Технология электрической сваркиПлавление и перенос электродного металла при дуговой сварке
Характер плавления и переноса электродного металла оказывает большое влияние на производительность сварки, взаимодействие металла со шлаком и газами; от него зависят устойчивость горения дуги, потери металла, формирование шва и другие технологические факторы.
Плавление электрода. Плавление электрода происходит главным образом за счет тепловой энергии дуги. Основной характеристикой плавления электрода являются линейная или массовая скорости плавления, измеряемые длиной или массой расплавленного электрода (проволоки) в единицу времени. Скорость плавления зависит от состава сварочной проволоки, покрытия, флюса, защитного газа, режима сварки, плотности и полярности тока, вылета электрода и ряда других факторов. Но и для одних и тех же условий сварки скорость плавления электрода не остается постоянной, а может постепенно изменяться. Поэтому на практике используют в качестве характеристики среднюю скорость плавления электрода, которая обычно определяется за некоторый произвольный, но значительно превосходящий длительность периода капельного перехода промежуток времени.
Поскольку средняя скорость плавления сильно зависит от режима сварки, при оценке влияния различных факторов на плавление электрода иногда удобнее пользоваться удельным (отнесенным к единице тока) значением этой характеристики, получившим название коэффициента расплавления. Скорость плавления электрода Gp связана с коэффициентом расплавления ар выражением
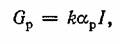
где k — коэффициент, зависящий от выбора единиц измерения.
Важнейшими показателями, характеризующими процесс плавления электрода, являются также коэффициент наплавки ссн и коэффициент потерь i|). Коэффициент наплавки, как и коэффициент расплавления, представляет собой удельное значение скорости
йаплавки. Скорость найЛавки бн связана с коэффиЦиён^бм й9-
плавки выражением
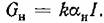

где gp и gn — соответственно массы расплавленного и наплавленного металла.
Выражение (2-14) справедливо лишь для электродов, не содержащих металлических присадок (железного порошка или ферросплавов) в покрытии.
При наличии металлических присадок в покрытии коэффициент "ф может получать отрицательные значения. В таких случаях он представляет собой разность между количеством потерянного металла и количеством металла, перешедшего из покрытия. Для электродов подобного типа суммарный коэффициент потерь можно определить из выражения

— масса
присадок металла из покрытия.
С помощью рассмотренных показателей можно определить такие характеристики, как выход наплавленного металла kc и выход годного металла k3.

Для электродов с металлическими присадками в покрытии этот показатель может быть значительно больше единицы (или больше 100%).
Выход годного металла k3 представляет собой отношение массы наплавленного металла к массе расплавленной части электрода:
части электрода; kn — коэффициент массы покрытия, представляющий собой отношение массы покрытия к массе покрытой части электродного стержня.
Скорость плавления электрода при всех способах дуговой сварки плавящиеся электродом возрастает с увеличением силы тока (рис. 2-23). В широком диапазоне режимов наблюдается пропорциональность между скоростью плавления электрода и силой сварочного тока. Однако в области малых и больших токов пропорциональность нарушается, что связано с изменением энергетических характеристик дуги, размера активных пятен и плотностей тока в них, нагревом электрода током. Увеличение скорости плавления электрода при больших плотностях тока вызвано также подогревом стержня электрода проходящим током. Нагрев электрода на вылете пропорционален квадрату силы тока, сопротивлению проволоки и длине вылета.
Скорость плавления электрода в основном определяется условиями выделения и передачи теплоты в анодной и катодной областях и зависит от полярности тока. При сварке на обратной полярности коэффициент расплавления практически не зависит от состава проволоки, покрытия, флюса или защитного газа. При сварке же на прямой полярности коэффициент расплавления изменяется в широких пределах в зависимости от состава и состояния поверхности проволоки, составов покрытия, флюса или защитного газа (рис. 2-24). Соответственно изменяется и напряжение дуги. В практике обычно пользуются значением номинального напряжения дуги UH — напряжения, характерного для данной марки электрода, проволоки, флюса или защитного газа при рабочей длине дуги.
Скорость плавления электрода можно регулировать, изменяя силу тока или величину катодного падения напряжения. Возможность увеличения скорости плавления покрытых электродов за
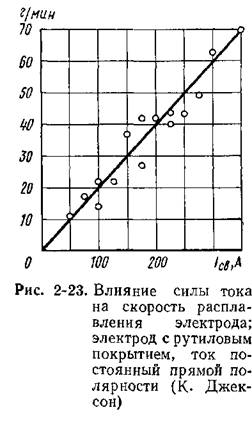
счет увеличения силы тока ограничена в связи с перегревом стержня электрода. При автоматических и полуавтоматических способах сварки это
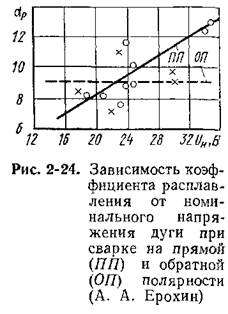
ограничение менее существенно из-за малых вылетов проволоки.
Введение в проволоку, покрытие или флюс веществ, повышающих катодное падение напряжения (а следовательно, и номинальное напряжение дуги), способствует повышению скорости плавления проволоки на прямой полярности. Изменение состава защитного газа оказывает сравнительно небольшое влияние на скорость плавления проволоки. Нанесение на сварочную проволоку небольших количеств солей щелочных или щелочноземельных металлов резко понижает скорость плавления катода. Это явление иногда используется для так называемого активирования проволоки с целью замедления скорости плавления и получения мелкокапельного переноса металла на прямой полярности.
При сварке покрытыми электродами скорость плавления электрода зависит и от толщины покрытия. Утолщение покрытия приводит к дополнительным затратам теплоты на его плавление, а также к увеличению мощности, выделяемой в столбе дуги. У электродов без металлических добавок в покрытии увеличение толщины покрытия ведет к бесполезным затратам на его плавление. Вводя в покрытие металлические добавки или железный порошок, можно существенно увеличить скорость наплавки. Увеличение толщины покрытия и повышение содержания в нем железного порошка позволяют значительно повысить плотность тока без опасения перегрева стержня электрода. Все эти факторы способствуют увеличению производительности сварки.
|