Технология термической обработки металловДефекты цементации и меры по их предупреждению
Иногда в заэвтектоидной зоне цементованного слоя цементит собирается в крупные участки, окруженные ферритом. Сталь, способная образовывать такую структуру, называется анормальной (рис. 99). Грубые включения цементита термической обработкой устранить трудно, и часто на поверхности получаются мягкие пятна. Особая структура и свойства анормальной стали объясняются недостаточным раскислением стали при выплавке. Окислы железа растворяются в стали и мешают поглощению углерода. Мягкие пятна на поверхности цементованного слоя особенно опасны для углеродистых сталей; для легированных сталей анормальность не столь опасна, в связи с влиянием легирующих элементов, повышающих прокаливаемость. При цементации деталей из легированных сталей легирующие элементы поверхностной зоны цементованного слоя окисляются, что снижает прочность цементованных деталей.
Атмосферы, применяемые для газовой цементации, содержат кислород, двуокись углерода и водяной пар. Нагрев деталей из легированных сталей в таких атмосферах сопровождается не только образованием окислов железа на поверхности металла,
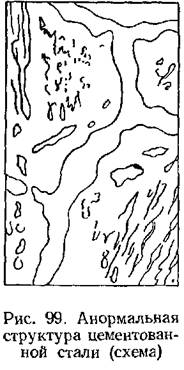

При внутреннем окислении: 1) железо взаимодействует с кислородом атмосферы печи с образованием на поверхности металла атомарного кислорода; 2) атомарный кислород диффундирует через кристаллическую решетку к зоне протекания реакций окисления; 3) легирующие элементы взаимодействуют с кислородом. Окисление легирующих элементов с образованием окислов возможно в том случае, если свободная энергия образования окислов легирующих элементов ниже свободной энергии образования окислов железа. В зависимости от способности к внутреннему окислению легирующие элементы располагаются в следующем
(в со-


. На величину зоны внутреннего окисления влияет расход эндогаза. С повышением расхода эндогаза увеличивается глубина зоны внутреннего окисления. Глубина окисленного слоя определяется также температурой, длительностью процесса и содержанием кислорода в печной атмосфере и может достигать 0,03 мм, но возможно и более глубокое залегание окислов. На глубину зоны внутреннего окисления влияет количество легирующего элемента. С увеличением содержания хрома толщина слоя окислов уменьшается. При содержании в стали до 0,4% Мп зона внутреннего окисления не наблюдается. С повышением содержания марганца, особенно более 1 %, значительно увеличивается толщина окисленного слоя. Титан содержится в сталях в небольших количествах, а поэтому влияние его незначительно. Такие элементы, как никель и молибден, уменьшают внутреннее окисление, особенно молибден, который не окисляется в эндотермической атмосфере. На процесс внутреннего
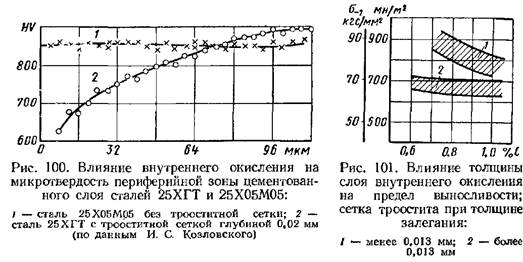
окисления влияет и шероховатость поверхности. С уменьшением шероховатости поверхности уменьшается глубина залегания окислов и их количество. Внутреннее окисление уменьшает содержание легирующих элементов в твердом растворе, что снижает легированность стали, повышает критическую скорость закалки (понижает прокаливаемость) и при закалке в масле приводит к немартенситному превращению аустенита. Поэтому в структуре цементованного слоя на поверхности появляется темная сетка, называемая трооститной сеткой, что приводит к снижению микротвердости при закалке (рис. 100). При отсутствии внутреннего окисления в цементованном слое образуется однородная дисперсная структура мартенсита. Внутреннее окисление влияет на прочностные показатели деталей. Наибольшее снижение прочностных показателей происходит при толщине залегания трооститной сетки более 0,013 мм (рис. 101).
Для устранения трооститной сетки (сохранения закаливаемости) за 5—10 мин до окончания процесса вводят в печную атмосферу аммиак в количестве 2,5—10% (при 10%-ной добавке аммиака трооститная сетка не образуется). Это приводит к повышению твердости при закалке в связи с легированием поверхностного слоя азотом (содержание азота в поверхностной зоне слоя достигает 0,1—0,2%). Но для деталей больших сечений азот не увеличивает устойчивости аустенита даже при содержании его в слое до 0,5—0,6%.
Долговечность деталей можно повысить, устраняя влияние зоны внутреннего окисления последующей обработкой на металлорежущих станках, при которой удаляется зона слоя, содержащая продукты немартенситного распада. Но в условиях массового производства это не всегда возможно. Кроме того, при обработке на металлорежущих станках может понизиться прочность тонких поверхностных слоев. Поэтому основными мерами борьбы с вредным влиянием внутреннего окисления являются: 1) применение сталей, легированных элементами, не склонными к окислению в эндотермической атмосфере; 2) увеличение скоростей охлаждения при закалке, что предотвращает появление продуктов немартенситного распада в поверхностных слоях деталей.
