Технология электрической сваркиХолодные трещины
В отличие от кристаллизационных трещин холодные трещины образуются в сварных соединениях при остывании их до относительно невысоких температур, как правило, ниже 200° С К этому времени металл шва и околошовной зоны приобретает высокие упругие свойства, присущие ему при нормальных температурах. Холодные трещины являются типичным дефектом сварных соединений из среднелегированных и высоколегированных сталей перлитного и мартенситного классов. Значительно реже они возникают в соединениях из низколегированных ферритно-перлитных сталей и высоколегированных сталей аустенитного класса. Ввиду преимущественного возникновения холодных трещин в соединениях из восприимчивых к закалке мартенситных и перлитных сталей трещины этого типа иногда называют закалочными. Холодные трещины наиболее часто поражают околошовную зону и реже металл шва.
Выявляют трещины внешним осмотром, с помощью ультразвука, по макро- и микрошлифам, а также по излому образцов.
По внешнему виду Холодные трещины отличаются от кристаллизационных и горячих трещин меньшей шириной, что четко проявляется на слабо протравленных макро- и микрошлифах.
В зависимости от расположения в сварном соединении различают продольные и поперечные трещины, залегающие в металле шва и околошовной зоне (рис. 6-13). Особо выделяют продольные трещины, залегающие в зоне сплавления шва с основным металлом (рис. 6-13, б), которые называют отрывами. Продольные трещины, расположенные в околошовной зоне, называют отколами (рис. 6-13, а). Часто встречаются также поперечные и продольные трещины, переходящие из околошовной зоны в шов. Переход трещин из шва в околошовную зону встречается значительно реже. Поперечные трещины, зародившиеся в околошовной зоне и перешедшие в шов, показаны на рис. 6-14. Трещины отмеченных видов могут выходить и не выходить на поверхность свариваемого металла. В зависимости от этого их называют наружными или внутренними трещинами.
Отколы являются наиболее общим и частым дефектом сварных соединений. Отрывы встречаются, как правило, в сварных соединениях из закаливающихся сталей, в которых металл шва имеет аустенитную структуру. Такую структуру получают путем соответствующего легирования швов с целью придания им высоких
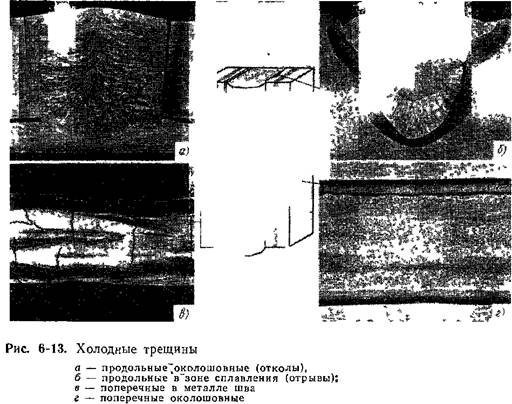
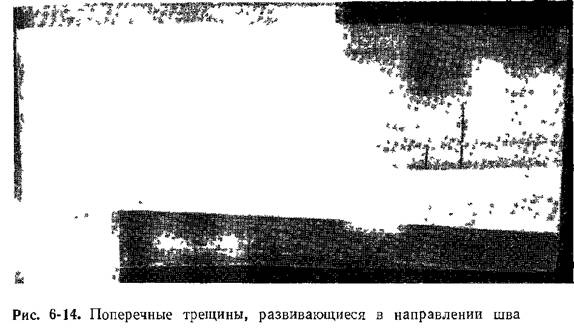
пластических свойств и обеспечения высокой сопротивляемости околошовной зоны образованию отколов.
Поперечные трещины в околошовной зоне встречаются редко и, как правило, только при сварке многослойных швов.
Холодные трещины в шве образуются, главным образом, при повышенном содержании в металле шва углерода и легирующих элементов, близком к содержанию их в основном металле. Это бывает редко, так как с целью повышения стойкости металла шва против образования кристаллизационных трещин содержание углерода в шве обычно устанавливают более низким, чем в основном металле.
Основным видом холодных трещин в сварных соединениях являются околошовные трещины, в связи с чем условия и причины их образования изучены достаточно подробно.
