Технология электрической сваркиКлассификация электродов
Электроды для ручной дуговой сварки классифицируют по следующим основным признакам: по назначению — для сварки стали, чугуна, алюминия, для наплавочных работ и т. п ; по типу покрытия — целлюлозные, рутиловые, фтористо-кальциевые, ильменитовые, рудно-кислые и др.; по механическим свойствам металла шва; по способу нанесения покрытия — окунанием или опрессовкой; по количеству покрытия, нанесенного на стержень, — голые электроды, тонкопокрытые, толстопокрытые.
Все эти признаки тесно взаимосвязаны. Группы тех или иных признаков положены в основу классификации электродов в национальных стандартах различных стран. Электроды для сварки и наплавки сталей в зависимости от назначения в соответствии с ГОСТ 9466—60 подразделены на ряд классов: для сварки углеродистых и легированных конструкционных сталей; для сварки легированных теплоустойчивых сталей; для сварки высоколегированных сталей с особыми свойствами; для наплавки поверхностных слоев с особыми свойствами.
Электроды для сварки конструкционных и теплоустойчивых сталей согласно ГОСТ 9467—60 классифицированы по механическим характеристикам металла шва и сварного соединения, выполненных этими электродами. Электроды для сварки теплоустойчивых сталей классифицированы, кроме того, и по химическому составу металла шва. ГОСТ 9467—60 устанавливает в зависимости от состава следующие виды покрытий электродов для сварки конструкционных и теплоустойчивых сталей: рудно-кислое, обозначаемое буквой Р; рутиловое — Т; фтористо-кальциевое—Ф; органическое — О.
Электроды для сварки высоколегированных сталей с особыми свойствами по ГОСТ 10052—62 подразделены на ряд типов в зависимости от химического состава наплавленного металла и механических свойств металла шва. Каждому типу может соответствовать одна или несколько марок электродов. Марка электродов характеризуется определенным составом покрытия и электродного стержня, технологическими свойствами и свойствами металла шва.
Механические свойства, регламентируемые стандартом или техническими условиями для электродов данной марки, относятся к случаю наплавки металла или сварки стыкового шва сравнительно небольшой длины. В зависимости от условий сварки механические свойства металла шва реальной сварной конструкции могут отличаться от свойств электродов, указанных в стандарте или паспорте.
Наиболее полно свойства каждой конкретной марки электродов отражены в паспорте. Паспорт содержит следующие сведения: условное обозначение электродов, их назначение, марку сварочной проволоки и данные о покрытии электродов. К последним относятся состав, номера стандартов или технических условий на составляющие покрытий, соотношение массы покрытия и массы стержня, толщина покрытия в зависимости от диаметра стержня, режимы сушки и прокалки, а также условия хранения электродов. В паспорте содержатся также краткие технологические указания по сварке, характеристики расплавления электродов, химический состав и свойства наплавленного металла, металла~шва или сварного соединения.
Общие требования, предъявляемые к электродам, регламентированы ГОСТ 9466—60. Это размеры и допуски отклонений от номинальных размеров, качество покрытия, влагостойкость покрытия, требования к технологическим и металлургическим свойствам электродов. Этим же стандартом обусловлены правила приемки электродов, методы испытаний швов и сварных соединений, условия маркировки и упаковки, данные о документации на электроды.
Условное обозначение электродов для дуговой сварки сталей и наплавки состоит из обозначения марки и типа электрода, диаметра стержня и номера стандарта. В условном обозначении электродов для сварки конструкционных и теплоустойчивых сталей указан также вид покрытия. Например, условное обозначение электрода АНО-7 Э50А-5,0-Ф ГОСТ 9467—60 расшифровывается следующим образом: АНО-7 — марка электрода; Э50А — тип электрода (Э— электрод для дуговой сварки, 50-— минимальное гарантируемое временное сопротивление металла шва в кгс/мм2; А — гарантирование получения повышенных пластических свойств металла шва); 5,0 — диаметр электродного стержня в мм; Ф — фтористо-кальциевое покрытие; ГОСТ 9467—60—номер стандарта на данный электрод.
