Технология электрической сваркиСварка под флюсом
Сварка под флюсом в большинстве случаев используется как автоматический процесс. Полуавтоматическая сварка под флюсом применяется в значительно меньшем объеме, чем автоматическая. Процесс ведется преимущественно в нижнем положении. Объем работ, выполняемых при помощи сварки под флюсом, из года в год увеличивается. Интенсивное развитие автоматической сварки под флюсом обусловлено высокой производительностью этого способа, стабильным качеством сварки, малым расходом электродного металла и электроэнергии и хорошими условиями труда.
При сварке под флюсом производительность процесса по машинному времени повышается в 6—12 раз, что даже при коэффициенте использования сварочной установки 0,5 в 3—6 раз превосходит производительность ручной сварки покрытыми электродами. При сварке на специальных, так называемых форсированных режимах, применяемых при изготовлении труб большого диаметра и широкополых двутавровых балок, производительность повышается в 15—20 раз. За счет повышения коэффициента использования сварочной установки можно добиться значительного дальнейшего роста производительности сварки под флюсом. Повышение производительности при автоматической сварке под флюсом достигается за счет использования больших токов и повышения плотности тока в электроде (табл. 3—1).
Резкое повышение абсолютной величины тока и плотности тока в электроде без увеличения потерь на угар и разбрызгивание и без ухудшения формирования шва возможно благодаря наличию плотного слоя флюса вокруг зоны сварки; это предотвращает выдувание жидкого металла шва из сварочной ванны и сводит потери на угар и разбрызгивание до 1—3%. Увеличение силы тока
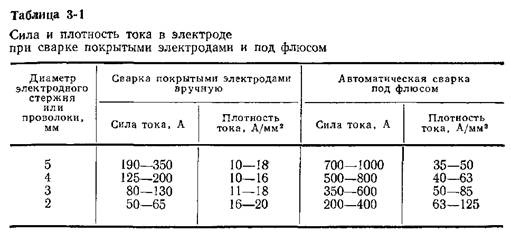
позволяет сваривать металл значительной толщины без разделки кромок с одной или двух сторон (производительность сварки для этого случая определяется в основном глубиной проплавления основного металла) и увеличивать количество наплавляемого в единицу времени металла. Коэффициент наплавки при сварке под флюсом составляет 14—18 г/А-ч против 8—12 г/А-ч при сварке покрытыми электродами. Повышение силы тока, увеличение глубины провара и коэффициента наплавки позволяют повысить производительность и при сварке многослойных швов. Отсутствие брызг — также серьезное преимущество сварки под флюсом, так как отпадает надобность в трудоемкой операции очистки от них поверхности свариваемых деталей.
При сварке под флюсом обеспечивается высокое и стабильное качество сварки. Это достигается за счет надежной защиты металла шва от воздействия кислорода и азота воздуха, однородности металла шва по химическому составу, улучшения формы шва и сохранения постоянства его размеров. В результате обеспечивается меньшая вероятность образования непроваров, подрезов и других дефектов формирования шва и отсутствие перерывов в процессе сварки, вызванных необходимостью смены электродов.
За счет уменьшения доли электродного металла в металле шва в среднем с 70% при сварке покрытыми электродами до 35% при сварке под флюсом и уменьшения потерь на угар, разбрызгивание и огарки снижается расход электродного металла и электроэнергии. Отпадает необходимость в защите глаз и лица рабочего и несколько уменьшается количество выделяемых в процессе сварки вредных газов, что улучшает условия труда. Для приобретения квалификации автосварщика необходимо затратить значительно меньше времени и средств, чем для овладения специальностью сварщика, работающего вручную.
Автоматическую и полуавтоматическую сварку под флюсом применяют в заводских и монтажных условиях для выполнения швов, расположенных в нижнем положении, обычно при толщине металла 2—100 мм. Сваривают стали различного состава, медь, титан, алюминий и сплавы на их основе. Сварку алюминия ведут не под флюсом, а по флюсу (см. гл. 11). За рубежом под флюсом сваривают и горизонтальные швы, расположенные на вертикальной плоскости. В отечественной промышленности этот способ из-за трудности удаления шлаковой корки и удержания флюса не находит практического применения. Сварку под флюсом широко используют и при наплавочных работах. Автоматическую сварку под флюсом ведут сварочной проволокой сплошного сечения диаметром 1—6 мм при силе тока 150—2000 А и напряжении дуги 22—55 В, полуавтоматическую— сварочной проволокой диаметром 0,8—2 мм при силе тока 100—500 А и напряжении дуги 22—38 В. В обоих случаях возможно применение активированной и порошковой проволок.
Основным методом автоматической и полуавтоматической сварки под флюсом является сварка одной дугой. С целью повышения производительности труда при сварке многослойных швов одной дугой в разделку вводят металлические наполнители в виде порошка, проволоки, окатышей и других материалов. В некоторых случаях наполнители вводят не только для увеличения производительности, но и для улучшения качества шва.
