Технология электрической сварки металлов и сплавов плавлениемТехнология наплавки
Наплавка — это процесс нанесения при помощи сварки слоя металла на поверхность изделия. Путем наплавки получают изделия с износостойкими, кислотоупорными, жаростойкими, антифрикционными и тому подобными свойствами. Наплавку применяют при изготовлении новых и восстановлении изношенных деталей. В первом случае технический и экономический эффект достигается в результате получения биметаллических изделий с оптимальным сочетанием свойств металлов наплавленного и основного. Примером таких изделий могут служить сосуды атомных энергетических установок, клапаны двигателей внутреннего сгорания, детали газовой, нефтяной и водяной трубопроводной арматуры, конусы и чаши загрузочных устройств доменных печей и т. п. Наплавка в ремонтном деле эффективна благодаря тому, что восстановленная деталь часто в несколько раз дешевле новой детали и при правильно выбранной технологии восстановления не уступает ей по работоспособности.
Наплавка может быть осуществлена многими способами. Наиболее широко для этой цели применяют различные виды и приемы дуговой сварки.
Выбор состава наплавленного металла
Современная сварочная техника использует для наплавки сплавы весьма различного состава. Наплавленный металл можно классифицировать по разным признакам: структуре, химическому составу, назначению и т. п. В табл. 13-1 приведен проект классификации наплавленного металла по химическому составу, предложенный Международным институтом сварки (МИС). Каждому типу наплавленного металла соответствует много конкретных составов металла. Наиболее важные из них рассмотрены ниже.
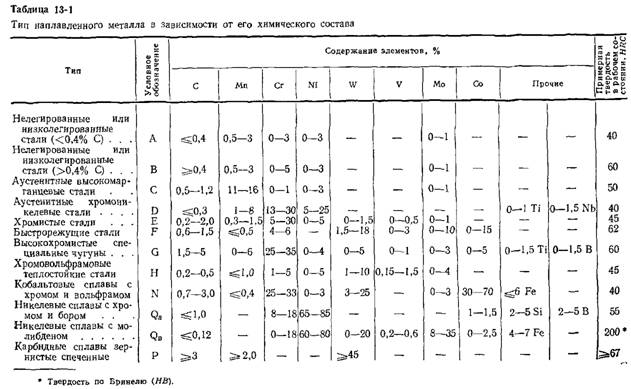
Для характеристики наплавленного металла данных только о химическом составе и твердости недостаточно. В зависимости от скорости охлаждения, режима термообработки и, наконец, от ориентации первичных кристаллитов по отношению к разрушающим нагрузкам наплавленный металл одного и того же химического состава обладает разной работоспособностью.
Тип наплавленного металла выбирают на основе анализа условий службы рабочих поверхностей наплавляемой детали. Поэтому важнейшим свойством наплавленного металла является способность его сопротивляться определенным видам изнашивания. Однако пока не существует стандартных методов определения износостойкости материалов, подобных тем, при помощи которых определяют такие характеристики, как предел прочности, ударную вязкость, твердость и т. п. Изнашивание как процесс постепенного изменения размеров детали очень чувствителен к изменению условий внешнего воздействия, т. е. к условиям испытаний. Поэтому в литературе по вопросам износостойкости различных материалов содержится большое количество несопоставимых и противоречивых данных. Кроме того, условия службы различных деталей весьма разнообразны, часто одна и та же деталь подвергается одновременно нескольким видам изнашивания.
Эти обстоятельства, с одной стороны, затрудняют лабораторную оценку износостойкости наплавленного металла, а с другой — усложняют выбор оптимального металла для определенных условий эксплуатации. Натурные же испытания наплавленных деталей, которые дают наиболее достоверные результаты, очень трудоемки и требуют много времени. Для приближенной оценки износостойкости наплавленного металла ниже приведены данные по износу отдельных типов металла, полученные при помощи сравнительно распространенных методик испытаний. Износостойкость наплавленного металла рассмотрена для типов металла в соответствии с классификацией МИС.