Кроме температуры возникновения, внешнего вида и расположения в соединении важнейшей отличительной чертой холодных трещин является их задержанное зарождение и замедленное развитие. Они возникают по истечении некоторого времени после окончания сварки и затем медленно, на протяжении нескольких часов и даже суток, распространяются в металле.
Типичный пример зарождения и развития продольной трещины в околошовной зоне однослойного стыкового соединения стали 35ХЗНЗМ толщиной 14 мм схематически показан на рис. 6-15. Первая зародышевая микротрещина появилась через 25 мин после сварки (под флюсом в один проход) при температуре около 130° С. На протяжении первого часа после сварки появилось еще несколько микротрещин (рис. 6-15, а) на границах зерен, выходящих на поверхность свариваемых листов. Они отчетливо обнаруживались с помощью ультразвука и под микроскопом, но были невидимы невооруженным глазом. В дальнейшем появились новые

и развивались ранее возникшие микротрещины (рис. 6-15, б, в). Этот процесс происходил медленно— макроскопическая трещина образовалась лишь на третьи сутки (рис. 6-15, г). Если начальное развитие холодных трещин идет по границам зерен, то в дальнейшем оно может проходить как по границам, так и по телу зерна (рис. 6-15, 5).
Описанная выше картина зарождения и развития холодных трещин может существенно изменяться в зависимости от химического состава основного металла, размеров и толщины соединяемых деталей, условий их закрепления перед сваркой, способов и режимов сварки и других факторов. Факторы, понижающие сопротивляемость сварных соединений образованию холодных трещин, ускоряют их зарождение и развитие, а факторы, повышающие эту сопротивляемость, замедляют.
Большое разнообразие условий для возникновения холодных трещин в реальных сварных конструкциях приводит к тому, что в одних случаях макроскопические холодные трещины появляются через несколько минут после сварки, а в других—после нескольких часов и суток. Известны примеры, когда трещины возникали даже по истечении нескольких десятков суток. Они могли образоваться только вследствие развития начальных микротрещин, возникших в соединении в первые часы после сварки и затем прекративших свой рост ввиду недостаточной величины сварочных напряжений или других причин. Впоследствии при хранении конструкций могли произойти неблагоприятные изменения внешних условий, способствующие развитию микротрещин в макротрещины. В условиях монтажа и эксплуатации сварной конструкции дополнительным фактором, который мог вызвать не только возобновление роста микротрещин, но и их образование, является суммирование сварочных напряжений с напряжениями от внешних нагрузок.
Холодные трещины чаще всего развиваются прерывисто (скачкообразно), причем одновременно может развиваться несколько микротрещин. Если же в соединении при сварке накопилась большая энергия упругой деформации, то после начального периода замедленного развития холодная трещина растет мгновенно (взрывообразно) и со значительным звуковым и механическим эффектом распространяется на все сечение соединения. Отдельные детали при этом расходятся в стороны.
Объяснить причины образования холодных трещин весьма трудно. При испытании на растяжение поперечных образцов сварного соединения, склонного к образованию отколов, разрушение происходит вне околошовной зоны по основному металлу или шву при весьма высоких напряжениях (более 50 кгс/мм2). Вместе с тем замер поперечных сварочных напряжений в этих соединениях показал, что они низки (порядка 10—20 кгс/мм2). Было непонятно, почему такие низкие напряжения вызывают разрушение наиболее прочного участка сварного соединения — металла околошовной зоны.
Забиваем Сайты В ТОП КУВАЛДОЙ - Уникальные возможности от SeoHammer
Каждая ссылка анализируется по трем пакетам оценки: SEO, Трафик и SMM.
SeoHammer делает продвижение сайта прозрачным и простым занятием.
Ссылки, вечные ссылки, статьи, упоминания, пресс-релизы - используйте по максимуму потенциал SeoHammer для продвижения вашего сайта.
Что умеет делать SeoHammer
— Продвижение в один клик, интеллектуальный подбор запросов, покупка самых лучших ссылок с высокой степенью качества у лучших бирж ссылок.
— Регулярная проверка качества ссылок по более чем 100 показателям и ежедневный пересчет показателей качества проекта.
— Все известные форматы ссылок: арендные ссылки, вечные ссылки, публикации (упоминания, мнения, отзывы, статьи, пресс-релизы).
— SeoHammer покажет, где рост или падение, а также запросы, на которые нужно обратить внимание.