Металлургические процессы, происходящие при сварке покрытыми электродами. Металлургические процессы при дуговой сварке покрытым электродом характеризуются малыми количествами реагирующих веществ, кратковременностью и высокими температурами взаимодействия фаз. От характера и интенсивности металлургических реакций существенно зависит химический состав, а следовательно и механические свойства металла шва. Перенос электродного металла через дуговой промежуток в основном осуществляется каплями. Расплавленное покрытие частично переносится через дуговой промежуток в виде шлаковой оболочки вокруг капель металла, а частично непосредственно стекает в ванну. В процессе сварки наблюдается значительное перемешивание металла и шлака, что увеличивает межфазную поверхность металл-шлак. На торце электрода и в дуговом промежутке капли металла и шлака нагреваются до температуры 2100—2300° С, а средняя температура металла в сварочной ванне составляет примерно 1700—1800° С. Температура газов (плазмы) в столбе дуги достигает 5000—6000° С. Большие межфазные поверхности и высокая температура обеспечивают при сварке интенсивное взаимодействие металла со шлаком и газами.
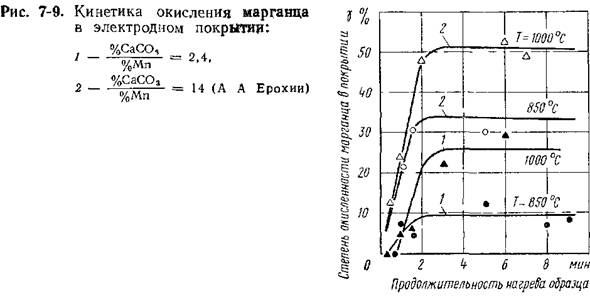
Процессы, происходящие при нагреве твердого покрытия на конце электрода, имеют очень важное значение, так как от характера их протекания зависят состав, количество поступающих в атмосферу дуги газов, степень окисления ферросплавов и др. В твердом покрытии при нагреве происходит разложение или сгорание органических веществ, диссоциация карбонатов и окислов, окисление ферросплавов. Так, диссоциация магнезита начинается уже при температуре около 430° С, а мрамора — около 540° С; Мп02 начинает диссоциировать в атмосфере воздуха при температуре 470° С, переходя в Мп203. Органические составляющие начинают разлагаться еще при более низких температурах. При наличии окислителей в покрытии органические вещества сгорают, образуя газовые смеси, состоящие в основном из С02, Н2, Н20 и СО.
Забиваем Сайты В ТОП КУВАЛДОЙ - Уникальные возможности от SeoHammer
Каждая ссылка анализируется по трем пакетам оценки: SEO, Трафик и SMM.
SeoHammer делает продвижение сайта прозрачным и простым занятием.
Ссылки, вечные ссылки, статьи, упоминания, пресс-релизы - используйте по максимуму потенциал SeoHammer для продвижения вашего сайта.
Что умеет делать SeoHammer
— Продвижение в один клик, интеллектуальный подбор запросов, покупка самых лучших ссылок с высокой степенью качества у лучших бирж ссылок.
— Регулярная проверка качества ссылок по более чем 100 показателям и ежедневный пересчет показателей качества проекта.
— Все известные форматы ссылок: арендные ссылки, вечные ссылки, публикации (упоминания, мнения, отзывы, статьи, пресс-релизы).
— SeoHammer покажет, где рост или падение, а также запросы, на которые нужно обратить внимание.
SeoHammer еще предоставляет технологию Буст, она ускоряет продвижение в десятки раз,
а первые результаты появляются уже в течение первых 7 дней.
Зарегистрироваться и Начать продвижение
Значительное влияние на кинетику и степень диссоциации составляющих покрытия оказывают их минералогический состав, дисперсность, степень гидратации, состав покрытия и т. д. Добавление окислов, фторидов и металлических порошков к карбонатам приводит к смещению интервала диссоциации карбонатов в область низких температур. Это вызвано прежде всего улучшением теплопроводности покрытий и развитием экзотермических реакций окисления.
Одной из главных реакций, происходящих в твердой фазе при нагреве покрытия, является окисление ферросплавов кислородом воздуха и углекислым газом, выделяющимся при диссоциации карбонатов. Наличие карбоната в покрытии способствует большему окислению ферросплавов к моменту расплавления покрытия (рис. 7-9).
Состав и количество газов в атмосфере дуги зависят от типа покрытия При плавлении покрытий рудно-кислого, рутилового и органического типов в результате разложение органических составляющих и окисления углерода образуются главным образом водород, окись углерода и пары воды При введении в рутиловое покрытие карбонатов атмосфера дуги содержит значительное количество углекислого газа. При сварке электродами с фтористо-кальциевым покрытием атмосфера дуги содержит углекислый газ, окчсь углерода и пары воды.

В табл. 7-14 приведены результаты анализа газов, образующихся при сварке электродами с различными покрытиями. Кроме этих газов в атмосфере дуги всегда имеется азот воздуха. Количество его в основном определяется эффективностью газовой защиты.