Абразивный износ обусловлен наличием абразивной среды в зоне трения; разрушение поверхностей трения происходит в результате местного пластического деформирования, микроцарапания и микрорезания абразивными частицами. Абразивный износ испытывают многие детали почвообрабатывающих машин, загрузочных и разгрузочных устройств строительных и дорожных машин. Стойкость наплавленного металла против абразивного износа оценивали на машинах Х4-Б и НК, разработанных М. М. Хрущовым, М. А. Бабичевым и Е. С. Берковичем.
Машина Х4-Б (рис. 13-1, а) снабжена вращающимся диском с шлифовальным полотном /, к которому усилием Р прижат образец 2. Держатель образца имеет специальный привод радиального перемещения. За один оборот диска образец перемещается к центру на величину, равную половине диаметра образца. Машина НК (рис. 13-1, б) имеет неподвижное медное кольцо 5, по которому скользят образцы 4. Образцы закреплены в специальных державках
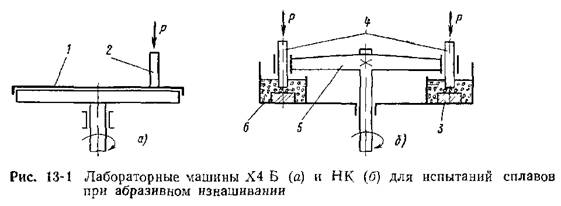
вращающейся поперечины 5. Медное кольцо расположено на дне кольцевого сосуда 6, в котором находится вода с кварцевым песком. Условия испытаний: удельная нагрузка, нормальная к поверхности изнашивания, 0,1 кгс/мм2, скорость трения —0,6 м/с, средний размер зерен абразива 0,06—0,08 мм (на электрокорундовом шлифовальном полотне машины Х4-Б) и 0,05— 0,25 мм (на машине НК). В качестве эталона использовали отто-жженную сталь 45, относительную износостойкость е определяли как отношение потери массы образца-эталона к потере массы наплавленного образца.
Как видно на рис. 13-2, наивысшей износостойкостью обладает наплавленный металл типов F и Р, т. е. с высоким содержанием вольфрама. В тип Р включены также композиционные сплавы, полученные пропиткой литого карбида вольфрама вязким сплавом-связкой. Несколько уступает упомянутым типам наплавленный металл типа G, но он значительно дешевле высоковольфрамовых сплавов. Среди сплавов типа G более высокой износостойкостью обладают заэвтектические высокохромистые чугуны с бором.
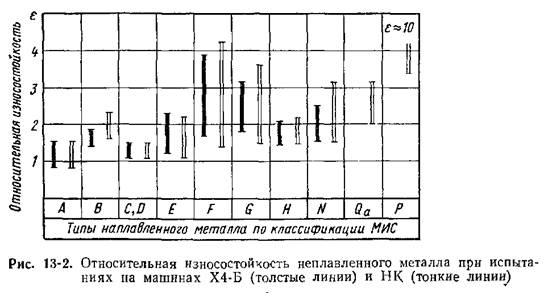
Многие детали (ножи дорожных машин, лемехи плугов, работающие в почве с валунами, била дробилок и т. п.) испытывают абразивный износ с ударами. Интенсивность этих ударов о наплавленную поверхность при эксплуатации весьма неопределенная. Поэтому встречающиеся в литературе термины незначительные, умеренные, значительные и тому подобные ударные нагрузки условны, так как они не основаны на каких-либо объективных методах испытаний, отражающих реальные условия службы деталей. Наплавленный металл, предназначенный для работы в абразивной среде, условно разделен на три группы, отличающиеся по склонности к выкрашиванию, оцененной на основании опыта эксплуатации наплавленных деталей. Сплавы группы I наиболее, а группы III наименее хрупки; сплавы группы II занимают промежуточное место (табл. 13-2).
Металлы У30Х14СМФ, 70Х11НЗ, 70Х20РЗТ и Г13Н4 применяются для наплавки деталей, изготовленных не только из углеродистых сталей, но и из аустенитной стали 110Г13Л.
Забиваем Сайты В ТОП КУВАЛДОЙ - Уникальные возможности от SeoHammer
Каждая ссылка анализируется по трем пакетам оценки: SEO, Трафик и SMM.
