Практическая вибродиагностика и монтиторингВлияние дефектов износа поверхностей качения на вибрацию.
Дефекты износа поверхностей качения влияют на характер вибрации во всем частотном диапазоне, поскольку в процессе износа увеличивается коэффициент трения и при взаимодействии дефектных поверхностей возникают периодические удары, что приводит к росту интенсивности высших гармоник и увеличению случайных составляющих в сигнале вибрации. Для проявления дефектов износа характерно наличие инкубационного периода, т.е. их развитие, сопровождающееся высокой скоростью износа, хорошо заметно на последних этапах эксплуатации подшипника.
и их гармоники) и субгармоническими частотами.
Основным свойством дефектов износа, в отличие от дефектов изготовления поверхностей, является более сильное проявление в сигнале вибрации кратных гармоник в области низких и средних частот, высокий уровень случайной вибрации и наличие ударных импульсов.
Влияние нарушения смазки при эксплуатации.
В принципе, отклонение количества смазки от номинальной величины можно отнеси к дефектам сборки подшипникового узла, а ухудшение качества (коксование, появление твердых частиц и др.) к дефектам износа. Нарушения смазки — наиболее распространенная причина выхода из строя изначально бездефектного подшипника. Уровень высокочастотной вибрации и температуры подшипника существенно зависит от состояния смазки. Кроме того, иногда нарушения смазки могут приводить к появлению в спектре вибрации 3...4 пиков с интервалом в 80...130 Гц в области 900...1600 Гц.
Наибольшее распространение для определения оценки состояния подшипников качения и дефектов нашли две группы методов. Первая группа основана на выделении и анализе дискретных составляющих на основных частотах возбуждения колебаний в подшипнике (см. таблицу 9 — 01).
Диагностическими признаками дефектов служат частотные составляющие спектра и характеристики импульсов, следующих с частотой перекатывания тел качения по локальным дефектам (например, местам выкрашивания): амплитуда импульса, соотношение энергии импульса в уровню шума, амплитуды спектральных составляющих на частоте повторения импульсов и ее гармониках. Для выделения этих параметров из сложного сигнала используют спектральные и корреляционные методы, выделение огибающей и др. Вторую группу составляют методы диагностирования технического состояния подшипника в целом. При потере работоспособности агрегата не имеют значения дефекты, вызвавшие выход из строя подшипника. Важно, что его необходимо заменить. В силу этого состояние подшипника оценивается по степени развития деградационных процессов. Широкое распространение нашел метод ударных импульсов (8РМ), нашедший воплощение в оборудовании объединения 8 КГ.
Дефектам подшипников качения присущи некоторые особенности В частности, характерно появление в сигнале вибрации гармонических частотных составляющих некратных частоте вращения ротора. Обычно на ранней стадии развития дефектов подшипника появляются признаки дефектов только одного из колец и, затем, другого. При одинаковой степени развития дефекта вибрация, вызываемая внутренним кольцом, имеет более низкую интенсивность, чем наружным. По мере износа подшипника далее появляются дефекты тел качения и, наконец, сепаратора. На осциллограмме вибросигнала (особенно виброускорения) имеются ударные импульсы и выбросы, кривая вибрации обычно имеет случайный непериодический характер, однако некоторые импульсы могут быть периодичны. В спектре достаточно часто частотные составляющие, характерные для дефектов колец, модулируются частотой вращения ротора, приводя к появлению боковых частотных составляющих. С увеличением износа поверхностей качения: и количества локальных дефектов количество и уровень гармонических составляющих, боковых частот и разностных частот возрастают. Появление составляющих вибрации на резонансных частотах других деталей и узлов агрегата обычно говорит о сильном износе подшипника. Высокий уровень случайной вибрации (широкополосный шум) появляется при значительном нарушении геометрических размеров подшипника. При повышении вибрации подшипника или анализе причины его преждевременного выхода из строя следует установить с чем она связана: с износом, нарушениями смазки, избыточной статической нагрузкой или повышенной вибрацией. Дефекты смазки, избыточная статическая нагрузка и повышенная вибрация многократно ускоряют темп износа подшипника.
