Практическая вибродиагностика и монтиторингНагруженностъ деталей оборудования.
Нагрузки бывают нескольких видов: статические, динамические (переменные и ударные), циклические.
Статические нагрузки могут оказывать влияние на вибрации в оборудовании, главным образом в тех случаях, когда они вызывают изменение геометрической формы деталей, например кинематических пар. Кроме того, под действием статических нагрузок могут изменяться частоты собственных колебаний деталей, вследствие увеличения жесткости, например, под действием центробежных сил на диски и лопатки турбомашин. При действии достаточно высоких статических нагрузок в течение длительного времени явления ползучести материала могут привести к изменению геометрической формы деталей и появлению трещин.
Циклические нагрузки не вызывают вибраций оборудования, но приводят к явлениям усталости металла, что в свою очередь может оказать влияние на вибрацию.
Динамические нагрузки — основная причина колебания деталей агрегатов и их динамической напряженности, приводящей к усталостным поломкам.
Усталость.
Существуют несколько видов усталостных разрушений деталей: типичная усталость по действием переменных напряжений происходит из-за развития трещины, распространяющейся в материале по экспоненциальному закону; контактно-усталостные разрушения (питтинг, шелушение, усталостное выкрашивание контактных пар), начинающиеся с зарождения язвины или отдельного очага усталостного разрушения и, затем, с увеличением числа язвин относительно быстрого разрушения; коррозионно-усталостные разрушения деталей начинаются с очага коррозии (например, подверженных воздействиям агрессивных газов), служащего началом трещин, после заполнения которых продуктами коррозии происходит коррозионное растрескивание и разрушение деталей; термическая усталость на начальной стадии сопровождается слабым изменением геометрической формы тела вследствие образования сетки мелких трещин, затем магистральных трещин, приводящих к разрушению под действием динамических напряжений.
Под действием переменной нагрузки усталостная долговечность имеет обратно-степенную зависимость от ее значения с показателем степени порядка восьми и более в зависимости от материала.
Связь усталости и вибрации.
Вибрация вызывает усталостные разрушения деталей, действуя как переменная нагрузка. При появлении усталостных трещин изменяются собственные частоты колебаний деталей вследствие изменения их жесткости и могут изменяться демпфирование и характер колебаний (например, начинают проявляться эффекты нелинейности), что может вызвать изменение характера вибрации данной детали.
Характер изменений при усталостных процессах таков, что существует инкубационный, обычно длительный, период медленного накопления повреждений с постоянной скоростью, после которого происходит резкое увеличение скорости накопления повреждений. Такому закону очевидно должно следовать и изменение интенсивности вибрации, связанной с явлениями усталости. Однако при этом следует учитывать возможное изменение частот и форм колебаний вибрирующих деталей — возможны резкие изменения интенсивности колебаний деталей, вошедших в резонанс. Для нормально работающих деталей (исправное состояние) в инкубационном периоде развития усталостных дефектов изменение вибрации происходит с постоянной скоростью (при этом возможно случайное медленное флуктуирующее изменение интенсивности). На стадии быстрого разрушения увеличивается частота случайных флуктуации и их размах (дисперсия), т.к. увеличивается скорость случайных изменений.
Закономерности ползучести.
В процессе ползучести выделяют три периода: сначала постепенное уменьшение скорости пластической деформации, затем процесс протекает с минимальной постоянной скоростью, причем с ростом напряжения и температуры скорость пластической деформации растет, и при этом продолжительность данного периода с точки зрения эксплуатации агрегата уменьшается, и, наконец, скорость деформации нарастает, пока не наступит разрушение.
Остаточная деформация.
Нагрузки, вызывающие напряжения, которые превышают предел упругости, могут привести к остаточной деформации и появлению трещин. Остаточные деформации изменяют геометрическую форму и размеры деталей, что влияет на вибрационные процессы, генерируемые взаимодействием деталей (кинематических пар).
Износ.