SeoHammer делает продвижение сайта прозрачным и простым занятием.
Ссылки, вечные ссылки, статьи, упоминания, пресс-релизы - используйте по максимуму потенциал SeoHammer для продвижения вашего сайта.
Что умеет делать SeoHammer
— Продвижение в один клик, интеллектуальный подбор запросов, покупка самых лучших ссылок с высокой степенью качества у лучших бирж ссылок.
— Регулярная проверка качества ссылок по более чем 100 показателям и ежедневный пересчет показателей качества проекта.
— Все известные форматы ссылок: арендные ссылки, вечные ссылки, публикации (упоминания, мнения, отзывы, статьи, пресс-релизы).
— SeoHammer покажет, где рост или падение, а также запросы, на которые нужно обратить внимание.
SeoHammer еще предоставляет технологию Буст, она ускоряет продвижение в десятки раз,
а первые результаты появляются уже в течение первых 7 дней.
Зарегистрироваться и Начать продвижение
Газоабразивный износ вызывается механическим действием твердых частиц, перемещаемых потоком газа. Разрушение поверхности происходит в результате срезания, выкрашивания, выбивания и многократного пластического деформирования поверхностных микрообъемов. Этому виду износа подвергаются детали трасс пневмотранспорта, лопатки пылевых вентиляторов и насосов, клапаны, конусы и чаши загрузочных устройств доменных печей, сопла реактивных двигателей, работающих на твердом топливе, и т. п.
Интенсивность изнашивания определяется скоростью, свойствами и формой абразивных частиц, температурой и степенью
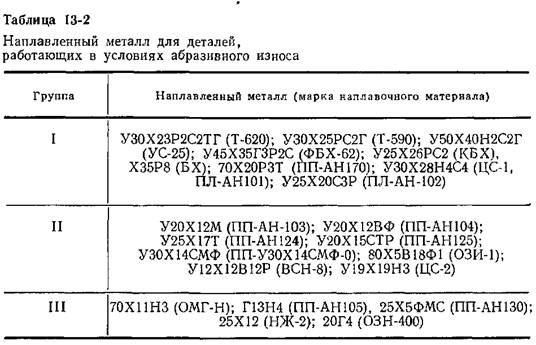
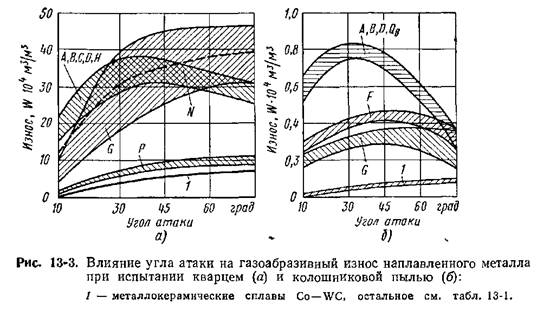
запыленности газового потока, физико-механическими свойствами изнашиваемого материала и рядом других факторов. Важнейшим кинематическим фактором является угол наклона вектора скорости абразивных частиц к поверхности изнашиваемой детали — угол атаки. Изменение угла атаки сопровождается изменением процесса разрушения поверхностного слоя и скорости изнашивания. Поэтому газоабразивную износостойкость оценивают при регламентированном угле атаки.
На рис. 13-3 показаны некоторые обобщенные данные об износе наплавленного металла, полученные при обдувке образцов запыленным газовым потоком. В качестве абразива использовали кварцевый песок и колошниковую пыль с размером частиц 0,05— 0,4 мм. Концентрация абразива в потоке составляла 10% по массе, скорость абразивных частиц 250—350 м/с, температура потока 400° С. Износ w выражали отношением объема изношенного материала к объему израсходованного абразива.
При испытании кварцевым песком металл типов А, В, G, D и Н изнашивался примерно одинаково, максимум износа соответствовал углу атаки 30—45°. Высокохромистые чугуны типа С обладают преимуществом только при малых углах атаки, при больших же углах атаки обычная углеродистая сталь изнашивается меньше многих типов высоколегированного наплавленного металла высокой твердости. В широком диапазоне углов атаки высокой износостойкостью обладает композиционный сплав на основе литых карбидов вольфрама при их содержании ~50 об. % и размерах частиц карбидов 0,6—1,5 мм. На рис. 13-3, а этот сплав условно отнесен к типу Р.
