Технология электрической сваркиЭлектроды для сварки углеродистых и низколегированных сталей
Для сварки углеродистых и низколегированных сталей применяют преимущественно электроды с рудно-кислым, рутило-вым, органическим и фтористо-кальциевым покрытиями. Наибольшее распространение в нашей стране получили электроды с рутиловым покрытием. Доля электродов с рутиловым покрытием в настоящее время составляет около 70% общего выпуска электродов. Для сварки особо ответственных конструкций применяют главным образом электроды с фтористо-кальциевым покрытием. Доля отечественных электродов с органическим покрытием невелика. Эти электроды применяют главным образом при строительстве магистральных трубопроводов. Все более широкое распространение получают высокопроизводительные электроды с железным порошком в покрытии на рутиловой и фтористо-кальциевой шлакообразующей основе.
Все указанные электроды изготовляют с использованием сварочной проволоки Св-08 и Св-08А. Легирование металла шва при сварке электродами этой группы осуществляется путем введения легирующих составляющих в покрытие.
Электроды со стабилизирующим покрытием. Стабилизирующее покрытие наносят на электродный стержень тонким слоем. Масса покрытия составляет обычно 1—2% массы стержня.
Повышение устойчивости горения дуги достигается введением в состав покрытия соединений калия и натрия (хромата, бихро-мата, силиката, карбоната и др.), а также карбонатов кальция, магния или бария. Наличие в покрытии солей щелочных и щелочноземельных металлов приводит к уменьшению энергии, выделяемой на катоде при сварке постоянным током прямой полярности, вследствие чего резко снижается скорость плавления электрода.
Из-за больших потерь от угара и разбрызгивания, малой скорости расплавления, отсутствия возможности производить сварку на повышенных токах электроды со стабилизирующим покрытием обладают весьма низкой производительностью.
Механические свойства металла шва, сваренного электродами со стабилизирующим покрытием, низкие и практически не отличаются от свойств металла шва, сваренного голой проволокой. Вследствие этого электроды со стабилизирующим покрытием применяют чрезвычайно редко, лишь для сварки неответственных изделий.
окисления марганца (7-2) и железа:
Реакция (7-7) приводит к обогащению жидкого металла кислородом. Значительное количество теплоты, выделяющейся при окислении марганца, обеспечивает высокую скорость расплавления электрода. Основная часть марганца в ферромарганце в процессе сварки окисляется, и лишь небольшая часть переходит в металл шва. Металл, наплавленный электродами с рудно-кислым покрытием, по химическому составу чаще всего соответствует кипящей стали и содержит до 0,12% С, до 0,10% Si, 0,6—0,9% Мп, до 0,05% S и до 0,05% Р. Содержание газов обычно находится в следующих пределах: 0,09—0,12% кислорода, 0,015—0,025% азота, 20—25 см3/100 г водорода.
Электроды с рудно-кислым покрытием позволяют производить сварку переменным и постоянным током. При нормальной толщине покрытия (коэффициент массы покрытия 30—40%) эти электроды пригодны для сварки во всех пространственных положениях
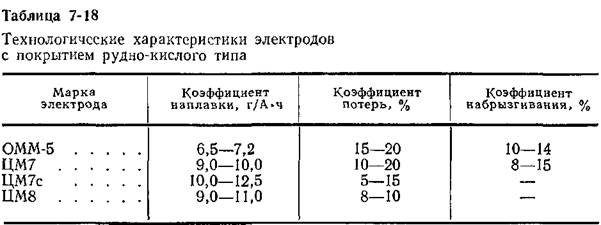
При большой толщине покрытия электроды применяются только для сварки в нижнем положении. В табл, 7-18 приведены некоторые технологические характеристики электродов с рудно-кислым покрытием.
Металл швов, выполненных электродами с рудно-кислым покрытием, склонен к образованию кристаллизационных трещин. Это обусловлено высоким содержанием в нем газов и неметаллических включений.
Шлаки, образующиеся при расплавлении рудно-кислых покрытий, обладают сравнительно небольшой способностью обессеривать металл шва. По вышеизложенным причинам электроды с рудно-кислым покрытием не рекомендуется применять для сварки сталей с повышенным содержанием серы и углерода, а также для сварки жестких конструкций, в которых могут возникать значительные напряжения.
Электроды с рудно-кислым покрытием позволяют сваривать металл с ржавыми кромками и окалиной, вести сварку удлиненной дугой и обеспечивают при этом получение плотных швов. Поры при сварке электродами этого типа могут возникать при чрезмерно высокой температуре их прокалки, при повышенном содержании марганца в покрытии, при сварке сталей с высоким содержанием кремния или серы.
