Технология переработки нефти и газа. Часть 1Влияние основных условий на процесс предварительной гидроочистки бензиновых фракций
Процесс гидроочистки основывается на реакции гидрогенизации, в результате которой органические соединения серы, кислорода и азота превращаются в углеводороды, сероводород, воду и аммиак. Подробно эти реакции были рассмотрены в предыдущей теме.
Сернистые соединения в прямогонных бензиновых фракциях представлены меркаптанами, сульфидами, дисульфидами, полисульфидами и тиофенами. Кроме того, не исключено наличие элементарной серы, образующейся при термическом разложении сернистых соединений в процессе перегонки нефти и в результате окисления сероводорода при контакте с воздухом.
В зависимости от строения, сернистые соединения превращаются в процессе гидроочистки в парафиновые или ароматические углеводороды с выделением сероводорода:
Легче всего гидрируются алифатические (меркаптаны, сульфиды и др.) сернистые соединения и труднее – тиофены. С увеличением средней молекулярной массы и температуры кипения бензиновых фракций уменьшается скорость реакций гидрообессеривания. Это вызвано изменением типа сернистых соединений, присутствующих в них.
Азотистые соединения в бензиновых фракциях представлены в основном пирролами, пиридинами, аминами, а в высококипящих бензиновых фракциях – хинолинами; также возможно присутствие и других типов азотистых соединений. Содержание азотистых соединений в прямогонных бензиновых фракциях незначительно. В бензиновых фракциях вторичного происхождения их концентрация значительно выше (в 5 ÷ 10 раз).
В процессе гидроочистки азотистые соединения превращаются следующим образом:
Кислородсодержащие соединения спирты, эфиры, фенолы - в условиях гидроочистки превращаются в углеводороды и воду. Наиболее стойкие из этих соединений - фенолы.
Реакции гидрогенолиза сернистых, азотистых и кислородсодержащих соединений в условиях процесса гидроочистки (в присутствии катализатора при температуре от 300 до 400 ºС и парциальном давлении водорода от 1,0 до 3,0 МПа) приводят к практически полному удалению серы, азота и кислорода в виде сероводорода, аммиака и воды.
В процессе гидроо чистки одновременно с вышеописанными протекают также реакции с участием углеводородов (изомеризация, гидрирование непредельных, частичное дегидрирование нафтеновых и дегидроциклизация парафиновых углеводородов и др.).
Непредельные углеводороды гидрируются, превращаясь в соответствующие парафиновые углеводороды. Содержание непредельных углеводородов в сырье установок каталитического риформинга (до гидроочистки) не должно превышать 2 % масс.., так как они при высоких температурах быстрее углеводородов других классов образуют кокс, который откладывается в змеевиках печей и на катализаторе. Их остаточное содержание в гидрогенизате не должно превышать 0,5 % мас. Особенно нежелательно присутствие в сырье диеновых и ацетиленовых углеводородов.
В прямогонных бензинах могут присутствовать в небольших количествах органические соединения, имеющие в своем составе галогены (обычно хлор) и некоторые металлы (свинец, медь, мышьяк и др.). Примеси металлов при попадании на катализатор риформинга, накапливаются на нем и вызывают его необратимую дезактивацию.
Нерегулируемое и чрезмерно большое поступление галогенов (хлора) на катализатор риформинга приводит к аномальному усилению его кислотной функции и способствует развитию реакций крекинга, что ускоряет закоксовывание катализатора. В процессе гидроочистки соединения, содержащие металлы и галогены, также разрушаются. Металлы отлагаются на катализаторе гидроочистки, а образующийся хлористый водород удаляется в отпарной колонне. Одновременное присутствие хлористого водорода, сероводорода и паров воды в дистиллятном потоке этой колонны может вызвать ускорение процессов коррозии в соответствующем холодильном оборудовании. Содержание указанных примесей обычно резко возрастает при переработке бензиновых фракций вторичных процессов.
Основные реакции, протекающие в процессе гидроочистки являются экзотермическими (идут с выделением теплоты), но поскольку содержание примесей в прямогонном бензине незначительно, процесс его гидроочистки не сопровождается значительным повышением температуры газопродуктовой смеси.
