Технология электрической сварки металлов и сплавов плавлениемМетоды легирования наплавленного слоя
Нужные свойства наплавленного слоя обычно получают легированием, т. е. введением в его состав легирующих примесей. Существует много методов легирования. Методы легирования и способы наплавки взаимосвязаны — выбранный способ наплавки, как правило, диктует рациональный метод легирования, и, наоборот, эффективный метод легирования требует применения соответствующего способа наплавки. С другой стороны, основными признаками, по которым следует оценивать метод легирования, являются: точность (надежность) получения заданного химического состава наплавленного металла при возможных колебаниях режимов наплавки, однородность состава по объему наплавленного слоя, экономичность и удобство применения метода легирования. Что касается экономичности метода легирования, то здесь необходимо учитывать целесообразность применения тех или иных легирующих элементов для данного объекта наплавки и потери этих легирующих элементов при выборе метода легирования.
Легировать сварочную ванну можно за счет обменных реакций между металлом и шлаком (окислами), через газовую среду и путем введения металлических добавок. Примером легирования за счет обменных реакций являются известные кремние- и марган-цевовосстановительные процессы при сварке и наплавке под флюсами АН-348-А, ОСЦ-45, АН-60 и др. Легирование посредством газовой фазы имеет место при дуговой наплавке плавящимся электродом в атмосфере воздуха или азота, когда наплавленный металл содержит заметные количества азота. Благодаря этому повышается износостойкость хромистых сплавов или регулируется количество аустенитной фазы.
Однако эти два процесса легирования для износостойкой наплавки применяют редко, так как они не могут обеспечить необходимый уровень содержания легирующих элементов. Поэтому наибольшее распространение получило легирование путем введения в сварочную ванну металлических сплавов, чистых металлов и металлоподобных соединений. Кинетика растворения металлических добавок и металлоподобных соединений в жидких металлах изучена еще недостаточно.
При ручной наплавке штучными электродами легирование осуществляется введением легирующих элементов в покрытие электрода или в электродный стержень. Применяют и комбинированный метод легирования, когда легирующие примеси вводят и в стержень, и в покрытие.
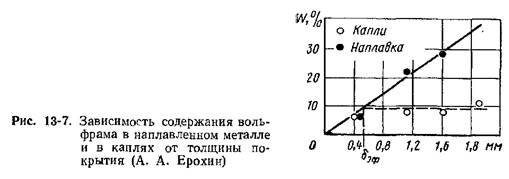
Процессы легирования протекают на стадии капли и в сварочной ванне. Концентрация легирующего элемента в наплавленном металле пропорциональна толщине легирующего покрытия (коэффициенту массы покрытия). При некоторой толщине покрытия, которую А. А. Ерохин назвал эффективной толщиной, процессы
на стадии капли достигают насыщения, и дальнейшее увеличение толщины покрытия не приводит к изменению концентрации элемента в капле (рис. 13-7). Последнее обстоятельство свидетельствует о том, что возрастание концентрации легирующего элемента при увеличении толщины покрытия больше эффективной происходит за счет процессов в сварочной ванне. Эффективная толщина покрытия зависит главным образом от его температуры плавления. Чем больше толщина покрытия отличается (в большую сторону) от эффективной толщины, тем больше вклад ванны в процесс легирования.
Визуальное наблюдение за плавлением электрода и данные скоростной киносъемки показывают, что в этом случае наружные слои покрытия стекают непосредственно в ванну, минуя каплю. Такой характер плавления электрода существенно влияет на результаты легирования. Металлические легирующие добавки покрытия, попадая в хвостовую часть ванны, не успевают полностью раствориться и равномерно распределиться в расплаве. В результате возрастает макрохимическая неоднородность наплавленного металла.
Описанный выше неблагоприятный процесс плавления покрытия электрода можно использовать и для достижения положительного эффекта. Так, создание многослойного покрытия, в котором износостойкие частицы расположены в наружном слое, позволит в известной степени избежать их растворения в расплаве, что уменьшит охрупчивание матрицы сплава и сохранит износостойкие частицы от разрушения при высоких температурах дуги. Внутренний слой покрытия должен быть достаточно тугоплавким, чтобы уменьшить эффективную толщину покрытия.