Азот диссоциирует в дуговом промежутке (рис. 7-10). Диссоциация азота повышает скорость его абсорбции расплавленным железом.
Снижение количества азота в металле шва при сварке покрытыми электродами достигается надежной газошлаковой защитой. Максимальное содержание азота наблюдается в металле шва, сваренного электродами со стабилизирующим покрытием. Оно составляет 0,1—0,2% и значительно превышает максимальную растворимость азота в железе при комнатной температуре. С увеличением толщины покрытия содержание азота в металле шва снижается (рис. 7-11). Газообразующие компоненты в процессе плавления электрода выделяют значительное количество газов и снижают парциальное давление азота в атмосфере дуги, что обеспечивает уменьшение его содержания в металле шва (рис. 7-12).
Содержание азота в металле шва зависит от степени его легирования. Повышение содержания углерода в проволоке или по-


крытии приводит к снижению содержания азота в металле шва. Углерод снижает растворимость азота в железе. Кроме того, окисление углерода способствует уменьшению абсорбции азота вследствие снижения парциального давления азота у реакционной границы газ—металл. Марганец в небольших количествах снижает содержание азота в металле шва, а с повышением концентрации увеличивает его содержание, что связано с образованием нитридов и изменением структуры металла.
Кремний снижает растворимость азота в стали. Значительно увеличивает содержание азота легирование швов хромом и молибденом. Увеличение содержания титана (свыше 0,2%) и алюминия (свыше 1%) в наплавленном металле приводит к росту содержания азота. При высоких содержаниях этих элементов практически весь азот в металле шва находится в виде нитридов.
Большое влияние на содержание азота в металле шва оказывает режим сварки. Повышение напряжения дуги (удлинение дуги) приводит к ухудшению газовой защиты расплавленного металла и возрастанию концентрации азота в металле шва (рис. 7-13). Увеличение содержания азота в металле шва, вызванное удлинением дуги, особенно заметно при недостаточно надежной шлаковой защите металла.
С увеличением силы тока увеличивается температура капель. В сталях типа 18-8 это приводит к снижению растворимости азота, а в низкоуглеродистой стали — напротив, к увеличению растворимости. Поэтому увеличение силы тока вызывает снижение содержания азота при сварке сталей типа 18-8, а при сварке низкоуглеродистой стали содержание азота сначала растет, а затем начинает снижаться вследствие интенсивного испарения металла и уменьшения парциального давления азота у реакционной границы газ—металл. Содержание азота в металле шва при сварке постоянным током на прямой полярности, как правило, выше,

чем на обратной. Это связано с более благоприятными условиями контактирования металла с азотом при сварке на прямой полярности, а также более низкой температурой капель и меньшим испарением металла.
Большое влияние на процесс поглощения азота металлом при сварке оказывает содержание кислорода в атмосфере дуги. Кислород в дуге взаимодействует с молекулярным азотом ? с образованием N0. Попадая на металл капель или ванны, N0 диссоциирует. Образующиеся при этом атомарные азот и кислород активно растворяются в металле.
Водород, как и азот, оказывает вредное воздействие на качество металла шва. В зависимости от температуры водород может находиться в молекулярном, атомарном или ионизированном состоянии. Степень диссоциации водорода зависит от температуры (см. рис. 7-10). В столбе дуги подавляющее количество водорода находится в атомарном состоянии. При дуговой сварке покрытыми электродами содержание водорода в металле шва в ряде случаев может превышать величину растворимости его в железе при равновесных условиях и температуре кристаллизации. Растворимость водорода в жидких сплавах железа зависит от концентрации легирующих элементов (рис. 7-14).
Кислород является элементом, наиболее активно препятствующим поглощению водорода жидким железом. С повышением содержания кислорода в металле растворимость водорода понижается. Раскислители (марганец, кремний, титан, алюминий), связывая растворенный в стали кислород, могут тем самым косвенно влиять на содержание в ней водорода.
При сварке покрытыми электродами главным источником водорода является покрытие. В процессе нагрева покрытия электрода и при его плавлении происходит разложение органических составляющих, диссоциация карбонатов и окислов, взаимодействие между составляющими покрытия и другие реакции, которые определяют парциальное давление водорода и паров воды в атмосфере дуги, а следовательно, и их содержание в металле шва. Характер протекания этих процессов определяется главным образом составом и влажностью покрытия (рис. 7-15).
