Обмотока машин постоянного и переменного токаИзготовление катушек статорных двухслойных обмоток
Заготовка катушек
Намотка двухслойных катушек обмотки ведется на обыкновенном лобовом станке, к планшайбе которого прикрепляется специальное раздвижное приспособление, подобное рассмотренному нами раньше (рис. 8-3).
Чтобы намотать катушки этой обмотки, имеющей вид, показанный на рис. 9-22, производят подсчет длины растянутого шаблона, на который следует установить кулачки в намоточном приспособлении.
Пусть, например, общая длина катушки будет состоять из следующих составных частей: прямой части 480 мм, плюс две

длины лобовых частей по 145 мм = 290 мм, плюс две длины закруглений при переходе от прямой пазовой части к лобовой по 2,5 мм = 5 мм.
480 + 290 + 5 = 775 мм.
Следовательно, кулачки приспособления следует установить друг от друга на расстоянии 775 мм. Внутренний радиус головок принимается равным 10 мм. Следовательно, расстояние между внутренними сторонами головок (по диаметру) должно быть равно 20 мм. Радиус головок со стороны выводов делается обычно больше (около 12,5 мм). Установив по месту и закрепив планкой кулачки, приступают к намотке катушек. Слабое натяжение проводника при намотке может вызвать увеличение размеров лобовых частей катушки. Начало проводника прикрепляется ручными тисочками к раме раздвижного приспособления. Дольше намотка производится поперечной укладкой с горизонтальными прокладками. В процессе намотки в головках лобовых частей прокладывают электрокартонные прокладки.
После намотки катушки скрепляют как в прямой части, так и в лобовых частях хлопчатобумажной лентой, ранее подложенной под первые витки. Затем катушки с длиной витка до 1000 мм могут растягиваться на этом же приспособлении, а при длине витка более 1000 мм растяжка с целью придания формы катушке производится на специальных ручных растяжных станках (рис. 9-23).

Растяжной станок в основном состоит из станины, на которой смонтирован вал 1 с установленными на нем стойками 2, пазовыми зажимами 3 и головко-держателями 4.
Катушка (лодочка) закладывается сначала в головки.5, затем в пазовые зажимы 3. При вращении поворотного плеча 6 происходит растяжка катушки на заданный шаг и угол разворота пазовых частей катушки.
Во время растяжки головкодержатели 4 сближаются до стопорных колец 7, которые служат ограничителями растяжки. В настоящее время ручные растяжные станки заменяются пневматическими, на которых можно растягивать катушки любого размера.
6. Рихтовка и компаундировка катушек
Снятые с намоточного станка и покрытые хлопчатобумажной лентой катушки не имеют еще тех очертаний, какие необходимы при укладке их в пазы статора. Для придания им соответствующей формы в лобовых и пазовых частях производится рихтовка, которая состоит из трех основных операций:
отгиб лобовых частей на шаблоне;
основная рихтовка пазовых и лобовых частей на шаблоне;
вывертка катушек после рихтовки на макете.
Лобовые части растянутых катушек находятся в одной плоскости с пазовыми частями. Для отгиба лобовых частей катушек применяются шаблоны с пазами, в которые вкладываются лобовые части катушек. Отгиб головок производится вручную на угол, достаточный для того, чтобы уложенные в пазы статора катушки не были выше активной стали. Основная рихтовка производится на специальном деревянном шаблоне (рис. 9-24) или на селуминовом, который более практичен.
В пазы шаблона катушка вставляется прямыми пазовыми частями. Поворотными планками, находящимися сверху пазов,

шаблон закрывается, после чего рихтуются лобовые части. Для этого пользуются деревянным или фибровым клином и ручником, которым подгоняют лобовые части вплотную к стенкам шаблона.
Благодаря рихтовочному шаблону лобовые части имеют соответствующую кривизну, пазовые части получают необходимый поворот сторон катушки (по пазам статора). Правильность рихтованной катушки выверяется на деревянном макете, представляющем собой часть стали статора. Неправильная рихтовка ведет к большим механическим усилиям при закладке сторон катушек в пазы, что влечет за собой повреждение основной изоляции.
После рихтовки катушки подвергаются компаундировке, выполняемой таким образом, как и компаундировка однослойных обмоток.
Определение размеров шаблона для рихтовки катушек двухслойной статорной обмотки
На рис. 9-25 показаны основные размеры шаблонов, которые определяются по формулам, приведенным в табл. 9-2.