Высокочастотная вибрация сильно затухает при распространении, что позволяет разделять сигналы подшипников разных подшипниковых узлов.
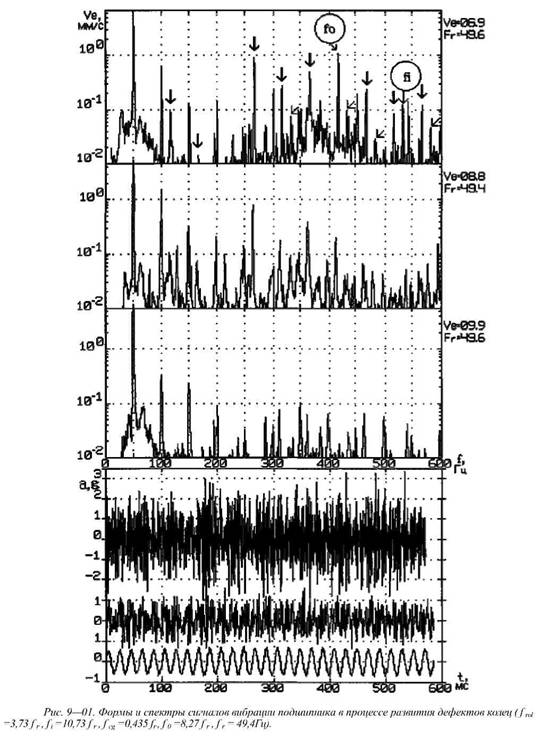
На рис. 9 — 01. приведена динамика изменения вибрации подшипника за период в 14 месяцев по мере появления износа и дефектов колец.
Усталостное разрушение подшипников проявлялось в виде выкрашивания материала дорожек колец и тел качения. В процессе ремонта агрегата произвели замену подшипников, однако, вызывающий повышенную вибрацию дефект электромагнитного происхождения не был устранен. Это приводило к тепловому расширению ротора и, как следствие, возникновению чрезмерно большой нагрузки на подшипники и их ускоренному выходу их строя.
Нижние форма и спектр сигнала измерены практически после ремонта. Для этого периода характерно отсутствие дефектов подшипников выразившееся в почти периодическом характере кривой виброускорения с невысокой амплитудой, сколько-нибудь заметные ударные импульсы отсутствуют. Спектр виброскорости включает преобладающую составляющую на частоте вращения ротора с высоким значением амплитуды, вызванную неуравновешенностью ротора. Уровень шумов сравнительно низок (случайная вибрация практически отсутствует).
Следующие (снизу —в верх) форма и спектр сигнала получены после года эксплуатации агрегата. Заметны значительные изменения формы сигнала вибрации: кривая вибрации непериодическая, появились ударные импульсы и случайная вибрация. Однако пиковое значение виброускорения пока еще невелико по величине — не превышает 1,5 § . Спектр виброскорости также изменился: появились составляющие на частотах возбуждения внутреннего и наружного колец, существенно повысился уровень шумов. Этому периоду соответствует появление локальных дефектов на наружном кольце подшипника.
Забиваем Сайты В ТОП КУВАЛДОЙ - Уникальные возможности от SeoHammer
Каждая ссылка анализируется по трем пакетам оценки: SEO, Трафик и SMM.
SeoHammer делает продвижение сайта прозрачным и простым занятием.
Ссылки, вечные ссылки, статьи, упоминания, пресс-релизы - используйте по максимуму потенциал SeoHammer для продвижения вашего сайта.
Что умеет делать SeoHammer
— Продвижение в один клик, интеллектуальный подбор запросов, покупка самых лучших ссылок с высокой степенью качества у лучших бирж ссылок.
— Регулярная проверка качества ссылок по более чем 100 показателям и ежедневный пересчет показателей качества проекта.
— Все известные форматы ссылок: арендные ссылки, вечные ссылки, публикации (упоминания, мнения, отзывы, статьи, пресс-релизы).
— SeoHammer покажет, где рост или падение, а также запросы, на которые нужно обратить внимание.
SeoHammer еще предоставляет технологию Буст, она ускоряет продвижение в десятки раз,
а первые результаты появляются уже в течение первых 7 дней.