Глубина гидроочистки бензиновой фракции зависит от температуры процесса, парциального давления водорода, объемной скорости подачи сырья, кратности циркуляции водородсодержащего газа (ВСГ) к сырью и свойств применяемого катализатора, на стабильность работы которого влияют температура, давление и соотношение расхода ВСГ к расходу сырья.
Температура. С ее увеличением глубина и скорость реакций гидрообессеривания и гидрирования непредельных углеводородов возрастает. Однако, при температурах выше 420ºС увеличивается интенсивность реакций гидрокрекинга. При этом снижается выход жидких продуктов, увеличивается отложение кокса на катализаторе и сокращается срок его службы. Оптимальная температура процесса гидроочистки зависит от состава сырья. При переработке прямогонных бензиновых фракций оптимальным диапазоном температур является 290 ÷ 360 ºС. В начале рабочего цикла (на высокоактивном катализаторе) устанавливается минимальная температура, обеспечивающая необходимую степень очистки сырья. Повышение температуры производится для компенсации снижения активности катализатора и поддержания заданной глубины очистки.
Преждевременное повышение температуры ускоряет закоксовывание катализатора, не увеличивая существенно глубины очистки.
Давление. При повышении общего давления в системе растет парциальное давление водорода, способствующее увеличению глубины гидроочистки, что связано с ростом концентрации реагентов в единице объема. При этом межрегенерационный период работы и срок службы катализатора возрастает. Оптимальный диапазон давления при гидроочистке 2,0 ÷ 4,0 МПа.
Забиваем Сайты В ТОП КУВАЛДОЙ - Уникальные возможности от SeoHammer
Каждая ссылка анализируется по трем пакетам оценки: SEO, Трафик и SMM.
SeoHammer делает продвижение сайта прозрачным и простым занятием.
Ссылки, вечные ссылки, статьи, упоминания, пресс-релизы - используйте по максимуму потенциал SeoHammer для продвижения вашего сайта.
Что умеет делать SeoHammer
— Продвижение в один клик, интеллектуальный подбор запросов, покупка самых лучших ссылок с высокой степенью качества у лучших бирж ссылок.
— Регулярная проверка качества ссылок по более чем 100 показателям и ежедневный пересчет показателей качества проекта.
— Все известные форматы ссылок: арендные ссылки, вечные ссылки, публикации (упоминания, мнения, отзывы, статьи, пресс-релизы).
— SeoHammer покажет, где рост или падение, а также запросы, на которые нужно обратить внимание.
SeoHammer еще предоставляет технологию Буст, она ускоряет продвижение в десятки раз,
а первые результаты появляются уже в течение первых 7 дней.
Зарегистрироваться и Начать продвижение
Объемная скорость подачи сырья. Объемной скоростью называется отношение объема сырья, подаваемого в реактор за один час, к объему катализатора, находящегося в реакторе:
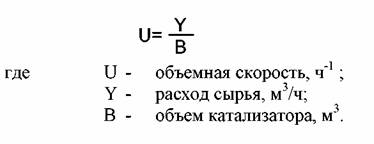
С увеличением объемной скорости уменьшается время пребывания сырья в реакторе, то есть время контакта молекул сырья с катализатором. В случае уменьшения объемной скорости (увеличения времени контакта сырья и катализатора) увеличивается глубина гидроочистки сырья. В зависимости от состава сырья и требуемой глубины очистки, объемная скорость процесса может лежать в пределах от 2,0 до 7,0 ч-1.
Для легких, более термически стойких нефтепродуктов, уменьшение глубины гидроочистки при повышении объемной скорости компенсируется за счет повышения температуры.
Активность катализатора. Чем выше активность катализатора, тем с более высокой объемной скоростью можно проводить процесс и глубже очищать сырье. Для определения активности катализатора сравнивают его обессеривающую способность с обессеривающей способностью эталонного образца. Испытания проводят на пилотной установке по специальной методике. Индекс активности рассчитывают по формуле:
серы в сырье;
- содержание серы в гидрогенизате, очищенном на эталонном катализаторе;
- содержание серы в гидрогенизате, очищенном на испытуемом катализаторе.