Пример определения размеров шаблона обмотки. Определим размеры шаблона для катушки, показанной на рис. 5-27:
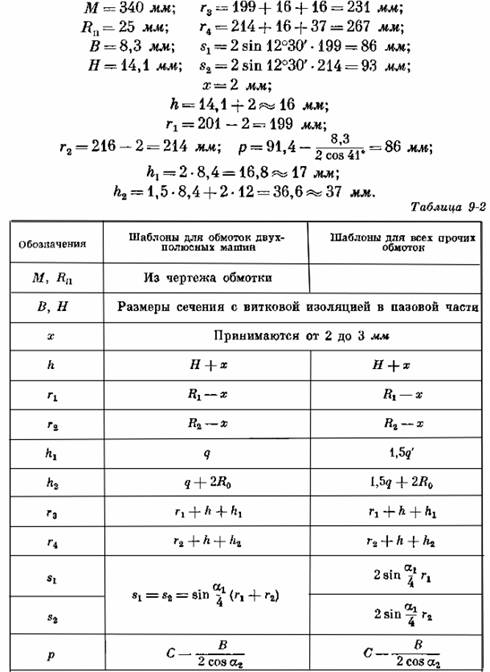
принимается равным 20 мм.
Все размеры при расчете округляются с точностью до 1 мм:
г. О прессовка
нахлестки. При опрессовке
пазовых частей после компаундировки удаляются излишки компаундной массы, выпрямляются витки на прямых частях и пазовые части доводятся до требуемого размера.
Для опрессовки служит пароводяной гидравлический пресс (рис. 9-5). Пресспланки и способ прессования такой же, как описанный ранее.
В современном производстве применяются также и пневматические прессы с пароводяными плитами.
Ручная прессовка обмоток может также производиться в винтовых прессах, но это не обеспечивает необходимой монолитности витков и получения равномерных размеров по всей длине.
После полного охлаждения катушка вынимается из пресса, подвергается рихтовке на деревянном шаблоне и проверке по макету, потом испытанию на электрическую прочность витковой изоляции по существующим нормам для данной конструкции.
Затем снимается киперная лента, и катушки отправляются для наложения корпусной изоляции, которая выполняется гильзовым или непрерывным способами.
Забиваем Сайты В ТОП КУВАЛДОЙ - Уникальные возможности от SeoHammer
Каждая ссылка анализируется по трем пакетам оценки: SEO, Трафик и SMM.
SeoHammer делает продвижение сайта прозрачным и простым занятием.
Ссылки, вечные ссылки, статьи, упоминания, пресс-релизы - используйте по максимуму потенциал SeoHammer для продвижения вашего сайта.
Что умеет делать SeoHammer
— Продвижение в один клик, интеллектуальный подбор запросов, покупка самых лучших ссылок с высокой степенью качества у лучших бирж ссылок.
— Регулярная проверка качества ссылок по более чем 100 показателям и ежедневный пересчет показателей качества проекта.
— Все известные форматы ссылок: арендные ссылки, вечные ссылки, публикации (упоминания, мнения, отзывы, статьи, пресс-релизы).
— SeoHammer покажет, где рост или падение, а также запросы, на которые нужно обратить внимание.
SeoHammer еще предоставляет технологию Буст, она ускоряет продвижение в десятки раз,
а первые результаты появляются уже в течение первых 7 дней.
Зарегистрироваться и Начать продвижение
Выполнение гильзовой изоляции на 6000 и 3000 в
Опишем сначала выполнение изоляции катушки для напряжения 6000 в. Начинается она с изолировки перехода от пазовой к лобовой части (рис. 9-26). Как уже было сказано, этот переход является наиболее ответственным и опасным (в отношении пробоя) местом. В гл. 5 была описана конструкция изоляции этого перехода.
Предварительно изолируется головка катушки пятью слоями лакированной ленты вполнахлестку, причем первый слой накладывается по всей головке, с заходом по 45—50 мм на прямые части.

Отступя на 9—10 мм от конца первого слоя, накладывают второй слой, который не доводят до конца первого слоя тоже на 9—10 мм. Третий слой накладывается с таким же смещением по отношению ко второму слою. Так накладывают пять слоев лакированной ленты.
После наложения изоляции на головку изолируется прямая часть лобовой части катушки. Здесь применяется микалента. Первый слой микаленты начинается непосредственно от конца первого слоя лакированной ленты изоляции головки и ведется вполнахлестки, с заходом по направлению к стали машины на 45—50 мм на прямую часть катушки. Второй слой микаленты накладывается от конца второго слоя лакированной ленты изоляции головки и, таким образом, перекрывает первый слой микаленты на 9—10 мму но не доводится на 9—10 мм до конца первого слоя микаленты. С такими же уступами в начале ив конце накладываются еще три слоя микаленты. Таким образом изолируются все четыре перехода от прямой к лобовой части катушки.

