Технология термической обработки металловОкончательная термическая обработка
Режущий инструмент в основном изготовляют из быстрорежущей стали. Высокой твердостью и теплостойкостью (красностойкостью) должна обладать только режущая часть инструмента, т. е. та часть, которая непосредственно производит работу, а хвостовая часть должна обладать только достаточной прочностью, поэтому для экономии дефицитной, дорогостоящей быстрорежущей стали инструмент диаметром 9—10 мм и более изготовляют составным: режущую часть из быстрорежущей стали, а хвостовую часть из углеродистой стали 40, 45, Стб или для повышения прочности из легированной стали 40Х.
Наилучшим способом соединения быстрорежущей и углеродистой части инструмента является стыковая сварка. Сваренные заготовки помещают в печь, нагретую до 650—700° С, затем в этой же печи отжигают. Место сварки следует выбирать с учетом технико-экономических показателей, т. е. с максимальной
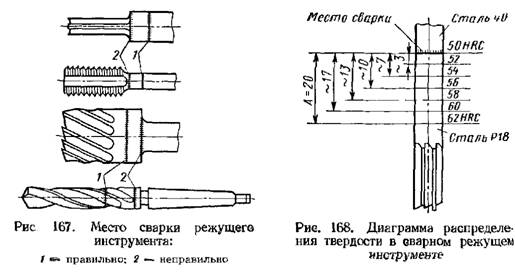
экономией быстрорежущей стали. Места сварки для некоторых типов инструментов приведены на рис. 167, Сваренные заготовки контролируют путем внешнего осмотра.
В соляных ваннах нагревают только часть сварного инструмента, изготовленную из быстрорежущей стали, которая должна иметь высокую твердость. Твердость в месте сварки должна быть не выше HRC 50—55, так как более высокая твердость увеличивает хрупкость инструмента.
Для получения зоны с постепенно снижающейся твердостью от рабочей части к месту сварки инструмент следует погружать в соляную ванну рабочей частью из быстрорежущей стали на рас стояние А (рис. 168) от места сварки. Это расстояние зависит от размера инструмента.

Режущую и хвостовую часть составного инструмента обрабатывают по разным режимам.
Термическую обработку режущего инструмента разделяют на три стадии: 1) предварительную термическую обработку — отжиг, высокий отпуск, улучшение — для снижения твердости, улучшения обрабатываемости резанием, снятия наклепа и подготовки структуры к последующим операциям термической обработки ; 2) окончательную термическую обработку — закалка и отпуск, формирующие эксплуатационные свойства инструмента; 3) дополнительную обработку после шлифования и заточки — цианирование, обработка паром, низкотемпературный отпуск для повышения стойкости, антикоррозионных свойств и улучшения товарного вида инструмента.
Закалка — основная операция термической обработки инструмента, которая определяет (вместе с отпуском) его стойкость в процессе эксплуатации. Твердость после закалки должна быть ИКС 62—65, структура — мартенсит скрытокристаллического или мелкоигольчатого строения (наличие игольчатого мартенсита допустимо для резцов некоторых типов) и равномерно распределенные карбиды. Величина зерна аустенита при нагреве под закалку должна соответствовать 10—11-му баллу и в отдельных случаях 9-му баллу (при увеличении 400 или 500). Состав мартенсита определяется химическим составом стали и условиями закалки. Содержание углерода в мартенсите углеродистой стали составляет 0,7—0,8%, в быстрорежущей 0,3—0,5%. Теплостойкость углеродистой и легированной сталей должна быть не ниже 200—250° С, а быстрорежущей — 600—650° С. Прочность инструмента зависит от характера распределения карбидов, количества остаточного аустенита и величины напряжений, возникающих в процессе закалки.
Все перечисленные свойства инструмента зависят от режимов и условий закалки. Основные факторы, влияющие на результаты закалки: способ, температура и скорость нагрева, продолжительность выдержки при нагреве и условия охлаждения. Нагрев инструмента под закалку может проводиться в электрических печах с воздушной или нейтральной атмосферой, в печах с нефтяным и газовым обогревом, в печах-ваннах с расплавленными солями, с помощью т. в. ч. и в кипящем слое. Наиболее распространен нагрев в печах-ваннах.
