Технология термической обработки металловЗакалка
Выбор температуры. Закалкой называется процесс термической обработки, заключающийся в нагреве стали до температуры выше критической и последующем достаточно быстром охлаждении для получения вместо механической смеси фаз пересыщенного твердого раствора с искаженной решеткой (мартенсита). В результате закалки прочность и твердость стали повышаются, а пластичность снижается.
т. е. выше линии 05 диаграммы железо—цементит.
. Структура после охлаждения будет мартенсит и феррит. Феррит, имеющий низкую твердость, понижает общую твердость закаленной стали; такая закалка называется неполной.
диаграммы железо—цементит. Так как эта ли-
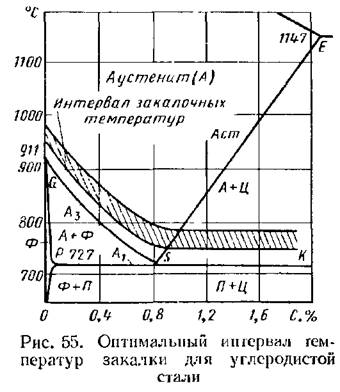
ния горизонтальная и соответствует температуре 727° С, для заэвтектопдпой стали можно указать интервал температуры нагрева для закалки 760—790° С. При таком нагреве исходная структура перлит и цементит не будет полностью превращаться в аустеинт, а часть вторичного цементита останется нераствореппой и структура будет аустенит и цементит. После охлаждения со скоростью больше критической аустенит превратится в мартенсит. Структура закаленной стали будет состоять из мартенсита и цементита; такая закалка будет неполной. Но если неполная закалка доэв-тектоидных сталей ухудшает их свойства, то неполная закалка заэвтектоидных сталей улучшает их свойства и является нормальной. Это объясняется тем, что в заэвтектоидных сталях в результате неполной закалки сохраняется избыточный цементит, обладающий большей твердостью по сравнению с мартенситом. Поэтому наличие в структуре закаленной заэвтек-тоидной стали кроме мартенсита еще и цементита повышает твердость и износостойкость стали.

Охлаждающие среды. Скорость охлаждения стали, нагретой до температуры закалки, влияет на результат закалки. Оптимальной закалочной средой является та среда, которая быстро охлаждает деталь в интервале температур минимальной устойчивости аустенита (550—650° С), чтобы предупредить его распад на фер-рито-цементптную смесь, и замедленно (или с очень большой скоростью) — в интервале температур мартенситного превращения (ниже 200—300° С), чтобы обеспечить одновременность мар-тенситообразования во всех зонах охлаждаемой детали и этим снизить опасность образования трещин.
Наиболее распространенными закалочными средами являются вода, водные растворы солей, щелочей, масло, расплавленные соли. При охлаждении в воде и масле, температура кипения которых ниже температуры охлаждаемых в них деталей, скорость охлаждения различна в начальном, среднем и конечном периодах охлаждения и подразделяется на три стадии (рис. 56):I — пленочного кипения; II — пузырчатого кипения; III — конвективного теплообмена. Между этими стадиями в промежутках а и б наблюдается переходное состояние.
Стадия пленочного кипения характеризуется образованием вокруг охлаждаемой детали паровой пленки, отделяющей раскаленную поверхность от жидкости, и поэтому скорость охлаждения на данной стадии сравнительно невелика.
Стадия пузырчатого кипения наступает при более низких температурах охлаждаемой поверхности, когда паровая пленка разрушается, создается непосредственный контакт жидкости с деталью; при кипении жидкости возникают пузырьки пара, на что затрачивается большое количество тепла, в связи с чем охлаждение происходит с большой скоростью.
Стадия конвективного теплообмена наступает при понижении температуры на поверхности ниже температуры кипения жидкости. Скорость теплоотвода в этой стадии низка, и охлаждение протекает с небольшой скоростью.
Вода охлаждает быстрее, чем масло (в 6 раз при 550—650° С и в 28 раз при 200° С) (рис. 57). Поэтому воду применяют для охлаждения деталей из сталей с большой критической скоростью закалки (углеродистые стали) , а в масле охлаждают детали из стали с малой критической скоростью закалки (легированные стали).
что объясняется частичным от-
пуском мартенсита при охлаждении в масле. Данный способ охлаждения широко применяется для деталей сложной формы, подвергаемых поверхностной закалке при индукционном нагреве.
