Технология электрической сварки металлов и сплавов плавлениемСварка плавлением высоколегированных сталей и сплавов
При изготовлении изделий из высоколегированных сталей и сплавов применяют все виды сварки плавлением: под флюсом, покрытыми электродами, в среде защитных газов, плазменную, контактную, электрошлаковую, электроннолучевую, а также специальные виды сварки: диффузионную в вакууме, сварку трением и др. Значительную часть узлов из жаропрочных сталей и сплавов изготовляют пайкой.
Сварка под флюсом. Сварка под флюсом является ведущим технологическим процессом в производстве химической и нефтехимической аппаратуры из коррозионностойких сталей. Находит применение она и при производстве изделий из жаропрочных сталей и сплавов.
Столь широкое применение сварки под флюсом обусловлено рядом существенных преимуществ ее перед ручной сваркой. При сварке под флюсом, как и при других методах механизированной сварки плавлением, можно получать швы практически любой длины без перерывов. При этом резко уменьшается число кратеров. Это имеет большое значение, так как на высоколегированных швах возможность образования кристаллизационных трещин в Кратерах значительно выше, чем на углеродистых.
Но самое большое значение имеет постоянство условий сварки под флюсом и, как следствие, постоянство химического состава и свойств металла шва. Это очень важно в отношении высоколегированных сталей и сплавов, потому что незначительное изменение химического состава металла шва может привести к образованию в нем кристаллизационных трещин или существенному ухудшению его коррозионных или жаропрочных свойств. Например, повышение в металле аустенитного шва количества углерода на 0,02—0,03% в ряде случаев может привести к потере его коррозионной стойкости, а повышение содержания кремния на 0,2—0,3% может быть причиной образования кристаллизационных трещин и т. д.
Сварка под флюсом дает возможность получать гладкие швы практически без чешуек с плавным переходом к основному металлу. Такие швы отличаются более высокой коррозионной стойкостью по сравнению со швами, выполненными вручную. Это еще одно немаловажное преимущество сварки под флюсом перед всеми видами ручной сварки.
Техника сварки под флюсом высоколегированных сталей и сплавов практически не отличается от техники сварки обычных углеродистых сталей. Имеется, однако, ряд специфических особенностей, характерных только для высоколегированных сталей и сплавов.
К числу этих особенностей относится преимущественное использование постоянного тока. Это вызвано тем, что для сварки высоколегированных сталей и сплавов применяют фторидные и высокоосновные бесфтористые флюсы, сварка под которыми на переменном токе затруднена. Сварку под фторидными флюсами независимо от их окислительной способности производят постоянным током обратной полярности, а под высокоосновными бесфтористыми флюсами •— постоянным током прямой полярности.
Сварку под флюсом высоколегированных сталей и сплавов выполняют швами относительно небольшого сечения (более стойки против кристаллизационных трещин), что предопределило преимущественное использование в этом случае тонкой проволоки. Наиболее широко применяют проволоку диаметром 2—3 мм, в то время как при сварке углеродистых сталей предпочтительна более толстая проволока (диаметром 3—5 мм). В связи с этим при сварке высоколегированной проволокой приходится значительно уменьшать вылет электрода.
Проволока из аустенитных сталей и сплавов из-за пониженной теплопроводности и высокого электрического сопротивления при прочих равных условиях плавится быстрее, чем обычная низкоуглеродистая проволока. Поэтому для получения сварных швов с хорошим формированием вылет электрода приходится еще больше уменьшать (примерно в 1,5—2 раза по сравнению с вылетом обычной стальной проволоки). Так, при сварке аустенитной проволокой диаметром 2—3 мм вылет электрода не должен превышать 20—30 мм.
Температура плавления аустенитных сталей и сплавов на 50—150° С ниже, чем обычных углеродистых. Поэтому для получения провара такой же глубины, как и на углеродистых сталях, при сварке под флюсом, а также и других видах сварки плавлением аустенитных сталей и сплавов величину тока следует уменьшать на 10—30%.
Особое внимание при механизированной сварке сталей и сплавов этой группы необходимо обращать на состояние токо-подводящих мундштуков. Из-за более высокого коэффициента трения высоколегированной проволоки по меди и медным сплавам мундштуки быстро изнашиваются. В результате нарушается электрический контакт между мундштуком и проволокой и ухудшается формирование шва; возможно образование дефектов типа непроваров, подрезов и др.
