Паровые турбины. Часть 2Конструкции стационарных паровых турбин
НЕКОТОРЫЕ ОБЩИЕ ПРИНЦИПЫ КОНСТРУИРОВАНИЯ ТУРБИН
Перед рассмотрением конкретных конструкций турбин, представленных в этой главе, имеет смысл остановиться на некоторых принятых в турбостроении общих принципах конструирования паровых турбин. Поскольку выбор параметров пара и частоты вращения рассмотрены выше, то они предполагаются заданными. Естественно, задано и назначение турбины.
Турбины конденсационные, с противодавлением и теплофикационные относительно небольшой мощности, примерно до 50 МВт, выполняются в одном цилиндре (рис. 10.1, а). Также одноцилиндровой может быть турбина и большей
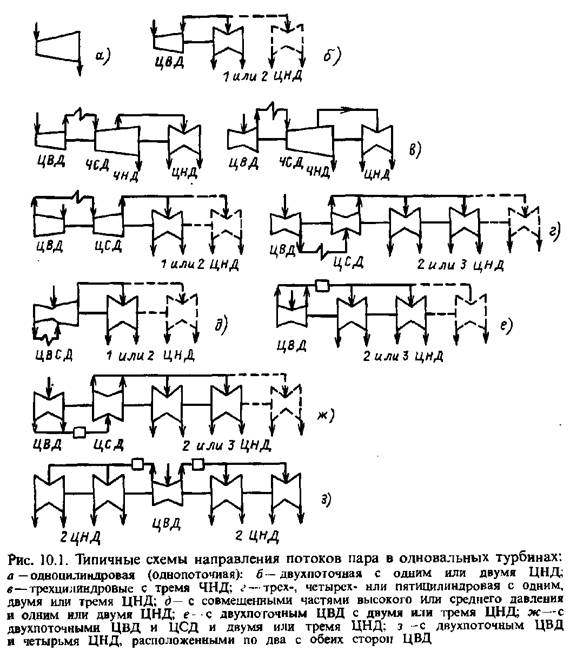
мощности—до 100—150 МВт, если она создается с противодавлением, с большими отборами пара для внешнего потребителя и конденсационная с относительно плохим вакуумом. Однако обычно турбины с теплофикационными отборами пара, хотя для них может и не требоваться дублирования потоков пара в части низкого давления, для лучшей организации отборов и их регулирования при мощности 50— 100 МВт не удается выполнить в одном цилиндре.
Паровые турбины для утилизационных ПГУ выполнятся одно- или двухцилиндровыми (рис. 10.1, а и 6).
Многоцилиндровые агрегаты для ТЭС и ТЭЦ состоят из ЦВД, ЦСД (если он имеется), одного или нескольких ЦНД.
Обычно цилиндры располагаются по потоку пара. После ЦНД устанавливается электрогенератор. Для турбин АЭС возможно как такое же расположение цилиндров, так и иное (рис. 10.26, 10.27 и 10.32), когда первый цилиндр ЦВД располагается в центральной части агрегата, а по бокам его находятся ЦНД (рис. 10.1, з).
В настоящее время одновальные турбины проектируются не более чем с пятью цилиндрами. В этом случае валопровод агрегата, состоящий из роторов турбины и ротора генератора, имеет шесть основных участков.
Очевидно, что увеличение числа цилиндров означает не только удорожание турбины, но приводит к большей величине тепловых расширений, большему числу опор — подшипников, соединений роторов — муфт, более густому спектру собственных частот валопровода. При этом возрастают требования к изготовлению и монтажу агрегата, к жесткости фундамента, что в конечном счете вызывает повышенные трудности обеспечения надежности всего турбоагрегата. Кроме того, увеличивается длительность и стоимость ремонта. Поэтому пятицилиндровые агрегаты выполняются только при их большой мощности, сочетаемой в конденсационных турбинах с глубоким расчетным вакуумом. Такими являются турбины для ТЭС мощностью 800 и 1200 МВт (рис. 1.4 и 10.13), быстроходные турбины для АЭС мощностью 500 МВт и более (рис. 10.26, 10.27, 10.32). Принципиально можно выполнить турбину с шестью цилиндрами. Однако по указанным выше причинам таких турбин нет даже в перспективных проектах агрегатов сверхбольшой мощности. Длительный опыт работы ТЭС и АЭС показал возможность обеспечения высокой эксплуатационной надежности пятицилиндровых машин.
Выбор числа цилиндров, как было рассмотрено в гл. 6, определяется на основе технико-экономических расчетов. Нельзя не отметить некоторой тенденции турбостроительной промышленности к уменьшению числа цилиндров. Это объясняется трудностями обеспечения электростанций холодной циркуляционной водой и, следовательно, получения глубокого вакуума, а также стремлением снизить трудо- и металлоемкость изготовления. Уменьшение числа цилиндров при заданных мощности, частоте вращения и давлении в конденсаторе возможно за счет сокращения числа ЦНД (при этом необходимы или большие размеры — кольцевые площади - последних лопаток, или сохранение тех же последних лопаток и, как следствие, снижение экономичности) и за счет объединения в одном, первом цилиндре частей высокого и среднего давления турбины—совмещенного ЦВСД (рис. 10.34). Недостатком конструкции совмещепного ЦВСД является ограничение числа ступеней этих двух частей турбины и тем самым некоторое уменьшение КПД, а также определенные трудности компактного, рядом с цилиндром расположения большого числа клапанов.