SeoHammer еще предоставляет технологию Буст, она ускоряет продвижение в десятки раз,
а первые результаты появляются уже в течение первых 7 дней.
Зарегистрироваться и Начать продвижение
Понадобились многолетние исследования, прежде чем были выяснены основные закономерности образования холодных трещин при сварке и было установлено, что основными факторами, определяющими их возникновение и развитие в сварных соединениях, являются закалочные явления, суммарные напряжения (сварочные и от внешних нагрузок) и водород. Для изложения основных результатов этих исследований рассмотрим водородную и закалочную гипотезы образования холодных трещин, предложенные еще в 1944 г. и непрерывно развивающиеся до настоящего времени.
В соответствии с водородной гипотезой основным фактором, определяющим стойкость околошовной зоны против образования трещин, является водород, поступающий в околошовную зону из металла шва. Гипотеза основывалась на экспериментальных фактах, свидетельствующих о том, что применение низководородных и аустенитных электродов приводит к заметному повышению сопротивляемости соединений образованию отколов.
Согласно гипотезе, попадающий при сварке в металл шва водород диффундирует в околошовную зону. Здесь, скапливаясь в микропустотах и несовершенствах атомной решетки и превращаясь из атомарного в молекулярный, он создает громадное давление, под действием которого и происходит разрушение металла, т. е. образование трещин. Высокую сопротивляемость образованию околошовных трещин соединений с аустенитным швом объясняли тем, что швы с аустенитной структурой в условиях сварочного термического цикла удерживают практически весь водород и перемещения водорода в околошовную зону не происходит.
Водородная гипотеза долгое время была общепринятой, хотя и не основывалась на прямых данных о связи отколов с содержанием водорода в околошовной зоне. Однако экспериментальные данные, полученные методом вакуум-нагрева отдельных участков сварного соединения (рис. 6-16, б, г), а также путем наблюдения за выделением из сварного соединения диффузионного водорода (рис. 6-16, а, б), показали, что при одинаковых условиях сварки содержание водорода в околошовной зоне при аустенитной структуре металла шва значительно выше, чем при ферритной структуре. На рис. 6-16, а, б видно, что диффузионный водород из
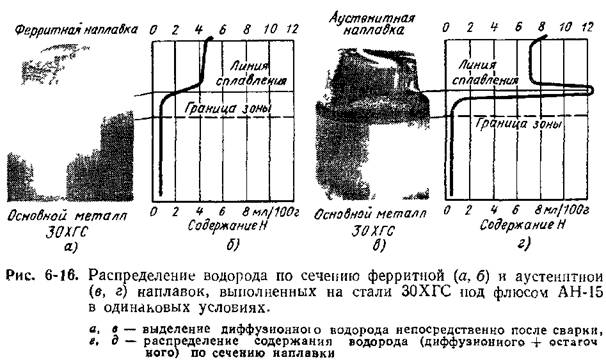
околошовной зоны выделяется только при аустенитном наплавленном металле. В этих опытах производилась однослойная наплавка валиков под флюсом на сталь ЗОХГС толщиной 30 мм. Данные о высоком содержании водорода в околошовной зоне соединений с аустенитным швом также получены и с помощью локального спектрального анализа.
Наряду с этим имеются многочисленные сведения о значительном повышении стойкости околошовной зоны против образования трещин при снижении содержания водорода в металле шва. Так, например, при снижении содержания водорода в металле шва в 1,5—2 раза, достигаемом при использовании постоянного тока взамен переменного, заметно повышается стойкость околошовной зоны против образования холодных трещин при сварке низколегированной ферритной проволокой сталей типа 25ХГС.
Таким образом, водород в одних случаях существенно влияет на стойкость околошовной зоны против образования трещин, в других же, например при сварке среднелегированных сталей аустенитной проволокой, его роль второстепенна. Это позволяет заключить, что водород не является главным и тем более единственным фактором, определяющим образование холодных трещин в сварных соединениях. Его влияние на их образование необходимо рассматривать совместно с действием других факторов, обусловленных преимущественно закалочными явлениями в околошовной зоне и сварочными напряжениями. В соединениях с аустенитным швом положительное действие других факторов значительно преобладает над отрицательным действием водорода.