, выделяются карбиды легирующих элементов, что приводит к обеднению твердого раствора легирующими элементами. Одновременно снижается концентрация углерода в твердом растворе цементованного слоя на глубине 0,2 мм от поверхности. Образовавшиеся карбиды сохраняются и во втором периоде насыщения при пониженном углеродном потенциале.
Следовательно, при ступенчатых режимах цементации даже при оптимальной концентрации углерода на поверхности происходит перераспределение легирующих элементов между фазами цементованного слоя. В результате при последующей закалке в масле в структуре цементованного слоя появляется троостит-ная сетка (в связи с понижением прокаливаемости), снижаются поверхностная твердость и долговечность деталей. Для предотвращения образования трооститной сетки в цементованном слое в связи с образованием карбидов не следует осуществлять ступенчатые режимы цементации для деталей из сталей, склонных к образованию стойких карбидов, или применять стали, менее склонные к образованию карбидной фазы при ступенчатой цементации (по экспериментальным данным это стали, содержащие не менее 0,5% Мо и не более 0,5% Сг).
Обезуглероживание поверхности цементованного слоя происходит при подстуживании на воздухе и при отсутствии автоматического регулирования углеродного потенциала во втором периоде насыщения.
В процессе цементации и последующей закалки на мартенсит изменяются размеры и форма деталей под влиянием различных напряжений: остаточных (от предыдущей обработки), термических (образовавшихся при нагреве и охлаждении), структурных (возникающих в результате фазовых и структурных превращений) и внешних (под действием собственной массы деталей или массы садки). Для уменьшения коробления и стабилизации размеров деталей в процессе насыщения и последующей термической обработки могут быть рекомендованы: подготовка структуры и снятие наклепа после предварительной обработки; правильная укладка, фиксация и транспортировка деталей на приспособлениях; стабилизация всех технологических параметров химико-термической обработки; правильный выбор применяемого оборудования; повышение равномерности нагрева и охлаждения (например, закалка в горячем масле с температурой 160—180° С); повышение равномерности насыщения (принудительная циркуляция печной атмосферы, регулирование углеродного потенциала); закалка деталей, склонных к короблению, в оправках и штампах; обработка холодом цементованных деталей высокой точности после закалки на мартенсит и др.
Забиваем Сайты В ТОП КУВАЛДОЙ - Уникальные возможности от SeoHammer
Каждая ссылка анализируется по трем пакетам оценки: SEO, Трафик и SMM.
SeoHammer делает продвижение сайта прозрачным и простым занятием.
Ссылки, вечные ссылки, статьи, упоминания, пресс-релизы - используйте по максимуму потенциал SeoHammer для продвижения вашего сайта.
Что умеет делать SeoHammer
— Продвижение в один клик, интеллектуальный подбор запросов, покупка самых лучших ссылок с высокой степенью качества у лучших бирж ссылок.
— Регулярная проверка качества ссылок по более чем 100 показателям и ежедневный пересчет показателей качества проекта.
— Все известные форматы ссылок: арендные ссылки, вечные ссылки, публикации (упоминания, мнения, отзывы, статьи, пресс-релизы).
— SeoHammer покажет, где рост или падение, а также запросы, на которые нужно обратить внимание.
SeoHammer еще предоставляет технологию Буст, она ускоряет продвижение в десятки раз,
а первые результаты появляются уже в течение первых 7 дней.
Зарегистрироваться и Начать продвижение
Неравномерная глубина цементованного слоя является ре-зультатом неравномерности температуры в рабочем пространстве печи, плохой циркуляции печной атмосферы, наличия загрязнений и сажи на поверхности цементуемых деталей.
Недостаточная глубина цементованного слоя получается при нарушении режима подачи карбюризатора, понижении температуры цементации, недостаточной выдержке, излишнем количестве деталей в печи, загрязнении рабочего пространства печи сажей и коксом, плохой герметичности рабочего пространства печи. Эти же причины приводят к понижению концентрации углерода в цементованном слое.
Чрезмерно большая глубина цементованного слоя и повышенная концентрация углерода в слое с образованием грубых карбидных включений или сетки — результат высокой температуры процесса, длительной выдержки, применения активного карбюризатора и большой скорости его подачи.
Отслаивание закаленного цементованного слоя происходит при резком переходе цементованного слоя к сердцевине или наличии карбидной сетки из-за высокой активности и большой скорости подачи карбюризатора.
Пятнистая цементация получается при анормальной структуре стали, загрязнении деталей, неравномерном отложении сажи на цементуемой поверхности, неправильной укладке деталей. Так как появление дефектов при цементации может быть связано не только с природой стали, как показано выше, но и с нарушением технологии процесса цементации, основным требованием при проведении цементации является строгий контроль и соблюдение технологического режима.
|