Направление потоков пара в многоцилиндровой турбине определяется рядом факторов — уменьшением усилий, действующих на упорный подшипник, сокращением взаимных осевых перемещений валопровода и системы корпусов, уменьшением тепловых деформаций, расположением трубопроводов, органов парораспределения и т. д.
Первый цилиндр — ЦВД может выполняться однопоточным с подводом пара с конца (рис. 10.5, 10.19—10.25, 10.35—10.38) или в среднюю часть (рис. 10,1, г, 10.10, 10.13, 10.41 и др.). При подводе пара в ЦВД в среднюю часть добавляются некоторые потери энергии в проточной части (теряется выходная энергия пара после первого Ьтсека, имеется небольшая потеря давления в перепуске), но сокращаются потери в концевых уплотнениях. Однако главное преимущество такого подвода — меньшие температурные разности в корпусе цилиндра. Достоинством подвода пара в средней части является уравновешивание осевого усилия в пределах одного цилиндра.
В некоторых турбинах при больших объемных пропусках пара на входе в цилиндр двухпоточная конструкция с одинаковыми потоками пара и соответственно одинаковой проточной частью выполняется не только в ЦНД, но и в ЦСД (рис. 1, 4, а также, например, рис. 10.10, 10.15 и др.) и даже в ЦВД (рис. 10.1, г, 10.27, 10.32). При этом полностью уравновешиваются осевые усилия, однако число ступеней в цилиндре и, следовательно, длина ротора увеличиваются.
Забиваем Сайты В ТОП КУВАЛДОЙ - Уникальные возможности от SeoHammer
Каждая ссылка анализируется по трем пакетам оценки: SEO, Трафик и SMM.
SeoHammer делает продвижение сайта прозрачным и простым занятием.
Ссылки, вечные ссылки, статьи, упоминания, пресс-релизы - используйте по максимуму потенциал SeoHammer для продвижения вашего сайта.
Что умеет делать SeoHammer
— Продвижение в один клик, интеллектуальный подбор запросов, покупка самых лучших ссылок с высокой степенью качества у лучших бирж ссылок.
— Регулярная проверка качества ссылок по более чем 100 показателям и ежедневный пересчет показателей качества проекта.
— Все известные форматы ссылок: арендные ссылки, вечные ссылки, публикации (упоминания, мнения, отзывы, статьи, пресс-релизы).
— SeoHammer покажет, где рост или падение, а также запросы, на которые нужно обратить внимание.
SeoHammer еще предоставляет технологию Буст, она ускоряет продвижение в десятки раз,
а первые результаты появляются уже в течение первых 7 дней.
Зарегистрироваться и Начать продвижение
В многоцилиндровой конструкции стремятся организовать противоположное направление потоков пара в цилиндрах, чтобы в значительной степени уравновесить осевые усилия. При этом следует помнить, что в турбинах с промежуточным перегревом пара при переходных процессах может произойти существенное перераспределение усилий, в результате чего упорное давление в подшипнике (даже при общем уравновешивании при стационарном режиме) может оказаться весьма значительным.
Конденсационная или теплофикационная турбина типа Т, ТК или ПТ в одно- или реже (рис. 10.37) в двухцилиндровом исполнении имеет один поток низкого давления. Если в турбине предусмотрены специальные ЦНД, то, как правило, число потоков низкого давления четное — два, четыре, шесть или даже восемь. В то же время большинство модификаций турбин К-300-23,5 спроектировано с тремя потоками низкого давления. При такой мощности, глубоком вакууме и длине последней лопатки, примерно равной одному метру (при 501/с), эта конструкция была целесообразной — уменьшение числа потоков до двух привело бы примерно к удвоенной потере с выходной скоростью из последней ступени и увеличению в ней изгибающих напряжений. Выполнение же турбины К-300-23,5 с четырьмя потоками ЧНД потребовало бы еще одного цилиндра и заметно повысило бы стоимость установки.
Однако нельзя не отметить, что нечетное число потоков требует, как в данном случае, совмещения в одном цилиндре частей низкого и среднего давлений; имеются также некоторые трудности модернизации и унификации с другими турбинами.
Цилиндры турбины могут выполняться одностенными (од-нокорпусными) с установкой диафрагм прямо в корпусе (см., например, турбину К-17-1,5П КТЗ, рис. 10.44) или с обоймами, в каждой из которых располагаются несколько диафрагм (см., например, ЦВД турбины К-210-12,8, рис. 10.5) или группы сопловых лопаток реактивных ступеней, и двухкорпусными (см. ЦВД на рис. 10.14, 10.27 и др.).
Обоймы позволяют конструктивно организовать отборы пара для регенерации и других нужд, облегчают унификацию, т. е. использование одних и тех же корпусов для различных проточных частей, упрощают обработку корпуса. При пуске турбины обоймы несколько сокращают температурные градиенты в деталях цилиндра, улучшая показатели маневренности. В то же время при обойменной конструкции корпус выполняется большего диаметра, увеличиваются размеры фланцев.