При испытаниях в тех же условиях колошниковой пылью доменной печи (более мягкий абразив) наиболее распространенный
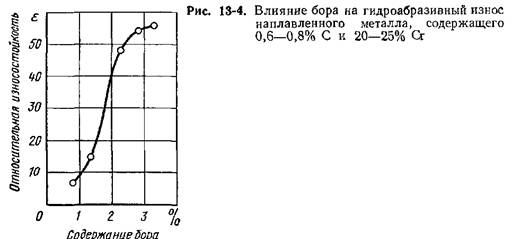
тип наплавленного металла G оказался более износостойким, чем типы А, В, D, QB, не только при малых углах атаки, но и при больших (рис. 13-3, б). Поэтому при выборе наиболее износостойкого металла необходимо учитывать не только угол атаки, но и свойства абразива.
Гидроабразивный износ во многом сходен с газоабразивным, но носителем абразивных частиц является не газ, а жидкость. Гидроабразивному износу подвергаются рабочие колеса и улитки земснарядов и Песковых насосов, лопасти и камеры гидротурбин, работающие на реках, несущих большое количество абразивных частиц, а также пульпопроводы гидротранспорта. Интенсивность гидроабразивного износа во многом зависит от условий обтекания детали жидкостью, которые в конечном счете определяют углы встречи абразивной частицы с изнашиваемой поверхностью.
Для оценки гидроабразивной износостойкости наплавленного металла в улитку насоса земснаряда, разрабатывавшего песчаные почвы (концентрация в воде песка 10—30%), вмонтировали кассету с наплавленными образцами. По потере массы образца судили об износостойкости наплавленного металла. В каждую кассету монтировали также образец-эталон из стали СтЗ. Испытывали наплавленный металл типов В, С, D и G.
Наиболее высокой износостойкостью обладали высокохромистые чугуны (тип G). Они в 10—60 раз превосходили износостойкость низкоуглеродистой стали. В доэвтектических чугунах увеличение количества эвтектики сопровождалось повышением износостойкости. Еще более высокой износостойкостью обладали за-эвтектические чугуны. Максимальная износостойкость была достигнута для сплава, содержащего 0,7—0,8% С и 20—25% Сг, при дополнительном легировании его бором до 3,0% (рис. 13-4). Наплавленный металл типов А, В, С, D обладал низкой износостойкостью и по величине износа мало отличался от обычной низкоуглеродистой стали. В дальнейшем качественная сторона результатов этих испытаний была полностью подтверждена испытаниями наплавленных деталей землесосов, разрабатывавших песчаные почвы.
Кавитационная эрозия появляется главным образом в результате импульсного механического воздействия гидравлических ударов потока жидкости на поверхность металла. Кавитации подвержены гребные винты, лопасти и камеры проточного тракта гидротурбин, рабочие колеса и камеры различных гидромашин.
Наличие коррозионной среды ускоряет процесс кавитационного разрушения. Поэтому для работы в условиях кавитации применяют коррозионностойкие стали.
Высокой стойкостью против кавитационного разрушения обладают хромистые стали с мартенситной структурой (тип Е). Применение этих сталей для наплавки затруднено из-за появления трещин и необходимости предварительного подогрева деталей. Более технологичны аустенитные хромоникелевые стали 18-8 типа D, но более высокой износостойкостью обладают стали с нестабильным аустенитом, который при микроударном нагружении превращается в мартенсит. К сталям с нестабильным аустенитом относятся 30Х10Г10, Х15Н8, Х13Н9 и др. Наличие в структуре б-феррита снижает кавитационную стойкость, поэтому стали с высоким содержанием хрома (20—25%) хуже противостоят кавитации чем стали с 13—15% Сг.
Высокую кавитационную стойкость имеют нержавеющие мар-тенситостареющие стали 0Х12Н5АМ2Т. Эти стали приобретают необходимые свойства в результате воздействия термического цикла сварки и поэтому специальной термообработки не требуют.