Закалочная гипотеза холодных трещин основана на большом экспериментальном материале исследований закалочных явлений в металле вообще и в сварных соединениях в частности. При этом особое значение имеют исследования, установившие наличие и сущность замедленного разрушения закаленных сталей и металлов.
Согласно этой гипотезе, механизм образования холодных трещин можно описать следующим образом. В процессе охлаждения в околошовной зоне сварного соединения закаливающихся сталей образуется характерная мартенситная структура металла и сложное напряженное состояние, обусловленное суммированием сварочных и структурных напряжений. Для большинства конструкционных сталей, при сварке которых наблюдается образование холодных трещин, структурные превращения в околошовной зоне заканчиваются в основном при охлаждении до температур порядка 150° С. К этому моменту завершается и формирование напряженного состояния в сварных соединениях из этих сталей.
Характерной и отличительной особенностью напряженного состояния сварных соединений, закаливающихся сталей с феррит-ным или аустенитным швом является возникновение сложного распределения продольных сварочных напряжений (рис. 6*17); это распределение характеризуется наличием сравнительно высоких напряжений сжатия в участке зоны на границе со швом и

высоких напряжений растяжения в соседнем участке этой зоны, а также в сварном шве. Такое распределение продольных напряжений обусловлено значительным увеличением объема металла околошовной зоны, непосредственно граничащего со швом, вследствие мартенситного превращения. В поперечном направлении возникают небольшие растягивающие напряжения в средней части соединения (по длине) и напряжения сжатия по краям (см. рис. 6-17). В результате на границе раздела шов—основной металл появляются большие скалывающие напряжения, способствующие замедленному разрушению закаленной стали и образованию холодных трещин типа отколов.
Замедленное разрушение происходит вследствие снижения прочности некоторых металлов под влиянием длительного статического нагружения при близких к комнатным температурах. В отдельных случаях это снижение прочности очень значительное. Так, например, для стали с повышенным содержанием углерода и легирующих элементов (типа 35ХГС) непосредственно после закалки с высоких температур (1200° С) длительная прочность может составить всего 10% кратковременной прочности. Причины замедленного разрушения перегретой закаленной стали заключаются в особой ее структуре.
Сервис онлайн-записи на собственном Telegram-боте
Попробуйте сервис онлайн-записи VisitTime на основе вашего собственного Telegram-бота:
— Разгрузит мастера, специалиста или компанию;
— Позволит гибко управлять расписанием и загрузкой;
— Разошлет оповещения о новых услугах или акциях;
— Позволит принять оплату на карту/кошелек/счет;
— Позволит записываться на групповые и персональные посещения;
— Поможет получить от клиента отзывы о визите к вам;
— Включает в себя сервис чаевых.
Для новых пользователей первый месяц бесплатно.
Зарегистрироваться в сервисе
Типичная структура закаленной стали, склонной к замедленному разрушению, наблюдается в участке перегрева околошовной зоны (рис. 6-18). Она характеризуется крупным зерном и соответственно крупными мартенситными иглами, выходящими своими торцами на границы зерен. В результате изменений в пограничных объемах зерен искажается атомное кристаллическое строение металла. Можно предполагать, что по строению и свойствам эти пограничные участки зерен приближаются к аморфным телам.
Как известно, аморфные тела могут претерпевать значительную деформацию во времени под действием постоянной нагрузки, недостаточной для сколько-нибудь заметного деформирования тел при кратковременном ее действии. В свете современных представлений
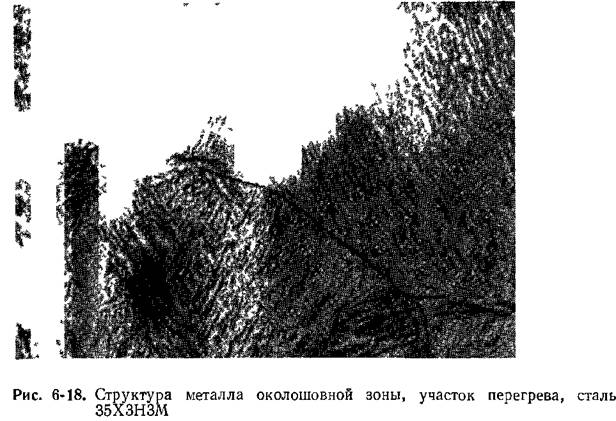
о строении мартенсита отмеченное искажение кристаллической решетки следует связывать также с тем, какой мартенсит образуется в околошовной зоне — дислокационный, относительно пластичный, или двойниковый, весьма хрупкий. Последнее определяется содержанием углерода в стали и температурой мартен-ситного превращения (см. гл 6).
