Технология термической обработки металловВнутренние напряжения в закаленной стали
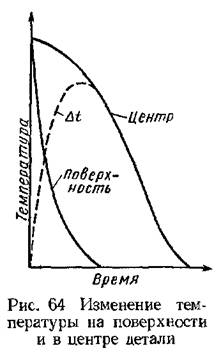
При закалке в детали возникают значительные внутренние напряжения — термические и структурные.
тем
больше, чем ниже температура поверхности. Период охлаждения, когда разность температур достигает максимума, является наиболее вероятным для развития внутренних напряжений. В этот период охлаждения в поверхностных слоях детали будут возникать напряжения растяжения, а в сердцевине — напряжения сжатия. В процессе дальнейшего охлаждения происходит перераспределение напряжений и после окончания охлаждения: при температуре до 20° С поверхностные слои детали будут испытывать напряжения сжатия, а сердцевина — напряжения растяжения (рис. 65, а). Эти напряжения называются остаточными напряжениями.
Структурные напряжения возникают в результате того, что превращение аустенита в мартенсит (связанное с увеличением объема) в разных местах детали происходит не одновременно. Температура мартенситного превращения сначала достигается в поверхностных слоях, в которых появляются временные сжимающие напряжения, а во внутренних слоях напряжения растяжения. Затем мартенситное превращение протекает во внутренних слоях и знак напряжений на поверхности и в сердцевине изменяется. Эпюра структурных остаточных напряжений после сквозной закалки имеет вид, показанный на рис. 65, б.
При закалке термические и структурные напряжения суммируются
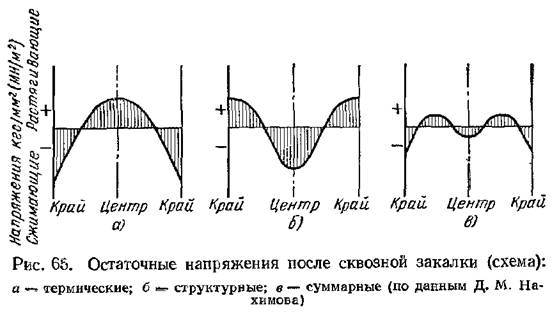
В зависимости от условий охлаждения, сечения деталей, глубины закалки и других факторов суммарные остаточные напряжения могут быть различными. Один из примеров эпюры суммарных остаточных напряжений показан на рис. 65, в.
Структурные напряжения опасны тем, что они возникают при появлении хрупкой структуры мартенсита. Если напряжения достигнут предела прочности, то образуются трещины. Наиболее опасными являются напряжения растяжения на поверхности, возникающие в основном вследствие структурных напряжений, которые надо при закалке уменьшать.
Способы закалки. Непрерывную закалку в одной среде (рис. 66, кривая 1) применяют наиболее широко. Деталь нагревают до температуры закалки и охлаждают в одной среде. Если охлаждение производят в жидкой среде (воде, масле), то для равномерного охлаждения деталь, погрузив в жидкую среду, перемещают в вертикальной плоскости или круговыми движениями. Для равномерного охлаждения жидкость перемещают с помощью лопастей, установленных в закалочном баке, или непрерывно подают и отводят из закалочного бака охлаждающую жидкость. Если требуется закалить не всю деталь, а только определенную часть, в охлаждающую жидкость погружают эту часть детали или применяют струйное охлаждение. Такую закалку называют местной.
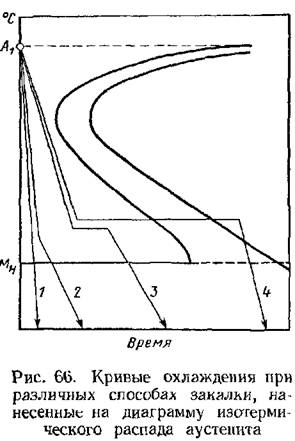
Для равномерной закалки и уменьшения коробления (особенно длинных цилиндрических деталей, тонких плоских деталей и др.) применяют специальные закалочные машины и прессы. В закалочной машине или закалочном прессе деталь при охлаждении находится в зажатом положении (например, валы и оси между зажимными роликами, зубчатые колеса —- в штампах, пилы — между плитами и т. п.).
Большое распространение имеют различные автоматизированные закалочные агрегаты непрерывного действия, в которых детали из закалочной печи после нагрева сбрасываются с конвейера в закалочный бак и выдаются из него с помощью конвейера. Недостатком закалки в одном охладителе (если закалка производится в воде) является возникновение значительных внутренних напряжений, которые могут вызвать появление трещин.
