазор между свариваемыми кромками стремится увеличиться, в результате чего создаются значительные растягивающие напряжения. Эти напряжения и приводят в некоторых случаях к образованию трещин в неуспевшем закристаллизоваться участке шва. Для устранения этого рекомендуется ставить прихватки со стороны, обратной наложению первого слоя (при двусторонней сварке), или уменьшать расстояние между прихватками.
Образование трещин в начале и конце шва обусловлено тем, что нежесткие выводные пленки не могут удержать концы листов
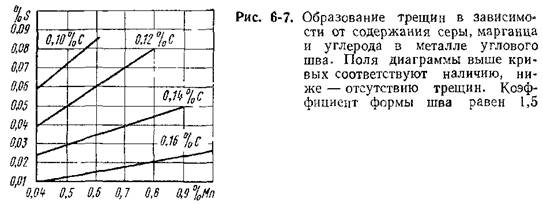
от расхождения. Радикальной мерой предотвращения таких трещин является надежное закрепление концов свариваемых деталей в приспособлении или увеличение жесткости выводных планок.
Влияние химического состава металла шва. Химический состав металла шва оказывает первостепенное влияние на его стойкость против кристаллизационных трещин. Все элементы, входящие в состав металла шва, условно могут быть отнесены к трем основным группам,
Первая группа — элементы, присутствие которых снижает стойкость металла шва против кристаллизационных трещин. Такие элементы принято называть вредными. Вторая группа — элементы, которые в зависимости от их сочетания и концентрации оказывают положительное (полезные примеси) или отрицательное (вредные примеси) влияние на стойкость металла шва против кристаллизационных трещин.
Третья группа — элементы, присутствие которых не оказывает влияния на стойкость металла шва против кристаллизационных трещин.
Сера — вредная примесь. Повышение содержания серы в металле шва резко снижает его стойкость против кристаллизационных трещин. Сера практически нерастворима в твердом железе, а поэтому находится в швах на стали в виде неметаллических сульфидных включений. Непосредственной причиной образования кристаллизационных трещин от серы являются легкоплавкие сульфидные прослойки, располагающиеся по границам кристаллитов металла шва. Критическое содержание серы в шве,—• т. е. ее содержание, выше которого наблюдается образование трещин, зависит от величины растягивающих напряжений, формы шва и его химического состава.
Для швов на углеродистых сталях наибольшее влияние на образование трещин кроме серы оказывают также углерод и марганец. На рис. 6-7 представлена зависимость между критическим содержанием серы и содержанием углерода и марганца в металле шва.
Все остальные факторы, определяющие стойкость металла шва против кристаллизационных трещин, подразумеваются постоянными. Приведенные данные свидетельствуют о том, что снижение содержания углерода приводит к снижению вредного влияния серы (критическое содержание серы повышается). Марганец в определенных пределах снижает вредное действие серы.
Сера переходит в металл шва из основного и дополнительного (присадочного) металлов и из материалов, входящих в состав электродного покрытия или флюса. Согласно действующим стандартам содержание серы в конструкционных сталях не должно превышать 0,05%, а обычно составляет 0,03—0,04%. Снижение содержания серы в стали в сравнении с этими количествами возможно, но связано с повышением стоимости выплавки стали.
Из экономических соображений целесообразнее снижать содержание серы в сварочных материалах, в частности в сварочной проволоке. ГОСТ 2246—70 ограничивает содержание серы в низкоуглеродистой и легированной сварочной проволоке в пределах 0,04—0,02"%. В некоторых марках высоколегированной проволоки это ограничение составляет 0,015%. Жестко ограничено содержание серы в электродных покрытиях и сварочных флюсах. Значительный практический интерес представляет обессеривание сварочной ванны за счет применения специальных флюсов и покрытий, при которых достигается переход серы из металла сварочной ванны в шлак.
Фосфор часто оказывает вредное влияние на стойкость металла шва против кристаллизационных трещин и приводит к резкому снижению ударной вязкости металла, особенно при пониженных температурах. Интенсивность влияния фосфора на образование кристаллизационных трещин пропорциональна содержанию легкоплавких фосфорсодержащих включений на границах кристаллитов металла шва. Возможность образования таких включений тем больше, чем выше концентрация фосфора и ниже его растворимость в твердом металле.
Забиваем Сайты В ТОП КУВАЛДОЙ - Уникальные возможности от SeoHammer
Каждая ссылка анализируется по трем пакетам оценки: SEO, Трафик и SMM.
SeoHammer делает продвижение сайта прозрачным и простым занятием.
Ссылки, вечные ссылки, статьи, упоминания, пресс-релизы - используйте по максимуму потенциал SeoHammer для продвижения вашего сайта.