Для наплавки гребных винтов из медных сплавов применяют двухфазные алюминиевые бронзы (10—14% А1). В наплавленных высокоалюминиевых бронзах образуется метастабильная {3-фаза, способная под действием микроударных нагрузок превращаться в мартенситоподобную (J-фазу, обладающую высокими упругими свойствами. Это значительно повышает общую кавитационную стойкость сплава (табл. 13-3),
Сервис онлайн-записи на собственном Telegram-боте
Попробуйте сервис онлайн-записи VisitTime на основе вашего собственного Telegram-бота:
— Разгрузит мастера, специалиста или компанию;
— Позволит гибко управлять расписанием и загрузкой;
— Разошлет оповещения о новых услугах или акциях;
— Позволит принять оплату на карту/кошелек/счет;
— Позволит записываться на групповые и персональные посещения;
— Поможет получить от клиента отзывы о визите к вам;
— Включает в себя сервис чаевых.
Для новых пользователей первый месяц бесплатно.
Зарегистрироваться в сервисе
Термическая усталость — это изменения структуры и формы, сопровождающиеся разрушением материалов в результате действия циклических нагревов и охлаждений. Трещины — наиболее характерный вид разрушения, вызываемый термической усталостью. Трещины возникают на поверхности детали после определенного числа циклов. Их количество непрерывно
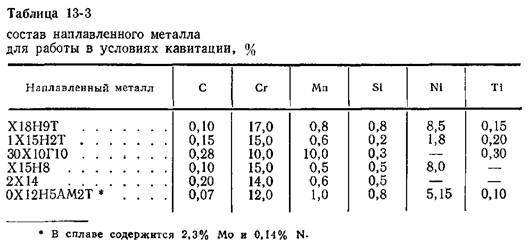
увеличивается с возрастанием числа циклов. В результате образуется сетка трещин, которую часто называют сеткой разгара. Характеристикой сопротивления материалов термической усталости обычно служит число циклов до появления трещин. Стандартная методика испытаний на термическую усталость пока отсутствует, поэтому сравнительные данные получают лишь при определенных параметрах работы испытательного стенда.
Термической усталости подвержены многие детали оборудования и различный инструмент: валки горячей прокатки, штампы для горячей штамповки, пресс-формы для литья под давлением, хоботы завалочных машин, контейнеры для прессования профилей и т. п. С проблемой термической усталости чаще всего приходится сталкиваться при решении задач, связанных с наплавкой прокатных валков и штампов для горячей обработки металлов. Здесь в качестве наплавленного металла традиционным является применение штамповых сталей для горячей обработки, которые в соответствии с классификацией МИС относятся к типу Н (табл. 13-4). Такие детали, как прокатные валки, штампы и другой инструмент для горячей обработки, испытывают не только тепловые удары, которые приводят к трещинам термической усталости, но подвергаются одновременно и износу истиранием. Скорость распространения трещин в глубь металла и скорость истирания могут быть разными. Поэтому на изношенной поверхности детали отразится результат действия процесса, протекающего с большей скоростью, т. е. сетка трещин, либо задиры и риски. Различные типы наплавленного металла обладают разной склонностью к образованию трещин термической усталости и сопротивлением износу.
На рис. 13-5 приведены данные о сопротивлении износу и термической усталости ряда составов наплавленного металла типа Н. Испытания выполнены на машине, позволяющей оказывать одновременное воздействие на поверхность образца циклических теплосмен и трения о металл. Испытываемый образец прижимают к
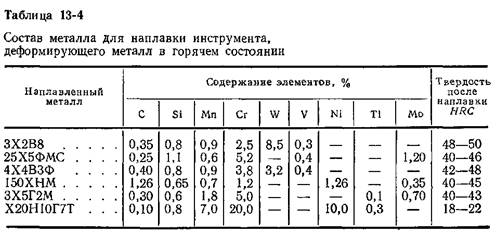
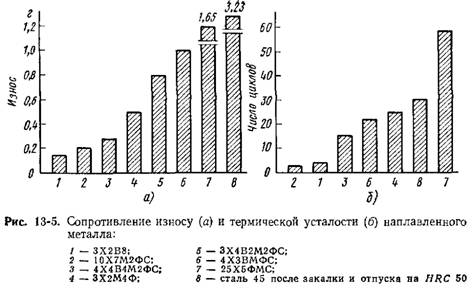
вращающемуся истирающему кольцу с давлением около 10 кгс/мм2, скорость трения 20—22 м/мин. Истирающее кольцо из стали Х18Н10Т нагревают газовой горелкой до температуры 950— 1000° С. Образец в течение 40 с истирается об это кольцо, нагреваясь до температуры 680—710° С, затем отводится и охлаждается струей воды до температуры 180° С, после чего цикл повторяется. На рис. 13-5, а величина износа указана после 200 циклов.
