Технология электрической сваркиШлаковая ванна
Шлаковой ванной называют объем жидкого шлака, в котором при сварке электрическая энергия преобразуется в тепловую. Вместе с тем шлаковая ванна защищает расплавленный металл от воздействия кислорода и азота воздуха, растворяет окислы и загрязнения на поверхности основного и электродного металлов и в некоторых случаях легирует металл шва. По химическому составу шлаковая ванна обычно представляет собой расплав различных окислов или солей.
В отличие от дугового разряда при электрошлаковых процессах нет явно выраженных приэлектродных областей. Ток переходит с электрода в шлаковую ванну сразу после того, как на его поверхности растворятся окислы. Обычно это происходит на глубине около 1 см от поверхности ванны. Еще несколькими миллиметрами глубже начинается плавление электрода. Оно заканчивается на глубине 20—30 мм в зависимости от скорости подачи электрода. Оплавляемый конец электрода все время сохраняет коническую форму, точнее форму параболоида вращения (рис. 2-7).
Электродный металл переносится в ванну каплями. Частота переноса капель возрастает с возрастанием скорости подачи электрода. При большой скорости подачи электрода, низком напряжении и малой глубине шлаковой ванны капли металла могут соединяться с металлической ванной раньше, чем отделятся от электрода. Такое металлическое соединение электрода с ванной существует очень короткое время; оно почти мгновенно разрушается под действием электродинамических усилий, возникающих в проводнике и резко увеличивающихся с возрастанием плотности тока. Однако вследствие большой частоты замыканий (несколько сотен в секунду) среднее время прохождения тока через металл может составлять значительную долю общего времени сварки. Это явление не носит характера короткого замыкания. Общая проводимость зоны сварки в момент замыкания возрастает всего в 1,5—1,7 раза. Мощность в зависимости от характеристики источника питания или изменяется незначительно, или несколько возрастает.
В отличие от дуговой сварки под флюсом при электрошлаковой сварке почти вся электрическая мощность передается шлаковой ванне, а от нее — электроду и основному металлу. Условием стабильности процесса является постоянство температуры шлаковой ванны, иначе говоря, равенство получаемой и отдаваемой ею теплоты. На рис. 2-8 показаны примерные зависимости выделяемой в шлаке и отдаваемой им мощности от средней температуры шлаковой ванны. При низких температурах кривая отдаваемой мощности всегда лежит выше кривой выделяемой мощности, так как теплоотдача происходит при всех температурах, превышающих температуру окружающей среды, а заметное выделение мощности в шлаке начинается при температуре, близкой к 1000° С. Характер кривой отдаваемой мощности зависит от геометрических размеров полости, в которой происходит сварка; глубины
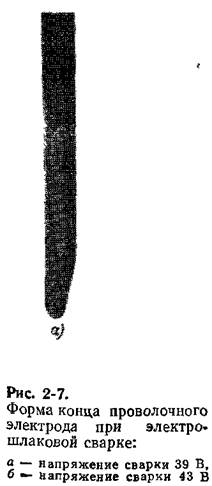
шлаковой ванны; коэффициентов теплопередачи от шлака к основному металлу и к охлаждающим устройствам; характера плавления основного металла; мощности, расходуемой на испарение летучих компонентов шлака; количества подаваемого в зону сварки присадочного металла и других факторов.
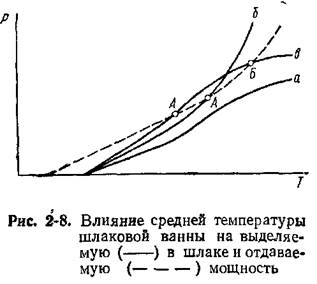
На характер кривой выделяемой мощности влияют зависимость электропроводности шлака от температуры, внешняя характеристика источника питания и глубина погружения электрода в шлак. В том случае, когда кривые выделяемой и отдаваемой мощности не пересекаются, процесс вообще невозможен (кривая а). Если кривые пересекаются в одной точке (кривая б), то процесс не может быть устойчивым: влево от точки пересечения (точка А) температура и мощность будут непрерывно падать, а вправо — расти. При наличии второй точки пересечения (точки Б на кривой а) процесс будет устойчивым.