Высокотемпературная прокалка рудно-кислого покрытия способствует снижению парциального давления водорода и паров воды в атмосфере дуги, а следовательно, и снижению содержания водорода в сварочной ванне. В результате степень пересыщения металла газом уменьшается и при снижении температуры расплавленного металла процесс дегазации идет медленно. Вялое кипение не обеспечивает дегазации металла до момента кристаллизации, и в металле образуются поры.
Высокотемпературная прокалка электродов и чрезмерное раскисление марганцем способствуют развитию кремневосстанови-тельного процесса и повышению концентрации кремния в жидком металле. Кремний, будучи поверхностно-активным элементом, адсорбируется на поверхности металла и ухудшает условия дегазации. Выделение газов при этом протекает медленно, что вызывает образование пор. Аналогичное влияние на условия дегазации металла оказывает сера, которая также обладает поверхностной активностью.
По механическим свойствам металла шва и сварного соединения электроды с рудно-кислым покрытием, как правило, относятся к типу Э42 (ГОСТ 9467—60). До недавнего времени электроды с рудно-кислым покрытием были наиболее массовыми. Наличие в покрытии значительного количества окислов железа и ферромарганца при сварке этими электродами обусловливает выделение в зону дыхания сварщика большого количества токсичных соединений марганца. В связи с повышенной токсичностью объемы выпуска электродов с рудно-кислым покрытием в последние годы резко сократились. Их заменили электроды с рутиловым покрытием.
Электроды с рутиловым покрытием. Шлакообразующую основу рутиловых покрытий составляют рутиловый концентрат, различные алюмосиликаты (слюда, полевой шпат, каолин и др.) и карбонаты (мрамор, магнезит). Газовая защита расплавленного металла обеспечивается за счет разложения органических составляющих покрытия, а также карбонатов. Раскисление металла осуществляется главным образом марганцем, вводимым с ферромарганцем,
Известные рутиловые покрытия условно можно разделить на две подгруппы: рутилалюмосиликатные и рутилкарбонатные. Шлакообразующую основу покрытий первой подгруппы составляют рутил и различные алюмосиликаты. Содержание карбонатов в них, как правило, не превышает 5%, Покрытия второй подгруппы содержат 10—15% карбонатов. В рутиловых покрытиях основными окислителями являются пары воды и углекислый газ.
Забиваем Сайты В ТОП КУВАЛДОЙ - Уникальные возможности от SeoHammer
Каждая ссылка анализируется по трем пакетам оценки: SEO, Трафик и SMM.
SeoHammer делает продвижение сайта прозрачным и простым занятием.
Ссылки, вечные ссылки, статьи, упоминания, пресс-релизы - используйте по максимуму потенциал SeoHammer для продвижения вашего сайта.
Что умеет делать SeoHammer
— Продвижение в один клик, интеллектуальный подбор запросов, покупка самых лучших ссылок с высокой степенью качества у лучших бирж ссылок.
— Регулярная проверка качества ссылок по более чем 100 показателям и ежедневный пересчет показателей качества проекта.
— Все известные форматы ссылок: арендные ссылки, вечные ссылки, публикации (упоминания, мнения, отзывы, статьи, пресс-релизы).
— SeoHammer покажет, где рост или падение, а также запросы, на которые нужно обратить внимание.
SeoHammer еще предоставляет технологию Буст, она ускоряет продвижение в десятки раз,
а первые результаты появляются уже в течение первых 7 дней.
Зарегистрироваться и Начать продвижение
Важное значение имеют окислительно-восстановительные реакции марганца и кремния, в значительной мере определяющие наличие силикатных неметаллических включений в металле шва, а следовательно, и его механические свойства. При сварке электродами с рутилкарбонатным покрытием кремневосстановитель-ный процесс получает меньшее развитие, чем при сварке электродами с рутилалюмосиликатным покрытием. Этому способствуют более высокие основность шлака и окислительный потенциал атмосферы дуги.
С увеличением основности шлака снижается количество неметаллических включений и кислорода в металле шва (рис. 7-22), повышаются его пластические свойства и стойкость против образования кристаллизационных трещин. На рис. 7-23 приведена зависимость ударной вязкости металла шва от основности шлака.
Благодаря указанным факторам электроды с рутилкарбонатным покрытием обеспечивают более высокое качество металла шва, чем электроды с рутилалюмосиликатным покрытием. Рутил-карбонатные покрытия имеют отечественные электроды марок

АНО-3, АНО-4, АНО-5, АНО-12, МР-1, МР-3; рутилалюмосили-катные покрытия — электроды АНО-1, ОЗС-3, ОЗС-4, ОЗС-6, ЦМ-9.