При электродуговой наплавке под флюсом применяют следующие методы легирования: I — применение легированной электродной проволоки или ленты (в том числе и металлокерамиче-ской ленты) и плавленого флюса; II — присадка легирующих материалов через проволоку или ленту (порошковую проволоку или ленту, проволоку с армированным легирующим покрытием и др.), плавленый флюс; III — использование низкоуглеродистой проволоки или ленты и легирующего флюса (керамического флюса, механической примеси ферросплавов к флюсу); IV — наплавка по неподвижной присадке в виде прутка, ленты, порошка, пасты с полным расплавлением присадки.
Ни один из этих методов не встречается в чистом виде: электродный материал всегда в какой-то степени взаимодействует со шлаком и часть элементов переходит в наплавленный металл из флюса. При использовании легирующего флюса часть примесей может вноситься электродным материалом.
При наплавке под флюсом изменение параметров режима наплавки (силы тока, напряжения дуги, скорости наплавки, диаметра и вылета электрода) изменяет количество шлака, приходящееся на единицу массы расплавившегося электрода (относительная масса шлака), а также кинетические условия взаимодействия металла и шлака на стадии капли. Характер влияния этих изменений на процесс легирования зависит от того, что является основным источником поступления легирующих элементов — электродный материал или флюс.
При легировании через проволоку и наплавке под химически активными флюсами — силикатами (АН-348-А, ОСЦ-45, АН-60) увеличение относительной массы шлака, происходящее при повышении напряжения дуги или уменьшении силы тока, сопровождается окислением легирующих элементов и легированием сварочной ванны кремнием и марганцем из флюса. Указанные изменения режима наплавки сопровождаются изменением и кинетических условий взаимодействия фаз на стадии капли: возрастает время существования капли и ее взаимодействие с окислительным шлаком. В результате при изменении режимов наплавки изменяется и химический состав наплавленного металла.
При наплавке под менее активными флюсами влияние относительной массы шлака на процессы окисления и легирования уменьшается; этому способствует меньшая окислительная способность флюса и то обстоятельство, что обычно не вся масса жидкого шлака взаимодействует с металлом. Меньшее влияние на химический состав наплавленного металла оказывают и кинетические условия. Таким образом, при легировании через проволоку влияние режима на химический состав наплавленного металла тем меньше, чем меньше окислительная способность применяемого флюса.
Забиваем Сайты В ТОП КУВАЛДОЙ - Уникальные возможности от SeoHammer
Каждая ссылка анализируется по трем пакетам оценки: SEO, Трафик и SMM.
SeoHammer делает продвижение сайта прозрачным и простым занятием.
Ссылки, вечные ссылки, статьи, упоминания, пресс-релизы - используйте по максимуму потенциал SeoHammer для продвижения вашего сайта.
Что умеет делать SeoHammer
— Продвижение в один клик, интеллектуальный подбор запросов, покупка самых лучших ссылок с высокой степенью качества у лучших бирж ссылок.
— Регулярная проверка качества ссылок по более чем 100 показателям и ежедневный пересчет показателей качества проекта.
— Все известные форматы ссылок: арендные ссылки, вечные ссылки, публикации (упоминания, мнения, отзывы, статьи, пресс-релизы).
— SeoHammer покажет, где рост или падение, а также запросы, на которые нужно обратить внимание.
SeoHammer еще предоставляет технологию Буст, она ускоряет продвижение в десятки раз,
а первые результаты появляются уже в течение первых 7 дней.
Зарегистрироваться и Начать продвижение
Продолжительность взаимодействия капли с окружающей средой и относительная масса шлака уменьшаются при увеличении силы сварочного тока, кроме того, относительная масса шлака уменьшается при увеличении скорости наплавки. Поэтому изменение химического состава наплавленного металла в зависимости от изменения режима наплавки меньше в области больших токов и больших скоростей наплавки. Эти процессы относятся к верхним слоям многослойной наплавки, когда влияние основного металла и его доли в наплавленном невелики.
Рассмотрим кратко особенности легирования, когда основным источником поступления легирующих элементов (в виде металлических добавок) является флюс. Как и при легировании через проволоку, наиболее важным является взаимодействие фаз на стадиях капли и сварочной ванны. При плавлении электрода под слоем легирующего флюса капли на конце электрода имеют уже значительный уровень легирования. Доля легирования на стадии капли (содержание элемента в капле по отношению к его содержанию в наплавленном металле) зависит от концентрации легирующего элемента во флюсе и от режима наплавки.
