Технология электрической сваркиИспользование шлаковых корок
При механизированных сварке и наплавке под флюсом в результате расплавления флюса образуется значительное количество шлаковых корок, которые обычно не используют. Вместе с тем в сущности составы и свойства шлака и флюса отличаются мало. Разница состоит в небольшом изменении химического состава флюса в процессе сварки и наличии в шлаке металлических капель различного размера.
В шлаке по сравнению с исходным флюсом обычно содержится несколько больше окислов железа и окиси кальция и несколько меньше CaF2. Поэтому шлак по сравнению с флюсом имеет несколько пониженную стойкость против образования кристаллизационных трещин и пор в металле шва и не может служить полноценной заменой флюса при сварке. Однако во многих случаях можно механически примешивать к флюсу некоторое количество измельченной шлаковой корки,*не ухудшая этим заметно качество металла шва или наплавки.
При определении количества измельченной шлаковой корки, которое можно примешивать к флюсу, следует учитывать, насколько высока в данных конкретных производственных условиях стойкость сварных швов против образования пор и кристаллизационных трещин. Необходимо также принимать во внимание и другие возможные стороны влияния такого примешивания на качество сварных соединений. Чем выше стойкость швов против образования пор и кристаллизационных трещин, тем большей может быть примесь к флюсу измельченной шлаковой корки. Необходимым условием использования шлаковых корок в качестве примеси к флюсу является предупреждение загрязнения их землей, смазкой и т.д., так как эти вещества ухудшают качество швов. Размер частиц измельченной шлаковой корки должен быть таким же, как и зерен флюса. На предприятиях, имеющих собственные флюсовые мастерские, использовать шлаковые корки можно, добавляя их к шихте для выплавки флюса
Флюсы для сварки и наплавки легированных сталей. Большинство требований, предъявляемых к флюсам для сварки углеродистых сталей, действительны и для флюсов, предназначенных для сварки легированных сталей. Дополнительное требование — минимальное окисление легирующих элементов, вводимых в шов из основного металла и сварочной проволоки. Имеют место также трудности в обеспечении хорошей отделимости шлака с поверхности швов, содержащих ванадий или ниобий, а также хром.
Отделимость шлаковой корки зависит от окисляющего действия жидкого флюса на поверхность затвердевшего шва. Длительность этого действия очень невелика и составляет для обычных режимов электродуговой сварки 20—30 с. Жидкий шлак, содержащий значительные количества FeO, MnO, Si02 и Ti02, окисляет поверхность затвердевшего металла шва. Образующаяся весьма тонкая окисная пленка прочно удерживается на его поверхности. Если поверхность металла окислена, а в составе шлака находятся соединения, прочно сцепляющиеся с окисной пленкой на шве (А1203, Сг203 и др.), следует ожидать прочного удерживания шлака на поверхности металла.
Введение в сварочную ванну небольших количеств сильных раскислителей значительно улучшает отделимость шлака. Прочность удерживания шлака возрастает при содержании в нем заметных количеств окислов ванадия, ниобия, хрома и алюминия, что приводит к образованию в ближайшем ко шву слое шлака соединений, имеющих такую кристаллическую решетку, которая достраивает решетку закиси железа. Для улучшения отделимости шлаковой корки с поверхности шва следует принимать меры, затрудняющие образование и рост окисной пленки.
Выполнение требований, предъявляемых к флюсу как в отношении минимального окисления примесей, так и легкой отделимости шлака, обеспечивается применением флюсов с низким содержанием окислов железа, марганца, кремния и титана, т. е. с пониженными окислительными свойствами.
Снижение содержания Si02 во флюсе для автоматической и полуавтоматической дуговой сварки с целью уменьшения окисляющего действия ухудшает его формирующие свойства. При сварке под флюсом качество формирования швов остается удовлетворительным, если уменьшение содержания Si02 во флюсе компенсируется соответствующим повышением содержания А1203, способного подобно Si02 придавать флюсу вязкость, делать его длинным. Поэтому в составе флюсов для сварки легированных сталей обычно много окиси алюминия, причем ее концентрация тем выше, чем меньше содержание Si02.
Плавленые флюсы для сварки и наплавки легированных сталей (см. табл. 7-31). Сведения о строении, цвете и размере зерен, а также объемной массе приведены в табл. 7-32—7-34. Флюсы АН-20С, АН-20СМ и АН-20П имеют одинаковый химический состав и отличаются лишь по размеру и строению зерен. Эти флюсы предназначены для дуговой автоматической наплавки легированных сталей и сварки легированных сталей соответствующими сварочными проволоками.
Флюс АН-22 предназначен для электрошлаковой сварки и дуговой автоматической сварки и наплавки легированной сварочной проволокой; флюсы АН-26С, АН-26П и АН-26СП — для автоматической и полуавтоматической сварки нержавеющих, корро-зионностойких и жаропрочных сталей соответствующими сварочными проволоками. Индекс СП указывает, что флюс состоит из зерен стекловидного и пемзовидного строения. При надлежащем выборе технологии низкокремнистые флюсы перечисленных выше марок можно применять для сварки и наплавки иных типов стали в сочетании с соответствующими сварочными проволоками.