Увеличение количества органических составляющих в покрытии приводит к повышению содержания водорода в металле шва. Введение карбонатов в покрытие снижает парциальное давление водорода в атмосфере дуги и количество водорода в металле
Сервис онлайн-записи на собственном Telegram-боте
Попробуйте сервис онлайн-записи VisitTime на основе вашего собственного Telegram-бота:
— Разгрузит мастера, специалиста или компанию;
— Позволит гибко управлять расписанием и загрузкой;
— Разошлет оповещения о новых услугах или акциях;
— Позволит принять оплату на карту/кошелек/счет;
— Позволит записываться на групповые и персональные посещения;
— Поможет получить от клиента отзывы о визите к вам;
— Включает в себя сервис чаевых.
Для новых пользователей первый месяц бесплатно.
Зарегистрироваться в сервисе

шва. Наличие фтористых соединений в составе покрытия способствует снижению концентрации водорода в металле благодаря связыванию его в химически прочное и нерастворимое в металле соединение HF.
Содержание водорода в металле шва зависит и от режимов сварки. С увеличением силы тока концентрация водорода в шве возрастает (рис. 7-16). Объясняется это увеличением температуры дуги и капель электродного металла. Увеличение напряжения дуги приводит к снижению концентрации водорода в металле шва. Удлинение дуги вызывает подсос воздуха из окружающей атмосферы, снижение парциального давления водорода в атмосфере дуги и повышенное окисление металла. В результате поглощение водорода расплавленным металлом снижается.
Процесс поглощения водорода металлом идет преимущественно на стадии капли. Этому способствуют более высокая температура и большая удельная поверхность расплавленного металла.
Газы атмосферы дуги окисляют расплавленный электродный металл. При сварке электродами со стабилизирующим покрытием расплавленный металл окисляется главным образом кислородом, попадающим в атмосферу дуги из окружающего воздуха. Кислород при температуре дуги в значительной степени диссоциирован (рис. 7-10). Окисление металла с участием атомарного кислорода идет более интенсивно, чем молекулярного.
При сварке толстопокрытыми электродами количество кислорода, попадающего в атмосферу дуги из окружающего воздуха, незначительно и расплавленный металл окисляется преимущественно водяным паром и углекислым газом, образующимися при нагреве и расплавлении покрытия. Состав газов в атмосфере дуги зависит и от режима сварки. Увеличение длины дуги приводит к ухудшению защиты капель расплавленного металла, подсосу
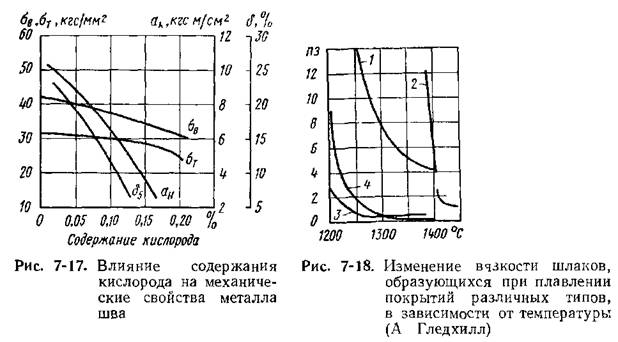
воздуха из окружающей атмосферы и повышению окисления металла (см. рис. 7-13).
Кислород в металле резко ухудшает его механические и технологические свойства (рис. 7-17). С повышением содержания кислорода снижаются временное сопротивление, предел текучести, ударная вязкость, ухудшаются ковкость, коррозионная стойкость, жаропрочность и другие свойства металла шва. Выделение азота и водорода, а также окиси углерода из сварочной ванны является в основном причиной образования пор (см § 6-4)
Получение плотных швов может быть достигнуто либо путем снижения содержания газов в сварочной ванне ниже предела растворимости при температуре кристаллизации (плавления), либо обеспечением процесса дегазации металла сварочной ванны до момента кристаллизации. Первый способ обеспечения плотных швов реализуется при сварке электродами с фтористо-кальциевым покрытием. Высокая температура прокалки, введение фторидов и карбонатов в покрытие, хорошее раскисление ванны обеспечивают низкое содержание водорода, азота и кислорода в металле шва.
При сварке электродами с рудно-кислым, рутиловым и органическим покрытиями сварочная ванна содержит большое количество газов (водорода, кислорода). Благодаря этому образование и выделение пузырьков газа (кипение ванны) происходит, когда металл находится в жидком состоянии и имеет малую вязкость. В этих условиях пузырьки свободно удаляются до момента кристаллизации металла и поры не образуются.
|