Для сварки под флюсом высоколегированных сталей и сплавов используют почти все сварочные проволоки, предусмотренные ГОСТ 2246—70 (табл. 10-22). Кроме того, для сварки сталей и сплавов этой группы применяют довольно большое количество сварочных проволок, выпускаемых по ведомственным техническим условиям (табл. 10-23).
Высоколегированные жаропрочные стали и сплавы сваривают в основном подфторидными безокислительными флюсами АНФ-1П, АНФ-5, АНФ-8, АНФ-23, АНФ-24, 48-ОФ-6, а также окислительными бескремнистыми флюсами АНФ-17 (система CaF3— А1203—МпО) и АНФ-22 (система CaF2—В203). Для сварки коррозионностойких сталей наибольшее применение получили низкокремнистые флюсы АН-26, 48-08-10 и АНФ-14 (см. § 42). Практически все флюсы для сварки высоколегированных сталей и сплавов способны гидратироваться. Поэтому во избежание образования пор в швах их необходимо прокаливать непосредственно перед сваркой.
Флюсы, используемые для сварки коррозионностойких сталей, подлежат обязательному контролю на углерод. Содержание его во флюсе не должно превышать 0,2%, а в случае сварки сверх-низкоуглеродистых сталей содержание углерода во флюсе желательно ограничить до 0,1%.
Современные фторидные флюсы в сочетании с высоколегированными проволоками позволяют успешно сваривать ответственные конструкции из высоколегированных сталей и сплавов. Ручная дуговая сварка. Высоколегированные стали и сплавы вручную сваривают так же, как и обычные конструкционные стали. Вместе с тем имеется ряд специфических особенностей, главные из которых: преимущественное применение электродов с фтористо-кальциевым покрытием; сварка на постоянном токе обратной полярности*; сварка короткой дугой без поперечных колебаний конца электрода; сварка сравнительно короткими электродами на небольших токах.
Забиваем Сайты В ТОП КУВАЛДОЙ - Уникальные возможности от SeoHammer
Каждая ссылка анализируется по трем пакетам оценки: SEO, Трафик и SMM.
SeoHammer делает продвижение сайта прозрачным и простым занятием.
Ссылки, вечные ссылки, статьи, упоминания, пресс-релизы - используйте по максимуму потенциал SeoHammer для продвижения вашего сайта.
Что умеет делать SeoHammer
— Продвижение в один клик, интеллектуальный подбор запросов, покупка самых лучших ссылок с высокой степенью качества у лучших бирж ссылок.
— Регулярная проверка качества ссылок по более чем 100 показателям и ежедневный пересчет показателей качества проекта.
— Все известные форматы ссылок: арендные ссылки, вечные ссылки, публикации (упоминания, мнения, отзывы, статьи, пресс-релизы).
— SeoHammer покажет, где рост или падение, а также запросы, на которые нужно обратить внимание.
SeoHammer еще предоставляет технологию Буст, она ускоряет продвижение в десятки раз,
а первые результаты появляются уже в течение первых 7 дней.
Зарегистрироваться и Начать продвижение
В соответствии с ГОСТ 9466—60 и 10052—62 типы электродов для сварки высоколегированных сталей и сплавов обозначаются индексами Э, ЭАФ, ЭФ и ЭА (табл. 10-24).
Размеры и общие технические требования к указанным электродам регламентированы ГОСТ 9466—60. Условное обозначение электродов в соответствии с этим ГОСТом должно включать марку электрода, тип электрода, диаметр сварочной проволоки и номера ГОСТов.
Для примера приведем условное обозначение электродов ОЗЛ-7 типа ЭА-1Б диаметром 4 мм, применяемых для сварки сталей типа Х18Н10Т: ОЗЛ-7 — ЭА-1Б-4,0 ГОСТ 10052—62 и ГОСТ 9466—60.
Ряд марок электродов для сварки высоколегированных сталей и сплавов предусмотрен также ведомственными техническими условиями.