Двустенная конструкция цилиндра позволяет разделить перепад давления и, главное, температурный перепад между корпусами, выполнить и стенки и фланцы корпусов более тонкими, уменьшить коробление их, ускорить пуск турбины. Иногда в ЦВД или после промперегрева в ЦСД внутренний цилиндр достаточно выполнить только для первых групп ступеней, где температура выше. Примеры этого представлены на рис. 10.13, 10.27 и др.
В цилиндрах среднего давления внутренние корпуса обычно выполняются после промперегрева в зоне высоких температур, а также в двухпогочных ЦСД (рис. 10.19, 10.13 и др.).
В ЦНД возможно простое однокорпусное выполнение цилиндра (рис. 10.5), более сложное двухкорпусное (рис. 10.32) и даже трехкорпусное. Такие сложные конструкции ЦНД связаны с трудностями организации отборов пара, с выполнением части корпуса, поддерживающей диафрагмы и сопловые лопатки, независимой от основного, внешнего корпуса, что необходимо для того, чтобы перемещения внешнего корпуса не сказывались на зазорах в проточной части. В некоторых конструкциях внешний корпус ЦНД по существу является корпусом конденсатора, охватывая единую систему ЦНД — конденсатор (рис. 10.28).
Корпуса турбин активного типа, что характерно для турбин отечественного производства, имеют горизонтальный разъем, плотность которого обеспечивается толстыми фланцами, в которых в ЦВД, а в случае промежуточного перегрева и в ЦСД при переходных режимах могут возникнуть недопустимо большие температурные градиенты.
Корпуса высокого давления обычно не имеют вертикального разъема, поскольку обеспечить плотность на так называемом кресте — месте пересечения вертикального ц горизонтального разъемов — при высоком давлении довольно трудно. В то же время в ЦСД (рис. 10.10), а также в одноцилиндровых турбинах имеются вертикальные фланцы (рис. 10.44), которые облегчают изготовление корпуса. В ЦНД вертикальное разделение корпуса связано главным образом с необходимостью уменьшения его габаритов для облегчения транспортировки.
Корпуса высокого и среднего давления выполняются литыми из высоколегированных сталей, иногда сварно-литыми, редко сварно-штампованными. Корпуса ЦНД, а также выходные патрубки большинства конденсационных и теплофикационных турбин выполняются сварными из листовой углеродистой стали.
Подвод пара в ЦВД осуществляется с помощью сопловых коробок, применяемых не только при сопловом, но иногда и при дроссельном парораспределении (рис. 10.13). Эти сопловые коробки, находящиеся под воздействием небольших перепадов температур, облегчают условия пуска турбины, уменьшая температурные градиенты в корпусе ЦВД, позволяя выполнить тоньше стенки корпуса.
В турбинах сверхкритического давления (рис. 4.33, 10.10, 10.41 и др.), где имеются и двойной корпус, и сопловые коробки, конструкция в наиболее горячей части ЦВД является трехстенной, благодаря чему повышается маневренность агрегата. Сопловые коробки могут быть цельными, с общим подводом от клапанной коробки, и разделенными перегородками на сопловые сегменты (рис. 4.30, а, б, 4.31).
Такая конструкция применяется, например, в турбинах небольшой мощности НЗЛ и КТЗ. При этом максимальная степень парциальности регулирующей ступени должна быть меньше или в крайнем случае ненамного больше половинной. В противном случае сложно или даже невозможно завести сопловую коробку в корпус турбины.
В мощных турбинах, как и в большинстве турбин с сопловым парораспределением, каждый регулирующий клапан имеет свою сопловую коробку. Для уменьшения потерь энергии по концам сопловых сегментов стремятся эти коробки расположить как можно ближе друг к другу (рис. 4.32).
Сервис онлайн-записи на собственном Telegram-боте
Попробуйте сервис онлайн-записи VisitTime на основе вашего собственного Telegram-бота:
— Разгрузит мастера, специалиста или компанию;
— Позволит гибко управлять расписанием и загрузкой;
— Разошлет оповещения о новых услугах или акциях;
— Позволит принять оплату на карту/кошелек/счет;
— Позволит записываться на групповые и персональные посещения;
— Поможет получить от клиента отзывы о визите к вам;
— Включает в себя сервис чаевых.
Для новых пользователей первый месяц бесплатно.
Зарегистрироваться в сервисе
Наиболее удачна конструкция сопловой коробки, когда максимальная парциальность очень близка к единице и потери от частичного подвода при всех открытых клапанах практически отсутствуют. Такая конструкция применена в турбинах К-800-23,5 и К-500-16 ЛМЗ. Тот же принцип закладывается в- мощных турбинах с дроссельным парораспределением, где подвод осуществляется через специальную коробку практически по всей окружности (рис. 10.14), а также после промперегрева пара (рис. 10.20).
Клапаны * турбины на входе разделяются на стопорные (быстрозапорные) и расположенные вслед за ними регулирующие. Регулирующие клапаны могут устанавливаться как в общей клапанной коробке, так и раздельно. Общая клапанная коробка обычно присуща системе подъема клапанов с помощью единой траверсы (см. рис. 4.30).