Для повышения а ктивности катализатора гидроочистки после регенерации, то есть для перевода металла катализатора из менее активной оксидной формы в более активную сульфидную, проводится его осернение сероорганическими соединениями или водородсодержащим газом с большой концентрацией сероводорода. Со временем активность катализатора падает за счет отложений на его поверхности и в пористой структуре кокса. Частичную регенерацию катализатора гидроочистки можно провести гидрированием коксовых отложений путем циркуляции водорода при температуре 400 ÷ 420 °С. Однако при этом возможен переход металла из сульфидной формы в металлическую. Поэтому требуется значительная осторожность при использовании данного способа. Кроме того, такая регенерация не эффективна, если коксообразование произошло в результате падения давления в системе или превышения температуры выше допустимой. Поэтому даже кратковременное снижение давления в системе, превышение температуры процесса, прекращение циркуляции водородсодержащего газа недопустимо. В этих случаях, для восстановления активности катализатор подвергается паровоздушной регенерации.
Кратность циркуляции водородсодержащего газа. Соотношение между объемом водородсодержащего газа при 0˚С и 0,1 МПа и объемом сырья при 20˚С, поступающих в реактор, называется кратностью подачи (или кратностью циркуляции) водородсодержащего газа. При стехиометрических соотношениях водород/сырье реакции гидрирования сернистых соединений могут протекать практически нацело, но скорость их будет очень мала из-за низкого парциального давления водорода. Поэтому процесс проводят при избытке водорода. Количество подаваемого циркулирующего водородсодержащего газа (в нормальных метрах кубических, нм ) приходящегося на 1 м жидкого сырья, называется кратностью циркуляции. Кратность циркуляции ВСГ при гидроочистке бензиновых фракций не должна быть ниже 90 нм /м сырья.
Концентрация водорода в циркулирующем водородсодержащем газе влияет на необходимую кратность ВСГ к сырью и парциальное давление водорода в реакторе. Она может колебаться в пределах от 65 до 85 %, в зависимости от состава сырья, содержания кокса и хлора на катализаторе риформинга.
В результате предварительной гидроочистки получается гидрогенизат, пригодный для использования в блоке риформинга. При применении би- и полиметаллических катализаторов риформинга к нему предъявляются следующие требования.
Фракция 62-180 С
Массовая доля серы, %, не более 0,00005
Массовая доля азота, %, не более 0,0001
Содержание воды, % масс, не более 0,002
Массовая доля непредельных углеводородов, %, не более 0,5 Фракционный состав:
температура начала перегонки, ºС, не ниже 68
50% перегоняется при температуре, ºС, не выше 125
температура конца кипения, ºС, не выше 180
Фракция 80-180 С Фракционный состав:
•температура начала перегонки, ºС не ниже 80
• 50% перегоняется при температуре, ºС не выше 125
•температура конца кипения, ºС не выше 180
Массовая доля серы, %, не более 0,00005
Массовая доля азота, %, не более 0,0001
Содержание воды, % масс, не более 0,002
Массовая доля непредельных углеводородов, %, не более 0,5
Влияние основных условий на процесс каталитического риформинга
Основные параметры процесса:
температура в зонах реакции, ºС 470 ÷ 530
давление на выходе из последнего реактора ри- 1,9-2,0/1,2 ÷
форминга, МПа (изб). В знаменателе приведены дан- 1,40
ные для четвертого реактора секции 200 ЛК-6У №2
объемная скорость подачи сырья, ч-1 1,1 ÷ 1,5
кратность циркуляции ВСГ , нм /м сырья 900 ÷ 1300
мольное отношение водород/углеводород не менее 4
Температура на входе в реакторы является основным регулируемым параметром процесса и должна поддерживаться на минимально возможном уровне, обеспечивающим получение катализата с заданным содержанием ароматических углеводородов. Она оказывает значительное влияние на скорость протекающих реакций, что, в конечном счете, определяет выход целевых продуктов. При увеличении температуры выход катализата снижается, а степень его ароматизации, и соответственно октановые числа, возрастают. Повышение температуры, наряду с увеличением выхода аренов, ускоряет реакции расщепления углеводородов, главным образом парафиновых. Температура на входе в реакторы при проведении процесса не должна превышать 530 ºС. За счет протекания реакций, осуществляющихся с поглощением теплоты, в реакторе происходит снижение температуры. Перепад температуры по слою реактора может достигать 50-70оС. Он определяется тепловым эффектом реакций, протекающих в реакторе.