Выводные концы сначала изолируют пятью слоями лакированной ленты. Затем производят изолировку двух прямых частей катушки (включая и пазовую часть) наложением на них микафолия для образования гильз. Длину листа определяют, исходя из среднего периметра гильзы, как это было описано в § 9-1. Так как гильза должна перекрыть ступенчатый переход изоляции лобовой части, то заготовка микафолия производится таким образом, чтобы при обертывании катушки листы микафолия перекрывали последовательно уступы слоев изоляции лобовой части. Для этого в листе микафолия с обеих его сторон делают вырезы в виде ступеней или скашивают их. В нашем случае это скашивание должно быть равно 45—50 мм с каждой стороны.
Каждый оборот накладываемого микафолия проутюживается двумя работницами. Одна из них утюжит, а вторая для равномерного прилегания микафолия и устранения складок плотно приглаживает место утюжки сухой тряпкой отрывистыми движениями рук по направлению накладывания микафолия.
Как было указано ранее, более качественное наложение микафолия получается, когда листы его размягчаются на горячей плите при температуре 70—80° С и обертываются вокруг изолируемой стороны катушки, затем эта сторона закладывается в обкаточный станок. При утюжке получается излом изоляции, морщинистость, неплотности. Проглаживание по микафолию сухой тряпкой не устраняет полностью эти дефекты.
Обкатка — наиболее совершенный способ наложения микафо-лиевой изоляции.
После наложения микафолия катушки поступают на вторую опрессовку, которая производится в тех же пароводяных прессах, но в коробчатых пресспланках (рис. 9-27), внутренний размер которых равен размеру опрессованной катушки.
Стороны катушек выдерживаются в прессах до размягчения лаковой основы в микафолиевой гильзе. Затем для скорейшего остывания катушки через плиты пропускается вода. Катушка остается в прессах до полного остывания. После опрессовки микафолиевой изоляции с концов ее осторожно удаляют ножом или отпаривают утюгом компаунд или лаковую основу, и катушки поступают на дальнейшую изолировку лобовой части и головок. На лобовую часть накладывают ленту из лакоткани толщиной 0,2 мм на небольшом участке и затем поверх нее накладывают еще один оборот лакоткани вполнахлестки той же толщины. Слои лакоткани накладываются на микафолиевую опрессовку примерно над местом начала первого слоя лакоткани, который наложен под микафолием, и ведутся вполнахлестки до той же точки на другой стороне, причем изолировка головки выполняется в 3/4 нахлестки. Лакоткань доводят до второй стороны катушки и закрепляют ее здесь, отступя 16 мм от края прессовки.
Поверх лакоткани накладывается хлопчатобумажная лента толщиной 0,22 мм от опрессовки до середины головки с той или другой стороны лобовых частей. Ленту закрепляют шеллачным или бакелитовым лаком.
После выполнения изоляции лобовая часть прокрашивается быстросохнущим лаком два раза: катушка считается готовой и передается на испытание электрической прочности пазовой изоляции, а также на витковое испытание.
При выполнении изоляции на 3000 в толщина наложенного микафолия на пазовую часть должна быть порядка 1,5 мм. Внутренний конус выполняется двумя слоями микаленты вполнахлестки. На микафолиевую опрессовку накладывается один слой лакоткани и один слой тафтяной ленты толщиной 0,22 мм.
Конус выполняется также уступами на длине 16 мм; второй слой накладывают, отступая от первого на 9 мм. Толщина листов микафолия берется 0,25—0,30 мм.
Изолировка концов выполняется двумя слоями лакоткани и одним слоем тафтяной ленты.
Процессы наложения микафолиевой изоляции и выполнение конуса аналогичны описаннным (для изоляции при напряжении 6000 в).
В настоящее время внедряется термореактивная гильзовая изоляция из стеклослюдинитового полотна толщиной 0,17 мм марки ЛТСС, обозначение букв в марке: Л — лента; Т — термореактивная; С — слюдинит; С — стеклополотно на термореактивном эпоксидно-идитоловом лаке.
Двусторонняя толщина изоляции для напряжения 6000 в — 4,5 мм. Поверх гильзы стеклянная лента марки ЛЭС толщиной 0,2 мм, наложенная впритык.
Витковая изоляция выполняется из слюдопластоленты — 1 слой вполнахлеста. На лобовые части и выводные концы ста-торной катушки накладывается эластичная изоляция: слюдопла-столента, эскапоновая лента. Выполнение общей изоляции начинается с изолировки головок и выводных концов. Головки, выводные концы и половина лобовых частей катушки изолируются 5-ю слоями вполнахлеста липкой синтетической лентой марки ЛСЭЛ толщиной 0,19 мм, сводя изоляцию на конус около 25 мм на 1/2 длины лобовой части. Оставшаяся половина лобовых частей и уголки изолируются 6-ю слоями синтетической лентой в х/2 нахлеста с заходом на пазовую часть, не доходя до железа на */2 вылета. Выводные концы после изолировки катушки прибандажируются к лобовым частям стеклянной лентой, а в местах отгиба чулком АСЭЧ диаметром 2 мм.
