Технология термической обработки металловДиффузионное хромирование
Хромирование — процесс насыщения поверхностного слоя стали хромом для повышения коррозионной стойкости и жаростойкости, а при хромировании высокоуглеродистых сталей — для повышения твердости и износостойкости.
При хромировании в порошкообразных смесях детали нагревают в стальных ящиках в смеси, состоящей из 50% хрома (феррохрома), 49% глинозема (каолина) и 1% хлористого аммония. Применяют также смесь, состоящую из 60% хрома (феррохрома), 35% глинозема (каолина) и 5% соляной кислоты. Измельченный хром (феррохром) сначала обрабатывают соляной кислотой, а затем смешивают с глиноземом (каолином). Температура хромирования 1000—1050° С, выдержка 6—12 ч, получаемая толщина слоя 0,08—0,15 мм на деталях из низкоуглеродистой стали и 0,01—0,03 мм на деталях из высокоуглеродистой стали.
При хромировании в смеси хрома (феррохрома) с хлористым аммонием протекают реакции:

При контакте поверхности нагретой детали с газообразным
хлоридом хрома происходит реакция

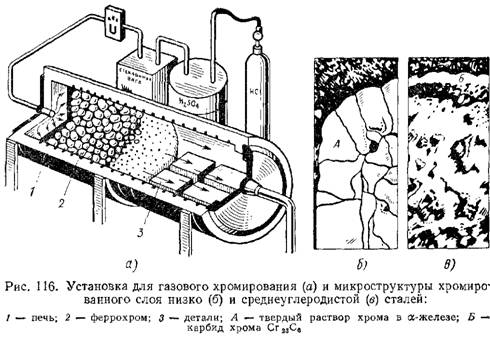
Образующийся атомарный хром диффундирует в поверхность детали.
Газовое хромирование осуществляют следующим образом, Через реторту, где помещены феррохром (хром) и детали (рис. 116), пропускают смесь водорода и хлористого водорода или газообразный хлористый водород (хлор). В первом случае водород пропускают через концентрированную соляную кислоту и вытесненный хлористый водород вместе с водородом поступает в реторту, нагретую до 950—1000° С. При воздействии на феррохром (хром) хлористого водорода образуется легкоиспаряющийся хлорид хрома:

который и диффундирует в поверхность детали. После выдержки в течение 5—6 ч получается слой толщиной 0,08—0,10 мм.
или 20—25% порошка
феррохрома. После выдержки в течение 10—15 мин получается слой толщиной 0,01—0,03 мм; недостаток способа — понижение активности ванны в связи с накапливанием продуктов реакции.
Хромированию подвергают детали из сталей с различным содержанием углерода. С повышением содержания углерода в стали процесс хромирования замедляется. При одной и той же температуре и выдержке на деталях из низкоуглеродистой стали получается значительно более глубокий слой, чем на деталях из высокоуглеродистой стали. В зависимости от содержания углерода в хромируемой стали фазовый состав и свойства хромированного слоя получаются различными.
. Содержание углерода в поверхностном слое достигает 7—8%, а хрома — 75— 95%. В зоне, расположенной непосредственно за хромированным слоем, содержание углерода повышено по сравнению с содержанием углерода в сердцевине в связи с тем, что не весь продиффун-дировавший к поверхности углерод используется для образования карбидного поверхностного слоя, так как скорость диффузии углерода больше скорости диффузии хрома.
Твердость поверхности деталей из хромированной низкоуглеродистой стали невысокая — НV 180—280, а деталей из высокоуглеродистой стали доходит до НУ 1350 и превосходит твердость не только цементованной и закаленной стали, но и азотированной. Хромированный слой на деталях из средне- и высокоуглеродистой сталей обладает высокой износостойкостью. Хромированный слой на деталях из низкоуглеродистой стали обладает хорошей пластичностью; детали можно сгибать, осаживать, сплющивать и т. п. Хромированный слой на деталях из высокоуглеродистой стали обладает повышенной хрупкостью, особенно на острых гранях, что является его основным недостатком.
Антикоррозионными свойствами во многих средах (растворах поваренной соли, морской воде, сернистых и углекислых газах и т. п.) обладают хромированные слои, полученные на деталях из любых сталей, но более стойки стали с карбидным слоем, которые хорошо сопротивляются действию 20%-ной соляной кислоты и 30—50% -ной азотной кислоты. Жаростойкость хромированной стали ограничивается температурой 800° С. Хромированию подвергают различные детали: клапаны компрессоров, втулки наеосов, матрицы для холодной высадки и др.
|