Технология электрической сваркиТепловые процессы при сварке плавлением
Под тепловыми процессами при сварке принято подразумевать повышение температуры свариваемых изделий (и присадочного материала) под влиянием источников сварочного нагрева, распространение теплоты по изделию и отвод ее в окружающую среду. Изменение температуры определяет, помимо явлений плавления и кристаллизации металла, прохождение целого ряда сопутствующих процессов в материале изделия — структурные превращения, объемные изменения, упруго-пластические деформации и т. д. Эти процессы оказывают значительное влияние на качество сварного соединения и всей конструкции в целом.
Значительные заслуги в разработке фундаментальных основ теории тепловых процессов при сварке принадлежат главным образом советским ученым и в первую очередь академику Н. Н. Ры-
калину.
Подводимая к свариваемому изделию (присадочному металлу) теплота характеризуется величиной тепловой мощности и законом распределения ее в пространстве и времени. Эти характеристики во многом зависят от способа и условий сварки, формы соединения и других факторов. Рассмотрим эти вопросы применительно к наиболее типичным способам сварки плавлением.

где U, I — соответственно средние значения падения напряжения на дуге и силы тока в цепи; ср — коэффициент мощности или форм-фактор. Наиболее вероятные значения коэффициента ср находятся в пределах 0,8—-0,95.
Часть теплоты сварочной дуги бесполезно теряется в окружающей среде, а большая часть идет на нагрев и плавление присадочного и основного металлов, электродного покрытия либо флюса и на химические реакции в зоне сварки. Величина тепловой мощности дуги, теряемой в окружающее пространство, как и величина qp, зависит от многих трудноучитываемых параметров режима сварки. В связи с этим значения основных составляющих теплового баланса дуги принято определять, пользуясь понятием эффективного к. п. д., например, эффективный к. п. д. нагрева изделия дугой т]и, нагрева электрода дугой т]э, нагрева флюса дугой т]ф и т. д.
Величины эффективных к. п. д. определяются обычно экспериментальным путем и представляют собой отношение тепловой мощности данной статьи теплового баланса к тепловому эквиваленту электрической энергии дуги. Калориметрическими опытами установлено, что эффективный к. п. д. процесса нагрева изделия сварочной дугой зависит главным образом от условий ее горения (табл. 2-3).
Коэффициент т|и уменьшается с увеличением длины дуги и повышается с увеличением скорости сварки и углублением дуги в сварочную ванну. На величину т]и влияет и форма детали в зоне сварки — так называемый геометрический фактор. Например, при наплавке валика открытой дугой в разделку шва значения г]и на 5—10% выше, чем при наплавке на плоскость. Повышение

при углублении дуги в сварочную ванну связано с улучшением теплообмена между дугой и изделием, а также с уменьшением потерь теплоты с разбрызгивающимся электродным материалом.
Опыт показывает, что в дугах, мало погруженных в металл изделия, скорость плавления электродов не зависит от длины дуги. Это означает, что плавление происходит главным образом за счет энергии, получаемой электродами от примыкающих к ним областей дуги и потенциальной энергии электронов. В этих случаях к. п. д. дуги приближенно может быть найден из соотношения

— падения напряжения в катодной области, анод-
поэтому их к. п. д.

Расчет по уравнению (2-10) для большинства открытых дуг длиной 3—6 мм дает к. п. д. 50—65%. При полном погружении дуги, когда потери излучения столба возможны только через зазоры между поверхностью ванны и стержневым электродом, к. п. д. по уравнению (2-11) оценивается примерно в 75—85%.
Теплота, затрачиваемая дугой на нагрев электрода, флюса или защитного газа (жидкости), также во многом зависит от характеристики дуги, условий и режима сварки. В табл. 2-3 приведены отдельные данные для этих величин, дающие представление о количестве теплоты, расходуемой дугой на нагрев электрода, флюса и защитного газа.
Характерно, что сумма всех эффективных коэффициентов (с учетом т)и), как правило, заметно больше единицы (за исключением сварки неплавящимся электродом). Это связано с наличием

непрерывного теплообмена между отдельными потребителями тепловой энергии сварочной дуги. Например, для случая сварки плавящимся электродом под флюсом теплота, затраченная на нагрев электрода и флюса, участвует затем в нагреве основного металла, что в определенной степени оказывает влияние на характер ввода теплоты сварочной дуги в изделие. Согласно наиболее распространенной схеме, теплота непосредственно передается изделию через эффективное пятно дуги, конвективными потоками плазмы вдоль столба дуги и радиационным излучением. Распределение удельного теплового потока q таких дуг приближенно можно выразить кривой Гаусса (нормальным законом распределения):