Что умеет делать SeoHammer
— Продвижение в один клик, интеллектуальный подбор запросов, покупка самых лучших ссылок с высокой степенью качества у лучших бирж ссылок.
— Регулярная проверка качества ссылок по более чем 100 показателям и ежедневный пересчет показателей качества проекта.
— Все известные форматы ссылок: арендные ссылки, вечные ссылки, публикации (упоминания, мнения, отзывы, статьи, пресс-релизы).
— SeoHammer покажет, где рост или падение, а также запросы, на которые нужно обратить внимание.
SeoHammer еще предоставляет технологию Буст, она ускоряет продвижение в десятки раз,
а первые результаты появляются уже в течение первых 7 дней.
Зарегистрироваться и Начать продвижение
Так как растворимость фосфора в аустените меньше, чем в феррите, опасность образования кристаллизационных трещин от фосфора значительно больше в аустенитных швах. Наиболее Опасен фосфор для швов с чисто аустенитной структурой. Если же на ранних стадиях кристаллизации металла шва кроме аустенита образуется и феррит, опасность образования трещин значительно уменьшается, так как большая часть фосфора растворяется в металле. Фосфор является потенциальной причиной кристаллизационных трещин и в швах на некоторых средиелегированных сталях.
Влияние фосфора и серы на образование кристаллизационных трещин взаимно усиливается тем, что места ликвации этих элементов в металле шва совпадают. Углерод также усиливает вредное влияниефосфора. При обычных концентрациях фосфор в низкоуглеродистых и низколегированных швах кристаллизационных трещин не вызывает.
Фосфор попадает в металл шва из основного и электродного металлов и из материалов, входящих в состав покрытий и флюсов. В конструкционных углеродистых сталях содержание фосфора допускается не более 0,055%, а в легированных сталях — не более 0,03%. Согласно ГОСТ 2246—70 содержание фосфора в сварочной проволоке не должно превышать 0,04%. В электродное покрытие и флюс фосфор попадает в основном с марганцевой рудой.
Углерод является важнейшим элементом, определяющим структуру и свойства металла шва, его прочность и поведение при эксплуатации. Вместе с тем углерод оказывает резко отрицательное влияние на стойкость металла шва против кристаллизационных трещин. В швах на углеродистых и низколегированных сталях углерод усиливает вредное действие серы. При сварке высоколегированных сталей углерод способствует образованию по границам кристаллитов легкоплавких пленок карбидного происхождения, что снижает стойкость швов против кристаллизационных трещин. Критическое содержание углерода зависит от конструкции узла, наличия или отсутствия предварительного подогрева, формы шва и содержания в нем других элементов, в первую очередь серы (см. рис. 6-7).
Углерод попадает в металл шва из основного и электродного или присадочного металлов. Чтобы снизить содержание углерода в металле шва, применяют сварочную проволоку и электродные стержни с низким содержанием углерода, уменьшают долю основного металла в шве. За счет взаимодействия металла с газовой и шлаковой фазами может происходить окисление (угар) углерода, что также снижает его содержание в шве.
Так как углерод является наиболее дешевым и недефицитным элементом, повышающим прочность металла шва, задача рациональной технологии сварки должна заключаться в сохранении в металле шва возможно более высокого количества углерода, еще не вызывающего снижения стойкости против трещин.
Кремний способствует образованию кристаллизационных трещин в швах на углеродистых сталях. Однако его вредное действие в этом отношении значительно слабее, чем углерода. В чисто аустенитных хромоникелевых швах кремний более опасен в отношении образования кристаллизационных трещин, чем в швах углеродистой стали. Это обусловлено выделением на границах кристаллитов пленок силицидов и других легкоплавких неметаллических соединений. Появление ферритной составляющей в структуре аустенитных швов повышае! их стойкость против образования трещин.
Кремний переходит в шов из основного и дополнительного металла и за счет восстановления его из электродного покрытия или флюса. Рациональная технология сварки должна обеспечи вать присутствие в шве кремния в количестве, повышающем стойкость его против пор (см. ниже), но не вызывающем снижения стойкости против образования трещин. Растворяясь в феррите, кремний повышает его прочность, что весьма желательно. Оптимальное содержание кремния зависит от способа сварки, типа шва и состава основного металла и при сварке углеродистых ц низколегированных конструкционных сталей колеблется в пределах 0,15—0,6%.
Никель при небольших концентрациях в металле шва не оказывает влияния на стойкость его против возникновения кристаллизационных трещин. При высоких концентрациях (свыше 1—2%) никель усиливает вредное влияние серы, способствуя этим образованию кристаллизационных трещин. Это влияние никеля обусловлено образованием легкоплавких включений сульфида никеля.