Сервис онлайн-записи на собственном Telegram-боте
Попробуйте сервис онлайн-записи VisitTime на основе вашего собственного Telegram-бота:
— Разгрузит мастера, специалиста или компанию;
— Позволит гибко управлять расписанием и загрузкой;
— Разошлет оповещения о новых услугах или акциях;
— Позволит принять оплату на карту/кошелек/счет;
— Позволит записываться на групповые и персональные посещения;
— Поможет получить от клиента отзывы о визите к вам;
— Включает в себя сервис чаевых.
Для новых пользователей первый месяц бесплатно.
Зарегистрироваться в сервисе
Есть и другой вариант: до наложения гильзы 3 слоя слюдо-пластоленты и 2 слоя синтетической ленты, после гильзы — 2 слоя синтетической ленты.
Заготовка полотна, рассчитанная, как ранее описано, для микафолия с учетом +30%, на уплотнение изоляции при опрессовке. Материал кладется стеклянной подложкой книзу на электроплиту с температурой 60—70° С и прогревается в течение 5—10 сек, затем обертывается вокруг пазовой части, поверх 3—4 оборота парафинированной бумаги и закладывается между плитами обкаточного станка для обкатки при температуре 220—240° С в течение 5—10 мин (в зависимости от габаритов катушки). Удельное давление нажимных утюгов 30—40 кГ/см2. После этого сторона катушки закладывается в холодный пресс и под давлением 25—35 кГ/см2 охлаждается. Размер прессиланок подбирают на 0,5 мм меньше номинального размера высоты сечения стороны катушки. То же повторяют со второй стороной катушки. После этого производится окончательная изолировка и замотка киперной лентой по всей длине катушки.
Подготовка к компаундировке. Ранее подготовленные картонные прокладки толщиной 0,2 мм, шириной по высоте катушки, длиной равные всей прямолинейной части катушки, пропитанные в 10% растворе каучука в толуоле (СКТ), для лучшего отлипания накладываются на каждую сторону по 2 шт. и скрепляются киперной лентой вполнахлеста. После этого укладываются на стеллажи (кареты) для компаундирования.
Режим компаундирования. Вакуумная сушка 740 мм ртутного столба при температуре 80—100° С в течение 2-х ч. Затем загонка компаундной массы для гидростатической опрессовки в течение 14 ч давлением 7 ати и температуре 150—160° С. Температура размягчения массы 110—115° С по Кольцу и Шара. По окончании режима компаундирования с остывших катушек снимаются картонные прокладки, хлопчатобумажные ленты очищаются от остатков битумной массы. При наличии утолщений, снимается защитная стеклянная лента, зачищается компаундная масса и накладывается новая стеклянная лента, пропитанная в битумно-масляном лаке воздушной сушки. Подчистку компаундной массы надо делать очень аккуратно, не повредив изоляцию. Данная конструкция гильзовой изоляции в отличие от микафолиевой получается более монолитная, не вспухает при длительном хранении. Это обеспечивается термореактивным связующим.
Непрерывная изоляция из микаленты на органических связующих
После намотки и растяжки на станке катушка проходит следующие операции:
изолировку витков и подготовку к компаундировке;
первую предварительную прессовку;
первую компаундировку;
опрессовку;
рихтовку;
проверку по макету;
изолировку;
вторую компаундировку;
окончательную отделку.
Изолировка витков, т. е. прокладка горизонтальных прокладок и подготовка к первой компаундировке, производится аналогично описанной ранее.
Операция первой компаундировки или пропитки ведется, как было указано выше (см. § 9-1). Так как размеры катушек после компаундировки увеличиваются вследствие излишков наплывшей компаундной массы, то после пропитки производят опрессовку пазовой части в прессе под давлением с паровым подогревом. Из нее выдавливается лишняя компаундная масса, придается монолитность и прямолинейность пазовой части и размер катушки доводится до требуемого.
Прессовки лобовой части катушки не производят.
Катушки охлаждают в прессе, пропуская воду через нажимные плиты, и затем вынимают. С катушки снимают наложенную временно хлопчатобумажную ленту с наплывами компаундной массы, и она поступает сначала на рихтовку в деревянном шаблоне (рис. 9-24), а затем на изолировку.
Изолировка выполняется микалентой шириной 13—15 мм на углах и головках и 19—22 мм в прямолинейных местах пазовой и лобовых частей. Толщина микаленты 0,17 мм. Микалента накладывается вполнахлестки по всей катушке непрерывно. Накладывать микаленту надо очень тщательно, с затяжкой каждого оборота, чтобы создать возможно большую плотность слоев и равномерность размеров в сечении изолируемой катушки.