При увеличении напряжения дуги и уменьшении силы тока, когда относительная масса шлака возрастает, содержание легирующих элементов в капле остается примерно постоянным.
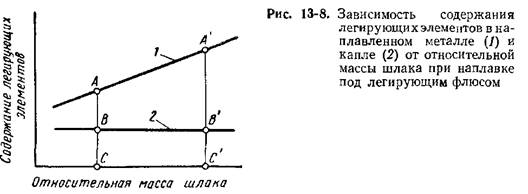
В этих же условиях уровень легирования наплавленного металла повышается (рис. 13-8), и доля легирования на стадии капли убывает: ВС/АС > ^>BrCIACf. Незначительное влияние режима наплавки на состав капли, по-видимому, связано с тем, что с каплей взаимодействует сравнительно небольшая и постоянная доля расплавившегося флюса и что в условиях высоких температур и интенсивного перемешивания взаимодействующих фаз процесс обогащения капли легирующими элементами успевает пройти достаточно полно. Таким образом, при наплавке под легирующим флюсом влияние режима наплавки на состав наплавленного металла происходит, в основном, через процессы, протекающие на стадии ванны. После расплавления легирующего флюса, состоящего из смеси ферросплавов и шлакообразующих материалов, ввиду весьма ограниченной растворимости металлов в шлаке образуется дисперсная система, в которой дисперсионной средой является шлак, а дисперсной фазой — металл. Происходит коагуляция и слияние металлических частиц и осаждение их в сварочную ванну, причем часть частиц успевает достичь сварочной ванны, а часть застревает и (при соответствующих условиях) окисляется в шлаке. Потери в шлаковой корке зависят от физико-химических свойств как шлака, так и осаждающихся частиц. Так, при введении в виде механической примеси порошков никеля и вольфрама в малоокислительный флюс 48-ОФ-6 потери никеля выше, чем вольфрама. Это объясняется большей плотностью вольфрама. При этом на процесс осаждения частиц из шлака в сварочную ванну влияет и вязкость шлака. Потери в шлаковой корке находятся в обратной зависимости от продолжительности пребывания шлака и сварочной ванны в жидком состоянии, если шлак обладает малоокислительными свойствами.
Стабильность химического состава наплавленного металла обеспечивается в том случае, если увеличение расхода источника легирования, например относительной массы шлака, компенсируется повышением потерь легирующих элементов в результате окисления и застревания в шлаке. Поэтому стабильность химического состава наплавленного металла при разных режимах наплавки можно повысить, применив легирующий флюс с повышенной окислительной способностью, хотя этот путь с точки зрения экономии легирующих элементов невыгоден. При легировании же через проволоку такое решение ведет к уменьшению стабильности состава наплавленного металла. Изменение потерь в шлаковой корке при разных режимах наплавки не всегда происходит в нужном направлении, и управлять этими потерями с целью получения стабильного состава наплавленного металла очень трудно.
При наплавке под легирующим флюсом электродной лентой сила тока и напряжение дуги влияют на относительную массу шлака незначительно. Поэтому при наплавке электродной лентой в отличие от наплавки проволочным электродом обеспечивается более стабильный химический состав наплавленного металла.
Потери легирующих элементов в шлаковой корке существенно возрастают при их высоком содержании во флюсе, и это свидетельствует о нецелесообразности применения легирующих флюсов (керамических, флюсов-смесей) для получения высоколегированного наплавленного металла.
При наплавке плавящимся электродом по неподвижной легирующей присадке в виде порошка, пасты и т. п. количество присадки выбирают так, чтобы она вся переплавлялась дугой. Наплавку обычно производят под плавленым флюсом низкоуглеродистой проволокой. Благодаря энергичному перемешиванию металла в сварочной ванне примесь, введенная указанным путем, распределяется равномерно по сечению наплавленного слоя. При равномерном распределении примеси по длине наплавляемого валика можно получить наплавленный металл заданного состава.
Если на изделие нанесено заданное количество легирующего материала, то химический состав наплавленного металла в значительной мере зависит от скорости подачи электродной проволоки (силы тока) и скорости наплавки. Это обусловлено тем, что на единицу массы легирующего элемента будет приходиться разное количество электродного металла, разбавляющего присадочный. Кроме того, состав наплавленного металла зависит от напряжения дуги, что обусловлено изменением относительной массы шлака. Поэтому заданный химический состав наплавленного металла можно получить в весьма ограниченном диапазоне режимов.
