Химикаты из древесиныИзготовление картона на картоноделательных машинах
Изготовление многослойного листового картона. Для выработки многослойного листового картона применяют одно- и двухцилиндровые папочные и плоскосеточные машины. На рис. 27 показана автоматизированная поточная линия производства

электроизоляционного листового картона, Масса концентрацией 0,4—0,8 %, подготовленная для отлива, поступает в напорный ящик открытого типа, откуда напускается на движущуюся сетку. На сеточном столе происходит отлив и формование элементарного слоя картона массой 45—60 г/м 2 . Сухость слоя картона после сеточного стола (отсасывающего вала) составляет 13— 18%.
Элементарный слой с отсасывающего вала сжатым воздухом передается на прессовое сукно форматного вала, на который он наматывается до определенной толщины. Форматный вал расположен на двух обрезиненных прессовых валах диаметром 600 мм. Один из них укреплен на неподвижной, а второй на подвижной опорах с пневматическим устройством для изменения и регулировки давления при отжиме картона. Форматный вал имеет автоматический нож и механизм регулировки заданной толщины картона, приводимый в движение сжатым воздухом.
По достижении нущной толщины картон автоматически срезается с форматного вала ножом, выдвигающимся через щель из тела форматного вала. Кромка разрезанного картона отдувается сжатым воздухом через вторую щель в форматном вале, и лист картона падает на приемный роликовый транспортер. Скорость движения транспортера в момент приемки срезанного листа совпадает с линейной скоростью форматного вала, а затем снижается до 20 м/мин. Толщина сошедшего с форматного вала картона задается в зависимости от объемной массы готового картона после каландрирования. Сухость картона после форматного вала составляет 23—27 %.
С приемного роликового транспортера листы картона поступают в трехъярусный загрузочный роликовый транспортер, а затем в гидравлический пресс. Картон прессуется в трехъярусном прессе при удельном давлении 2—5 МПа между плитами при температуре 80—90 °С. Сухость картона после пресса 55—60 %.
Листы картона загружают в пресс транспортером из бронзовых сеток. Этими же сетками после прессования листы картона выгружаются на транспортер. Такой же сеткой обтянута верхняя плита пресса. Таким образом, лист картона при прессовании зажат между двумя сетками. Это способствует удалению воды, улучшает поверхность картона и предохраняет плиты от. з агрязнения. Все процессы прессования автоматизированы.
После прессования листы картона из пресса выводятся подвижными сетками на трехъярусный транспортер, который подает их в тоннельную сушилку с калориферным обогревом и прижимными сетками. По длине сушилка разделена на 13 зон; в каждой поддерживается различная температура воздуха. В конце сушилки расположена охладительная камера, оборудованная увлажнительной установкой. Режим сушки зависит от вида картона и его толщины.
По окончании сушки листы картона влажностью 4—8 подаются транспортерами на дисковый станок для обрезки профильных кромок. Обрезанные кромки картона дробятся на кусочки длиной 5—10 мм и пневмотранспортером подаются в циклон, а затем в гидроразбиватель для брака.
После сушки картон содержит 4—8 % влаги, а для его отделки требуется влажность 10—14. Поэтому картон увлажняют на специальных станках, затем кипоукладчиком укладывают на металлический поддон, установленный на рольганге, в стопы высотой до 3 м и оставляют для отлежки в течение 1—5 суток в помещении с относительной влажностью воздуха не ниже 75—80 %. Во время отлежки влажность по толщине листа выравнивается, повышается пластичность картона, и он легче каландрируется. По окончании отлежки картон поступает на каландр. Каландрированием достигается уплотнение и повышение лоска картона, а также выравнивание его толщины. Для каландрирования листового картона обычно применяют двухвальные сатинированные и фрикционные каландры.