где qm — наибольший тепловой поток в центре пятна, Вт/см2; k— коэффициент сосредоточенности источника, 1/см2; г— радиальное расстояние от оси дуги, см.
Наиболее близко такой схеме соответствуют дуги сравнительно небольшой мощности при сварке покрытыми электродами с небольшим количеством шлакообразующих в покрытии, а также дуги с неплавящимся электродом, горящие в среде аргона. При сварке мощными дугами электродами с качественным покрытием либо под флюсом значительная часть теплоты вводится в изделие через присадочный материал, шлак или флюс (см, рис, 2-14), что приводит к существенно более сложному распределению теплового потока.
Электрошлаковая сварка. Выделение теплоты при электрошлаковом процессе происходит в результате прохождения электрического тока через расплавленный шлак. Выделяемое в шлаковой ванне в единицу времени количество теплоты qQ пропорционально тепловому эквиваленту подводимой электрической энергии. Другие источники теплоты столь невелики, что ими можно пренебречь. Эффективная мощность источника теплоты при электрошлаковой сварке всегда меньше q0, так как она не включает часть теплоты, теряемой шлаковой ванной на теплоотдачу в окружающую среду и в формирующее устройство (рис. 2-15). Теплота поступает в

изделие с расплавленным электродным металлом и в результате конвективного теплообмена между шлаковой ванной и поверхностью основного металла.
Забиваем Сайты В ТОП КУВАЛДОЙ - Уникальные возможности от SeoHammer
Каждая ссылка анализируется по трем пакетам оценки: SEO, Трафик и SMM.
SeoHammer делает продвижение сайта прозрачным и простым занятием.
Ссылки, вечные ссылки, статьи, упоминания, пресс-релизы - используйте по максимуму потенциал SeoHammer для продвижения вашего сайта.
Что умеет делать SeoHammer
— Продвижение в один клик, интеллектуальный подбор запросов, покупка самых лучших ссылок с высокой степенью качества у лучших бирж ссылок.
— Регулярная проверка качества ссылок по более чем 100 показателям и ежедневный пересчет показателей качества проекта.
— Все известные форматы ссылок: арендные ссылки, вечные ссылки, публикации (упоминания, мнения, отзывы, статьи, пресс-релизы).
— SeoHammer покажет, где рост или падение, а также запросы, на которые нужно обратить внимание.
SeoHammer еще предоставляет технологию Буст, она ускоряет продвижение в десятки раз,
а первые результаты появляются уже в течение первых 7 дней.
Зарегистрироваться и Начать продвижение
Перенос теплоты в ванне приближенно можно представить следующей схемой. Сварочный ток в основном проходит через зону шлаковой ванны, ограниченную усеченным конусом, верхнее основание которого имеет диаметр электрода (активный конус шлаковой ванны). Максимальная температура этой зоны более 2000° С. По мере приближения к металлической ванне температура активной зоны несколько снижается вследствие уменьшения плотности тока и наличия интенсивных конвективных потоков.
Металлическая ванна аккумулирует значительную долю теплоты, выделяемой в шлаковой ванне. Таким образом, по сравнению с дуговой сваркой при электрошлаковой сварке в передаче теплоты от источника нагрева к основному металлу участвуют значительные массы жидкой среды (расплавленного шлака и металла), распределение теплоты в которой в большой степени определяется конвективными потоками.

