Технология электрической сварки металлов и сплавов плавлениемНаплавка плоских поверхностей
При наплавке плоских поверхностей, например защитных листов бункерных устройств, ножей для резки металла, ножей бульдозеров и т. д., требуется наплавить возможно большую площадь при наименьшей глубине про-плавления основного металла и минимальном короблении деталей. Простейший способ наплавки под флюсом — наплавка отдельных валиков на таком расстоянии друг от друга, чтобы не нужно было удалять шлаковую корку отдельно с каждого валика. Шлак удаляют со всех валиков сразу, затем наплавляют валики в свободных промежутках, чтобы получить по возможности ровную поверхность. При таком способе много времени затрачивается на насыпание и удаление флюса. Провар основного металла получается глубокий, в результате чего возникает значительное коробление изделия.
Более совершенна широкослойная наплавка, когда электроду сообщено поперечное колебательное движение и в каждом крайнем положении совершается дополнительное движение электрода или изделия на шаг наплавки. Электрод при этом возвращается к краю наплавляемой полосы до затвердевания шлаковой корки. В зависимости от режима и вязкости применяемого шлака возможна наплавка полосы шириной до 400 мм без удаления шлаковой корки и насыпанного флюса. Глубина проплавления в данном случае может быть уменьшена по сравнению с наплавкой отдельными валиками, кроме того, меньше затраты времени на удаление шлаковой корки.
Более производительны многоэлектродная наплавка и наплавка электродной лентой (табл. 13-14 и 13-15). Наплавка лентой — более надежный процесс благодаря более простой конструкции механизма подачи электрода.
Износостойкую наплавку плоских поверхностей целесообразно также выполнять порошковой проволокой и лентой открытой дугой, сообщая электроду поперечные колебания с необходимым размахом. Так как в данном случае отсутствует шлаковая корка большой толщины, то размах колебаний электрода практически
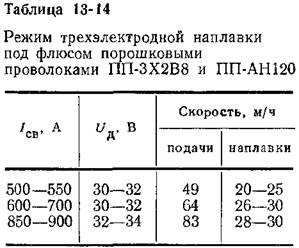
неограничен. Это обстоятельство, а также отсутствие затрат времени на удаление шлаковой корки и уборку флюса позволяют дополнительно повысить производительность наплавки. При наплавке с поперечными колебаниями электрода наплавляемая полоса может образовываться из общей ванны или из отдельно сформированных поперечных валиков.
Наплавку с общей ванной применяют, если требуется
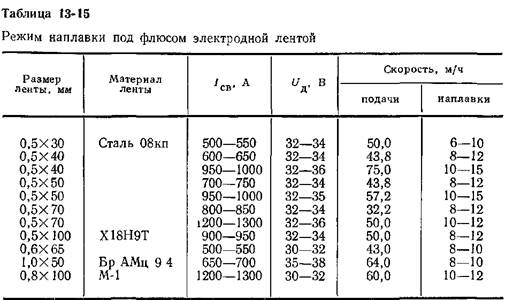
наплавлять сравнительно узкие полосы (до 100 мм), так как при больших размерах сварочной ванны во избежание стекания жидкого металла наплавляемую деталь необходимо устанавливать в строго горизонтальном положении. Кроме этого, особенно при наплавке чугуна на сталь, возможно образование трещин с большим раскрытием и неблагоприятной ориентацией по отношению к разрушающим нагрузкам. При необходимости наплавить за один проход широкие полосы целесообразна наплавка с формированием отдельных валиков.
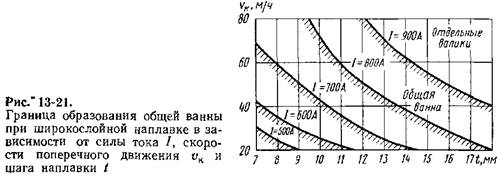
На рис. 13-21 представлены границы образования общей ванны при широкослойной наплавке открытой дугой порошковой лентой ПЛ-АН101 (см. табл. 13-8 и 13-9) с размахом колебаний электрода 200 мм. При уменьшении скорости колебаний электрода и шага наплавки, а также при увеличении силы тока дуги образуется общая ванна. При прочих равных параметрах режима этому способствует и уменьшение размаха колебаний. Шагом наплавки в данном случае называется величина перемещения электрода в направлении, перпендикулярном к направлению колебательного движения электрода. Шаг осуществляется в каждом крайнем положении электрода.