Металл, наплавленный электродами с рутиловым покрытием, по химическому составу соответствует полуспокойной или спокойной стали и содержит до 0,12% С; 0,5—0,8% Мп; 0,10— 0,30% Si; до 0,05% S и до 0,05% Р. Содержание газов в металле швов, выполненных электродами с рутиловым покрытием, обычно находится в следующих пределах; 0,05—0,10% кислорода, 0,015— 0,025% азота, 25—30 см3/100 г водорода.
Электроды с рутиловым покрытием обладают высокими сва-рочно-технологическими свойствами: обеспечивают отличное формирование швов с плавным переходом к основному металлу, малые потери металла от разбрызгивания, легкую отделимость шлаковой корки, стабильное горение дуги при сварке на переменном и постоянном токе любой полярности. Металл шва, сваренного электродами с рутиловым покрытием, мало склонен к образованию пор при колебаниях длины дуги, при сварке влажного и ржавого металла, при сварке по окисленным поверхностям. Причины образования пор при сварке электродами этого типа такие же, как и при сварке электродами с рудно-кислым покрытием. Стойкость металла швов против образования кристаллизационных трещин несколько выше, чем у электродов с рудно-кислым покрытием.
В зависимости от толщины покрытия электроды могут быть предназначены для сварки либо во всех пространственных положениях, либо только в нижнем положении; от толщины покрытия зависят и технологические свойства электродов. По технологическим свойствам и содержанию железного порошка в покрытии электроды условно могут быть разделены на три группы (табл, 7-19),
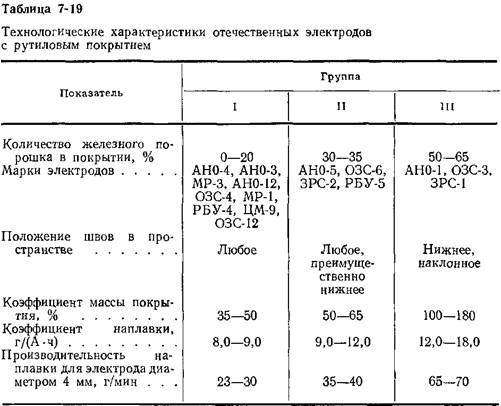
В покрытиях электродов первой группы железный порошок введен в небольших количествах (до 15—20%) с целью улучшения сварочно-технологических свойств электродов, а именно: устойчивости горения дуги, равномерного плавления покрытия, снижения разбрызгивания расплавленного металла и т. д. Производительность электродов при этом возрастает мало. Основное назначение электродов первой группы — сварка металлов средней толщины (3—12 мм) в монтажных и заводских условиях, где преобладают короткие и криволинейные швы, расположенные в различных пространственных положениях.
В покрытиях электродов второй группы железный порошок содержится в количестве 30—35%. Введение в покрытие такого количества железного порошка с одновременным увеличением толщины покрытия (до определенных пределов) позволяет не только улучшить сварочно-технологические свойства электродов, но и повысить их производительность. Электроды второй группы называют универсальными электродами повышенной производительности.
Этими электродами можно сваривать во всех пространственных положениях, но наиболее эффективно их применение в заводских условиях, где большинство швов сваривают в нижнем положении. Электроды второй группы следует применять при

сварке швов большой про тяженности с большим ка тетом при толщине основ ного металла 10—20 мм. Электроды третьей
группы (с высоким содержанием железного порошка) называют высокопроизводительными. Эти электроды пригодны для сварки конструкций только в нижнем или наклонном положениях. Рекомендуются главным образом для заводской сварки при наличии швов большой протяженности. В отличие от рудно-кислых рутиловые покрытия обеспечивают более благоприятные санитарно-гигиенические характеристики электродов. На рис. 7-24 приведены данные о выделении пыли и токсичных окислов марганца при сварке электродами с рути-ловым и рудно-кислым покрытиями различных марок.
По механическим свойствам металла шва и сварного соединения электроды с рутиловым покрытием чаще всего относятся к типам Э42-Э46 и предназначены для сварки ответственных конструкций из низкоуглеродистых и низколегированных сталей (табл. 7-20).
Благодаря высоким сварочно-технологическим свойствам, механическим свойствам металла шва и благоприятным санитарно-гигиеническим характеристикам электроды с рутиловым покрытием получили очень большое распространение в различных отраслях народного хозяйства. Широкое внедрение этих электродов взамен электродов с рудно-кислым покрытием позволило коренным

образом улучшить санитарно-гигиенические условия Труда сварщиков и рабочих смежных профессий и дало народному хозяйству большой экономический эффект.
|