Сервис онлайн-записи на собственном Telegram-боте
Попробуйте сервис онлайн-записи VisitTime на основе вашего собственного Telegram-бота:
— Разгрузит мастера, специалиста или компанию;
— Позволит гибко управлять расписанием и загрузкой;
— Разошлет оповещения о новых услугах или акциях;
— Позволит принять оплату на карту/кошелек/счет;
— Позволит записываться на групповые и персональные посещения;
— Поможет получить от клиента отзывы о визите к вам;
— Включает в себя сервис чаевых.
Для новых пользователей первый месяц бесплатно.
Зарегистрироваться в сервисе
Тепловой эффект реакции в процессе риформинга зависит главным образом от содержания в сырье циклоалканов, так как именно реакции дегидрирования циклоалканов сопровождаются интенсивным поглощением теплоты. Если для алканового сырья отрицательный тепловой эффект составляет 295 - 364, то для циклоалканового 410 - 670 кДж на 1 кг сырья.
Поскольку теплота реакции отнимается от тепловой энергии газосырьевой смеси, температура последней падает. Поэтому к реакционной смеси, чтобы обеспечить приемлемые для процесса условия, необходимо подводить теплоту. Это обстоятельство вынуждает распределять катализатор в несколько реакторов и между ними подогревать газосырьевую смесь в секциях печи. В первых реакторах поглощение теплоты наиболее велико, так как содержание циклоалканов в сырье наибольшее, в последних наоборот. Чтобы сделать подвод тепла более равномерным, катализатор размещают в нескольких реакторах неравномерно: в первом по ходу сырья реакторе наименьшее количество катализатора, в последнем наибольшее. В итоге, на общую глубину ароматизации влияют не только параметры процесса и содержание в сырье нафтеновых углеводородов, но и правильное распределение катализатора между реакторами. Соотношение загрузки катализатора по реакторам в зависимости от состава сырья может быть 1,5: 3,5: 5, или 1: 2: 4 или 1: 3: 7 и др.
Перепад температуры в реакторах риформинга определяется суммарным тепловым эффектом протекающих реакций. Общий тепловой эффект зависит от соотношения этих реакций на данной ступени риформинга:
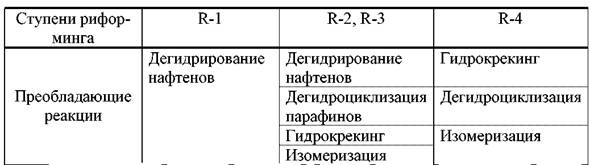
Температурный перепад, особенно в первой ступени риформинга, может служить характеристикой активности катализатора. По мере отработки катализатора и накопления в нем кокса, понижения концентрации водорода в циркулирующем ВСГ суммарный перепад температуры в реакторах снижается. Однако в некоторых случаях понижение перепада температуры в реакторах может свидетельствовать о чрезмерном содержании хлора на катализаторе.
Высокая температура процесса способствует в большей степени протеканию нежелательных реакций, сопровождающихся повышенным коксо и газообразованием, чем желательных. Однако регулируемый постепенный подъем температуры в течение периода между регенерациями катализатора необходим для поддержания высокого октанового числа получаемого катализата. При этом его выход снижается.
Парциальное давление водорода в зоне реакции оказывает существенное влияние на процесс ароматизации. Результаты кинетических расчетов для реакции дегидрирования шестичленных нафтеновых углеводородов показывают, что в одинаковых условиях по мере возрастания после определенного предела парциального давления водорода степень их превращения падает. Процесс ароматизации парафиновых углеводородов также тормозится с увеличением парциального давления водорода. В то же время, рост парциального давления водорода подавляет процесс коксообразования. Таким образом, влияние парциального давления водорода на выход ароматических углеводородов носит нелинейный экстремальный характер (рис. 5.6). Во всех случаях при повышении парциального давления водорода снижается содержание непредельных углеводородов в жидких продуктах реакции.