Из силикатов, алюминатов и алюмосиликатов магния состоит флюс 48-ОФ-10. В его составе много CaF2. Флюс предназначен для дуговой наплавки лентой и сварки легированных и низколегированных сталей. Для наплавки легированных сталей и чугуна предназначен флюс АН-28. Суммарное содержание Si02 и А1203 в нем составляет 43—53%, СаО и CaF2 47—53%. Флюс имеет пемзовидное строение и цвет от белого до темно-серого. Высокие стабилизирующие свойства флюса АН-28 позволяют надежно вести наплавку не только проволокой, но и широкой лентой. Для сварки легированных сталей предназначен и флюс АВ-5 (табл. 7-37).
Забиваем Сайты В ТОП КУВАЛДОЙ - Уникальные возможности от SeoHammer
Каждая ссылка анализируется по трем пакетам оценки: SEO, Трафик и SMM.
SeoHammer делает продвижение сайта прозрачным и простым занятием.
Ссылки, вечные ссылки, статьи, упоминания, пресс-релизы - используйте по максимуму потенциал SeoHammer для продвижения вашего сайта.
Что умеет делать SeoHammer
— Продвижение в один клик, интеллектуальный подбор запросов, покупка самых лучших ссылок с высокой степенью качества у лучших бирж ссылок.
— Регулярная проверка качества ссылок по более чем 100 показателям и ежедневный пересчет показателей качества проекта.
— Все известные форматы ссылок: арендные ссылки, вечные ссылки, публикации (упоминания, мнения, отзывы, статьи, пресс-релизы).
— SeoHammer покажет, где рост или падение, а также запросы, на которые нужно обратить внимание.
SeoHammer еще предоставляет технологию Буст, она ускоряет продвижение в десятки раз,
а первые результаты появляются уже в течение первых 7 дней.
Зарегистрироваться и Начать продвижение
Проведенные в ИЭС им. Е. О. Патона исследования показали, что введение в состав низкокремнистых флюсов окислов железа способствует значительному улучшению механических свойств металла шва. С этой целью разработаны флюсы АН-17, АН-17М и другие, имеющие стекловидное строение и черный цвет.
Разработка составов низкокремнистых флюсов за рубежом вызвана необходимостью при сварке углеродистых сталей уменьшить окисление вводимого с проволокой марганца. Высококремнистые безмарганцевые флюсы типа UM20 или UM30, содержащие около 50% Si02, вследствие развития кремневосстановитель-ного процесса значительно уменьшают содержание марганца в металле сварочной ванны.
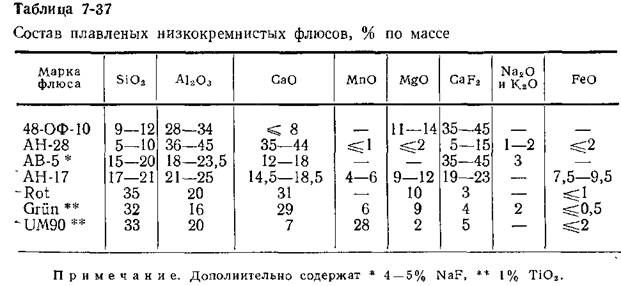
Меньшего окисления марганца достигли заменой части Si02 окисью алюминия — флюс Rot, а также введением в состав флюса окислов марганца — флюсы UM90 и Grun (см. табл. 7-38).
Хотя окислительное действие низкокремнистых флюсов, особенно не содержащих окислов марганца, на металл сварочной ванны невелико, все же оно достаточно, чтобы полностью или в значительной степени окислить и перевести в шлак такие элементы, как титан, алюминий, цирконий и др. Недо татком этих флюсов является также плохая отделимость шлака от поверхности швов, содержащих ванадий и ниобий, вследствие окисления поверхности шва жидким шлаком. Низкокремнистые флюсы мало пригодны для получения стабильноаустенитных швов и сварки высоконикелевых жаропрочных сплавов ввиду недопустимо высокой окислительной способности, загрязнения металла шва неметаллическими силикатными включениями и значительного перехода кремния в шов.
Перечисленные недостатки низкокремнистых флюсов вызвали необходимость разработки и применения бескремнистых, безмарганцевых флюсов, не содержащих в своем составе Si02, MnO и других непрочных окислов или же содержащих их только в качестве загрязняющей примеси. Бескремнистые флюсы состоят из таких прочных окислов, как А1203, СаО и MgO, а также из фторидов щелочных и щелочноземельных металлов (табл. 7-38).
Флюс 48-ОФ-6 применяют при автоматической дуговой сварке и наплавке легированных сталей. Состоящий из фтористого кальция и прочных окислов (см. табл. 7-38), он мало влияет на химический состав металла шва. Гранулированный по мокрому способу флюс 48-ОФ-6 с целью возможно более полного удаления из него влаги обязательно прокаливают при высокой температуре.
Для автоматической дуговой наплавки легированных сталей предназначены флюсы АН-30 и АН-70 (см. табл. 7-38). Флюс АН-30 имеет стекловидное строение зерен, флюс АН-70 — пемзовидное. К бескремнистым относятся флюсы АНФ-6 и АНФ-7, нашедшие


преимущественное применение при электрошлаковом переплаве Зерна этих флюсов имеют камневидное строение.
|