Электроннолучевая сварка. Энергия или мощность электронного луча, выходящего из электромагнитной системы WCB, может быть представлена в виде суммы
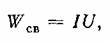
где / — сила тока пучка электронов, мА; U — ускоряющее напряжение, кВ.
Эффективность нагрева изделия существенным образом зависит от уноса энергии, обусловленного испарением материала изделия, отражением излучения в окружающую среду, вторичной и термоэлектронной эмиссией электронов, а также электромагнитным излучением. Электроннолучевая сварка характеризуется весьма малыми размерами пятна нагрева (до 10~5 мм2), значительно меньшими, чем у сварочной дуги (около 1 мм3). С увеличением плотности подводимой энергии возрастают потери теплоты, связанные с испарением металла в зоне нагрева. Это определяет границу предельной интенсивности для электронного луча при сварке плавлением примерно в пределах 103—104 кВт/см3.
Характерным для электроннолучевой сварки является глубинный подвод тепловой энергии к свариваемому изделию. Последнее объясняется свойством электронов луча проникать на определенную глубину (пробег электрона), теряя энергию на всем пути торможения. Значительное влияние на глубинный характер источника нагрева при электроннолучевой сварке оказывает давление луча, способствующее вытеснению жидкого металла из зоны активного пятна. Давление луча на жидкий металл в 5—10 раз превышает давление дуги при аргоно-дуговой сварке в сходных условиях и обусловливается испарением металла.
Сварка лазерным лучом. Эффективный к. п. д. нагрева изделия при лазерной сварке весьма невелик, что вызвано главным образом низким к. п. д. лампы накачки и кристалла рубина. Баланс энергии лазера при сварке ясен из рис. 2-16.
Рассмотренные выше источники теплоты являются наиболее характерными, однако далеко не исчерпывают возможных типов источников, используемых при сварке плавлением. При сварке плавлением теплота не только подводится к изделию, но и непрерывно отводится от него. Это происходит за счет естественных и искусственных стоков теплоты. Естественными являются стоки теплоты, связанные с излучением и конвекцией от нагретой поверхности изделия в окружающую среду. Искусственные стоки осуществляются путем специальных технологических мер, заключающихся, например, в создании интенсивного конвективного

теплообмена между определенными участками поверхности изделия и охлаждающей жидкой либо газообразной средой.
При теплообмене излучением теплота переносится между удаленными друг от друга нагреваемой деталью ?и окружающими предметами посредством электромагнитного излучения в соответствии с законом Стефана-Больцмана, т. е. тепловой поток пропорционален разности четвертых степеней абсолютных температур поверхностей, участвующих в теплообмене. При конвективном теплообмене теплота с поверхности изделия уносится жидкостью или газом, движение которых создается принудительно, а при естественной конвекции это движение обусловлено различием в плотности нагретых и ненагретых объемов.
Величину теплового потока конвективного теплообмена qK между поверхностью тела с температурой Т и охлаждающей средой с температурой Тс оценивают по правилу Ньютона:

где ак— коэффициент конвективной теплоотдачи, определяемый экспериментально.
В обычных условиях сварки при отсутствии заметных воздушных потоков величина ак составляет примерно 0,002— 0,005 Вт/см2° С. Выражение (2-12) часто используют и для описания общей суммарной теплоотдачи с поверхности изделия путем лучеиспускания и конвекции. Это возможно, поскольку погрешность от такого описания существенно проявляется только в зоне, нагретой выше 700—800Q С, где радиационные тепловые потоки значительно превышают конвективные. При температурах поверхности 400° С и ниже роль лучеиспускания в теплоотдаче по сравнению с конвекцией невелика.
Распространение теплоты в изделии происходит преимущественно по законам теплопроводности, хотя определенное влияние на перенос теплоты вблизи сварочной ванны оказывают конвективные потоки в жидком металле. Их роль тем сильнее, чем больше объем сварочной ванны.

На основе указанных принципов местного и временного влияния можно считать, что особенности тепло- и массопереноса в жидком металле сварочной ванны, так же как и кратковременные отклонения эффективной мощности источника от среднего значения, оказывают ограниченное влияние на температурное поле и только в основном вблизи мгновенного положения сварочной ванны.
Анализ температурного поля в изделии при движении источника сварочного нагрева обычно принято производить в системе пространственных координат, перемещающейся с источником сварочного нагрева. Это удобно, поскольку через некоторый период времени от начала движения при постоянной скорости и эффективной тепловой мощности сварки наступает так называемое квазистационарное состояние, когда подвижное температурное поле практически не меняется,
Длительность наступления квазистационарного состояния (длительность периода теплонасыщения) зависит от скорости сварки, расстояния рассматриваемого объема от источника нагрева и интенсивности отвода теплоты от него. Период теплонасыщения сокращается с уменьшением расстояния от источника нагрева, увеличением скорости сварки и теплопроводности материала, ростом массы изделия и интенсивности отдачи теплоты в окружающую среду, а также с уменьшением теплоемкости материала. На рис. 2-17 и 2-18 приведены изолинии температурного поля предельного (квазистационарного) состояния в тонкой пластине в зависимости от режима сварки (рис. 2-17) и теплофизи-ческих свойств материала (рис. 2-18).
Сервис онлайн-записи на собственном Telegram-боте
Попробуйте сервис онлайн-записи VisitTime на основе вашего собственного Telegram-бота:
— Разгрузит мастера, специалиста или компанию;
— Позволит гибко управлять расписанием и загрузкой;
— Разошлет оповещения о новых услугах или акциях;
— Позволит принять оплату на карту/кошелек/счет;
— Позволит записываться на групповые и персональные посещения;
— Поможет получить от клиента отзывы о визите к вам;
— Включает в себя сервис чаевых.
Для новых пользователей первый месяц бесплатно.
Зарегистрироваться в сервисе
Результаты исследования такого типа данных показывают следующее. При постоянной эффективной мощности соответствующие определенным температурам изотермы уменьшаются по длине и ширине примерно пропорционально увеличению скорости сварки v. С возрастанием эффективной мощности источника q нагретые выше определенной температуры области увеличиваются быстрее по длине, чем по ширине. Однако увеличение по ширине опережает рост величин q. Одновременное увеличение q и v при постоянной погонной энергии q/v сварки приводит в основном к увеличению длины изотерм. Ширина изотерм также увеличивается, но стремится к определенному пределу. Увеличение