Исходя из замедленного характера разрушения сварных соединений и учитывая приведенные выше сведения о напряженном состоянии и структуре околошовной зоны, способствующих такому разрушению, зарождение и развитие холодных трещин можно описать следующей схемой (рис 6-19). Еще в процессе завершения структурных превращений крупнозернистый металл околошовной зоны с грубыми мартенситными иглами, как бы подготовленный к замедленному разрушению по границам зерен, подвергается воздействию сложнонапряженного состояния. Этот металл подвергается естественному испытанию на стойкость против замедленного разрушения непосредственно в процессе сварки.
Рассмотренное выше сложнонапряженное состояние на предлагаемой схеме отражено следующим образом: в околошовной зоне у границы со швом действуют продольные напряжения сжатия ог и поперечные напряжения растяжения о2 В примыкающем участке шва у этой границы действуют продольные напряжения растяжения аг и те же поперечные напряжения растяжения а2. При этих условиях на границе раздела возникают значительный перепад продольных напряжений (—ах)—(+сух) и значительные напряжения сдвига. По границам зерен околошовной зоны, направленным

под углом 45° к оси шва, возникают значительные касательные напряжения т. Такое напряженное состояние способствует зарождению трещины замедленного разрушения на стыке трех зерен (см. рис. 6-19), которая в дальнейшем постепенно развивается в полном соответствии с изложенными выше представлениями.
Так зарождаются околошовные трещины всех видов — продольные (отрывы и отколы) и поперечные (собственно околошовные и переходящие в шов). Направление дальнейшего развития зародившейся трещины зависит от способности металла того или иного участка сварного соединения противостоять ее развитию, а также от конкретного сочетания продольных и поперечных напряжений и, в частности, от величины перепада напряжений на границе шов— околошовная зона. При этом, как правило, начальная стадия развития холодных трещин связана с границами крупных зерен.
Образованию отрывов в соединениях легированных сталей с аустенитным швом помимо перепада напряжений и наличия крупных зерен в околошовной зоне способствуют низкая пластичность и прочность зоны сплавления. Следует также учитывать, что такие причины замедленного разрушения (развития холодных трещин), как перегрев металла и большой перепад продольных напряжений, действуют одновременно и совместно только на границе шов— околошовная зона. Поэтому отмеченная граница в наибольшей степени подвержена образованию продольных трещин. Кроме того, металл околошовной зоны вблизи шва часто ослабляется развитием высокотемпературной химической неоднородности и неблагоприятным видоизменением неметаллических включений, обусловленным нагревом до высоких температур, близких к точке плавления.
Образование поперечных трещин также начинается в околошовной зоне на участке перегрева и обычно свидетельствует о высоком уровне продольных напряжений в соединении. В сравнительно редких случаях, преимущественно в соединениях с многослойными швами, поперечные холодные трещины могут зарождаться в околошовной зоне на некотором расстоянии от участка перегрева, в местах, где развиваются весьма высокие напряжения растяжения (см. рис. 6-17). Возможно также зарождение поперечных трещин в самом металле шва. Обычно это имеет место в многослойных малопластичных швах.
Выше было рассмотрено возникновение зародышей холодных трещин по границам зерен вследствие нарушения по этим границам атомного строения металла. В реальных металлах возможен и другой механизм образования зародышей таких трещин, связанный с наличием неметаллических включений. Последние могут располагаться в металле по границам и телу зерен. Зародышами холодных трещин могут стать неметаллические включения при их неблагоприятных форме, химическом составе и расположении, а также горячие трещины — надрывы, возникающие в участке крупного зерна околошовной зоны. В результате неизбежного нагрева этого участка до температур, близких к солидусу, в нем происходят значительные изменения исходных неметаллических включений основного металла. Это имеет существенное значение при электрошлаковой и дуговой однослойной сварке толстого металла.
Отмеченные изменения происходят в наибольшей степени в тех участках соединения, где максимальный перегрев околошовной зоны сочетается с высокими временными напряжениями растяжения при температурах, близких к солидусу. Такое неблагоприятное сочетание условий имеет место при сварке кольцевых швов толстостенных сосудов.