Для сварки коррозионностойких аустенитных сталей типа 18-10 и 17-13, жаропрочных сталей типа 14-14 и 14-16 и жаро-
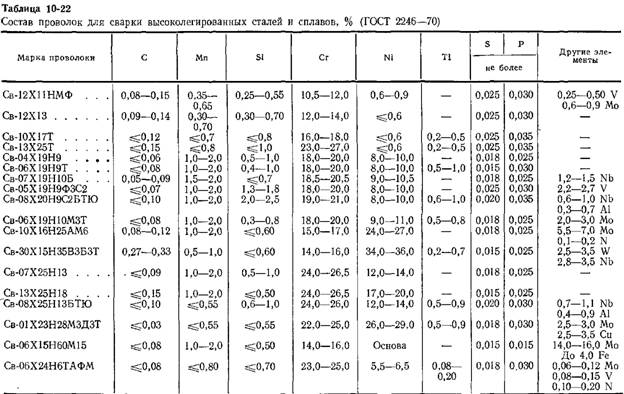
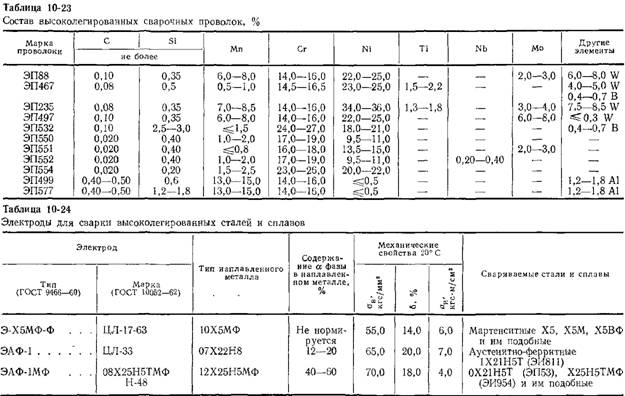
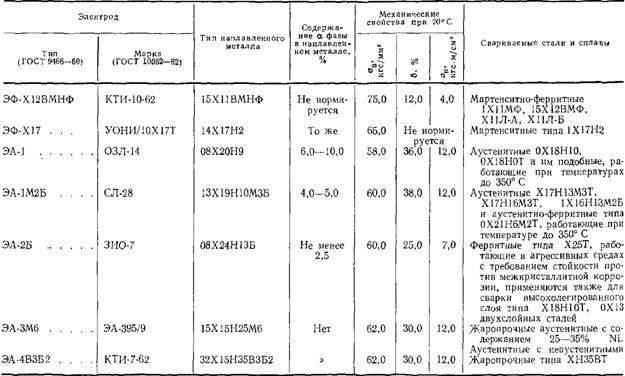
Стойких сталей типа 25-20 ГОСТ 10052—62 и рядом технические условий рекомендуется довольно много однотипных электродов. Ту или иную марку электродов необходимо выбирать в зависимости от конкретных условий эксплуатации сварных соединений.
Режимы сварки высоколегированных сталей и сплавов аусте-нитными электродами назначают с таким расчетом, чтобы отношение величины тока к диаметру электрода не превышало 25— 30 А/мм (табл. 10—25). При сварке аустенитными электродами в вертикальном или потолочном положении силу тока уменьшают на 10—30% по сравнению с этим параметром при сварке в нижнем положении. Электроды перед сваркой во избежание образования пор в металле шва надлежит прокаливать при температуре 250—400° С в течение 1—1,5 ч.
Газоэлектрическая сварка в аргоне и гелии. Газоэлектрическая сварка заняла прочные позиции в производстве сварных конструкций из высоколегированных сталей и сплавов. Наряду с такими старыми способами сварки, как аргоно- и гелиево-дуго-вая, успешно применяют также сварку в углекислом газе и в различных газовых смесях.
Замечательной особенностью аргоно- и гелиево-дуговой сварки является стабильность дуги, высокое качество сварных швов, обусловленное хорошей защитой зоны сварки от воздуха, и, что особенно важно, возможность наложения швов, занимающих произвольное положение в пространстве. При аргоно-дуговой сварке защита дуги и сварочной ванны от воздуха более надежна, чем в случае использования гелия, так как аргон тяжелее воздуха.
Аргоно-дуговую сварку высоколегированных сталей и сплавов производят плавящимся и неплавящимся (вольфрамовым) электродами. В первом случае применяют постоянный ток обратной полярности, во втором—прямой.