Клапанные коробки как общие, так и индивидуальные располагаются непосредственно на корпусе и на значительном расстоянии от ЦВД. В последнем случае достоинством является возможность упростить конструкцию и изготовление корпуса, облегчить доступ к клапанам, в некоторых турбинах—упростить систему управления клапанами. Недостатком же являются дополнительные паровые объемы после клапанов, что увеличивает разгон турбины после их закрытия.
В некоторых конструкциях для уменьшения потерь давления объединяют стопорный и регулирующий (при дроссельном парораспределении), а также отсечный и регулирующий клапаны. Такая конструкция наиболее часто встречается в турбинах насыщенного и слабоперегретого пара АЭС и после промперегрева турбин высоких параметров. В турбинах насыщенного пара перед ЦНД (после сепаратора и промперегревателя) из-за очень больших объемных пропусков пара зачастую вместо клапанов применяются поворотные заслонки (см. рис. 5.21).
Как правило в турбинах, которые рассмотрены ниже, клапаны устанавливаются вертикально, что позволяет уменьшить площадь, занимаемую агрегатом. Определенные преимущества (но компоновке, по сокращению паровых трактов и тем самым уменьшению потерь давления до входа в первую ступень цилиндра) имеет горизонтальное расположение клапанной системы.
Одним из важнейших вопросов конструирования является организация тепловых расширений и операция турбины. Малые зазоры в уплотнениях и проточной части, далеко не всегда симметричная конструкция, высокие температуры и очень большая длина турбоагрегата требуют тщательного подхода к решению этой задачи.
Простейшая одноцилиндровая турбина с противодавлением обычно имеет корпус, свободно опирающийся на корпуса (стулья) подшипников и непосредственно не связанный с фундаментом (рис. 10.2, а) и лежащий на стульях подшипников почти на уровне горизонтального разъема. Между лапами и стульями подшипников закладываются поперечные шпонки, организующие поперечное расширение корпуса относительно оси машины; (строго) радиальным это перемещение будет при плоскостях опирания, совпадающих с осью турбины.
Во многих случаях имеются еще нижние вертикальные (радиальные) шпонки, служащие этой же цели (рис. 10.2, г).
Иногда, например, в некоторых турбинах КТЗ корпус турбины невысоких начальных параметров и небольшой длины имеет жесткую фланцевую связь (по нижней половине окружности) с корпусом подшипника (см. рис. 10.43). Корпус переднего подшипника, а также корпус заднего подшипника турбины с противодавлением свободно располагаются на фундаментной плите с продольными шпонками в осевой плоскости турбины.
В турбинах с противодавлением между корпусом заднего подшипника и фундаментной плитой имеются еще поперечные шпонки; пересечение линий этих поперечных шпонок с вертикальной плоскостью, проходящей через ось турбины, дает так называемый фикс-пункт (мертвую точку турбины), от которого во все стороны направляются расширения системы корпусов.
В конденсационных турбинах цилиндры низкого давления обычно опираются боковыми лапами на фундаментные рамы (см. схемы на рис. 10.2). В большинстве турбин небольшой и средней мощности (рис. 10.5 и 10.38) корпуса опорных подшипников ЦНД со стороны выхода пара выполняются заодно с нижней половиной выходного патрубка. В такой конструкции ЦНД имеет еще одну, а в двухпоточном ЦНД даже две опоры. В связи с повышенными требованиями к жесткости опор сложных многороторных валопроводов в современных многоцилиндровых турбинах подшипники ЦНД выполняются независимо от выходного патрубка и устанавливаются на своих фундаментных балках (рис. 10.13, 10.28, 10.32).
Фикс-пункт конденсационной турбины образуется обычно в зоне одного из ЦНД (несколько фикс-пунктов в одном агрегате может быть в конструкциях большой длины с несколькими ЦНД, см., например, рис. 10.31) пересечением линии поперечных шпонок под боковыми лапами ЦНД с вертикальной плоскостью, проходящей через продольные и вертикальные шпонки.