Рис. 2-17. Влияние режима сварки на температурное поле квазистационарного состояния в стальной пластине толщиной 1 см; К = 0,38 Вт/см, су = 4,8 Дж/см3-град, а = 0,08 см2/с
а — изменение скорости сварки у;
б — изменение мощности источника теплоты q,
в — изменение мощности н скорости при q/v = const
теплопроводности материала, при прочих равных условиях, способствует заметному укорочению изотерм и некоторому их сужению. Уменьшение теплоемкости металла су оказывает примерно такое же влияние, как и уменьшение скорости сварки.
Для массивных тел влияние перечисленных параметров режима сварки и свойств материала на температурное поле квазистационарного состояния качественно такое же, как и при сварке пластин. Однако, в отличие от сварки пластин, изменение скорости сварки в основном влияет только на ширину изотерм, а не на их длину.
Термический цикл. Изменение температуры данной точки тела во времени называется термическим циклом. При однопроходной сварке (наплавке) имеет место простой термический цикл,
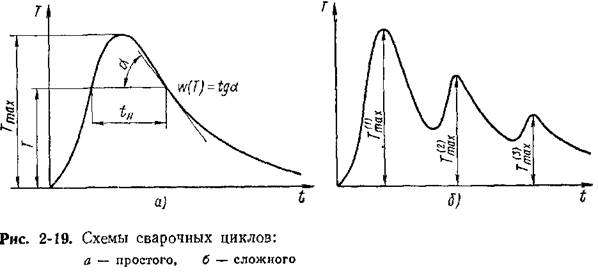
показанный на рис. 2-19, а. При многопроходной сварке термический цикл сложный (рис. 2-19, б). Основными параметрами простого термического цикла являются максимальная температура, скорость нагрева и скорость охлаждения, а также длительность пребывания материала выше заданной температуры. Эти характеристики зависят от режима сварки, теплофизических свойств материала, конфигурации изделия, условий его охлаждения, температуры предварительного подогрева.
Заметное влияние на термические циклы металла шва и околошовной зоны оказывает также и способ сварки, особенно, если сравниваются электрошлаковая и дуговая сварка или же сварка электронным лучом. На рис. 2-20 приведены характерные термические циклы для околошовной зоны с максимальной температурой нагрева 1300° С при сварке стального изделия. Кривая / относится к однопроходной электрошлаковой сварке пластин толщиной 100 мм на режиме /св = 450 A, U = 38—40 В, v = 0,7 м/ч;

