Технология электрической сваркиКраткая характеристика основных видов сварки
Электрическая дуговая сварка. При электрической дуговой сварке, или коротко-дуговой сварке, нагрев и плавление металла осуществляется дуговым разрядом, возникающим между электродами. Энергию, необходимую для образования и поддержания дугового разряда, получают от источников питания постоянного или переменного тока. Широкое практическое применение находит дуга прямого действия (рис. 1-3, а), горящая между свариваемым металлом и специальным стержнем-электродом. Для сварки используется теплота, выделяемая в столбе дуги и на электродах.
Значительно меньшее применение находит дуга косвенного действия, горящая между двумя стержнями-электродами. В этом случае для расплавления основного металла, который не включен в электрическую цепь, используется теплота, выделяемая при соприкосновении свариваемой поверхности со столбом (плазмой) дуги, и теплота, получаемая за счет излучения и конвекции. Сварку дугой косвенного действия можно выполнять как с присадочным металлом, так и без него. Ограниченное применение

дуги косвенного действия обусловлено ее меньшей эффективностью. Возможно использование комбинированной дуги, включенной в сварочную цепь по схеме, приведенной на рис. 1-3, б, или по трехфазной схеме (рис. 1-3, в). В этих случаях дуговой разряд возникает между электродами и между электродами и основным металлом.
Дуговую сварку можно выполнять неплавящимся и плавящимся электродом. Сварку неплавящимся электродом осуществляют дугой прямого или косвенного действия. Шов образуется за счет плавления основного металла или основного и присадочного металлов. Материал электрода не участвует в образовании шва, к. п. д. дуги прямого действия достигает 0,3—0,4, к. п. д. дуги косвенного действия — 0,2—0,3.
При сварке угольным электродом питание дуги, как правило, осуществляется от источника постоянного тока при прямой полярности — электрод соединен с отрицательным, а основной металл с положительным полюсом (зажимом) источника питания. Сварка угольным электродом при обратной полярности (основной металл соединяется с отрицательным, а электрод — с положительным полюсом источника питания) не находит практического применения из-за перегрева электрода, а при сварке стали — также из-за значительного науглероживания металла шва. При сварке на прямой полярности науглероживание основного металла не наблюдается. Сварку вольфрамовым электродом ведут на постоянном токе при прямой полярности или на переменном токе с обязательной защитой области дуги инертным газом, предохраняющим электрод от окисления.
При сварке плавящимся электродом дуга горит между основным металлом и металлическим стержнем заданного химического состава, подаваемым в зону дуги по мере плавления. В состав шва входит расплавленный основной металл и металл плавящегося электрода— электродный металл, а в некоторых случаях еще и присадочный металл.
В качестве плавящегося электрода используют сварочную (электродную) проволоку круглого сечения, порошковую проволоку, электродную ленту и специальные электроды более сложной формы. Питание дуги осуществляется от источника переменного или постоянного тока при прямой либо обратной полярности. В некоторых случаях (например, при сварке на больших скоростях несколькими дугами) применяют комбинированное питание от источников постоянного и переменного тока.
В зависимости от числа электродов различают сварку одним, двумя и тремя электродами. Возможна сварка и большим числом электродов. Сварку, при которой все электроды подсоединены к одному полюсу источника питания, называют двухэлектродной (многоэлектродпой) сваркой, или сваркой сдвоенным (строенным) электродом. Если каждый из электродов получает независимое питание, процесс называют двухдуговым (многодуговым).
Сварка дугой прямого действия плавящимся электродом является основным видом электрической сварки плавлением, к. п. д. дуги при этом способе достигает 0,7—0,9.
Сварку плавящимся электродом дугой прямого действия можно осуществлять без присадочного металла (рис. 1-4, а) или с присадочным металлом. Присадочный металл подают в зону сварки вручную или механизмом в виде проволоки, ленты и т. п. (рис. 1-4, б) или вводят в разделку (зазор) между свариваемыми кромками (рис. 1-4, в) в виде прутка, порошка, крошки, стружки, окатышей и т. п.
Процесс сварки состоит из ряда последовательных операций, в результате которых формируется шов. К этим операциям относятся возбуждение и поддержание дугового разряда, манипуляция электродом для придания шву нужной формы и для направления электрода по оси соединения, перемещение дуги вдоль свариваемых кромок по мере формирования шва заданного сечения, прекращение процесса. В зависимости от того, производятся ли указанные операции вручную или при помощи механизмов, различают ручную полуавтоматическую и автоматическую сварку.
При ручной сварке все операции, необходимые для образования шва, выполняют вручную без применения механизмов; электродами длиной 250—450 мм — сварка плавящимся электродом, или 200—300 мм — сварка неплавящимся электродом. Для подвода тока к электроду служит специальный держатель. В процессе сварки держатель находится в руке сварщика.
При полуавтоматической сварке плавящимся электродом механизирована операция подачи электрода в зону дуги, для чего служит специальный подающий механизм. Манипуляции электродом, выполняемые для поддержания заданного режима, придания шву нужной формы и перемещения дуги вдоль свариваемых кромок, осуществляют вручную или при помощи простейшего механизма, приводимого в движение от руки. Сварку производят сварочной проволокой сплошного сечения или порошковой проволокой, подаваемыми из кассеты или непосредственно из бухты.