значительно увеличивает ее закаливающую способность в связи с расширением интервала пузырчатого кипения (почти полностью исключается стадия пленочного кипения). Положительным является также то, что эти растворы при низких температурах мартенситного превращения охлаждают медленнее, чем вода. При поверхностной и объемной закалках применяют струйное или душевое охлаждение.
Для охлаждения применяют также водо-воздушные смеси, подаваемые через форсунки. Изменением соотношения воды и воздуха, а также давления смеси можно менять скорость охлаждения. Такое охлаждение применяют при закалке крупных деталей. Масло обладает небольшой скоростью охлаждения в области температур мартенситного превращения, что обеспечивает одновременность мартенситообразования, и поэтому опасность образования трещин резко уменьшается. Кроме того, закаливающая способность не изменяется с повышением температуры масла до 150° С. Но масло легко воспламеняется, пригорает к поверхности детали; под влиянием высокой температуры охлаждаемых деталей
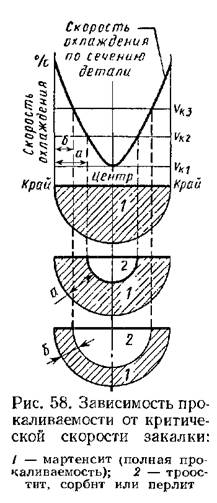
масло постепенно начинает густеть, и закаливающая способность его понижается. Охлаждающую способность воды увеличивают добавки, образующие теплоизоляционные пленки. В ГДР разработана закалочная среда аква-пласт, поставляемая потребителю в виде концентрата— высоковязкой прозрачной жидкости, содержащей кроме растворенной пластмассы антикоррозионный ингибитор. Этот концентрат легко растворяется в воде. Изменяя концентрацию аква-пласта, можно получить любую скорость охлаждения. Смягчающее закалочное действие аква-пласта по сравнению с водой объясняется более высокой вязкостью и образованием на поверхности детали тонкой пленки пластмассы, затрудняющей теплообмен. При охлаждении в растворе аква-пласта закалочных трещин не возникает.
Забиваем Сайты В ТОП КУВАЛДОЙ - Уникальные возможности от SeoHammer
Каждая ссылка анализируется по трем пакетам оценки: SEO, Трафик и SMM.
SeoHammer делает продвижение сайта прозрачным и простым занятием.
Ссылки, вечные ссылки, статьи, упоминания, пресс-релизы - используйте по максимуму потенциал SeoHammer для продвижения вашего сайта.
Что умеет делать SeoHammer
— Продвижение в один клик, интеллектуальный подбор запросов, покупка самых лучших ссылок с высокой степенью качества у лучших бирж ссылок.
— Регулярная проверка качества ссылок по более чем 100 показателям и ежедневный пересчет показателей качества проекта.
— Все известные форматы ссылок: арендные ссылки, вечные ссылки, публикации (упоминания, мнения, отзывы, статьи, пресс-релизы).
— SeoHammer покажет, где рост или падение, а также запросы, на которые нужно обратить внимание.
SeoHammer еще предоставляет технологию Буст, она ускоряет продвижение в десятки раз,
а первые результаты появляются уже в течение первых 7 дней.
Зарегистрироваться и Начать продвижение
В качестве охлаждающей среды при закалке используют также кипящий (псевдоожиженный) слой. Псевдоожижение заключается в интенсивном перемешивании частиц твердого зернистого материала (например, корунда, песка, руды, металлического порошка) восходящим потоком газа. При достаточной скорости газа твердые частицы приобретают подвижность и слой становится похожим на вязкую жидкость. Скорость охлаждения в кипящем слое зависит от размера частиц, теплопроводности газа и может быть отрегулирована в широких пределах. Для предохранения деталей сложной формы от коробления при закалке применяют охлаждение в специальных штампах и приспособлениях. Расплавленные соли применяют при ступенчатой и изотермической закалке.
Прокаливаемость стали. Под прокаливаемостью подразумевают способность стали закаливаться на определенную глубину. Прокаливаемость не надо смешивать с закаливаемостью, которая характеризуется максимальным значением твердости, приобретенной сталью в результате закалки. Прокаливаемость — одна из важнейших характеристик качества стали, во многом определяющая служебные свойства, надежность и долговечность работы машин. Знать фактическую прокаливаемость различных сталей необходимо для их рационального применения.
то скорость охлаждения в сердцевине будет меньше критической скорости закалки для данной стали, и детали будут прокаливаться только на некоторую глубину а или б, т. е. прока-ливаемость будет неполной и в сердцевине образуются троостит, сорбит или сохранится исходная структура. Следовательно, чем меньше критическая скорость закалки, тем больше прокаливаемость.