Сварку вольфрамовым электродом сталей и сплавов с высоким содержанием алюминия с целью разрушения окисной пленки рекомендуется выполнять на переменном токе.
При выполнении швов вольфрамовым электродом возможно попадание в металл шва частиц вольфрама. Наиболее частая причина разрушения электрода — неправильный выбор силы тока (чаще всего чрезмерно большая сила тока для данного диаметра электрода). Для получения качественных, ровных, хорошо сформированных швов необходимо своевременно затачивать вольфрамовый электрод. Это исключает перемещение активного пятна по торцу электрода; шов становится ровнее, без искривлений, с практически одинаковой глубиной провара по всей длине. Сварку в аргоне и гелии вольфрамовым электродом выполняют без присадочной проволоки (преимущественно при изготовлении конструкций из тонколистовых сталей) и с присадочной проволокой, вручную и на автомате (табл. 10-26 и 10-27). Сварку вручную необходимо выполнять так, чтобы конец присадочной проволоки все время находился в струе защитного газа.
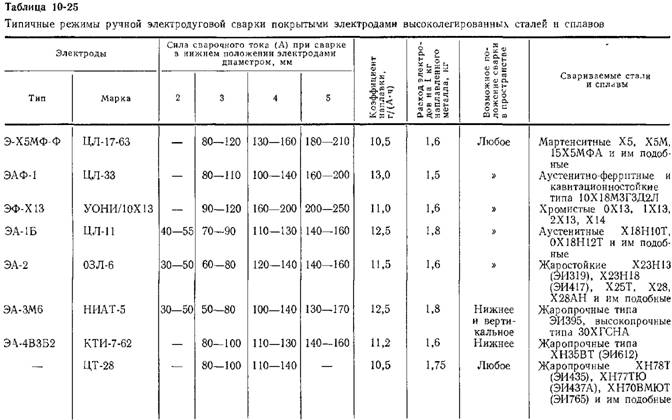
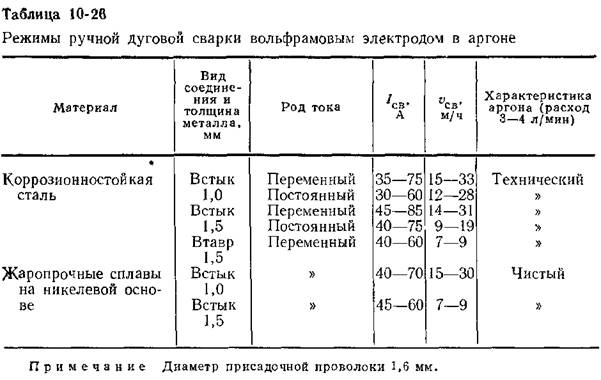
Аргоно-дуговая сварка плавящимся электродом имеет свои особенности, отличающие ее от сварки под флюсом и покрытыми электродами. Эта особенность состоит в том, что перенос металла в дуге должен быть струйным, а не капельным. Струйный процесс, как известно, возможен только при сварке на токах большой плотности. Например, при сварке проволокой типа 18-10 диаметром 1 мм струйный процесс устанавливается при силе тока порядка 190 А, а для проволоки диаметрами 1,6 и 2 мм— при силе тока не менее 240 и 320 А соответственно.
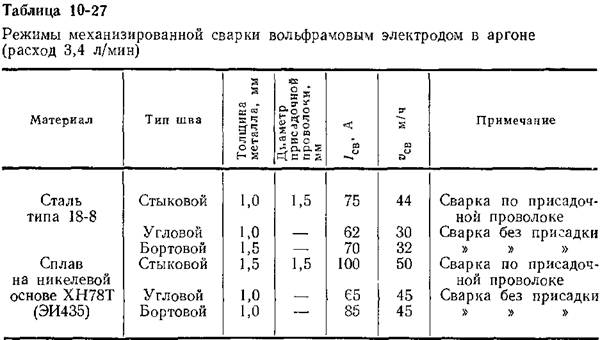
Известна разновидность аргоно-дуговой сварки плавящимся электродом, так называемой пульсирующей (периодически зажигаемой) дугой. При этом процессе дуга растягивается, сила тока падает и становится возможной сварка стали малой толщины (менее 0,5 мм).