Для подвода тока к электроду служит держатель. Сварочная проволока от подающего механизма к держателю в большинстве случаев поступает по гибкому шлангу. Поэтому полуавтоматическую сварку иногда называют шланговой.
При автоматической сварке операции по возбуждению и поддержанию дугового разряда осуществляются сварочной головкой, а перемещение дуги (по мере отложения шва заданного сечения) вдоль свариваемых кромок — сварочной тележкой. Рабочий не принимает непосредственного участия в образовании шва, а управляет процессом сварки при помощи вспомогательных устройств (пульт управления, корректор). Автоматическая сварка является не полностью автоматизированным, а лишь механизированным процессом. Однако термин автоматическая (и полуавтоматическая) сварка общепринят в отечественной и иностранной литературе.
Забиваем Сайты В ТОП КУВАЛДОЙ - Уникальные возможности от SeoHammer
Каждая ссылка анализируется по трем пакетам оценки: SEO, Трафик и SMM.
SeoHammer делает продвижение сайта прозрачным и простым занятием.
Ссылки, вечные ссылки, статьи, упоминания, пресс-релизы - используйте по максимуму потенциал SeoHammer для продвижения вашего сайта.
Что умеет делать SeoHammer
— Продвижение в один клик, интеллектуальный подбор запросов, покупка самых лучших ссылок с высокой степенью качества у лучших бирж ссылок.
— Регулярная проверка качества ссылок по более чем 100 показателям и ежедневный пересчет показателей качества проекта.
— Все известные форматы ссылок: арендные ссылки, вечные ссылки, публикации (упоминания, мнения, отзывы, статьи, пресс-релизы).
— SeoHammer покажет, где рост или падение, а также запросы, на которые нужно обратить внимание.
SeoHammer еще предоставляет технологию Буст, она ускоряет продвижение в десятки раз,
а первые результаты появляются уже в течение первых 7 дней.
Зарегистрироваться и Начать продвижение
Автоматическую сварку плавящимся электродом ведут в большинстве случаев сварочной проволокой сплошного сечения диаметром 1—б мм. Проволока так же, как и при полуавтоматической сварке, подается из специальной кассеты или из бухты. Возможно применение порошковой проволоки и ленты. При автоматической сварке обеспечивается постоянство режима сварки (сила тока, напряжение, скорость сварки и др.), что обусловливает однородность качества шва по всей его длине. Автоматическая сварка обладает меньшей мобильностью, чем полуавтоматическая и ручная сварка, требует наличия специального оборудования и большей точности подготовки и сборки деталей под сварку, так как возможности изменения режима сварки на ходу в зависимости от колебания величины зазора, угла разделки кромок и т. п. весьма ограничены.
При сварке неплавящимся электродом из-за малого расхода электрода в процессе сварки нет необходимости в механизации операции его подачи в зону дуги. Эту операцию легко осуществляют вручную. При полуавтоматической сварке механизирована только операция передвижения дуги вдоль свариваемых кромок.
При дуговой сварке происходит энергичное взаимодействие находящегося в расплавленном состоянии металла сварочной ванны с кислородом и азотом воздуха, что приводит к изменению химического состава и ухудшению механических, коррозионных и других свойств металла шва. Поэтому возникает необходимость в защите зоны сварки от окружающего воздуха. Применявшаяся в первые годы развития сварочной техники сварка голым электродом и электродом со стабилизирующим покрытием сейчас используется в весьма ограниченном объеме и в книге не рассмотрена.