Корпуса переднего и промежуточного подшипников располагаются незакрепленными на фундаментных балках или плитах. Между стулом подшипника и плитой закладывается
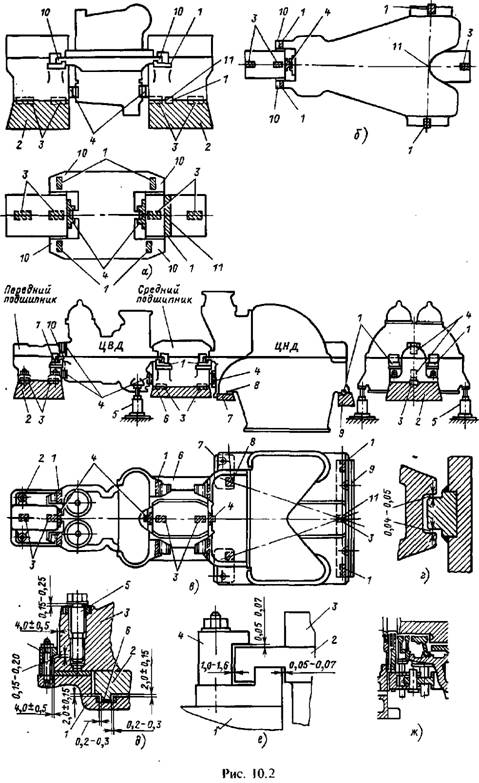
Рис. 10.2. Различные схемы опирация цилиндров и направления тепловых расширений неподвижных частей турбины;
а -турбина с противодавлением; 6 одноцилиндровая конденсационная турбина; в — двухцилиндровая конденсационная турбина; 1 поперечные шпонки; 2 -б, 7 и 9 фундаментные рамы; 3 —продольные шпонки; 4- вертикальные (радиальные) шпонки; 5— пружинные опоры; 8 косые направляющие шпонки; 10- лапы цилиндра; 11-мертвая точка (фикс-пункт) системы неподвижных частей турбины относительно фундамента; г- вертикальная шпонка между корпусом турбины и стулом подшипника; д— лапа опирания корпуса турбины на стул подшипника, применяемая в турбинах ХТЗ; е то же в турбинах ЛМЗ и ТМЗ; 1—корпус (стул) подшипника; 2 лапа нижней половины цилиндра; 3 горизонтальный фланец верхней половины цилиндра; 4 -прижимные скобы; 5 — домкратный болт; 6 - монтажная прокладка; ж вертикальная шпонка между корпусом турбины и стулом переднего подшипника с передачей перемещения корпуса в осевой плоскости, применяемая НЗЛ
продольная шпонка не допускающая боковые, поперечные перекосы корпуса (см. схему на рис. 10.2, в). В некоторых турбинах (см. рис. 10.43) корпус переднего подшипника устанавливается на фундаменте с помощью гибкой опоры.
Перемещения корпусов турбины и корпусов ее подшипников, вызванные тепловыми расширениями, должны происходить свободно, без заеданий на плоскостях опирания корпусов и боковых лап. Важно, чтобы эти перемещения в продольном направлении были строго в вертикальной плоскости, проходящей через ось турбины. Для этого применяется ряд мер: усилия передаются не через боковые лапы и их поперечные шпонки (есть конструкции, где под боковыми лапами нет поперечных шпонок, см. рис. 10.13 и 10.32), а через радиально расположенные шпонки.
Примером последнего является устройство, применяемое в турбинах НЗЛ, показанное на рис. 10.46. Иногда для передачи усилий используются тяги, размещенные по бокам —справа и слева от оси турбины примерно в плоскости горизонтального разъема. В случае обычной, наиболее широко применяемой в нашем турбостроении конструкции (рис. 10.13) плоскости опирания корпусов подшипников на фундаментной плите имеют специальное покрытие с низким коэффициентом трения- из фторопласта.
рассмотрены в § 6.3. С точки зрения технологии изготовления ротора это изменение диаметра имеет небольшое значение.
В ряде конструкций по некоторым причинам (размеры поковки, станков, печей и другого оборудования на заводе) максимальный диаметр необлопаченного ротора ограничен и выполнение ротора с одной ступенью, имеющей диаметр, заметно превышающий корневые диаметры остальных ступеней, может быть нерациональным или даже невозможным. Это касается в первую очередь регулирующей ступени, хотя увеличение диаметра этой ступени, особенно в турбинах с большим начальным объемным пропуском пара, может оказаться целесообразным для сокращения числа ступеней и повышения устойчивости КПД турбины при переменном режиме.
Конструктивно ротор может быть выполнен с насадными дисками (рис. 10.3,а), цельнокованым (рис. 10.3,6), сварным (рис. 10.3, г)исварно-кованым, также смешанного типа — цельнокованым в первых ступенях с последующими насадными дисками (рис. 10.3, в).
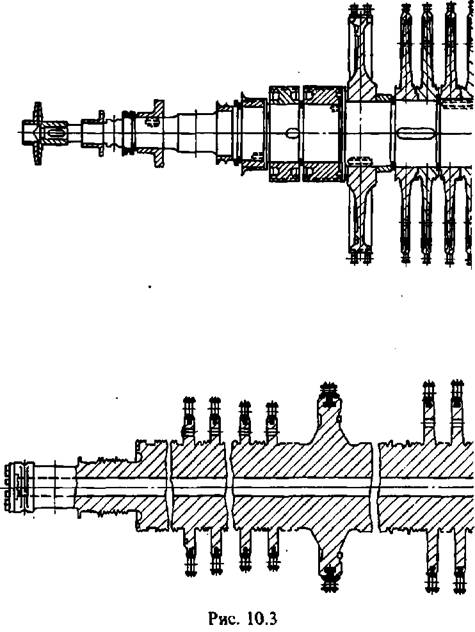
Ротор с насадными дисками проще по конструкции и изготовлению; размеры его обычно ограничены длиной вала. Однако применение такого ротора в ряде случаев недопустимо.
Во-первых, при высоких температурах пара можно ожидать ослабления посадки диска на вал.
Во-вторых, напряжения в диске возрастают с увеличением диаметра внутренней расточки и за счет контактных напряжений при посадке. Поэтому сильно нагруженные диски большого внешнего диаметра, несущие длинные лопатки, в ряде конструкций ЦНД не могут быть выполнены насадными. Это относится, например, к ЦНД турбины К-1200-23,5 ЛМЗ (см. рис. 10.13).