При сварке высоколегированных сталей и сплавов, преимущественно аустенитных, применяют еще один вид сварки в аргоне — плазменно-дуговую.
Для сварки сталей и сплавов в инертных газах используют сварочные проволоки тех же составов, что и для сварки под флюсом (см. табл. 10-22 и 10-23).
Для сварки высоколегированных сталей и сплавов, легированных титаном и алюминием, рекомендуется аргон марки А, а в остальных случаях помимо марки А — также аргон марок Б и В.
Сварка в углекислом газе. При сварке высоколегированных сталей и сплавов плавящимся электродом в углекислом газе хром практически не окисляется. Переход титана из сварочной проволоки достигает 50% против 85% при сварке в аргоне и 65—70% при сварке под фторидными флюсами. Если проволока содержит до 0,10% С, возможно науглероживание шва на 0,02— 0,04%, что приводит к снижению его стойкости против межкри-сталлитной коррозии.
Если несколько повысить содержание в шве элементов-стабилизаторов (титана, ниобия) и элементов-ферритизаторов (кремния, алюминия, хрома), то, несмотря на науглероживание, может быть обеспечена требуемая коррозионная стойкость. На этом принципе создан ряд сварочных проволок для сварки высоколегированных аустенитных и хромистых сталей. Например, для сварки в углекислом газе сталей типа 18-10 (Х18Н10Т) применяется сварочная проволока Св-08Х20Н9С2БТЮ, для сталей типа 18-12 (Х18Н12Т) —проволока Св-08Х25Н13БТЮ, а для хромистых сталей типа 1Х17Н2— проволока 07Х18Н2Т (ЭП157). Эти проволоки имеют повышенное содержание хрома и дополнительно легированы кремнием, ниобием, титаном и алюминием.
Сервис онлайн-записи на собственном Telegram-боте
Попробуйте сервис онлайн-записи VisitTime на основе вашего собственного Telegram-бота:
— Разгрузит мастера, специалиста или компанию;
— Позволит гибко управлять расписанием и загрузкой;
— Разошлет оповещения о новых услугах или акциях;
— Позволит принять оплату на карту/кошелек/счет;
— Позволит записываться на групповые и персональные посещения;
— Поможет получить от клиента отзывы о визите к вам;
— Включает в себя сервис чаевых.
Для новых пользователей первый месяц бесплатно.
Зарегистрироваться в сервисе
Для примера в табл. 10-28 приведены ориентировочные режимы сварки в углекислом газе нержавеющей аустенитной стали аусте-нитной проволокой. Недостатком сварки в углекислом газе применительно к коррозионностойким сталям является довольно интенсивное разбрызгивание расплавленного металла (в среднем 10—12%) и образование очагов коррозии в месте приваривания брызг к металлу. Использование тонкой проволоки диаметром 1,0—1,5 мм и сварка на малых вылетах уменьшают разбрызгивание. Чтобы брызги не приваривались к металлу, рекомендуется его перед сваркой покрывать меловым раствором, замешанным на воде, или другим защитным слоем.
Недостатком сварки в углекислом газе является также образование на поверхности высоколегированного шва прочной
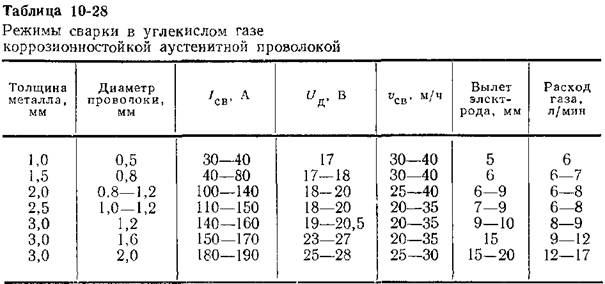
пленки окислов. Прочность сцепления этой пленки со швом тем больше, чем больше она содержит окислов хрома. В качестве одного из весьма эффективных средств борьбы с появлением окисной пленки при сварке в углекислом газе аустенитных сталей является подача в дугу небольшого количества фторидного сварочного флюса, например АНФ-5.
При сварке в углекислом газе на малых токах, так же как и при сварке в аргоне, удается выполнять швы, занимающие произвольное положение в пространстве. Это открывает большие перспективы для механизации сварочных работ на монтаже трубопроводов и других сооружений из коррозионностойких и жаропрочных сталей.
|