Широкое применение находит защита зоны сварки при помощи специального состава, наносимого на поверхность электродной проволоки (покрытый электрод) (рис. 1-5, а) или вводимого внутрь полого или имеющего специальную форму электрода (рис. 1-5, б и в). Последний называют порошковой проволокой. Роль покрытия сводится к защите зоны сварки от воздействия окружающего воздуха, легированию металла шва полезными элементами (а иногда и удалению из сварочной ванны вредных примесей) и к стабилизации дугового разряда.
При сварке покрытым электродом расплавляющееся по мере плавления стержня 1 покрытие 2 в зависимости от состава образует газовую или газошлаковую защиту 5, изолирующую зону дуги и сварочную ванну от атмосферного воздуха (рис. 1-6). По мере удаления дуги происходит остывание и кристаллизация металла сварочной ванны 4 и формирование шва 5. Расплавившееся покрытие всплывает на поверхность и после остывания образует шлаковую корку 6.
Как правило, покрытие наносят на электрод до сварки. При ручной сварке для обеспечения возможности подвода тока к электродному стержню на один из его концов на длине 20— 35 мм покрытие не наносят. Покрытая электродная проволока для автоматической сварки имеет специальную конструкцию, обеспечивающую возможность подвода к ней тока.
Широкое применение при автоматическом процессе находит защита зоны сварки гранулированным покрытием — флюсом

(рис 1-7). При этом способе флюс / подается в зону дуги отдельно от голой электродной проволоки 2. Флюс создает главным образом шлаковую защиту. Дуга горит между электродом и основным металлом в пузыре 5, образованном папами и газами, выделяемыми
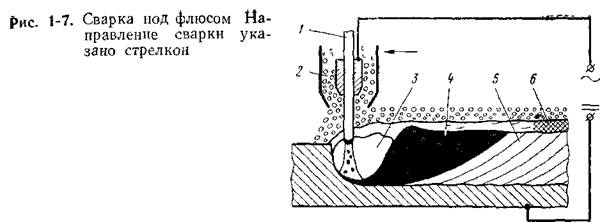
в столбе дуги. Столб дуги со* всех сторон окружен слоем флюса толщиной 30—50 мм. Под воздействием выделяемой дугой теплоты плавятся кромки свариваемого металла, электродная проволока и часть флюса, примыкающая к зоне дуги, и образуется сварочная ванна 4. По мере удаления дуги происходит кристаллизация сварочной ванны и формирование шва 5, соединяющего воедино свариваемые детали. Расплавленный флюс всплывает на поверхность сварочной ванны и при остывании образует шлаковую корку 6, легко отделяющуюся от шва. Нерасплавившаяся часть флюса может быть использована повторно. Расход флюса по массе примерно равен расходу электродной проволоки.
При сварке плавящимся электродом роль флюса в основном сводится к защите сварочной ванны и к обеспечению надлежащего качества металла шва. Защита зоны дуги флюсом применяется и при полуавтоматическом процессе.
При сварке с газовой защитой (рис. 1-8) зона сварки окружена газом /, подаваемым под небольшим избыточным давлением из сопла 2, обычно расположенного концентрично электроду. Газовая защита применяется при сварке плавящимся и неплавящимся электродом. Роль газа сводится в основном к физической изоляции сварочной ванны от окружающего воздуха. В качестве защитной среды служат инертные и активные газы и их смеси.

Дуговую сварку в защитных газах иногда называют газоэлектрической, однако этот термин не отражает сущности происходящих явлений. Газоэлектрическим может быть назван способ, при котором теплота для плавления металла получается не только за счет дугового разряда , но и за счет химических реакций или других процессов, происходящих в газовой фазе. При сварке в защитных газах часть теплоты, выделяемой за