В-третьих, жесткость ротора с насадными дисками может оказаться недостаточной. Другие упомянутые типы роторов
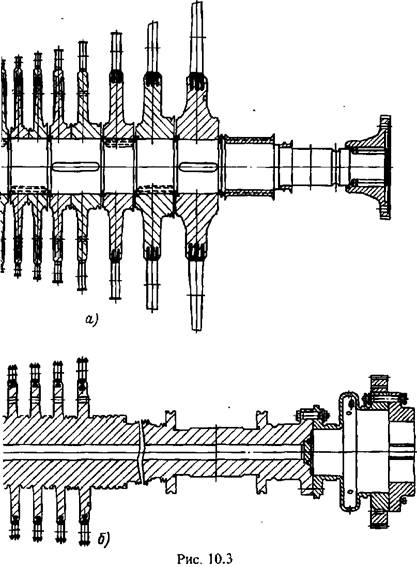
при той же длине (расстоянии между подшипниками) оказываются более жесткими. Кроме того, как правило, конструкция насадного диска с широкими втулками удлиняет ротор.
В-четвертых, в дисках, насаженных на вал, отмеченные выше увеличенные напряжения в месте посадки и особенно концентрация напряжений в шпоночных пазах стимулируют коррозионное растрескивание материала в тех элементах турбины, которые находятся в зоне, где процесс расширения пара происходит вблизи линии насыщения. Это может

относиться к ступеням низкого давления, а в некоторых турбинах и к последним ступеням части среднего давления. Высокие расчетные напряжения в насадных дисках могут потребовать сталей с повышенными пределами текучести, что также неблагоприятно сказывается при проявлении коррозионных эффектов.
Указанных недостатков нет у цельнокованого ротора. Однако размеры поковки такого ротора ограничены, его обработка более сложна и длительна. Цельнокованые роторы выполняются в ЦВД и ЦСД турбин высоких параметров пара, а также в ЦВД мощных турбин насыщенного пара (см. рис. 10.32) и некоторых других турбинах (см. рис. 10.45).
Для проверки качества крупной поковки, используемой для цельнокованых роторов паровых турбин, обычно ротор рассверливается по оси, что приводит к повышению напряжений в нем примерно вдвое по сравнению с цельным, несверленым ротором. Такое увеличение напряжений сказывается на возможности использования его для цилиндров низкого давления вследствие значительных центробежных сил от длинных последних лопаток и обычно несколько увеличенного диаметра поковки ротора ЦНД. В связи с этим в паровой турбине К-1200-23,5 ЛМЗ, в цилиндрах низкого давления турбин насыщенного пара ХТЗ применены рассматриваемые ниже сварные и сварно-кованые роторы. Однако для ЦНД турбины К-1000-5,9/50 ЛМЗ впервые в практике мирового парогурбо-строения удалось создать цельнокованый ротор без центрального сверления, показанный на рис. 10.4.
Барабанные роторы, роторы среднего давления и роторы ЦВД тихоходных турбин часто выполняют сварно-коваными. В этом случае размеры поковки уменьшаются.
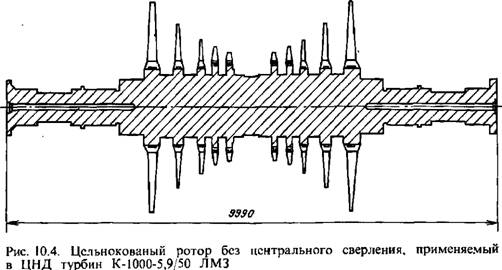
Сварные роторы, состоящие из нескольких дисков, свариваемых по периферии (рис. 10.3, г), нашли широкое распространение в ЦНД турбин как реактивного, так и активного типа. В ЦНД турбин активного типа из-за повышенной реактивности ступеней и меньшего влияния на КПД протечек помимо сопловой решетки иногда отказываются от диафрагменной конструкции, существенно повышая при этом диаметр уплотнений под сопловыми лопатками. Отсутствие диафрагм при том же числе ступеней сокращает осевые размеры ротора, что необходимо в некоторых конструкциях, в первую очередь из-за требований жесткости ротора. Важным преимуществом данной конструкции сварного ротора является возможность выполнить диски без центрального отверстия, придать им форму, близкую к равнопрочной. При той же внешней нагрузке это снижает максимальные напряжения в дисках примерно вдвое. Иногда сварная конструкция ротора применяется и в ЦВД (см. рис. 10.26).
Конструкция сварного ротора, в которой воздействию пара подвергается только внешняя его часть, испытывающая обычно не столь большие напряжения, благоприятна при возможном появлении коррозионного растрескивания металла. Так, в турбинах АЭС ХТЗ со сварными роторами не наблюдались аварии или предаварийное состояние, вызванное этим явлением. В то же время на многих зарубежных турбинах для АЭС с дисковой конструкцией роторов ЦНД были массовые случаи коррозионного воздействия как на диски, так и на валы турбин.
При изготовлении сварных роторов важно обращать особое внимание на конструкцию, технологию и качество сварных швов, тщательный их контроль. В противном случае возможны весьма серьезные аварии.