Для катушек напряжением 6000 в выводные концы и головки изолируются пятью слоями микаленты вполнахлестки, пазовая часть семью-девятью слоями микаленты, лобовая — на один слой меньше.
Для лучшего закрепления выводных концов у головки они закрепляются тремя-четырьмя оборотами веревочного бандажа диаметром 1—1,5 мм.
Поверх слоев микаленты накладывается хлопчатобумажная лента шириной 20—25 мм и толщиной 0,22 мм: в пазовой части — впритык, в лобовых частях и в головках — вполнахлестки. Затем поверх этого по всей длине накладывается киперная временная лента в х/3 нахлестки шириной 20—25 мм, толщиной 0,35—0,40 мм. Накладываемая хлопчатобумажная лента должна быть достаточно затянута. Далее катушки передаются на вторую компаундировку, которая является самым трудоемким процессом при выполнении непрерывной изоляции. Целью ее является сушка корпусной изоляции, удаление летучих веществ из изоляции и гидростатическая опрессовка ее.
Операция второй компаундировки включает:
сушку с доступом воздуха при температуре 155 —165° С — 5 ч;
сушку при вакууме не менее 720 мм ртутного столба — 8 ч;
сушку при вакууме 740 мм ртутного столба — 3 ч
засасывание компаунднои массы 1—2 ч
выдержку под давлением 7 кГ/см2 (гидростатическая опрессовка) — 5 ч. Температура в смесительном и рабочем котлах должна быть 155—165° С.
Режим компаундирования каждой партии изделий регистрируется с помощью приборов, записывающих температуру, давление и вакуум в котле.
На заводе ЛЭО Электросила процесс компаундирования проводится при помощи установки программного управления, которая осуществляет автоматическое регулирование и технологический контроль режимов. Введение такой установки значительно повысило качество компаундирования изоляции обмоток, получение требуемых размеров, уменьшение брака по вспухаемости изоляции, которая определяется выявлением глухого звука при простукивании металлическим предметом.
При компаундировке большое значение имеет температура, при которой она производится. Особенно важно, чтобы при впуске в пропиточный котел температура компаунднои массы и температура катушек были одинаковы. В противном случае весь процесс будет неудачен, и его повторяют снова.
Как было указано ранее, пропитка под давлением должна продолжаться 5 ч при условии хорошо разогретой компаунднои массы и при давлении не менее 7 кПсм2. При этом давлении (в данном процессе) катушки опрессовываются гидростатическим путем.
Из практики завода Электросила установлено, что температура размягчения компаунднои массы должна быть в пределах 120—127° по Кольцу и Шара. Рекомендуется для процесса компаундирования корпусной изоляции эту температуру поддерживать в максимальных пределах. Это способствует повышению монолитности изоляции и получению размеров сечения катушек в допустимых пределах; гидравлическая прессовка корпусной изоляции при этом не производится.
После компаундировки катушки охлаждаются, а затем их разбирают. Снимают киперную ленту с наплывом компаунднои массы. Определяются размеры сечения катушек. Если катушка тоньше, то ее можно выравнять, дополнительно наложив один слой мика-ленты или хлопчатобумажной ленты. Если же высота не позволяет, толщина выравнивается гибким миканитом. Если толщина катушки больше необходимых размеров, но не более чем на 0,5 мм, производят подчистку компаунднои массы или смену поверхностной защитной хлопчатобумажной ленты.
Выравнивание сечения катушек с компаундированной микалентной изоляцией в прессах не рекомендуется, так как это резко снижает электрическую прочность корпусной изоляции.
Выводные концы очищаются от компаундной массы сначала ножом, а потом механической щеткой. После этого катушки считаются готовыми и подвергаются электрическим испытаниям на витковое и корпус.
В связи с введением механизированного процесса наложения витковой изоляции из микаленты или любой ленточной изоляции изменен технологический процесс изготовления статорных катушек Для электрических машин напряжением от 400 до 6000 в применяется витковая изоляция, наложение которой ведется на механизированном станке (типа ШЛМ-1). Этот процесс состоит из следующих операций:
намотка витковой изоляции и изготовление катушки в виде круговой заготовки;
растяжка круговой заготовки в овальную форму в виде лодочки на станке;
первая опрессовка катушки (лодочки с витковой изоляцией) в гидравлическом прессе;
первая компаундировка катушки (лодочки);
растяжка катушки (лодочки);
вторая опрессовка растянутой катушки;
рихтовка на деревянном шаблоне;
наложение корпусной изоляции (окончательная изолировка) н наложение хлопчатобумажных лент механической защиты;
вторая компаундировка;
окончательная отделка.