счет химических реакций, в общем балансе теплоты весьма незначительна. Некоторое исключение представляют атомноводородная сварка, которая находит весьма ограниченное практическое применение, и сварка сжатой дугой. Разновидностью сварки в защитных газах является сварка с контролируемой атмосферой (рис. 1-9). Сварка происходит в камере, где сначала создается вакуум, затем камера заполняется аргоном, гелием или смесью газов (создается контролируемая атмосфера). При этом обеспечивается более полная защита сварочной ванны. Этот метод применяют при дуговой сварке непла-вящимся электродом химически активных металлов и сплавов автоматом, полуавтоматом или вручную. В некоторых случаях сварку в вакууме ведут без создания специальной атмосферы. Принципиально возможна, но находит весьма ограниченное применение сварка с комбинированной защитой, при которой газ и покрытие наносят на поверхность электродной проволоки при помощи электромагнитных сил (магнитное покрытие) или вводят внутрь электрода до сварки либо в процессе ее. Сварку с комбинированной защитой можно использовать как при полуавтоматическом, так и при автоматическом процессе.
Сервис онлайн-записи на собственном Telegram-боте
Попробуйте сервис онлайн-записи VisitTime на основе вашего собственного Telegram-бота:
— Разгрузит мастера, специалиста или компанию;
— Позволит гибко управлять расписанием и загрузкой;
— Разошлет оповещения о новых услугах или акциях;
— Позволит принять оплату на карту/кошелек/счет;
— Позволит записываться на групповые и персональные посещения;
— Поможет получить от клиента отзывы о визите к вам;
— Включает в себя сервис чаевых.
Для новых пользователей первый месяц бесплатно.
Зарегистрироваться в сервисе
В последние годы находит применение полуавтоматическая сварка активированной проволокой сплошного сечения и порошковой проволокой без дополнительной защиты. В состав активированной проволоки вводят элементы-раскислители и элементы, связывающие азот в стойкие нитриды, оказывающие незначительное влияние на качество металла шва, имеющего ферритную структуру. В сердечник порошковой проволоки вводят железный порошок, нитридо- и шлакообразующие составляющие.
Разновидностью дуговой сварки является плазменная сварка (сварка сжатой дугой). При сварке столб дуги имеет более высокую температуру. Это обусловливается свойством дугового разряда, заключающимся в том, что при искусственном сжатии столба дуги и охлаждении его наружных слоев наблюдается повышение температуры. Сжатая дуга образуется в дуговом разряде, возникающем в узком канале.
Если дуговой разряд возникает между вольфрамовым или медным электродом и основным металлом, то такая дуга называется дугой прямого действия, иногда именуемой проникающей дугой (рис. 1-10, а). Если одним из электродов служит сопло (оно может конструктивно совпадать с каналом, в котором создается столб плазмы), то такая дуга называется дугой косвенного действия или плазменной струей (рис. 1-10, б). Струя плазмы в этом случае выделяется из столба дуги в виде факела.
Для образования сжатой дуги вдоль ее столба через канал в сопле пропускается нейтральный одноатомный газ (аргон, гелий) или двухатомный газ (азот, водород, окись углерода или другие газы и их смеси). Газ сжимает столб дуги, что приводит к повышению его температуры до 16 000° С при дуге косвенного действия и до 33 000° С при дуге прямого действия, и образует так называемую холодную плазменную струю. Сжатая дуга является весьма концентрированным источником теплоты (удельная мощность более 500 кВт/см2). Газ в столбе сжатой дуги характеризуется высокой степенью ионизации, при которой он обладает весьма значительной электропроводностью, приближающейся к электропроводности проводника (например металла).
Для защиты плавильного пространства от окружающего воздуха вокруг сжатой дуги подается дополнительный защитный газ (аргон, углекислый газ), а иногда флюс. Для получения сжатой дуги служат специальные устройства — плазмотроны.
Сжатую дугу используют также для резки металла и напыления.
Для сварки находит применение микроплазменный процесс, при котором нагрев металла осуществляется высокотемпературной тонкой струей — лучом плазмы, обеспечивающей весьма высокую концентрацию энергии.

Электрошлаковая сварка. При электрошлаковом процессе основная часть энергии, расходуемая на нагрев и плавление металла, обеспечивается за счет теплоты, выделяемой в замкнутом объеме расплавленного шлака — шлаковой ванне при прохождении через нее тока. Шлаковая ванна 1 образуется (наводится) путем расплавления флюса, заполняющего пространство между кромками основного металла 2 и специальными охлаждаемыми водой приспособлениями—ползунами 5, плотно прижатыми к поверхности свариваемых