Термическую усталость образцов определяли на этой же установке, но нагреву газовой горелкой до температуры 680° С подвергали не кольцо, а образец, который затем охлаждался водяным душем. На рис. 13-5, б показано число циклов до появления первой трещины.
Износ возрастает при уменьшении в наплавленном металле содержания углерода и легирующих элементов, особенно вольфрама. Сопротивление термической усталости вольфрамовой стали ЗХ2В8 оказалось ниже, чем стали 45 и безвольфрамовой стали 25Х5ФМС. Между тем согласно исследованиям термических циклов службы валков стана 120 поперечно-винтовой прокатки, сопротивляемость образованию трещин наплавленного металла ЗХ2В8 более высокая, чем стали 45. Это указывает на существенное изменение сопротивления наплавленного металла термической усталости в зависимости от условий эксплуатации.
Проводя испытания различных материалов по одной методике и постоянных режимах, можно прийти к ошибочным рекомендациям, если не учитывать конкретных условий службы наплавляемых деталей. Между сопротивлением термической усталости. определяемым числом циклов до появления трещин, и механическими и теплофизическими характеристиками материалов отсутствует
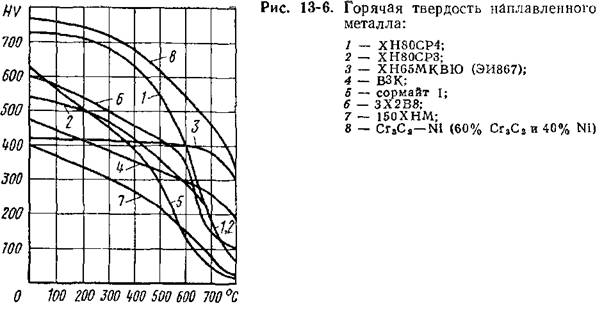
сдостаточно простая корреляция. Тем не менее важно рассмотреть горячую твердость наплавленного металла при работе деталей в условиях повышенных температур.
На рис. 13-6 показана зависимость твердости от температуры для наплавленного металла тех типов, которые обычно используют в условиях повышенных температур и высоких давлений. Твердость с повышением температуры для различных составов наплавленного металла изменяется по-разному. Наиболее высокой твердостью при температурах 500—700° С обладают кобальтовый стеллит, карбидная композиция и жаропрочные сплавы. Эти материалы, как правило, хорошо противостоят износу при повышенных температурах.
Износ при трении металла о металл при нормальных температурах происходит в подшипниках скольжения (коленчатые валы, оси, пальцы ковшовых цепей), а также при трении качения (крановые колеса, детали ходовой части гусеничных машин, скаты вагонеток и т. п.). В узле трения обычно присутствуют абразивные частицы: окалина, песок, руда, частицы наклепанного металла и др. На износостойкость трущейся пары влияет много факторов: соотношение твердости трущихся поверхностей, удельная нагрузка, концентрация и твердость абразива, микроструктура наплавленного слоя. Для наплавки деталей, работающих в этих условиях, чаще всего используют низколегированные стали типов А и В по классификации МИС (15Г2Х, ЗОХГСА, 20Х2Г2М, 50Х5ФТ, ЗХ5Г2М), а в тех случаях, где рабочие поверхности подвержены большим контактным нагрузкам, — самоупрочняющиеся стали с нестабильным аустепитом и др.
|