Конструкции рабочих лопаток и их посадка на диск и барабан рассмотрены в § 4.6.
Роторы отдельных цилиндров между собой и ротор турбины с ротором генератора соединяются с помощью муфт. В мощных турбинах, как правило, встречаются жесткие и полугибкие муфты [49].
Жесткие муфты как с насадными, так и откованными заодно с валом полумуфтами требуют повышенной точности сборки. Однако они позволяют более точно рассчитать критическую частоту колебаний валопровода, несколько сокращают его длину, а в некоторых конструкциях дают возможность ограничиться установкой вместо двух всего одного подшипника между двумя цилиндрами (см., например, участок между ЦВД и ЦСД турбины К-300-23,5 ЛМЗ на рис. 10.7, а также рис. 10.25 и др.). Примеры турбоагрегатов, имеющих только жесткие муфты, приведены на рис. 10.22, 10.34 и др.
При полугибких муфтах, применяемых, в частности, в ряде ранее спроектированных турбин ЛМЗ и ТМЗ (см. рис. 10.5), создается небольшой изгибающий момент, действующий на ротор. Эти муфты допускают незначительные перекосы валов.
Гибкие муфты чаще всего встречаются в транспортных и приводных турбинах, а также в турбоагрегатах относительно небольшой мощности, они допускают в некоторых пределах свободные взаимные перемещения соединяемых роторов. В турбинах применяются муфты кулачковые, пластинчатые, зубчатые (рис. 10.46) и со змеевидной пружиной. Применение гибкой муфты требует упорных подшипников для каждого из роторов. Следует отметить, что гибкая муфта сама может быть источником дополнительных осевых усилий.
Роторы и их элементы должны отвечать определенным критериям надежности. В отношении рабочих лопаток эти критерии кратко рассматривались в § 3.3 и 3.5; для дисков проверяются напряжения, которые обычно максимальны на внутренней расточке, а в сплошных дисках в центре. Кроме того, производится проверка вибрационной надежности диска совместно с облопачиванием. Вал турбины рассчитывается на прочность от действия крутящего момента, наибольшего в месте соединения турбины с генератором или приводной машиной. При соединении турбины с электрическим генератором проверка напряжений производится в условиях короткого замыкания, когда крутящий момент возрастает по сравнению с обычным режимом в несколько раз.
Наиболее ответственна вибрационная проверка валопровода и его отдельных элементов, которая выполняется с учетом податливости опор и фундамента и упругости масляной пленки в подшипниках. Для падежной работы турбины важна качественная балансировка ротора.
действующие на рабочие лопатки, неравномерно распределяются по окружности. При этом возникает неуравновешенная сила. К этому следует добавить неравномерные усилия, действующие на ротор от плотного пара над бандажом рабочих лопаток, в уплотнениях и т. п.
Большую роль могут сыграть силы, действующие па шейки вала со стороны масляного слоя в опорных подшипниках при динамических смещениях шеек вала. При появлении всех этих сил система склонна к автоколебаниям, частота которых примерно соответствует одной из критических скоростей валопровода, обычно наименьшей. Как показал опыт нагружения некоторых турбин большой мощности, колебания начинаются внезапно, при определенной нагрузке и также внезапно исчезают, когда нагрузка снижается.
Чем больше мощность, передаваемая ротором, чем плотнее пар, т. е. чем выше давление пара, чем ниже критическая частота ротора, тем скорее может возникнуть низкочастотная вибрация. Очевидно, что при определенных условиях можно говорить о предельной, так называемой пороговой мощности цилиндра высокого давления и тем самым всего агрегата [21 ].
Возможность появления низкочастотной вибрации должна учитываться при проектировании турбины, а на изготовленных агрегатах иногда приходится предпринимать ряд специальных мер. В первую очередь они касаются конструкции уплотнений. Желательна такая конструкция, при которой, несмотря на относительно малые протечки, прогиб ротора или же .выработка зазоров, например, при неправильно проведенных переходных режимах не привели бы к низкочастотной вибрации. Пример такого рода уплотнений показан на рис. 4.18, в. Во многих случаях эффективным способом является использование опорных подшипников с эллиптической расточкой вкладыша и особенно сегментных [21, 49].
В ряде конструкций скорость пуска турбины и количество пусков за весь ресурс времени работы агрегата, т. е. показатели его маневренности, ограничиваются температурными градиентами и концентрацией напряжений в роторах высокого и (при промперегреве) среднего давления. Поэтому обращается особое внимание на уменьшение концентрации напряжений, связанной с выточками на валу в зоне уплотнений, с пазами под шпонки насадных дисков, галтелями первых дисков, откованных заодно с валом. Лимитирующим показатели маневренности может стать разгрузочный диск, находящийся в высокотемпературной зоне. Иногда для уменьшения концентрации напряжений используются уплотнения не только без так называемых тепловых канавок, но и вообще упрощенного типа — без ступенек, хотя при этом возрастают протечки пара.
Ротор покоится на опорных подшипниках. Подшипники воспринимают нагрузку от ротора и дополнительные усилия, которые могут появиться при парциальном подводе пара, редукторной связи, неправильной работе гибкой муфты и из-за небаланса ротора.