Никель является ценным легирующим элементом. Растворяясь в феррите, он повышает прочность и ударную вязкость металла шва при обычных и пониженных температурах при сохранении высокой пластичности. Однако ввиду сравнительно высокой стоимости никель применяют лишь там, где замена его другим, более дешевым элементом, не дает нужного эффекта. При сварке углеродистых и низколегированных конструкционных сталей никель попадает в шов из основного и дополнительного металлов в количествах, не оказывающих отрицательного влияния на стойкость металла шва против образования трещин.
Марганец уменьшает вредное влияние серы, повышая стойкость шва на углеродистых, низколегированных и хромоникелевых аустенитных сталях против образования кристаллизационных трещин. Марганец обладает более высоким, по сравнению с железом, химическим сродством к сере. При достаточно высокой его концентрации в металле шва сера связывается в тугоплавкий сульфид марганца, включения которого менее опасны в отношении возникновения трещин, чем включения сульфида железа.
При высоком содержании марганца в металле шва в присутствии углерода возможно возникновение кристаллизационных трещин, вызванных легкоплавкой карбидной эвтектикой. В связи с этим в зависимости от концентрации марганец оказывает двойственное влияние на стойкость швов против образования кристаллизационных трещин. Так, например, для швов, содержащих 0,10—0,12% С, повышение содержания марганца до 2,5% оказывает положительное влияние на стойкость металла шва против образования трещин. Повышение содержания марганца от 2,5 до 4% не оказывает влияния, а дальнейшее повышение его содержания уменьшает стойкость металла шва против образования трещин. При повышении содержания углерода в металле шва полезное влияние марганца сказывается в более узких пределах концентраций. Так, при содержании 0,13—0,2% С полезное влияние марганца отмечается при содержании его до 1,8%.
Сервис онлайн-записи на собственном Telegram-боте
Попробуйте сервис онлайн-записи VisitTime на основе вашего собственного Telegram-бота:
— Разгрузит мастера, специалиста или компанию;
— Позволит гибко управлять расписанием и загрузкой;
— Разошлет оповещения о новых услугах или акциях;
— Позволит принять оплату на карту/кошелек/счет;
— Позволит записываться на групповые и персональные посещения;
— Поможет получить от клиента отзывы о визите к вам;
— Включает в себя сервис чаевых.
Для новых пользователей первый месяц бесплатно.
Зарегистрироваться в сервисе
Марганец является постоянной составляющей стали; растворяясь в феррите, он повышает его прочность. Марганец поступает в металл шва из основного и дополнительного металлов, а также из материалов, входящих в состав покрытия или флюса.
Хром, подобно марганцу, уменьшает вредное влияние серы, повышая стойкость швов против образования кристаллизационных трещин. Обладая более высоким, чем железо, химическим сродством к сере, хром связывает ее в тугоплавкий сульфид хрома. Растворяясь в феррите, хром повышает прочность металла. При высоком содержании хрома и повышенном содержании углерода возможно образование кристаллизационных трещин по легкоплавким карбидным прослойкам. Хром поступает в металл шва из основного и дополнительного металлов.
Кислород повышает стойкость швов против образования кристаллизационных трещин, вызываемых серой. Вместе с тем повышение содержания кислорода снижает ударную вязкость металла шва на углеродистых и низколегированных конструкционных сталях и уменьшает пластичность аустенитных швов. Кислород может попадать в металл шва из основного и дополнительного металлов, электродного покрытия, флюса, защитного газа или воздуха.
Одним из наиболее широко применяемых технологических методов повышения стойкости шва против образования кристаллизационных трещин является уменьшение в нем содержания вредных и увеличение полезных элементов. Изменения химического состава металла шва в желаемом направлении обычно достигают применением дополнительного металла с низкой концентрацией вредных примесей и содержащего полезные легирующие элементы, уменьшением доли участия основного металла в металле шва, а также выбором типа покрытия или флюса, при металлургическом взаимодействии которых с металлом сварочной ванны происходит очищение его от вредных и легирование полезными элементами.
Долю основного металла в шве уменьшают за счет применения соответствующих методов и режимов сварки (сварки на малых токах, двумя дугами, по присадочной проволоке и т. п.). Наиболее действенный метод предотвращения возникновения трещин в металле шва за счет применения основного металла с низким содержанием вредных элементов не всегда оправдан, так как ведет к повышению стоимости основного металла.
Для конструкций, работающих при повышенных температурах, необходимо стремиться к тому, чтобы металл шва по химическому составу был близок к основному металлу. Следует избегать различного легирования шва и основного металла, могущего привести в результате протекающих при этих температурах процессов диффузии к образованию в сварном соединения зоны с измененными свойствами (например, обезуглероженной зоны). Наличие структурной неоднородности может вызвать резкую концентрацию напряжений и преждевременный выход конструкции из строя.