деталей (рис. 1-11). Флюс плавится дугой, возникающей в начальный период сварки между основным металлом и электродной проволокой. После расплавления определенного количества флюса дуга шунтируется расплавленным шлаком и гаснет. Длина шлаковой ванны практически равна толщине основного металла, а ширина определяется зазором между свариваемыми кромками. Глубину шлаковой ванны выбирают в зависимости от технологических условий (состава основного металла, режима сварки и др.)-
Необходимая для осуществления шлакового процесса энергия доставляется от источника питания переменного или постоянного тока, подсоединяемого к основному металлу и плавящемуся электроду (электродам) 4, вводимому в зазор между свариваемыми кромками и погруженному в шлаковую ванну. Электрод располагают посередине шлаковой ванны или перемещают в зазоре от одной поверхности свариваемых деталей к другой. Ток к электроду подводится при помощи мундштука 5. Проходя через шлаковую ванну, ток нагревает ее до температуры, превосходящей температуру плавления основного и электродного металлов.
Шлак расплавляет кромки основного металла и электрод, который подается в шлаковую ванну со скоростью, равной скорости его плавления. Расплавленные электродный и основной металлы стекают на дно шлаковой ванны, образуя сварочную (металлическую) ванну 6. По мере удаления источника нагрева происходит затвердевание—кристаллизация металла сварочной ванны. Расплавленный шлак, находящийся над металлической ванной, достаточно надежно защищает металл от воздействия воздуха. По мере заполнения зазора между свариваемыми кромками мундштук при помощи специального привода передвигается вдоль свариваемого изделия.
Шлаковая ванна, наведенная в начале сварки данного шва, по мере его формирования перемещается от начала детали к ее концу. Для восполнения расхода шлака, затрачиваемого на образование корочки на поверхности шва и потери на испарение, в шлаковую ванну небольшими порциями добавляется флюс.
Электрошлаковую сварку, как правило, ведут при вертикальном положении изделий. Кромки расположены вертикально или под углом до 30° к вертикали.
Электрошлаковый процесс применяют для сварки углеродистых и легированных конструкционных сталей, специальных сталей, алюминия, титана и других металлов и сплавов. Возможна сварка металла практически неограниченной толщины.
В монтажных условиях часто возникает необходимость сварки вертикальных швов металла толщиной 10—12 мм. В этом случае из-за малого объема шлаковой ванны имеет место не шлаковый, а дуговой процесс. Этот процесс, получивший название дуговой сварки с принудительным формированием, в настоящее время находит ограниченное практическое применение. Дуговую сварку вертикальных швов с принудительным формированием выполняют также в защитных газах и порошковой проволокой. Оборудование и технология дуговой сварки с принудительным формированием мало отличаются от применяемых при электрошлаковой сварке.
Электроннолучевая сварка. При этом способе сварки для нагрева и расплавления основного металла используется энергия, получаемая в результате интенсивной бомбардировки его быстро-движущимися в вакууме электронами. При попадании на поверхность свариваемых деталей электроны тормозятся и происходит превращение кинетической энергии в тепловую (рис. 1-12). Свариваемая деталь /, помещенная в специальную герметическую камеру 2, в которой откачивающие воздух насосы обеспечивают требуемый вакуум, при помощи механизма 3 передвигается со скоростью сварки. Сварка производится электронным лучом 4, представляющим собой сфокусированный поток электронов.
Комплекс устройств, служащих для формирования и фокусировки электронного луча, называют сварочной электронной пушкой. В процессе сварки кинетическая энергия электронов превращается в тепловую, которая расходуется на плавление кромок свариваемых деталей. По мере удаления источника нагрева происходит затвердевание сварочной ванны и образование шва. Металл шва, так же как и при других видах сварки плавлением, имеет литую структуру. Концентрация энергии электроннолучевой сварки очень высока, что обеспечивает получение узкого и глубокого шва и узкой околошовной зоны. Провар при этом виде сварки, как правило, имеет форму острого клина. Оператор, осуществляющий сварку в зависимости от размеров камеры, находится за ее пределами или в самой камере.
Лазерная сварка. В последнее время в сварочной практике находят применение оптические квантовые генераторы, так называемые лазеры. При лазерной сварке нагрев и плавление металла осуществляются мощным световым лучом, получаемым от специальных твердых или газовых излучателей. Для управления сформированного излучателем луча служат специальные

оптические системы (рис. 1-13). Вакуум при сварке лазером не нужен, и сварка может осуществляться на воздухе даже на значительном расстоянии от генератора. Энергия, излучаемая лазерами, пока невелика и составляет от сотых долей до единиц джоулей. Коэффициент полезного действия лазеров также еще очень низок. Характерной является узкая и глубокая форма проплавления основного металла. Лазерная сварка может применяться в приборостроении и в специальных случаях.
Все существующие виды сварки плавлением имеют конечную цель — получение сварных соединений, обеспечивающих необходимую несущую способность сварной конструкции, ее длительную работу в условиях эксплуатации при минимальной затрате труда и средств. Очевидно, что рациональность использования того или иного вида сварки зависит от конкретных условий, и поэтому рекомендации по этому вопросу могут быть даны только для этих случаев.
|