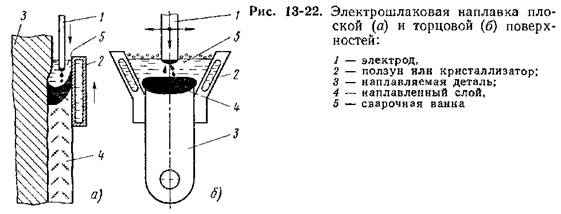
Электрошлаковую наплавку плоских поверхностей можно производить при вертикальном, нижнем и наклонном положениях наплавляемой поверхности. В качестве электродного материала используют проволоку сплошного сечения или порошковую, а также прокат различного профиля и литые стержни (рис. 13-22, а). Поперечные колебания электрода происходят по всей ширине детали. Для получения устойчивого электрошлакового процесса необходимо, чтобы глубина шлаковой ванны была не менее 30 мм. При уменьшении глубины ванны до 10—15 мм электрошлаковый процесс переходит в дуговой либо перемежающийся, при этом возможно образование непроваров.
Торцовые поверхности можно наплавлять электродом большого сечения (рис. 13-22, б). Шлаковая ванна наводится с помощью электропроводного флюса АН-25. Для получения полного сплавления наплавленного слоя с основным необходимо, чтобы площадь поперечного сечения электрода была примерно равна площади наплавляемой поверхности. В противном случае для получения полного сплавления необходимо применять электрод переменного сечения либо сообщать электроду соответствующее перемещение по наплавляемой поверхности.
Наплавка деталей сложной формы. При наплавке деталей сложной формы возможность визуального наблюдения за дугой и управление ею имеют большое значение. Наплавка под флюсом, несмотря на ряд преимуществ, исключает визуальное наблюдение за формированием валиков, часто требует использования различных флюсоудерживающих и формирующих устройств, вызывает пока непреодолимые трудности при работе в различных пространственных положениях.
Еще не найдены надежные и универсальные технические решения для механизации процесса удаления шлаковой корки, и в большинстве случаев для выполнения этой операции требуется тяжелый ручной труд. Поэтому длительное время применялась малопроизводительная ручная наплавка штучными электродами. В последние годы при восстановлении и упрочнении многих деталей сложной формы, а также деталей малого диаметра и глубоких внутренних поверхностей широкое применение нашла автоматическая и полуавтоматическая наплавка самозащитной порошковой проволокой, разработанной в ИЭС им. Е. О Патона. Простота
процесса, маневренность и возможность получения практически любого состава наплавленного металла, а также в 3—5 раз более высокая производительность по сравнению с наплавкой штучными электродами способствовали быстрому распространению этого способа наплавки.
Образующаяся на поверхности валиков тонкая пленка шлака не мешает наложению очередных валиков, а значит нет необходимости непрерывно удалять шлаковую корку. Это позволяет одному оператору обслуживать при автоматической наплавке несколько аппаратов. При наплавке крупных деталей вместо порошковой проволоки используют близкую по составу порошковую ленту, что дает дополнительный выигрыш в производительности. Наплавку сложных деталей также выполняют порошковой или сплошной проволокой в защитных газах.
Забиваем Сайты В ТОП КУВАЛДОЙ - Уникальные возможности от SeoHammer
Каждая ссылка анализируется по трем пакетам оценки: SEO, Трафик и SMM.
SeoHammer делает продвижение сайта прозрачным и простым занятием.
Ссылки, вечные ссылки, статьи, упоминания, пресс-релизы - используйте по максимуму потенциал SeoHammer для продвижения вашего сайта.
Что умеет делать SeoHammer
— Продвижение в один клик, интеллектуальный подбор запросов, покупка самых лучших ссылок с высокой степенью качества у лучших бирж ссылок.
— Регулярная проверка качества ссылок по более чем 100 показателям и ежедневный пересчет показателей качества проекта.
— Все известные форматы ссылок: арендные ссылки, вечные ссылки, публикации (упоминания, мнения, отзывы, статьи, пресс-релизы).
— SeoHammer покажет, где рост или падение, а также запросы, на которые нужно обратить внимание.
SeoHammer еще предоставляет технологию Буст, она ускоряет продвижение в десятки раз,
а первые результаты появляются уже в течение первых 7 дней.
Зарегистрироваться и Начать продвижение
Для изготовления деталей с торцовой наплавкой сложной формы используют прием стыко-шлаковой наплавки (рис. 13-23). Процесс начинается наведением шлаковой ванны на дне водо-охлаждаемой формы. Электродом служит хвостовик детали с приваренной пластиной или прутком из легированного металла, которые и расплавляются в первую очередь. В момент погружения хвостовика в шлак скорость подачи сперва уменьшают (для прогрева торца детали), а затем увеличивают до погружения детали в металлическую ванну. Происходит сварка хвостовика и отливки. Таким приемом успешно наплавляют зубья экскаваторов.
|