При закалке с подстуживанием деталь вынимают из печи и перед погружением в охлаждающую жидкость некоторое время выдерживают на воздухе (подстуживают). При подстуживании температура детали не должна понизиться ниже критической точки. Подстуживание уменьшает внутренние напряжения и коробление деталей,
При закалке в двух средах (прерывистая закалка, рис. 66, кривая 2) деталь охлаждают до 300—400° С в энергично действующем охладителе — воде, а затем для окончательного охлаждения переносят в слабый охладитель — масло. Такая закалка иначе называется закалкой в воде с переброской в масло. Быстрое охлаждение при закалке необходимо для того, чтобы в процессе охлаждения не произошло распада аустенита на феррито-цементит-ную смесь в интервале температур 500—600° С. Для превращения аустенита в мартенсит быстрое охлаждение не только не нужно, но и нежелательно, так как именно при быстром охлаждении в интервале мартенситного превращения и могут возникнуть трещины. В интервале мартенситного превращения для уменьшения возникающих структурных внутренних напряжений и предохранения от возможности возникновения трещин желательно замедленное охлаждение. Этому требованию и удовлетворяет закалка в двух средах.
для
никаких структурных превращений не происходит и мартенсит образуется при охлаждении детали на воздухе.
, температура плавления 150° С и др.
сталь находится в состоянии пластичного аустенита, и детали легко могут быть подвергнуты правке.
и 50% хлористого калия (КС1), сохраняется светлая поверхность, так как хлористые соли при нагреве, а щелочи при охлаждении практически не окисляют поверхности детали. Это позволяет закаливать детали после их окончательной обработки резанием без последующей очистки или травления.

Большее количество воды приводит к сильному кипению при погружении нагретых деталей. Повышение закаливающей способности щелочей при добавлении к ним воды объясняется тем, что происходит испарение воды. Необходимая для испарения воды теплота интенсивно отнимается от охлаждаемой детали. При испарении воды скорость охлаждения понижается, поэтому необходимо в ванну периодически добавлять воду (по мере надобности).
Забиваем Сайты В ТОП КУВАЛДОЙ - Уникальные возможности от SeoHammer
Каждая ссылка анализируется по трем пакетам оценки: SEO, Трафик и SMM.
SeoHammer делает продвижение сайта прозрачным и простым занятием.
Ссылки, вечные ссылки, статьи, упоминания, пресс-релизы - используйте по максимуму потенциал SeoHammer для продвижения вашего сайта.
Что умеет делать SeoHammer
— Продвижение в один клик, интеллектуальный подбор запросов, покупка самых лучших ссылок с высокой степенью качества у лучших бирж ссылок.
— Регулярная проверка качества ссылок по более чем 100 показателям и ежедневный пересчет показателей качества проекта.
— Все известные форматы ссылок: арендные ссылки, вечные ссылки, публикации (упоминания, мнения, отзывы, статьи, пресс-релизы).
— SeoHammer покажет, где рост или падение, а также запросы, на которые нужно обратить внимание.
SeoHammer еще предоставляет технологию Буст, она ускоряет продвижение в десятки раз,
а первые результаты появляются уже в течение первых 7 дней.
Зарегистрироваться и Начать продвижение
Недостатком ступенчатой закалки является возможность ее применения для деталей диаметром до 10 мм из углеродистой стали. Это объясняется тем, что для крупных деталей скорость охлаждения в соляной ванне является недостаточной для того, чтобы переохладить аустенит до температуры, немного превышающей температуру начала мартенситного превращения. В связи с недостаточной скоростью охлаждения в зоне наименьшей устойчивости аустенита (500—600° С) произойдет частичный распад с образованием феррито-цементитной смеси, и твердость получится пониженной.
Для деталей из легированных сталей ступенчатую закалку применять нецелесообразно, так как они закаливаются в масле, которое достаточно медленно охлаждает в интервале температур мартенситного превращения.
Изотермическую закалку, впервые предложенную Д. К. Черновым, применяют широко. Так же, как и при ступенчатой закалкег охлаждение деталей, нагретых до температуры закалки, производится в соляных ваннах. Температура соляной ванны при изотермической закалке 250—400° С. Детали выдерживают в соляной ванне в течение времени (согласно С-кривой для данной стали), необходимого для полного распада аустенита. После выдержки детали охлаждают на воздухе (см. рис. 66, кривая 4). В результате изотермической закалки образуется бейнит твердостью ИКС 45—55, но достаточно пластичный. Изотермическую закалку целесообразно применять для деталей, склонных к короблению и образованию трещин.
Для нагрева деталей при закалке применяют камерные, конвейерные печи и другие. Большое распространение имеют тигельные электрические и электродные печи-ванны. Печи-ванны удобны в работе; нагрев деталей в них происходит быстрее, чем в камерных печах. При нагреве в печах-ваннах детали находятся в расплавленной соли; в них также удобно нагревать детали путем частичного погружения в расплавленную соль. К недостаткам нагрева в печах-ваннах можно отнести малую стойкость тиглей и в связи с этим частые остановки ванн; необходимость соблюдения осторожности при работе (возможно выплескивание расплавленных солей при попадании влаги в ванну); взрывоопасность некоторых солей при перегреве; обезуглероживание деталей при нагреве в некоторых солях.
|