Механизированная изолировка катушек
Как было сказано выше, наложение микаленты является весьма трудоемким процессом, требующим известных навыков. Неоднократно делались попытки механизировать эти операции, однако разрешить эту задачу удалось только после Отечественной войны инженерам завода Электросила им. С. М. Кирова тт. Шварцману, Лысикову и Малыгину. г Ими созданы станки и разработана технология наложения витковой изоляции и изоляции от корпуса без применения ручного труда.
Наложение витковой изоляции производится с одновременным изготовлением первичной заготовки катушки, которая представляет собой круглый шаблон вместо лодочки, производится станком, кинематическая схема которого показана на рис. 9-28.
Как показано на рисунке, сматываемый с барабанов провод проходит через отверстие в центре направляющей втулки 2, вокруг который вращается так называемый обмотчик 2 с роликом микаленты 3. В то время как провод наматывается на приемный барабан 4, обмотчик накладывает на провод слой микаленты, являющейся междувитковой изоляцией. На обмоточной головке можно установить 3 обмотчика, для случая одновременного наложения 2-х—3-х слоев ленточной изоляции, что является необходимым для катушек напряжением более 6000 в. Полученная круглая заготовка на специальном станке (рис. 9-29) растягивается в лодочку.
Заготовка устанавливается со стороны выводных концов на неподвижной головке 2, противоположная сторона — на подвижной головке 3, прикрепляемых к верхней части 1 станка. Головка 3 перемещается по направляющим дб упора — ограничителя рабочего

хода 6, установленного соответственно длине лодочки. Ограничитель холостого хода 5 устанавливается соответственно диаметру круговой заготовки минус 10—15 мм. В зависимости от сечения лодочки можно одновременно укладывать для растяжки две-три круговые заготовки. Переключатель 7 служит для реверсирования электродвигателя 4.
В случае применения тонкой меди толщиной до 1,95 мм вторая прессовка катушек производится после компаундирования лодочек, затем лодочки растягиваются в катушки, рихтуются и на них накладывается корпусная изоляция.
При прессовке компаундированных лодочек получаются равномерные размеры по всей длине катушки как в пазовых, так и в лобовых частях. При прессовке же растянутых катушек лобовые части не прессуются, и поэтому местами получаются утолщения выше допустимых, особенно со стороны выводных концов.
Таким образом, в новом процессе изготовления катушек лодочка получается с уже наложенной витковой изоляцией. Помимо того, что механизация изолировки катушек значительно ускоряет и удешевляет этот трудоемкий процесс, здесь достигается еще одно чрезвычайно важное преимущество. Для изготовления катушек можно применять голый провод, так как основной является изоляция, наложенная при изготовлении катушки, а хлопчатобумажная изоляция провода совершенно не нужна. При этом заполнение паза медью может быть большим, так как объем, занятый ранее хлопчатобумажной изоляцией, может быть заполнен медью, т. е. в тот же паз может быть заложен провод с большим сечением. Все это повышает коэффициент использования машины-Так, например, если вместо меди с изоляцией ПБД, имеющей размеры сечения голого провода 4,7 X 2,44, а с изоляцией 5 X 2,74 мм, взять голый провод с размерами сечения 5,1 X 2,63 мм т. е. близкий по размерам к изолированному, то выигрыш в сечении при тех же размерах составит:

где 13,4 и 11,4 — соответствующие площади сечения провода.
Наиболее сложный и трудоемкий процесс — наложение изоляции от корпуса на катушечную обмотку.
Инженерам завода Электросила тт. Лысикову, Устименка и Смирнову удалось решить и эту проблему. По их конструкции на заводе Электросила в 1958 г. установлен станок (рис. 9-30). Он предназначен для изолировки статорных обмоток катушечного типа с длиной прямолинейной части от 320 мм и более, длиной лобовых частей от 90 мм и более при ширине катушки от 125 мм и более. На этом же станке можно изолировать и полукатушки якорной петлевой обмотки.
Сложные элементы катушки — головки и выводные концы — изолируются вручную, остальная часть — пазовая и лобовые части — машинным способом.
Для настройки станка по размерам и форме катушки подбираются сменные копиры 8, равные длине всей прямолинейной

части катушки. Копиры закрепляются на станине 1. Затем устанавливаются угловые секторы 11, по которым фиксируется угол перехода пазовой части катушки к лобовой.
Головки катушки надевают на катушкодержатели 6 и 7. При помощи поворотных приспособлений, имеющихся на столах 5 и 4, положение катушки регулируется таким образом, чтобы проекция всей длины ее пазовой и лобовых частей совпала с копиром и находилась посередине каретки 2 между двумя розетками обмотчиков 3. Изолировка производится по копиру, настроенному соответственно размерам и форме катушки.