Кривая б получается при жесткой характеристике источника питания и размерах межэлектродного пространства, мало или медленно изменяющихся с температурой ванны. Это бывает при большом сечении расплавляемого электрода, особенно когда оно соизмеримо с сечением образующегося шва. Чтобы получить кривую ву нужно либо уменьшить жесткость характеристики источника, либо изменить характер зависимости проводимости ванны от температуры.
С повышением температуры растет удельная электропроводность шлака, но уменьшается глубина погружения электрода, что снижает проводимость ванны. Этот фактор действует тем сильнее, чем меньше сечение плавящегося электрода, так как при малых сечениях электрода изменение линейных размеров больше при том же изменении количества расплавляемого металла. При малом сечении электрода изменения формы межэлектродного пространства достаточно для стабилизации температуры ванны Процесс идет устойчиво даже при совершенно жесткой характеристике источника питания и различных составах шлаковой ванны.
Вследствие вертикального положения оси шва поверхность металлической ванны оказывается расположенной ниже места плавления кромок (рис. 2-9). Расплавленный металл стекает вниз. Кромки 2 свободно омываются горячим шлаком 3 и интенсивно плавятся. Благодаря интенсивному перемешиванию шлака плавление кромок происходит на большем расстоянии от электрода 7, чем это возможно при дуговой сварке. Более раннему плавлению свариваемых кромок способствует также интенсивный подвод теплоты от металлической ванны 4, показанный на рис. 2-9
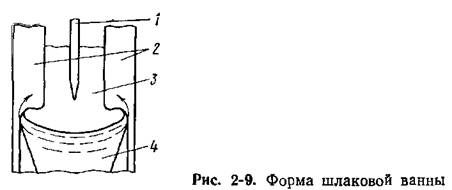
стрелками. В результате удаленный от кромки основной металл плавится несколько раньше, чем сама кромка.
Практическим следствием этих особенностей является малый расход флюса, составляющий, с учетом потерь на рассыпание, в среднем 5% массы наплавленного металла, и малый расход электрической энергии на 1 кг наплавленного металла — в 1,5— 2 раза меньше, чем при дуговой сварке. Еще более важным результатом этих особенностей является возможность осуществления однопроходной сварки металла толщиной до 150—200 мм на один электрод, а при большем числе электродов — металла практически неограниченной толщины.
При сварке проволокой значительная часть теплоты выделяется вследствие омического сопротивления электрода между местом токоподвода и концом электрода. При сварке плавящимся мундштуком или пластиной эта доля значительно меньше. Основная часть теплоты выделяется в сопротивлении растекания шлаковой ванны. При большой скорости подачи сварочной проволоки много теплоты может выделяться при кратковременных замыканиях электрода с ванной через капли жидкого металла.
Забиваем Сайты В ТОП КУВАЛДОЙ - Уникальные возможности от SeoHammer
Каждая ссылка анализируется по трем пакетам оценки: SEO, Трафик и SMM.
SeoHammer делает продвижение сайта прозрачным и простым занятием.
Ссылки, вечные ссылки, статьи, упоминания, пресс-релизы - используйте по максимуму потенциал SeoHammer для продвижения вашего сайта.
Что умеет делать SeoHammer
— Продвижение в один клик, интеллектуальный подбор запросов, покупка самых лучших ссылок с высокой степенью качества у лучших бирж ссылок.
— Регулярная проверка качества ссылок по более чем 100 показателям и ежедневный пересчет показателей качества проекта.
— Все известные форматы ссылок: арендные ссылки, вечные ссылки, публикации (упоминания, мнения, отзывы, статьи, пресс-релизы).
— SeoHammer покажет, где рост или падение, а также запросы, на которые нужно обратить внимание.
SeoHammer еще предоставляет технологию Буст, она ускоряет продвижение в десятки раз,
а первые результаты появляются уже в течение первых 7 дней.