Критическая скорость закалки уменьшается, и, следовательно, прокаливаемость увеличивается: 1) с повышением в стали содержания углерода и легирующих элементов (марганца, хрома, никеля, молибдена и других, за исключением кобальта), растворенных в аустените, повышающих устойчивость переохлажденного аустенита; 2) с укрупнением зерна аустенита (с уменьшением суммарной протяженности границ зерен аустенита, по которым преимущественно образуются центры кристаллизации).
Критическая скорость закалки увеличивается, и, следовательно, прокаливаемость уменьшается; 1) при неоднородной структуре, например при наличии карбидов, неметаллических включений, являющихся дополнительными центрами кристаллизации; 2) с уменьшением размера зерна аустенита (с увеличением суммарной протяженности границ зерен аустенита, по которым преимущественно образуются центры кристаллизации).
За глубину прокаливаемости обычно принимают расстояние от поверхности до зоны с полумартенситной структурой (50%
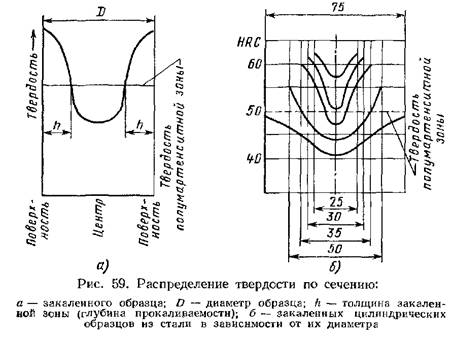
мартенсита и 50% троостита). Прокаливаемость определяют не по микроструктуре, а измерением твердости. Твердость стали с по-лумартенситной структурой зависит от содержания углерода, повышается с увеличением содержания углерода.
Прокаливаемость можно определить по излому, измерением твердости по сечению образца и измерением твердости по длине образца (методом торцовой закалки). Прокаливаемость по излому определяют на образцах сечением 20x20 мм, длиной 100 мм с надрезом для излома. Образцы нагревают в печи до температуры закалки, после выдержки охлаждают в воде, ломают и по излому определяют глубину прокаливаемости.
полученная как результат пересечения линии твердости полумар-тенситной зоны с кривой распределения твердости по сечению, и будет являться глубиной прокаливаемости; для данной стали в зависимости от размера (диаметра) образца и охлаждающей среды она будет различная (рис. 59, б).
Чтобы про-
под которым понимается диаметр максимального сечения образца, прокаливающегося насквозь в идеальной закалочной жидкости, отнимающей тепло с бесконечно большой скоростью.
Определять прокаливаемость по изменению твердости по сечению цилиндрического образца трудно, так как прежде чем измерить твердость, необходимо разрезать закаленный образец, имеющий большую твердость. Наиболее распространенным методом определения прокаливаемости в связи с его простотой и универсальностью является метод торцовой закалки, впервые предложенный акад. Н. Т. Гудцовым в 1924 г. Поэтому методу определяют прокаливаемость углеродистых и легированных конструкционных, инструментальных и подшипниковых сталей (за исключением сталей, закаливающихся на воздухе, и сталей с низкой прокаливае-мостью). Сущность данного метода заключается в следующем. Цилиндрический образец (диаметром 25 мм и длиной 100 мм) нагревают (с защитой от окисления) до температуры закалки и после выдержки помещают в специальную установку (рис. 60), в которой образец охлаждается с торца струей воды. Для измерения
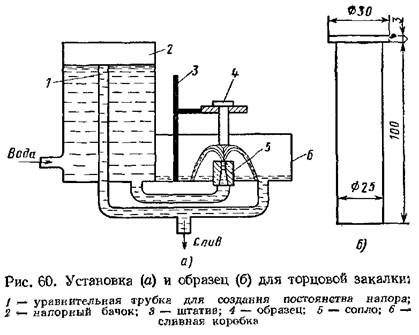
твердости закаленного образца по всей его длине с двух противоположных сторон сошлифовывают две фаски. Твердость измеряют от охлажденного торца. Распределение твердости наносят на диаграмму, на которой по вертикальной оси откладывают твердость, а по горизонтальной оси — расстояние от охлаждаемого
торца (рис, 61).
то сталь имеет большую прокаливаемость, чем сталь 2.