При изолировке на этом станке применяется комбинированный способ перемещения каретки: прямолинейно-поступательный на прямых участках и вращательный на радиусах, что дает возможность при постоянном числе оборотов розетки обмоточных головок накладывать изоляцию по всему сложному профилю катушки. В процессе изолировки каретка перемещается по копиру, а розетка обмоточных головок с роликами микаленты — по контуру изолируемой части катушки, с постоянной скоростью, обеспечивающей необходимый шаг наложения изоляции. Изоляция накладывается двумя обмоточными головками вполнахлестки, шаг наложения изоляции при этом равен 12 мм при ширине ленты 24 мм, сразу за один полный проход получается два слоя изоляции.
Можно применить и другой способ намотки — в 2/3 нахлестки с шагом намотки 8 мм. Опыт работы показал, что наложение изоляции вполнахлестки на станке обеспечивает более высокое качество катушек. Получается плавный переход изоляции углов на прямолинейные части, отсутствуют складки и можно применять микаленту с различной степенью влажности, что практически очень важно. Кроме того, большие расстояния между стыками лент приводят к увеличению электрической прочности изоляции.
Скорость вращения розетки обмоточной головки колеблется в пределах 160—240 об/мин.
В конце рабочего хода каретка автоматически выключается электрическим рычажным выключателем 10. При обратном холостом ходе розетка не вращается.
Рабочая скорость и холостой ход каретки могут быть изменены на ходу вращением махтовичка-вариатора с раздвижными конусами и жестким стальным кольцом. Вариатор изменяет общую скорость каретки и розетки в пределах от 100— до 400 об/мин. В такой же степени меняется поступательная скорость каретки. На каретке установлен электродвигатель мощностью 0,4 кет со скоростью вращения 1400 об/мин. Качество наложенной изоляции в значительной степени зависит от правильной установки катушки на станке. Проекция контура изолируемой катушки должна совпадать с копиром станка.
Правильность установки катушки проверяется розеткой обмоточных головок при холостом ходе каретки.
Комбинированная изоляция из микаленты и липкой синтетической ленты (стеклоэскапон)
При механическом изолировании можно создать любой натяг и производить весьма плотную намотку слоев изоляции. Но для этого требуется достаточная механическая прочность применяемых материалов, что, к сожалению, не обеспечивается из-за нестабильных механических свойств подложки микалентной бумаги.
Опыты, проведенные на ЛЭО Электросила, с применением промежуточных слоев механически прочных лент стеклоэскапоно-вой или стеклянной для дополнительной затяжки основной микалентной изоляции дали положительные результаты.
С целью проведения опытов в розетке обмоточной головки (см. рис. 9-30) были установлены еще два обмотчика для закрепления ролика липкой синтетической и стеклянной лент. Эти ленты закрепляются туго, путем подгонки винта и пружины в обмоточной головке.
Изолировка ведется в следующем порядке: 1-й проход станка — 2 слоя микаленты; 2-й проход станка — 1 слой микаленты и 1 слой синтетической липкой ленты; 3-й проход станка — 1 слой микаленты и 1 слой синтетической липкой ленты; 4-й проход станка — 1—2 слоя микаленты.
Размеры изолированной катушки должны быть в минусе против чертежных данных: по ширине на 0,5 мм, по высоте до 1—1,5 мм. На ощупь изолировка должна быть плотной. Поверх накладывается 1 слой защитной ленты.
Такая конструкция изоляции применяется для катушек при напряжении 6000—6300 в. Для катушек с числом одинарных витков (10 и более) и многовитковых, независимо от количества проводников в витке для затяжки рекомендуется применять стеклянную ленту толщиной 0,08—0,1 мм, шириной 15—20 мм. Ролик стеклянной ленты заправляется на 3-ю осевую втулку обмоточной головки станка и плотно закрепляется.
Изолировка производится в следующем порядке: 1-й проход станка — 2 слоя микаленты; 2-й проход станка — 2 слоя микаленты; 3-й проход станка — 1 слой стеклянной ленты; 4-й проход станка — 2 слоя микаленты.
Поверх один слой защитной стеклянной ленты. При расчете толщины изоляции катушки стеклянную ленту в расчет не принимают.
Таким способом изолируется сначала одна сторона катушки и после изготовления части катушек изолируется вторая сторона. Для этого приходится подстраивать держатели головок. .
На готовые катушки поверх основной изоляции накладывается вручную временная киперная лента, и только потом она передается в компаундировку по ранее описанному режиму.
Непрерывная теплостойкая изоляция
Широко внедряется нагревостойкая стеклослюдяная изоляция для статорных катушек ответственных электрических машин.
Для этих катушек применяется электротехническая медь марок ПСД и ПСДК. Конфигурация катушкам придается обычными способами, как это было ранее описано.