Зарегистрироваться и Начать продвижение
Наилучшие условия для получения глубокой шлаковой ванны обеспечиваются при вертикальном положении оси шва. Поэтому при электрошлаковой сварке используют обычно принудительное формирование. Сущность принудительного формирования состоит в искусственном охлаждении свободной поверхности металлической ванны. На рис. 2-10, а показан теоретический случай, когда обмен теплоты через свободную поверхность металлической ванны отсутствует. Рис. 2-10, б соответствует наличию подогрева металлической ванны расплавленным шлаком, как это бывает при сварке под флюсом. Если изменить направление теплоотвода на обратное, как показано на рис. 2-10, в, то ванна примет чашеобразную форму. Такая форма позволяет производить сварку при вертикальном положении оси шва.
Охлаждение производится обычно с помощью медных пластин, в свою очередь охлаждаемых проточной водой. Для введения электрода в пространство между кромками необходимо, чтобы хотя бы с одной стороны охлаждающаяся поверхность передвигалась вверх вдоль шва по мере его образования. Такое скользящее устройство называется ползуном. Ползун является одно* временно устройством, удерживающим шлаковую ванну от вытекания.
Важнейшими требованиями к шлакам для электрошлаковой сварки являются высокая температура кипения и отсутствие газообразования при нагреве до высоких температур. Некоторые шлаки кипят спокойно, без бурного выделения газов. Такое кипение

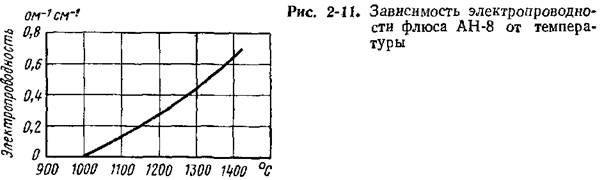
если оно не слишком интенсивно, не мешает процессу сварки, а, наоборот, служит хорошим регулятором температуры ванны, поглощая излишек энергии при повышении температуры. При прохождении электрического тока через шлак не происходит такого интенсивного выделения газов, сопровождающегося разбрызгиванием, как при дуговой сварке.
При установившемся электрошлаковом процессе разбрызгивания не происходит вовсе. Это позволяет вести сварку с открытой поверхностью шлаковой ванны. Подача флюса в ванну ограничивается очень небольшим количеством, равным количеству отлагающейся на поверхности шва шлаковой корки толщиной 1— 1,5 мм. Это составляет всего 2—3 % массы наплавленного металла. Благодаря малому количеству расплавляемого флюса хорошо используется электрическая энергия.
Поскольку основное назначение шлаков для электрошлаковой сварки — преобразование электрической энергии в тепловую, то и основной их характеристикой является электропроводность и ее зависимость от температуры. Электропроводность расплавленных шлаков резко повышается с ростом температуры, ниже определенной температуры они практически являются непроводниками (рис. 2-11). Это обстоятельство усложняет стабилизацию процесса.
Из химических веществ, устойчивых в жидком состоянии при температурах, превышающих температуру плавления сталей, наиболее стойкими являются различные соли, в первую очередь фториды и хлориды щелочных металлов. При температурах 1000—2000° С они дают расплавы, полностью диссоциированные на одно- и двухзарядные ионы. Такие расплавы при температурах плавления стали имеют проводимость порядка нескольких ом" хсм" обеспечивающую выделение достаточной для плавления черных металлов мощности при практически приемлемых напряжениях на электродах (порядка нескольких десятков вольт). Из однокомпонентных расплавов применяются фтористый кальций CaF2 для сварки сталей и фтористый натрий NaF для сварки и наплавки меди и ее сплавов.
Одним из недостатков чистого CaF2 является его высокая электропроводность, вследствие которой нужная температура ванны и мощность достигаются при напряжении на электродах ниже 30 В и сравнительно больших токах. Это требует повышения сечения токоподводящих проводов и токоведущих частей самого аппарата. Кроме того, расплав чистого фтористого кальция очень текуч, а это затрудняет удержание шлаковой ванны. Чаще применяются многокомпонентные шлаки, в состав которых входят CaO, MnO, CaF2 и другие соединения.
|