Зарегистрироваться и Начать продвижение
(помеченные наклонными стрелками) по

Этот пример иллюстрирует достаточно высокую чувствительность формы сигнала виброускорения к изменению состояния деталей подшипника качения.
На рис. 9 — 02. приведены форма сигнала виброускорения и спектры сигналов виброскорости подшипника агрегата, первый из которых (нижний спектр) собран после 2,5 лет безремонтной эксплуатации агрегата. Износ подшипника проявлялся в виде выкрашивания материала дорожек колец (кроме других на внутреннем кольце был обнаружен развитый локальный дефект) и тел качения.
Нижний спектр виброскорости содержит составляющие, кратные частоте вращения ротора, вызванные некоторым износом подшипника. Уровень шумов низок, случайная и высокочастотная вибрация сравнительно невелика.
Следующий (снизу —в верх) спектр получены после появления локальных дефектов внутреннего кольца подшипника. Заметны значительные изменения спектра виброскорости: появились высокочастотные составляющие на гармониках частоты возбуждения (и боковых частотах) внутреннего кольца, существенно повысился уровень шумов.
. Отчетливо наблюдаются периодические ударные импульсы, возникающие при перекатывании шариков по сильно развитому локальному дефекту внутреннего кольца с периодом 3,8 мс. Большое значение амплитуды и коэффициента пика 4,2 говорят о значительном развитии дефекта.
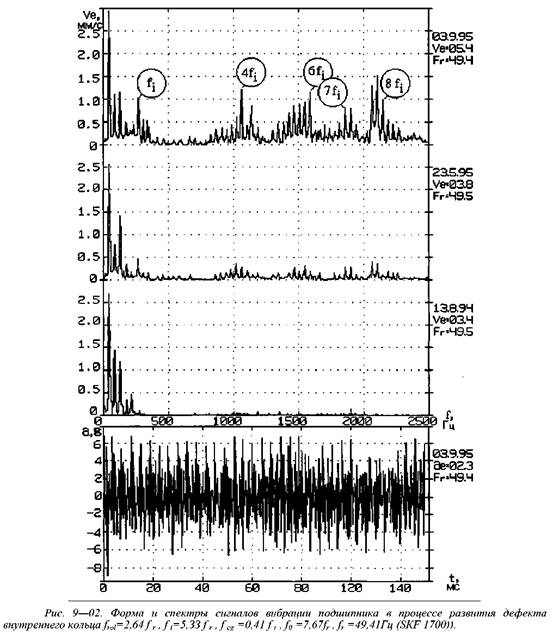
(приблизительно 263 Гц) и ее 4 —я, 6 —я, 7 —я и 8 —я гармоники,
(приблизительно 380 Гц) практически
не наблюдается, поэтому можно предположить, что дефекты внешнего кольца менее развиты. Характерно, что уровень шумов по мере развития дефектов возрастает и в верхнем спектре наибольший. За счет появления высокочастотной вибрации (если сравнивать нижний и верхний спектры) СКЗ виброскорости возросло белее чем в полтора раза, хотя вибрация на преобладающей частоте (частоте вращения ротора) практически не изменилась.
Этот пример показывает, что для повышения достоверности контроля состояния подшипников качения необходимо стараться расширять по мере возможностей частотный диапазон измерений вибрации и анализировать характер вибрации в высокочастотной области спектра.
На рис. 9 — 03. приведены форма сигнала виброскорости и спектр сигнала виброускорения подшипника, имеющего кроме износа, раковин и трещины внутреннего кольца износ остальных деталей, особенно внешнего кольца и шариков. Спектр вибрации подшипника включает составляющие на всех основных частотах возбуждения при работе подшипников, свидетельствующие о наличии дефектов всех деталей подшипника.
(приблизительно 222 Гц).

. Большие значения вибрации на этих частотах, присутствие в спектре частоты возбуждения сепаратора и высокий уровень шумов также говорят о предельном состоянии подшипника.
Кривая виброскорости имеет непериодический, "случайный" характер, амплитуда отдельных импульсов достигает 8 д , а значение коэффициента пика — 3,1.