Для оценки точности получения наплавленного металла заданного состава при различных методах легирования и изменении режимов наплавки И. И. Фрумин предложил диаграмму, построенную в координатах сила тока — напряжение. На эту диаграмму наносят линии равных концентраций того или иного элемента — изоконцентраты. Зная предельно допустимые максимальные и минимальные содержания элементов для данного сплава и нанося их в виде изоконцентрат на указанную диаграмму, получают область режимов, характеризующую точность метода легирования.
Чем шире диапазон режимов, при котором обеспечиваются допустимые отклонения в составе наплавленного металла, тем надежнее метод легирования. Диаграмма на рис. 13-9 показана для металла ЗХ2В8, наплавленного под флюсом с использованием перечисленных выше четырех методов легирования. По уменьшению
Сервис онлайн-записи на собственном Telegram-боте
Попробуйте сервис онлайн-записи VisitTime на основе вашего собственного Telegram-бота:
— Разгрузит мастера, специалиста или компанию;
— Позволит гибко управлять расписанием и загрузкой;
— Разошлет оповещения о новых услугах или акциях;
— Позволит принять оплату на карту/кошелек/счет;
— Позволит записываться на групповые и персональные посещения;
— Поможет получить от клиента отзывы о визите к вам;
— Включает в себя сервис чаевых.
Для новых пользователей первый месяц бесплатно.
Зарегистрироваться в сервисе
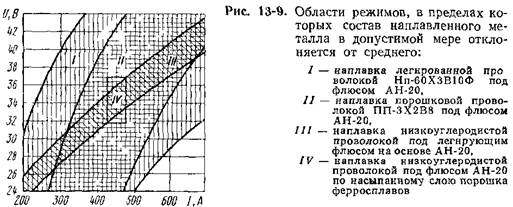
точности и надежности рассматриваемые методы легирования расположены в таком порядке: I, II, III, IV.
При электрошлаковой наплавке, когда расход флюса невелик, приемлемы методы легирования I и II. При этом используют кованые, катаные и литые электроды большого сечения. При механизированной наплавке открытой дугой легирование сварочной ванны осуществляют легированной или порошковой проволокой, подаваемой в дугу либо в качестве плавящегося электрода, либо присадки. Так, при плазменной наплавке в зависимости от примененного способа легирующие примеси вводят в токоведущую или присадочную проволоку (порошковую и легированную), в неподвижную присадку (проволоку, ленту, пасту, порошок, литые или металлокерамические присадки) и в порошок, вдуваемый в плазму.
Важной характеристикой процесса легирования является однородность химического состава наплавленного металла по объему, которая обусловлена, в первую очередь, равномерностью распределения легирующих элементов в самом электродном материале. Так, при исследовании при помощи метода математической статистики распределения легирующих элементов в наплавленном слое установлена разная степень однородности состава металла, наплавленного под флюсом холоднокатаной, металлокерамической и порошковой лентами. Металлокерамическая и холоднокатаная ленты дают наплавленный металл примерно с одинаковой однородностью. При наплавке порошковой лентой (конструкции, показанной на рис. 13-10, в) шириной 45 мм наплавленный металл менее однороден.
При выборе способа легирования необходимо учитывать много факторов. Так, требования к стабильности и однородности состава металла при наплавке коррозионностойких слоев и инструментальных сталей должны быть выше, чем при наплавке, например, износостойких слоев деталей, перерабатывающих горные породы. Порошковая проволока и тем более металлокерамическая лента дороже низкоуглеродистой и среднелегированной проволоки сплошного сечения. Применение этих сравнительно дорогостоящих материалов оправдывается в тех случаях, если необходимо получить легированный наплавленный металл со стабильным химическим составом- При наплавке по слою гранулированного порошка используют сравнительно недорогие материалы (порошок сормайта, сталинита), но этот метод малопригоден для деталей сложной формы и неприменим в тех случаях, когда требуется большая стабильность состава наплавленного металла.
Для решения многих задач легирования при дуговой наплавке особенно перспективны порошковая проволока, а также металло-керамическая и порошковая ленты.
|