Для повышения коэффициента расплавления электрода можно применять автоматическую и полуавтоматическую сварку под флюсом с увеличенным вылетом электрода. При этом достигается предварительный нагрев электродной проволоки на участке вылета.
Повысить производительность процесса и качество сварного соединения можно путем автоматической сварки под флюсом двумя и более электродами. Различают многоэлектродную и многодуговую сварку. При многоэлектродной сварке все электроды присоединены к одному полюсу источника питания. При многодуговой сварке каждый из электродов подсоединен к отдельному источнику питания и они электрически изолированы друг от друга.
Существуют две разновидности многодуговой сварки: сварка в общую ванну, когда расплавляемый всеми дугами металл образует единую ванну, кристаллизующуюся как одно целое (рис. 3-3, а); сварка в раздельные ванны, или, как ее называют,


сварка раздвинутыми дугами, в этом случае каждая дуга образует свою ванну и последующая дуга расплавляет уже закристаллизовавшийся слой, сваренный предыдущей дугой (рис. 3-3, б). Многоэлектродная сварка ведется только в общую ванну.
Промышленное применение находят такие разновидности сварки в общую ванну:
A. Сварка сдвоенным электродом на обычных скоростях. При этом способе электроды могут быть расположены так, как указано на рис. 3-4, а, б. Выбор схемы расположения электродов зависит от условий сварки. Сдвоенный электрод применяют при сварке по зазорам, при двусторонней сварке стыковых швов для уменьшения глубины провара от первого слоя, при сварке многослойных швов и наплавочных работах. Повышение производительности сварки в этом случае достигается за счет увеличения количества электродного металла, вводимого в сварочную ванну за единицу времени.
Забиваем Сайты В ТОП КУВАЛДОЙ - Уникальные возможности от SeoHammer
Каждая ссылка анализируется по трем пакетам оценки: SEO, Трафик и SMM.
SeoHammer делает продвижение сайта прозрачным и простым занятием.
Ссылки, вечные ссылки, статьи, упоминания, пресс-релизы - используйте по максимуму потенциал SeoHammer для продвижения вашего сайта.
Что умеет делать SeoHammer
— Продвижение в один клик, интеллектуальный подбор запросов, покупка самых лучших ссылок с высокой степенью качества у лучших бирж ссылок.
— Регулярная проверка качества ссылок по более чем 100 показателям и ежедневный пересчет показателей качества проекта.
— Все известные форматы ссылок: арендные ссылки, вечные ссылки, публикации (упоминания, мнения, отзывы, статьи, пресс-релизы).
— SeoHammer покажет, где рост или падение, а также запросы, на которые нужно обратить внимание.
SeoHammer еще предоставляет технологию Буст, она ускоряет продвижение в десятки раз,
а первые результаты появляются уже в течение первых 7 дней.
Зарегистрироваться и Начать продвижение
Б. Сварка трехфазной дугой, при которой увеличивается коэффициент наплавки, что обусловливает применение этого способа для наплавочных работ, для сварки многослойных швов и угловых швов большого сечения.
B. Двухдуговая или многодуговая сварка на больших скоростях, при которой используют два наклонных электрода или вертикальный и наклонный электроды (рис. 3-5, а). Вместо одного вертикального электрода применяют также сдвоенный электрод (рис. 3-5, б). Иногда в зону дуги подают присадочный металл. При этих схемах удается увеличить глубину проплавления основного металла и улучшить формирование шва, что позволяет резко повысить скорость, а следовательно, и производительность сварки. Многодуговую сварку на больших скоростях применяют при изготовлении труб большого диаметра, балок различного сечения, вагонных конструкций и др. Скорость при сварке угловых швов в настоящее время достигает 90 м/ч, а при сварке стыковых швов —

300 м/ч. Работы по изысканию путей дальнейшего повышения скорости сварки продолжаются.
При сварке в раздельные ванны электроды располагают так, как показано на схеме рис. 3-5, а. Минимальное расстояние между дугами определяется длиной сварочной ванны, а максимальное — длительностью пребывания шлака в жидком состоянии. Сварку второй дугой следует вести по жидкому шлаку. При затвердевании шлака процесс становится неустойчивым.
Сварка раздвинутыми дугами позволяет значительно повысить пластические свойства сварного соединения за счет снижения скорости остывания металла шва и околошовной зоны и повысить производительность процесса за счет увеличения количества наплавляемого за единицу времени электродного металла. Способ применяется при сварке швов на сталях, склонных к закалке, и при сварке многослойных швов на толстом металле.
При сварке раздвинутыми дугами удается повысить стойкость металла шва против кристаллизационных трещин. Этот эффект обусловлен снижением доли основного металла в металле шва й предварительным подогревом, достигаемым за счет действия первой дуги. Кроме того, вторая дуга почти полностью переплавляет слой металла, образовавшийся за счет действия первой дуги. При этом устраняются трещины, которые могли возникнуть в первом слое.
|