На рис. 9 — 04. показаны форма и спектр сигнала вибрации подшипника, имевшего нарушение смазки. В приведенном примере произошло старение смазки, выразившееся в практически полном отсутствии нормальной смазки в подшипнике: ее коксовании и появлении твердых частиц. В течение некоторого времени обслуживающий персонал наблюдал рост температуры подшипника, которая к моменту измерения приведенных формы и спектра сигнала вибрации достигла предельно допустимого значения, а также роста общего уровня вибрации.
. Кривая вибрации имеет непериодический, "случайный" вид, амплитуда
Большие значения амплитуды вибрации и
коэффициента пика 4,6 говорят об опасности дефекта.
Непосредственно после измерений агрегат был кратковременно остановлен и проведена замена смазки подшипника. После пуска агрегата температура нормализовалась и высокочастотная вибрация полностью исчезла. Следует отметить, что подобные спектры вибрации подшипника при нарушениях смазки встречаются не всегда.
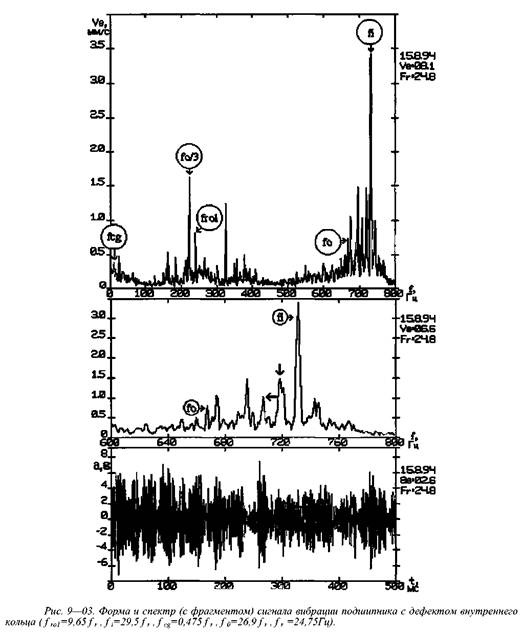
Одним из наиболее достоверных и удобных методов определения вида дефектов и оценки состояния подшипников качения является метод спектрального анализа огибающей высокочастотных составляющих сигнала вибрации, создаваемой ударными импульсами.
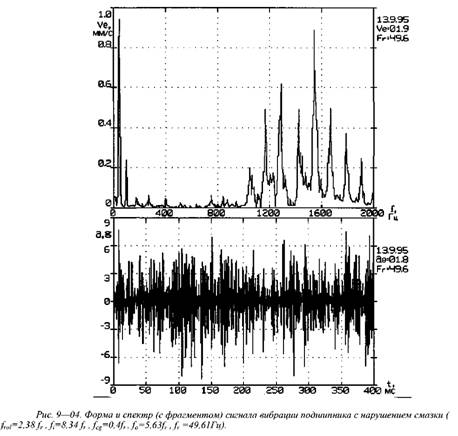
Наиболее существенным недостатком этого метода можно считать высокие потери при распространении вибрации, что требует максимального приближения датчика к подшипнику качения. В качестве диагностического признака весьма удобно использовать амплитудную модуляцию высокочастотной случайной вибрации подшипникового узла, а диагностического параметра — парциальные глубины модуляции случайного сигнала. Опыт показывает, что глубина модуляции случайной вибрации слабо зависит от частоты вращения подшипника и его габаритов, что позволяет устанавливать обобщенные уровни тревог, не зависящие от вида подшипника и агрегата. Установлено также, что чем шире полоса фильтра демодулятора, тем выше чувствительность измерительного тракта при обнаружении модуляции гармоническим сигналом случайного сигнала, спектральная плотность которого постоянна в пределах полосы пропускания фильтра. Из-за резонансов в подшипниковых узлах спектральная плотность сигнала не бывает постоянной в широкой полосе частот, что приводит к появлению ошибок измерения глубин модуляции. Поэтому наиболее целесообразно использовать фильтры с относительно небольшой полосой пропускания, например, треть октавные. Ошибки измерения появляются также когда в полосу пропускания фильтра демодулятора попадают гармонические составляющие сигнала вибрации, во избежание чего желательно, по мере возможностей, анализировать составляющие вибрации в полосе 10...15 кГц.