На рис. 6-20 показаны примеры зарождения холодных трещин от пленообразного неметаллического включения и от горячих трещин-надрывов.
При помощи электрошлакового и электроннолучевого переплавов можно существенно уменьшить общее количество неметаллических включений в основном металле, предельно ограничить содержание легкоплавких включений сульфидного происхождения и перевести их в более тугоплавкие соединения, а также достичь равномерного и мелкодисперсного распределения неметаллических включений в металле. При этом значительно повышается стойкость сварных соединений против образования холодных трещин. Аналогичные результаты можно получить, применив предварительную наплавку подлежащих сварке кромок.
Если наплавку выполнить металлом такого же химического состава, что и металл кромок, то стойкость соединения против образования холодных трещин обычно на 20—30% превысит стойкость соединения без наплавки. В этом случае эффект достигается вследствие благоприятных изменений состава и распределения неметаллических включений в наплавленном металле. Если же применить наплавку незакаливающимся металлом, например аустенитным, то можно почти полностью устранить опасность возникновения в соединениях холодных трещин.
Изложенное позволяет, с точки зрения закалочной гипотезы, объяснить влияние многочисленных и разнообразных факторов на стойкость соединений против образования холодных трещин. Рассмотрим этот вопрос на примере сварных соединений средне-легированных сталей. Исходным в этом объяснении является положение о том, что стойкость соединений против образования
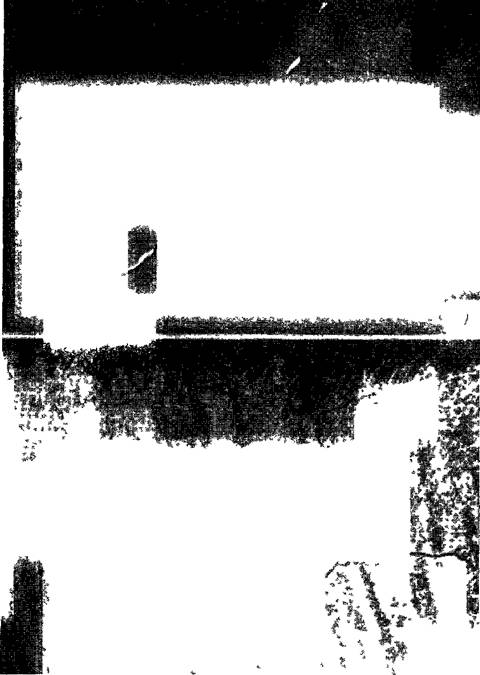
Рис. 6-20. Зарождение холодной трещины в участке перегрева с развитой высокотемпературной неоднородностью от пленообразного неметаллического включения (а) и надрыва (б): X 1000
холодных трещин определяется, с одной стороны, сопротивляемостью металла замедленному разрушению, и, с другой —напряженным состоянием в сварном соединении. При этом принципиально важно учитывать, во-первых, влияние различных факторов на изменение условий локальной пластической деформации по границам зерен и, во-вторых, их влияние на стойкость участков сварного соединения развитию холодных трещин.
Все факторы, вызывающие упорядочение атомного строения по границам зерен, затрудняющие образование сдвигов по этим границам и способствующие вовлечению в пластическую деформацию тела зерна, повышают стойкость металла против образования холодных трещин, затрудняя их зарождение. Такое же влияние оказывают факторы, исключающие или ослабляющие возможность образования зародышей холодных трещин от неметаллических включений, микроскопических горячих трещин-надрывов и т. п.
В связи с изложенным решающее влияние на стойкость сварных соединений среднелегированных сталей против образования холодных трещин оказывают перегрев в околошовной зоне, температурный интервал мартенситного превращения в этой зоне, а также в металле шва и скорость охлаждения околошовной зоны и металла шва в этом интервале. Чем меньше перегрев, выше температура мартенситного превращения и медленнее охлаждение, тем меньше нарушается атомное строение на границах зерен и соответственно затрудняется зарождение трещин. Кроме того, чем выше пластичность мартенсита, тем выше его сопротивляемость развитию трещин.