Общее давление Роль общего давления в процессе каталитического риформинга очень велика, так как при повышении давления (1 - 4 МПа) резко снижается скорость коксообразования. Одновременно повышение давления приводит к уменьшению выхода водорода, ароматических углеводородов и получаемого катализата (рис 5.7).
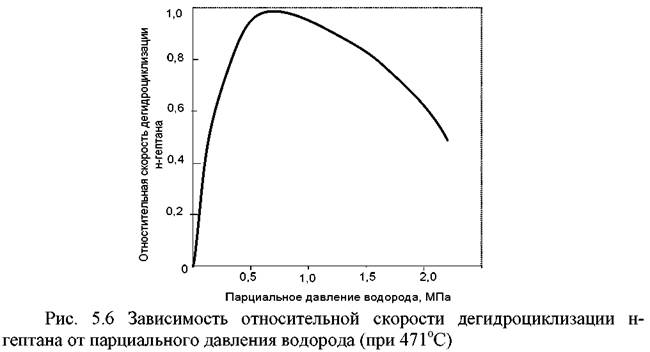
При более низком давлении их выход выше, но выше и коксообразование, следовательно, катализатор быстрее теряет активность, кроме того, растет скорость образования углеводородных газов.
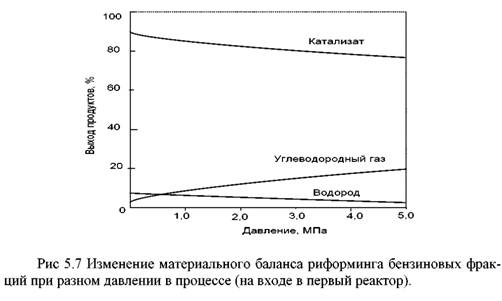
Влияние объемной скорости подачи сырья. Выход ароматических углеводородов и концентрация их в продуктах зависят от объемной скорости подачи исходного сырья. С ее увеличением выход катализата возрастае т, а степен ь ароматизации падает, что приводит к снижению суммарного выхода ароматических углеводородов в пересчете на исходное сырье и, соответственно, уменьшению октанового числа катализата. Однако это снижение в определенных пределах может быть скомпенсировано повышением температуры в реакторах риформинга.
При изменении расхода сырья всегда необходимо:
сначала повышать расход сырья, а затем температуру на входе в реактор;
сначала понижать температуру на входе в реактор, а затем понижать
расход сырья.
Средняя объемная скорость подачи сырья составляет обычно 1 - 2 ч-1 . Слишком низкие объемные скорости не всегда экономичны, так как при этом необходимо увеличивать объем катализатора, загружаемого в реактора. Это целесообразно осуществлять лишь в определенных пределах.
Кратность циркуляции и концентрация водородсодержащего газа. Мольное соотношение водород/сырье (H2/HC) определяется как отношение чистого водорода в ВСГ (моль/ч) к расходу сырья (моль/ч). От величины этого параметра зависит интенсивность коксообразования и, следовательно, стабильность и срок службы катализатора. Мольное отношение H2/HC прямо пропорционально кратности циркуляции водородсодержащего газа в системе и концентрации водорода в нем. Процесс риформинга осуществляется в среде газа с концентрацией водорода от 80 до 73 % об. в начале и конце цикла соответственно.
Разбавление паров сырья водородом благоприятно влияет на продолжительность работы катализатора. Кратность циркуляции колеблется в пределах 800 - 1800 нм3ВСГ/м3 сырья (при нормальный условиях). Повышение кратности циркуляции связано с увеличением эксплуатационных расходов на топливо, воду, электроэнергию.
Таблица 5.5, приведенная ниже, суммирует влияние каждого независимого параметра на показатели процесса риформинга.
Таблица 5.5 Влияние основных параметров на показатели процесса риформинга.
|