В мощных турбинах применяются только подшипники скольжения с постоянной подачей масла. Следует учесть, что шейки валов крупных турбин вращаются с большими окружными скоростями, достигающими 70 м/с и более. Опорные подшипники имеют баббитовую заливку и довольно мощные вкладыши. Для лучшей центровки валоировода, компенсации несовпадения осей подшипника и ротора, более равномерного восприятия осевого давления всеми колодками упорного подшипника во многих случаях вкладыши выполняются двойными; причем внутренний со сферической поверхностью (см., например, подшипники на рис. 10.21 и др.).
Упорный подшипник служит для установки ротора в осевом положении и восприятия осевых усилий. При этом следует учитывать, что по ряду причин осевое усилие, действующее на упорный подшипник, может оказаться существенно выше расчетного (см. § 8.8). Увеличение осевого усилия может вызываться изменением размеров в проточной части, увеличенными зазорами в диафрагменных уплотнениях, отложениями на лопатках. Могут существенно меняться осевые усилия при переходных процессах, особенно в турбинах с промперегревом. Кроме того, на осевые усилия могут влиять защемления в подвижных (гибких) муфтах, нерасчетные усилия от генератора и т. д. Следует помнить, что при некоторых аварийных ситуациях упорное усилие также может возрасти. В связи с этим упорные подшипники выбираются с большим запасом.
В мощных турбинах используются упорные подшипники с несколькими самоустанавливающимися колодками. Между колодками и упорным диском (гребнем подшипника) должна находиться масляная пленка, для чего необходима непрерывная подача масла. Подшипник проектируется так, чтобы в худшем случае при осевом сдвиге ротора и расплавлении баббитовой заливки в проточной части не произошло задевание ротора о неподвижные детали турбины. Во многих случаях колодки, изготавливаемые из бронзы, вообще выполняют без заливки.
Упорный подшипник имеет колодки с двух сторон. Если направление осевого усилия во всех режимах не меняется и определено достаточно надежно, то вторая группа так называемых установочных колодок может иметь меньшие размеры. В ряде машин обе группы колодок одинаковы.
Упорный гребень может быть выполнен заодно с валом, что чаще всего встречается в цельнокованых роторах (см., например, рис. 10.5), или посажен на вал с натягом (см., например, рис. 10.46). В некоторых турбинах КТЗ (рис. 10.43) упорным гребнем является диск центробежного масляного насоса. В ряде конструкций подшипник имеет два гребня, у каждого из которых своя группа колодок (см. рис. 10.19, 10.24 и др.).
Очень часто упорный подшипник объединяется с опорным: они имеют один общий вкладыш. В остальных случаях эти подшипники располагаются рядом. Иногда на валу выполняются два упорных диска, каждый со своими колодками воспринимающими усилие в противоположном направлении. Между дисками располагается упорный подшипник.
При проектировании турбины важную роль играет расположение упорного подшипника- чем дальше находится ступень от упорного подшипника, тем больше требуются осевые зазоры в проточной части. Увеличенные осевые зазоры и связанные с этим повышенные протечки в ступени особенно неблагоприятны в первых ступенях турбины с наименьшими высотами лопаток. Поэтому обычно упорный подшипник располагается со стороны первых ступеней ЦВД. В некоторых многоцилиндровых турбинах он располагается между ЦВД и ЦСД, что к тому же позволяет несколько сократить тепловые перемещения в ступенях ЦСД и ЦНД,
Для смазки подшипников турбинное масло подается специальными насосами, которые могут устанавливаться на валу турбины, быть связанными с валом через редук горную передачу или независимыми. В частности, возможно использование масляных насосов с электроприводом. При пуске и остановке турбины, а также в аварийных ситуациях недопустимо прекращение подачи масла, в связи с чем необходим специальный насос. За последнее время нашли распространение подшипники с полостями, располагаемыми над вкладышем и залитыми маслом, откуда при аварийной остановке турбины с неработающими масляными насосами масло подается в подшипники (см., например, рис. 10.13).
Для равномерного охлаждения ротора и облегчения последующего пуска турбины предусматривается возможность проворачивания ротора, для чего служат специальные валоноворотные устройства, чаще всего связанные с муфтой, соединяющей роторы турбины и генератора (см., например, рис. 10.7).
При конструировании турбины особое внимание обращается на обеспечение надежности при всех режимах ее работы, на сокращение времени для ее пуска и остановки, на повышение экономичности. Немаловажную роль в эксплуатации играет удешевление ремонта и сокращение времени, необходимого для ревизии и ремонта, так называемая ремонтопригодность, что также должно учитываться при создании агрегата.
Итоговым показателем проектируемой конструкции являются затраты на выработку электроэнергии, которые зависят от эксплуатационных затрат, т. е. в первую очередь от экономичности турбинной установки, от стоимости оборудования, и в том числе турбоагрегата. Поэтому стоимость турбины оказывает существенное влияние на проектирование агрегата, выбор его конструкции и материалов, технологичность. Большое значение имеет надежность оборудования. Авария и даже просто внеплановая остановка турбины, необходимость в частых ревизиях в конечном итоге увеличивают стоимость вырабатываемой электроэнергии.
|