Образование трещины затрудняется еще и тем, что как повышение температуры мартенситного превращения, так и замедление охлаждения, уменьшая перепад продольных напряжений на границе околошовная зона—шов, смягчают напряженное состояние в участке, где их возникновение наиболее вероятно. Если ограничить перегрев и предупредить образование мартенсита или достаточно высоко сместить температурный интервал его образования, то возникновения холодных трещин можно не опасаться. Их не будет и в том случае, если достаточно сильно замедлить охлаждение в мартенситном интервале температур. Мартенсит при таком охлаждении в среднелегированных сталях отпускается (самоотпускается) и становится не склонным к замедленному разрушению.
Отсюда следует, что наиболее простой и эффективный способ борьбы с холодными трещинами заключается в регулировании термического цикла сварки путем выбора соответствующих методов и режимов сварки, а также использования в необходимых случаях предварительного подогрева.
Идеальный термический цикл, обеспечивающий наивысшую стойкость против образования холодных трещин, приведен на рис. 6-21. Для сравнения на этом же рисунке показаны обычные
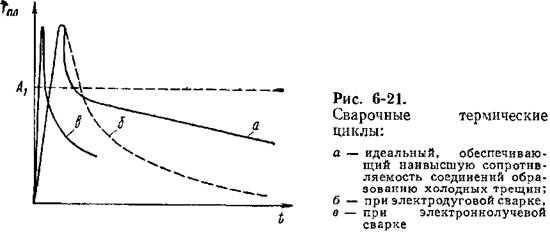
термические циклы для электроннолучевой и электродуговой сварки. При таком идеальном термическом цикле перегрев не развивается вследствие быстрого нагрева и охлаждения металла при температурах выше точки Av
Медленное охлаждение при температурах ниже точки Аг способствует развитию в соединениях из среднелегированных сталей перлитного и промежуточного превращений переохлажденного аустенита в околошовной зоне и металле шва и устранению или смещению мартенситного превращения в область высоких температур. Другими словами, уменьшается закалка металла сварного соединения, что повышает сопротивляемость стали замедленному разрушению и стойкость против образования холодных трещин.
Этому также способствует, причем весьма активно, замедленное охлаждение сварного соединения в область температур мартенситного превращения (ниже 350° С). В результате самоотпуска мартенсита при этих температурах упорядочивается кристаллическое строение металла в объемах, примыкающих к границам зерен, повышается пластичность металла в целом и затрудняется возникновение и развитие холодных трещин. Реальные термические циклы, близкие к идеальным, можно получить при электроннолучевой сварке с предварительным подогревом или при многослойной дуговой сварке толстого металла с предварительным подогревом.
Кроме отмеченных выше основных факторов, оказывающих решающее влияние на стойкость сварных соединений против образования холодных трещин, имеются дополнительные и производные факторы, которые также могут оказывать влияние на эту стойкость. К ним относятся содержание углерода и легирующих элементов в основном металле и шве, качество основного металла, деформационный цикл сварки, термообработка после сварки и др. (см. гл. 10).
Остановимся кратко на методах оценки стойкости сварных соединений против образования холодных трещин. Различают методы качественной и Количественной оценки стойкости сварных соединений против образования холодных трещин.
Качественную оценку проводят при помощи технологических проб на сварных образцах, в которых создают условия, способствующие образованию холодных трещин. Обычно прибегают к закреплению соединяемых элементов на жестком основании —• плите большой толщины и т. п.
Внешним осмотром и по макрошлифам устанавливают наличие или отсутствие в контрольном шве технологической пробы холодных трещин, определяют их вид и протяженность. По этим показателям приблизительно предполагают, будут ли в реальных сварных соединениях возникать трещины и какие, т. е. определяют пригодность тех или иных марок стали, сварочных материалов, методов, режимов и других условий сварки для изготовления конкретной сварной конструкции.
Оценка стойкости с помощью технологических проб весьма приближенная. В одних случаях она приводит к излишнему запасу этой стойкости и обусловливает неоправданное снижение прочности основного металла вследствие чрезмерного ограничения содержания углерода и легирующих элементов, неоправданному применению таких дорогих и трудноосуществимых технологических методов повышения стойкости, как предварительный подогрев и последующая термообработка соединений и т. п.
В других случаях оценка с помощью технологических проб может быть причиной недостаточной стойкости против образования холодных трещин. Последнее обычно обусловлено тем, что в ряде случаев напряженное состояние и деформации реальной конструкции оказываются намного большими, чем в технологической пробе.