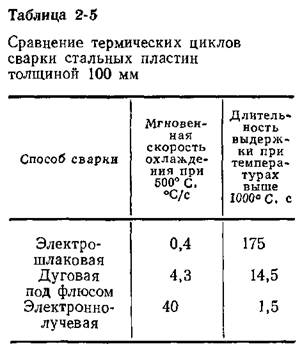
кривая 2 соответствует электродуговой сварке под флюсом стальной пластины толщиной 12 мм на режиме /св = 730 А, U = 46 В, v = 40,5 м/ч (сварка без разделки кромок с двух сторон); кривая 3 соответствует электроннолучевой сварке такой же пластины на режиме /С8 = 250 мА, U = 30 кВ; v = = 24 м/ч. В табл. 2-5 приведены данные о мгновенных скоростях охлаждения при температуре 500° С и длительностях выдержки металла (в рассматриваемом участке околошовной зоны Tfflax = 1300° С) при температурах выше 1000° С для указанных способов сварки.
Представление о влиянии теплофизических свойств материала и массивности изделия на температурные циклы в околошовной зоне дают кривые на рис. 2-21, а и б, относящиеся соответственно к однопроходной дуговой сварке тонких пластин (б = 12 мм) и многослойной дуговой сварке толстых пластин (б = 100 мм) из перлитной (кривая /) и аустенитной (кривая 2) сталей примерно на одном и том же тепловом режиме, характеризуемом величиной эффективной тепловой энергии q = 4050 кал/с и скоростью сварки v = 16 м/ч.
Из этих данных следует, что снижение теплопроводности материала уменьшает скорость изменения температуры точек околошовной зоны как на стадии нагрева, так и особенно на стадии охлаждения.
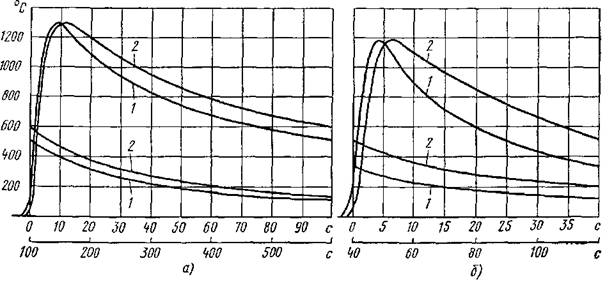
Рис. 2-21. Сопоставление термических циклов точек околошовной зоны при однопроходной сварке тонких пластин (а) и многопроходной сварке толстых пластин (б) из перлитной стали (1) и аустенитной стали (2)
Этот эффект несколько повышается с увеличением толщины (массивности) свариваемых изделий. Значительное влияние на температурные циклы точек околошовной зоны при одинаковом режиме сварки оказывает массивность изделия.
Широкое применение для оценки основных параметров термического цикла точек околошовной зоны получили расчетные методы теории тепловых процессов при сварке. Подробное изложение этих методов дано в специальной литературе. Ниже приведены расчетные зависимости для двух характерных случаев сварочного нагрева: тонкой пластины и массивного тела.
Тонкая пластина. Максимальные температуры Ттах в околошовной зоне на расстоянии у от центра шва могут быть приближенно оценены с помощью следующей зависимости:

где Т0 — начальная температура пластины; qiv — эффективная погонная энергия; у — объемная теплоемкость; б — толщина пластины; X — теплопроводность пластины; a —- коэффициент поверхностной теплоотдачи.
Из рис. 2-24 следует, что при малых произведениях ay максимальная температура прямо пропорциональна удельным тепло-вложениям q/v8 и обратно пропорциональна теплоемкости и расстоянию от оси шва. Мгновенная скорость охлаждения металла шва и прилегающей околошовной зоны при данной температуре Т

Длительность пребывания металла шва выше заданной температуры Т приближенно можно оценить из выражения

можно

(использована принятая в теории тепловых процессов индексация, при которой индекс 1 относится к стержням, 2 — к пластине, 3 — к массивному изделию).
Массивное тело. Рассмотрим полубесконечное тело (z > 0). Максимальные температуры в околошовной зоне на расстояния

от оси шва на поверхности тела (z = 0) приближенно можно определить, используя зависимость

В отличие от тонкой пластины в случае массивного тела максимальные температуры обратно пропорциональны квадрату расстояния от оси шва. Мгновенная скорость охлаждения металла шва и прилегающей околошовной зоны при температуре Т

т. е. в сходных условиях скорости охлаждения в массивном теле превышают скорости охлаждения в тонкой пластине при температуре Т в п раз, где

Длительность пребывания металла шва выше заданной температуры определяют из выражения, аналогичного зависимости (2-13):

раз более короткое, чем для тонких пластин
в сходных условиях.
время tH можно оценить по
номограмме на рис. 2-22, где приведено значение безразмерного
в зависимости от безразмерной температуры:

При многослойной сварке и*Ли наплавке Поверхностей смежными валиками тепловые воздействия отдельных слоев (соседних валиков) складываются и создают сложный термический цикл для точек околошовной зоны. Режим такой сварки является более гибким, поскольку он содержит большее число независимых параметров. Например, при многослойной наплавке режим содержит три независимых параметра, варьируя которыми, можно регулировать термические циклы в широких пределах. Такими параметрами являются погонная энергия отдельных слоев, длина участка и температура дополнительного подогрева.
|