Фрикционный каландр состоит из двух металлических валов, он отличается от обычного тем, что верхний вал является приводным, а нижний приводится от верхнего через шестеренчатую передачу с опережением на 18—20 %. Благодаря разности скоростей валов создается сильное трение между поверхностями листа и валами, за счет чего картон приобретает необходимый лоск. Линейное давление при каландрировании очень высоко и может изменяться в пределах от 1960 до 14 700 Н/см и более, в зависимости от вида вырабатываемого картона. Для повышения эффективности отделки валы каландра обогреваются паром. Скорость движения

валов 50—115 м/мин. После отделки картон сортируется; затем его упаковывают в деревянные щитки или ящики.
Изготовление ролевого картона. Для изготовления ролевого картона применяют многоцилиндровые, плоскосеточные и комбинированные картоноделательные машины, имеющие мокрую, сушильную и отделочную части.
Многоцилиндровые картоноделательные машины применяют для изготовления многослойного картона мас-
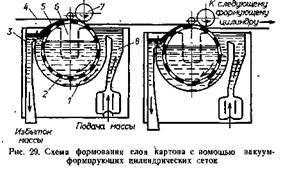
сой от 200 до 1200 г/м 2 . Машины" имеют до восьми сеточных цилиндров. На них можно получать ролевый картон стольких слоев, сколько установлено сеточных цилиндров.
Многослойный ролевый картон состоит из нескольких элементарных слоев; он значительно прочнее, чем картон такой же толщины, изготовленный отливом одного слоя на плоскосеточной машине. Кроме того, элементарные слои картона можно получать из разных волокнистых материалов. Например, наружные слои, от которых зависит внешний вид картона, изготовляют из лучшего волокнистого материала, чем внутренние слои. Это позволяет экономить дорогостоящее волокно — целлюлозу. Поэтому массовые виды картона — переплетный, коробочный и др. изготовляют на многоцилиндровых картоноделательных машинах. Схема кругло-сеточной картоноделательной машины К-06А, изготовляющей переплетный, коробочный и другие виды картона, представлена на рис. 28.
Забиваем Сайты В ТОП КУВАЛДОЙ - Уникальные возможности от SeoHammer
Каждая ссылка анализируется по трем пакетам оценки: SEO, Трафик и SMM.
SeoHammer делает продвижение сайта прозрачным и простым занятием.
Ссылки, вечные ссылки, статьи, упоминания, пресс-релизы - используйте по максимуму потенциал SeoHammer для продвижения вашего сайта.
Что умеет делать SeoHammer
— Продвижение в один клик, интеллектуальный подбор запросов, покупка самых лучших ссылок с высокой степенью качества у лучших бирж ссылок.
— Регулярная проверка качества ссылок по более чем 100 показателям и ежедневный пересчет показателей качества проекта.
— Все известные форматы ссылок: арендные ссылки, вечные ссылки, публикации (упоминания, мнения, отзывы, статьи, пресс-релизы).
— SeoHammer покажет, где рост или падение, а также запросы, на которые нужно обратить внимание.
SeoHammer еще предоставляет технологию Буст, она ускоряет продвижение в десятки раз,
а первые результаты появляются уже в течение первых 7 дней.
Зарегистрироваться и Начать продвижение
Сеточная часть машины состоит из восьми ванн с сеточными цилиндрами диаметром по 1500 мм. Предварительная прессовая часть состоит из двух обычных, двух отсасывающих прессов и отсасывающего гауч-пресса. Основная прессовая часть включает три отсасывающих пресса и сглаживающий пресс. Между вторым и третьим отсасывающими прессами расположены шесть картоно-сушильных и два сукносушильных цилиндра. Основная сушильная часть имеет закрытый колпак. Между каландрами установлены два картоносушильных и два холодильных цилиндра. Между 36-м и 37-м цилиндрами установлен клеильный пресс для проклейки картона с поверхности. Машина оснащена двумя 8-вальными каландрами и накатом барабанного типа. Заправка полотна картона в прессовой части пневматическая, в сушильной части — автоматическая.