По характеристическому расстоянию с помощью заранее построенных номограмм можно определить критические диаметры для образцов различной формы и размеров, охлаждаемых при закалке погружением в разные среды. Одна из таких номограмм, разработанная проф. М. Е. Блантером, приведена в упрощенном виде на рис. 62. Номограммой пользуются следующим образом. Пусть по данным торцовой пробы характеристическое расстояние равно 6 мм. Требуется определить критические диаметры при охлаждении в воде и масле шара, а также цилиндрической детали с отношением длины к диаметру
На шкале
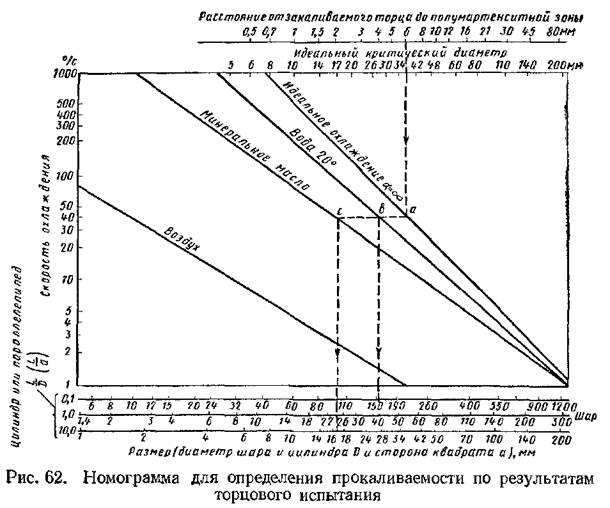
10,0. В точках
пересечения с этими шкалами читаем ответ — при закалке в воде критический диаметр для шара 40 мм, для цилиндра 27 мм; при закалке в масле — для шара 25 мм, для цилиндра 17 мм.
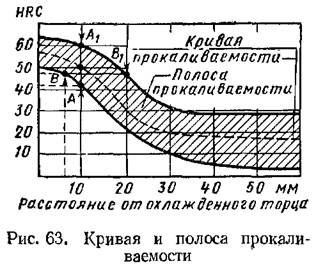
Так как прокаливаемость зависит от химического состава стали, а каждая марка стали содержит минимум и максимум входящих в нее элементов, то прокаливаемость стали данной марки характеризуется марочной полосой прокаливаемости, определяемой граничными кривыми, установленными для нескольких плавок данной марки стали (рис. 63). Вместо кривой или полосы прокаливае-
мости прокаливаемость стали характеризуется цифровыми


В зависимости от прокаливаемости сталь разделяют на мало-, средне- и глубокопрокаливающуюся, К малопрокаливающимся относят углеродистую и низколегированную стали, образцы из которых диаметром до 12 мм имеют сквозную прокаливаемость при охлаждении в воде. К среднепрокаливающейся относя г легированную сталь, которую при закалке охлаждают в масле. Максимальный диаметр цилиндрических образцов, закаливающихся по всему сечению, равен 100—150 мм. К глубокопрокаливающейся относят высоколегированную сталь, образцы из которой диаметром более 150 мм имеют сквозную прокаливаемость при охлаждении в масле. Характерной особенностью этих сталей является их способность закаливаться при охлаждении на воздухе. Поэтому метод торцовой закалки, осуществляемый в воздушной среде, может быть применен для определения прокаливаемости глубокопро-каливающихся сталей только при снижении скорости охлаждения образца со стороны, противоположной охлаждаемому торцу. Этого достигают, применяя различные методы; например, часть образца, противоположную охлаждаемому торцу, помещают в предварительно нагретую до 250—350° С печь или в теплоизоляционную упаковку и выступающий (из печи, из упаковки) торец образца охлаждают струей воды.
Сервис онлайн-записи на собственном Telegram-боте
Попробуйте сервис онлайн-записи VisitTime на основе вашего собственного Telegram-бота:
— Разгрузит мастера, специалиста или компанию;
— Позволит гибко управлять расписанием и загрузкой;
— Разошлет оповещения о новых услугах или акциях;
— Позволит принять оплату на карту/кошелек/счет;
— Позволит записываться на групповые и персональные посещения;
— Поможет получить от клиента отзывы о визите к вам;
— Включает в себя сервис чаевых.
Для новых пользователей первый месяц бесплатно.
Зарегистрироваться в сервисе
Для большинства деталей нет необходимости иметь сквозную прокаливаемость по всему сечению. Для обеспечения надежности работы деталей машин достаточно иметь закаленный слой, содержащий 90% мартенсита, на глубину не менее 1/4—1/2 радиуса детали. Только для некоторых деталей, например пружин и рессор (подвергающихся упругим деформациям), необходима сквозная прокаливаемость.
|