Возможны несколько видов износа, которые появляются в связи с одним или несколькими следующими процессами: микросрезанием, пластической или упругой деформацией, возникающей вследствие высоких местных напряжений, поверхностной усталостью при повторяющихся упругих деформациях поверхности, местным перегревом, окислением, забиванием микротрещин смазкой, что является причиной возрастания давления, которое приводит к повреждению поверхностного слоя. Эти процессы могут происходить одновременно и приводить к ниже перечисленным видам износа.
Абразивный износ. Возникает вследствие истирания трущихся поверхностей и прямо пропорционален удельному давлению на трущиеся поверхности и пути скольжения. Пример — износ подшипников. Истирание трущихся поверхностей, разделенных смазкой вызывает струйный износ, а контактирующих (например, при задеваниях) фрикционный.
Заедание. Возникает вследствие контакта поверхностей в условиях разрушения масляной пленки. Различают следующие стадии этого процесса: увеличение коэффициента трения из —з а нарушения режима смазки, резкий нагрев, разрушение поверхностного слоя, сопровождающееся свариванием металла двух поверхностей. Наиболее часто встречается в зубчатых муфтах и зацеплениях, а также поршневых агрегатах.
Усталостный износ (питтинг). Возникает вследствие усталости поверхностного слоя и при относительном скольжении поверхностей и вследствие микрошероховатостей. Наиболее часто встречается в зубчатых парах и подшипниках качения.
Коррозионный износ. Возникает вследствие взаимодействия деталей агрегата с агрессивной средой.
Кавитационная эрозия. Возникает вследствие локальных гидравлических ударов жидкости в зоне кавитации.
В процессе износа выделяют три стадии:
Забиваем Сайты В ТОП КУВАЛДОЙ - Уникальные возможности от SeoHammer
Каждая ссылка анализируется по трем пакетам оценки: SEO, Трафик и SMM.
SeoHammer делает продвижение сайта прозрачным и простым занятием.
Ссылки, вечные ссылки, статьи, упоминания, пресс-релизы - используйте по максимуму потенциал SeoHammer для продвижения вашего сайта.
Что умеет делать SeoHammer
— Продвижение в один клик, интеллектуальный подбор запросов, покупка самых лучших ссылок с высокой степенью качества у лучших бирж ссылок.
— Регулярная проверка качества ссылок по более чем 100 показателям и ежедневный пересчет показателей качества проекта.
— Все известные форматы ссылок: арендные ссылки, вечные ссылки, публикации (упоминания, мнения, отзывы, статьи, пресс-релизы).
— SeoHammer покажет, где рост или падение, а также запросы, на которые нужно обратить внимание.
SeoHammer еще предоставляет технологию Буст, она ускоряет продвижение в десятки раз,
а первые результаты появляются уже в течение первых 7 дней.
Зарегистрироваться и Начать продвижение
приработка, когда изменяется микро- и макроструктура поверхностей и имеет место уменьшение скорости износа;
нормальный износ, когда можно принять линейную связь между значением износа и временем;
прогрессивный износ, когда имеет место возрастание скорости износа.
Основными факторами, влияющими на значение нормального износа, являются удельное давление и относительная скорость движения трущихся деталей.
Износ деталей кинематических пар приводит к увеличению зазоров в парах, что усиливает проявление динамических сил взаимодействия деталей, приобретающего в некоторых случаях ударный характер, и обогащение вибросигнала шумовыми и импульсными составляющими. Износ может также изменить жесткостные характеристики системы, что влияет на частоты и формы колебаний.
Отказы из-за несовершенства изготовления и сборки оборудования.
Причинами отказов могут быть как эксплуатационные факторы, так и несовершенство изготовления и сборки оборудования. Эти причины весьма многообразны.
Причины отказов, закладываемые при проектировании машины, могут быть следующими: неудачный выбор формы деталей, например, с концентраторами напряжений и резким изменением сечений; неудачный выбор материалов и их сочетаний; недооценка нагрузок и действующих сил; неучет их возможных изменений в процессе эксплуатации машины и т. д.
Причинами отказов, закладываемыми при изготовлении машины, могут быть, например, неудачные допуски, использование бракованных деталей и материалов, нарушения технологии изготовления, неполнота контроля.
Нарушение технологии в процессе сборки — частая причина отказов, например, из-за неправильно установленных зазоров, пятна контакта, нарушения посадок, ослабления затяжки и др.