Формование многослойного картона осуществляется с помощью вакуум-формующих цилиндрических сеток (рис. 29). Основным элементом формующего устройства является цилиндрическая сетка 2, вращающаяся в ванне 1. Масса в ванну подается через напорный ящик 8, избыток массы через переливное устройство 3 возвращается в машинный бассейн. При вращении цилиндрической сетки под действием вакуума и напора массы на поверхности сетки образуется элементарный слой массы 5, а вода фильтруется внутрь барабана и через карманы 6 отводится в бассейн оборотной воды. На современных машинах элементарный слой картона, формируется под небольшим вакуумом. Для этого внутри сеточного цилиндра вентилятором создается вакуум 392—588 Па, способствующий получению элементарного слоя равномерной толщины и позволяющий повышать скорость машины. Сформированный элементарный слой массы отжимается съемным валиком 7 и, прилипая к бесконечному съемному сукну 4, транспортируется им к следующему формующему устройству, где на первый слой наслаивается второй элементарный слой массы и так далее на всех восьми формирующих устройствах.
Сформированное сырое 8-слойное картонное полотно съемным сукном подается в предварительную прессовую часть, где подвергается осторожному уплотнению и обезвоживанию с постепенным повышением давления от пресса к прессу. Таким образом, полотно подготовляется к повышенному давлению на основных прессах. Сухость полотна после предварительного прессования колеблется от 25 до 30 %. После предварительных прессов полотно поступает на основную прессовую часть машины, где происходит дальнейшее уплотнение и обезвоживание до сухости 35—40 %. Устройство этой части картоноделательной машины аналогично устройству прессовой части бумагоделательной машины. Далее полотно картона поступает на сушку. Сушка ролевого картона производится контактным способом на сушильных цилиндрах, которые расположены в два ряда в шахматном порядке. Имеются также карто-ноделательные машины, в которых сушильные цилиндры расположены в три ряда. Давление пара в сушильных цилиндрах поддерживается в пределах 0,25—0,5 МПа.
Для повышения качества отделки картон поступает на первый 8-вальный каландр, оборудованный мокрыми шаберами, при помощи которых можно производить поверхностную окраску или увлажнение картона. Затем картон подается на досушивающие цилиндры и на второй каландр для окончательной отделки.
Плоскосеточные картоноделательные машины применяют для выработки тарного и кровельного картона, а также некоторых видов бумаги из сульфатной целлюлозы — мешочной, кулечной и упаковочной. Эти машины имеют более высокую скорость (до 760 м/мин) и производительность (800—900 т/сут тарного картона), чем многоцилиндровые картоноделательные машины. Сеточная часть на некоторых плоскосеточных картоноделательных машинах оборудована двумя напорными ящиками. Второй ящик предназначен для дополнительного налива массы на сетку (покровного слоя).
На этих машинах изготовляют 2-слойный тарный картон. Ос 7 нова такого картона делается из целлюлозы высокого выхода, а наружный слой — из целлюлозы нормального выхода. Нанесение покровного слоя из более прочного волокнистого материала значительно повышает механические показатели и печатные свойства и улучшает внешний вид картона. Установка второго напорного ящика позволяет вырабатывать на более производительных длинносеточных машинах картон с облагороженной поверхностью, который ранее изготовляли на менее производительных многоци-линдровых машинах. По конструкции плоскосеточная машина аналогична бумагоделательной машине.
В СССР изготовляются плоскосеточные картоноделательные машины К-07 и К-10 для ваработки плоских слоев гофрированного картона, а также машины К-15 и К-09 для выработки картона и бумаги для гофрирования. Производительность их соответственно 500; 850; 320 и 500 т в сутки; рабочая скорость 200—400; 280—485; 200—400 и 300—400 м/мин; скорость привода для всех этих машин одинакова —в пределах 200—485 м/мин.
|