Такие катушки компаундированию не подвергаются. Нагревостойкая стекломикалента наносится на витки механическим способом, а корпусная (в зависимости от габаритов) может наноситься механически или вручную. Обычно при малом количестве слоев изоляции и при низком напряжении катушек, до 500 в, корпусная изоляция накладывается вручную. Монолитность витковой изоляции достигается пропиткой катушки в пропиточном кремнийорга-ническом лаке и последующей выпечкой при высокой температуре 180—200° С. Слои корпусной изоляции промазываются цементирующим клеящим кремнийорганическим лаком и затем выпекаются также при повышенной температуре.
Обычно для катушек с рабочим напряжением до 500 в корпусная изоляция состоит из четырех-пяти слоев стекломикаленты толщиной 0,15 мм, наложенной вполнахлестки на пазовые части. Лобовые части и головки имеют на 1 слой изоляции меньше.
Нанесение слоев изоляции производится с плотной затяжкой каждого оборота. Рекомендуется производить эту работу в хлопчатобумажных перчатках.
Перед пропиткой катушка по всей длине заматывается временной стеклянной лентой, если сушка проводится при температуре 180—200° С, при более низкой температуре 120—150° С — хлопчатобумажной киперной лентой.
Ниже приводится режим термической обработки катушек в зависимости от вида пропиточного вещества (табл. 9-3).

Если корпусная изоляция после сушки имеет отлип, необходимо ее сушить дополнительно при температуре 180° С 1—2 ч с применением лака ЭФ-ЗБСУ или при температуре 150° С 1—2 ч при лаке К-47.
Для пропитки: вязкость лака К-47 должна быть 12—13 сек по вискозиметру ВЗ-4, это соответствует содержанию нелетучих 35—40%; концентрация лака ЭФ-ЗБСУ — 40 %.
Корпусная изоляция при тепловой обработке разбухает, и для получения нужных размеров необходима подпрессовка изоляции. Для чего снимается временная лента и накладывается новая. Прессовка производится в гидравлических или пневматических прессах при удельном давлении не более 10—12 кГ/см2, чтобы не допустить механического повреждения изоляции. После этого киперная лента снимается, выводные концы катушки зачищаются на механических щетках. Особо тщательная зачистка требуется для катушек с нелужеными концами. Пайка таких катушек после укладки производится твердым припоем на сварочном, аппарате.
Лобовые части обжимаются в пневматическом приспособлении давлением сжатого воздуха 5—6 ати.
Для получения правильной формы лобовых частей производится окончательное формование катушки на шаблоне путем пригонки лобовых частей к опорным плоскостям, ударяя деревянным или капроновым молотком через фибровую оправку, не повреждая изоляцию.
Окончательно изготовленные катушки испытываются на витковое и на корпус.
Внутрипроводниковое форсированное охлаждение
В последние годы на заводе Электросила начато внедрение активной меди — полого провода прямоугольного сечения с толщиной стенки 1,3—1,5 мм для изготовления катушек статора.
Бухты с медной трубкой предварительно подвергаются гидравлическим испытаниям на проходимость и прочность на специальной испытательной установке (пневмо-гидравлический трансформатор). Один конец бухты после раскалибровки отверстия приключается к установке, а с другого конца визуально наблюдается появление обильной водяной струи, что свидетельствует об отсутствии закупорки канала проводника. После этого данный конец зажимается в призматических губках, создав давление воды 70 ати и выдерживается 5 мин. При этом давление по манометру не должно падать.
Далее бухта с трубкой пропускается через дефектоскоп типа ЭЗТМ-2М для выявления трещин, задиров, расслоения, забоин и т. п. Дефектоскоп является стационарным прибором и состоит из электронного блока, датчика и рихтовочного устройства. Контроль осуществляется при протягивании трубки через датчик с помощью намоточного устройства изолировочного станка для наложения витковой изоляции (см. рис. 9-28). Годная медь направляется для изготовления катушек в соответствии с чертежом. Технологический процесс выполнения таких катушек почти н& отличается от обычных — из сплошных проводников. Основное отличие состоит в том, что к выводным концам этих катушек припаиваются сварочным аппаратом, применив припой ПСр-15, специальные полые наконечники, через которые осуществляется циркуляция воды по схеме.
Контроль герметичности места пайки проводится на гидравлической установке давлением воды 15—20 ати в течение 30 мин. Давление по манометру не должно снизиться.
Также производится контроль гидравлического сопротивления. Для чего создается напор воды при постоянном давлении 0,8 ати, и при помощи мерной посуды засекается секундомером время вытекания воды до определенного уровня.
В качестве витковой и корпусной изоляции для этих катушек используется теплостойкая микалента марки ЛФКТ (ГОСТ 4268-65).
|