Другая частая причина — изменения конструкции или технологии, влияние которых на надежность машины трудно определяется при разработке и внедрении и проявляется в ходе эксплуатации машины.
В машинах протекают различные, связанные с их функционированием, динамические процессы, происходящие в различных средах: газовых, жидкостных, воздушных и т. д. Большинство этих процессов оказывают динамическое воздействие на элементы конструкции и вызывают их колебания. Некоторые динамические процессы (вибрационное горение, кавитация и др.) вызывают разрушение деталей машин. В диагностическом плане динамические процессы могут быть связаны с колебаниями элементов конструкции и как возбуждающие вибрацию, и как изменяющие ее.
Итак, в процессе эксплуатации структурные параметры оборудования изменяются, упорядоченность системы в целом и ее функциональные качества ухудшаются, деградируют. Для того чтобы измерить степень этой деградации в данный момент и прогнозировать ее на ближайшее время, необходимо знать закономерность изменений структурных параметров под воздействием типичных эксплуатационных факторов. Такими изменениями структурных параметров механизмов являются изменения, приводящие к постепенному или внезапному отказу механизма.
Неисправности элементов конструкции механизма, развитие которых в процессе эксплуатации до критического уровня, т. е. до наступления отказа, не может быть зарегистрировано и проконтролировано средствами диагностирования, условно называются неисправностями, вызывающими внезапный отказ. Как говорилось ранее, такого рода отказы возникают, например, при статическом разрушении от действия мгновенно возникшей нагрузки, превышающей прочность элемента, при усталостном разрушении, возникающем в результате производственных дефектов (трещина, не снятые напряжения). Внезапный характер возникновения таких изменений затрудняет их индивидуальное прогнозирование. Неисправности элементов конструкции механизма, возникновение и развитие которых может быть зарегистрировано на ранней стадии возникновения и проконтролировано до критического уровня, называются неисправностями, вызывающими постепенный отказ. Такого рода отказы являются следствием естественного износа, в результате чего происходит постепенное, монотонное изменение структурных параметров. При этом износ может быть прогрессирующим, ускоряющимся, в случае жесткого сопряжения элементов, либо замедляющимся в случае упругих сопряжений.
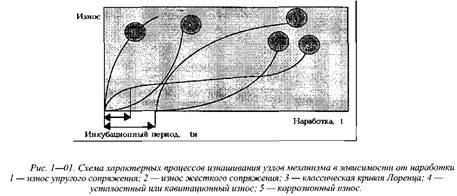
А нализируя графики, приведенные на рис. 1 — 01, можно заметить некоторую общность кривых и возможность с достаточной точностью их описания функцией вида:


— наработка.
В настоящее время показатель а экспериментально определен для многих
характерных объектов диагностирования. Например, для. и зменения теплового зазора клапана двигателя а= 1,1; для износа зубьев шестерен а — 1.5 и т. д.
В реальных условиях имеет место одновременное существование всех перечисленных типов деградации узлов механизма. Для того чтобы разработать метод и технологию диагностирования какого —л ибо объекта, необходимо знать закономерности изменения виброакустических характеристик со временем наработки.
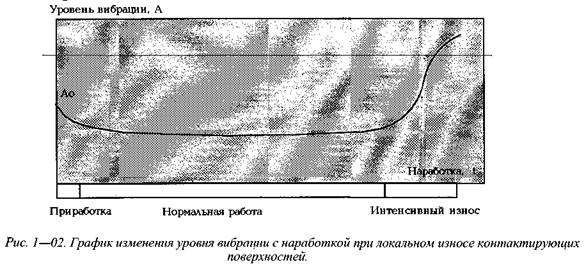
Как правило, эти закономерности не совпадают с изображенными на рис. 1 — 01, например, локальный износ контактирующих поверхностей вызывает сначала падение уровня вибрации (этап приработки), затем этот уровень практически остается неизменным на достаточно большом интервале времени (нормальная работа), и только на третьем этапе (интенсивный износ) наработки уровень начинает расти по экспоненте до момента отказа (рис. 1 — 02).
|