Влияние формы сварочной ванны. Изменение способа и режима сварки приводит к изменению формы сварочной ванны (формы шва) и, как следствие, к изменению направления роста столбчатых кристаллитов и характера их взаимного срастания. Конфигурация шва характеризуется коэффициентом формы —

отношением ширины шва к глубине проплавления. При узком и глубоком проваре (коэффициент формы шва 0,8—1,2) кристаллиты растут навстречу друг другу и встречаются между собой торцами под углом 180° или близким к нему (рис. 6-8, а). При чашеобразной форме провара (коэффициент формы шва 1,3—5) кристаллиты растут под острым углом друг к другу и встречаются торцами или боковыми гранями (рис. 6-8, б). При широком и неглубоком проваре (коэффициент формы шва более 5) кристаллиты растут параллельно друг другу и, не встречаясь, выходят на поверхность шва (рис. 6-8, в).
Влияние формы шва на стойкость его против образования кристаллизационных трещин наблюдается при дуговой, электрошлаковой и электроннолучевой сварке. Увеличение коэффициента формы шва до определенного предела (примерно 6) приводит к повышению стойкости металла шва против образования кристаллизационных трещин. Дальнейшее увеличение коэффициента формы шва снова приводит к снижению стойкости металла шва против образования кристаллизационных трещин. Швы с таким большим значением коэффициента формы встречаются главным образом при наплавке, выполняемой электродной лентой, и при сварке последнего прохода многослойного шва.
На рис. 6-9 приведена зависимость между критическим содержанием углерода в металле шва и коэффициентом формы шва для дуговой сварки под флюсом углеродистых конструкционных сталей. Все остальные факторы, оказывающие влияние на стойкость шва против образования трещин, практически постоянны. Содержание кремния в металле шва до 0,4%, содержание серы — до 0,04%. С увеличением коэффициента формы шва до определенного предела критическое содержание углерода возрастает. В зависимости от значения коэффициента формы шва данное содержание углерода может быть выше или ниже критического.
Такая же взаимосвязь существует между коэффициентом формы шва и критическим содержанием других элементов и распространяется на другие виды сварки плавлением. Неблагоприятные условия в отношении формы сварочной ванны создаются при

сварке первого слоя многослойного шва и углового шва с разделкой кромок, где требование обеспечения провара вершины угла предопределяет необходимость применения швов с малым коэффициентом формы (рис. 6-10, а, б). Из практики известно, что подобные швы обладают пониженной стойкостью против образования кристаллизационных трещин. Для улучшения условий формирования первого слоя многослойных швов увеличивают угол разделки и уменьшают величину притупления.
Неблагоприятные условия для кристаллизации металла шва создаются при сварке стыковых односторонних швов с полным проваром на флюсовой подушке. При этом в результате ограниченного теплоотвода от основания сварочной ванны столбчатые кристаллиты растут навстречу друг другу, что определяет большую вероятность появления трещин (рис. 6-11).
Изменение формы провара — одян яз широко применяемых технологических методов повышения стойкости металла шва против образования кристаллизационных трещин. Более высокое значение коэффициента формы шва, наряду с другими факторами, определяет большую стойкость против образования
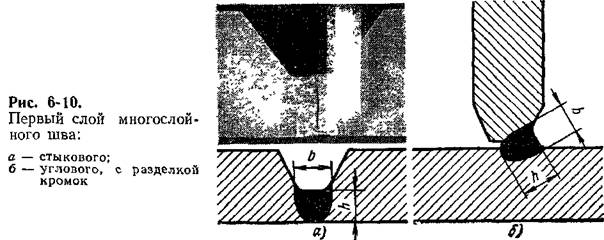

кристаллизадионных трещин швов, выполненных дуговой сваркой покрытыми электродами и электрошлаковой сваркой, по сравнению со айвами, сваренными под флюсом. При типичных для первых двух способов режимах сварки коэффициент формы шва изменяется в пределах 2,5—5,0 против 1,0—2,5 при сварке под флюсом. Повышению стойкости швов против образования кристаллизационных трещин при ручной дуговой сварке способствует снижение доли основного металла в металле шва, а при электрошлаковой сварке — и наличие сопутствующего подогрева.
В сварочной практике существует мнение, что швы с выпуклой формой поверхности обладают более высокой стойкостью против образования кристаллизационных трещин, чем швы с вогнутой формой поверхности. Это мнение не соответствует действительности. При прочих равных условиях стойкость металла того и другого шва против образования кристаллизационных трещин одинакова. Только, как это видно на рис. 6-2, в выпуклых швах трещины не выходят, а в вогнутых швах выходят на их поверхность.
|