Дефекты сборки и эксплуатации подшипников качения приводят к появлению в спектре огибающей гармонических составляющих с частотами приведенными в Таблице 9 — 01.
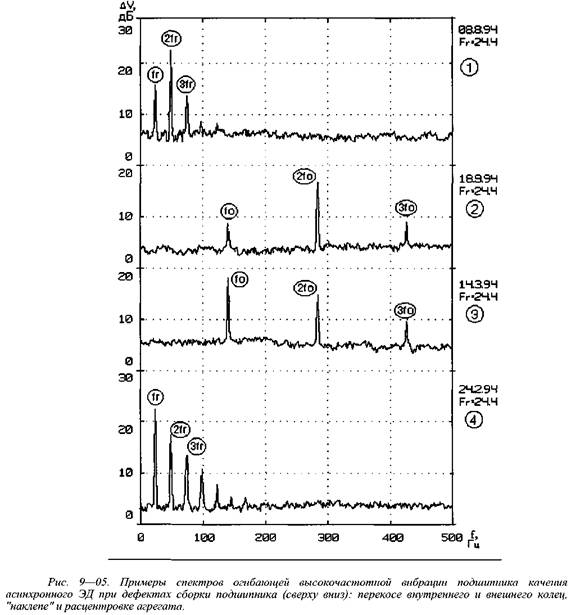
(рис. 9 — 05, позиция 1).
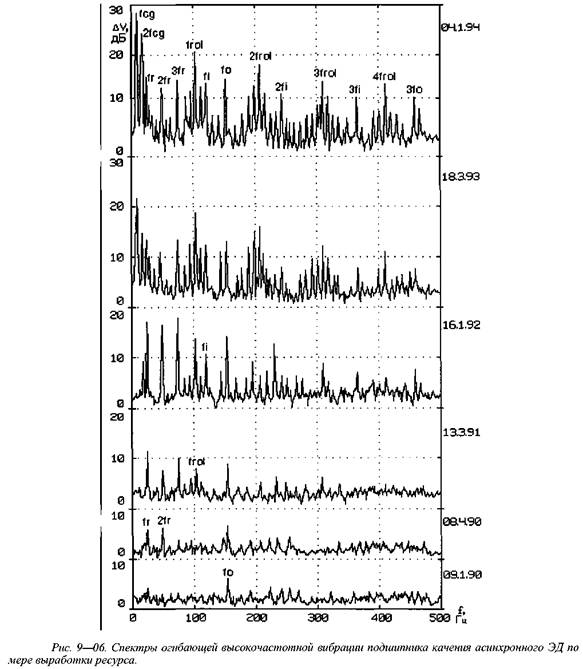
(рис. 9 — 05, позиция 3).
является преобладающей (рис. 9 — 05, позиция 4).
На рис. 9 — 06. приведены спектры огибающей высокочастотной вибрации подшипника качения асинхронного ЭД по мере выработки ресурса в течение примерно 30000 часов непрерывной эксплуатации.

говорящие о развитии небольших дефектов: перекоса внутреннего кольца и/или расцентровки, а также нарушении и/или износе тел качения.
Сервис онлайн-записи на собственном Telegram-боте
Попробуйте сервис онлайн-записи VisitTime на основе вашего собственного Telegram-бота:
— Разгрузит мастера, специалиста или компанию;
— Позволит гибко управлять расписанием и загрузкой;
— Разошлет оповещения о новых услугах или акциях;
— Позволит принять оплату на карту/кошелек/счет;
— Позволит записываться на групповые и персональные посещения;
— Поможет получить от клиента отзывы о визите к вам;
— Включает в себя сервис чаевых.
Для новых пользователей первый месяц бесплатно.
Зарегистрироваться в сервисе
в начальной стадии развития.
становится
вокруг
и их гармоник.
в значительной степени определяет ресурс подшипника качения и может успешно использоваться для решения задачи оценки и прогноза технического состояния подшипника качения.
|