В последние годы разрабатываются и находят практическое применение методы количественной оценки стойкости металла против образования холодных трещин, основанные на испытаниях сварных соединений путем замедленного разрушения. Сущность метода, предложенного Н. Н, Прохоровым, состоит в том, что с помощью специальных машин или устройств серия сварных образцов сравнительно небольших размеров подвергается испытанию на длительное растяжение или изгиб сразу же по окончании сварки. Сварка образцов обычно осуществляется в этих же устройствах. Испытания на растяжение, как и другие виды мягких нагружений, например кручение, заслуживают предпочтения, как более полно и точно выявляющие склонность металлов к замедленному разрушению.
Преимущества испытаний на изгиб заключаются в большей простоте испытательных устройств, так как на них необходимо создавать значительно меньшие усилия, чем на устройствах для растяжения (рис. 6-22). При выборе способа нагружения следует учитывать реальные условия работы испытываемого соединения.
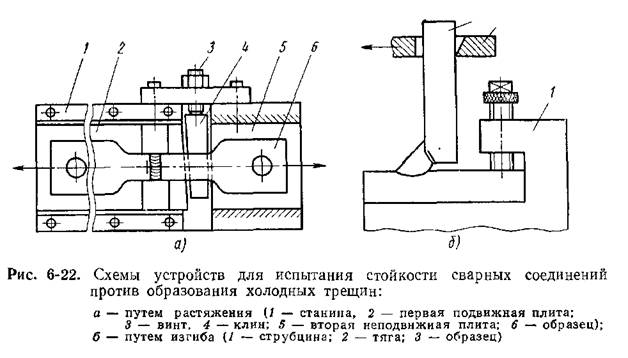
Испытания на замедленное разрушение проводятся в следующем порядке. Подлежащие испытанию образцы делят на три-четыре партии по два-три образца в каждой. Первоначально определяют кратковременную прочность, затем следующие партии испытывают при напряжениях, составляющих 50; 25; 10% кратковременной прочности, и для каждого напряжения определяют время разрушения. Максимальную продолжительность нагружения, как правило, устанавливают равной 24 ч, а в отдельных случаях 72 ч. По результатам испытания строят кривые замедленного разрушения.
Из приведенных на рис. 6-23 кривых, относящихся к случаю испытания на растяжение однослойных стыковых соединений, видно, что указанным методом можно количественно оценить влияние весьма незначительных и малозаметных изменений структуры и напряженного состояния сварных соединений на их стойкость против образования холодных трещин. Этот метод можно рекомендовать для широкого практического применения (подробнее см. в гл. 10). Изложенные выше закономерности и положения, относящиеся к образованию холодных трещин (причины их возникновения,
способы предупреждения, методы оценки стойкости металла), хотя и составлены на опытном материале, накопленном при
сварке легированных закаливающихся сталей, имеют общий характер и могут быть распространены также на стали и сплавы других классов с определенными уточнениями.
В частности, эти положения полностью пригодны для анализа процессов образования холодных трещин в сварных соединениях высоколегированных сталей, в околошовной зоне которых образуется мартенсит. Они также могут быть распространены и на случай образования холодных трещин в соединениях сплавов титана с высоким пределом текучести. При сварке таких сплавов в околошовной зоне и швах имеет место низкотемпературное превращение высокотемпературной фазы Р в фазу а.
Повышение содержания в фазе р алюминия Р-стабилизирую-щих примесей (О, N) свыше определенных пределов может привести к значительной локализации пластической деформации по границам зерен околошовной зоны (см. рис. 6-19).
В сварных соединениях титана вследствие более высокой температуры и меньшего объемного эффекта р~->а-превращения (по сравнению с мартенситным у — а-превращением в стали) замедленное разрушение развивается значительно менее интенсивно и требует более высокого уровня напряжений. Так, например, если в сварных соединениях крестовой пробы из закаливающихся сталей процесс развития трещины завершается на протяжении суток, то в случае сплавов титана с высоким пределом текучести он длится неделями и даже месяцами. Минимальные напряжения, вызывающие замедленное разрушение сварных соединений титана, особенно при низком содержании газов, по своей величине значительно ближе к пределу текучести, чем у закаливающихся сталей.
|