Высокая скорость нагрева в соляных печах-ваннах может вызвать значительные внутренние напряжения, деформацию и образование трещин. Поэтому рекомендуется применять ступенчатый нагрев под закалку для инструмента большого размера, сложной конфигурации из быстрорежущих и легированных сталей. Продолжительность выдержки при нагреве должна обеспечить сквозной нагрев инструмента до заданной температуры и полное завершение фазовых превращений. Время выдержки в расплавах солей может быть определено расчетным путем с учетом химического состава стали, температуры нагрева, формы и размеров инструмента или принято по данным машиностроительных и инструментальных заводов. При выборе среды охлаждения необходимо учитывать марку стали, форму и размер инструмента, требуемую структуру и твердость. Кроме того, поверхность после охлаждения должна быть чистой, без следов разъедания. Для охлаждения инструмента при закалке применяют воду и водные растворы, масла, расплавленные соли и щелочи, воздух. Воду и водные растворы применяют при закалке инструмента из углеродистой стали. Крупный инструмент рекомендуется сначала охлаждать в воде, а затем переносить в масло (при температуре начала мартенситного превращения). При охлаждении в масле значительно снижаются внутренние напряжения, но масло в процессе работы стареет, опасно в пожарном отношении и вызывает трудности в процессе отмывки и обезжиривания инструмента (особенно после нагрева в расплавленных солях). Поэтому его стараются заменить другими охлаждающими средами.
При ступенчатой и изотермической закалках применяют расплавы солей и щелочей. Их недостатки: изменение охлаждающей способности и жидкотекучести в процессе работы. Ниже приводится общая схема закалки инструмента из различных групп сталей.
Для инструмента из углеродистой стали: 1) подсушивание поверхности (во избежание разбрызгивания солей) при 400° С; 2) подогрев при 600—650° С (для инструмента с расчетной толщиной более 20 мм); 3) окончательный нагрев при 770—790° С; 4) охлаждение; инструмент с расчетной толщиной до 8 мм (метчики до 12 мм) охлаждают в расплаве солей при 160—180° С; инструмент с расчетной толщиной более 8 мм охлаждают до 150— 200° С в 5%-ном водном растворе поваренной соли, а затем переносят в масло и выдерживают до полного охлаждения.
Забиваем Сайты В ТОП КУВАЛДОЙ - Уникальные возможности от SeoHammer
Каждая ссылка анализируется по трем пакетам оценки: SEO, Трафик и SMM.
SeoHammer делает продвижение сайта прозрачным и простым занятием.
Ссылки, вечные ссылки, статьи, упоминания, пресс-релизы - используйте по максимуму потенциал SeoHammer для продвижения вашего сайта.
Что умеет делать SeoHammer
— Продвижение в один клик, интеллектуальный подбор запросов, покупка самых лучших ссылок с высокой степенью качества у лучших бирж ссылок.
— Регулярная проверка качества ссылок по более чем 100 показателям и ежедневный пересчет показателей качества проекта.
— Все известные форматы ссылок: арендные ссылки, вечные ссылки, публикации (упоминания, мнения, отзывы, статьи, пресс-релизы).
— SeoHammer покажет, где рост или падение, а также запросы, на которые нужно обратить внимание.
SeoHammer еще предоставляет технологию Буст, она ускоряет продвижение в десятки раз,
а первые результаты появляются уже в течение первых 7 дней.
Зарегистрироваться и Начать продвижение
Для инструмента из легированной стали: 1) подсушивание поверхности при 400° С; 2) подогрев при 600—650° С (для инструмента с расчетной толщиной бол ее 20 мм); 3) окончательный нагрев (температура определяется маркой стали); 4) охлаждение; инструмент с расчетной толщиной менее 20 мм охлаждают в расплаве солей; с толщиной более 20 мм — в масле.
Для инструмента из быстрорежущей стали: 1) подсушивание поверхности при 400° С; 2) первый подогрев при 600—650° С (для инструмента с расчетной толщиной более 20 мм); 3) второй подогрев при 800—850° С (обязателен для инструмента всех размеров); 4) окончательный нагрев; 5) охлаждение; длинный стержневой инструмент охлаждают в масле до 200—250° С и передают на правку; остальной инструмент рекомендуется охлаждать ступенчато: до 500—550° С в соляной ванне, далее на воздухе (инструмент с расчетной толщиной более 20 мм подстуживают на воздухе до 300—400° С, затем передают на отпуск).
в течение 3—5 мин при 70—80° С.
при темпера-
туре 140—200° С (чаще при 150—180е С) с последующим охлаждением на воздухе. В печах с воздушной атмосферой (даже при наличии циркуляции воздуха) стабильность свойств отпущенного инструмента не достигается.
Выдержка при отпуске инструментов из углеродистой и легированной сталей определяется температурой отпуска.
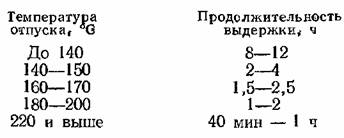
Для инструмента из быстрорежущей стали наиболее характерен трехкратный отпуск при 560—575° С с выдержкой по 1 ч с обязательным охлаждением после каждого отпуска на воздухе до 20е С, иначе в структуре остается неотпущенный мартенсит. Общая длительность отпуска составляет 15—24 ч, что не позволяет использовать его в единой поточной линии термической обработки инструмента. Поэтому в последнее время изыскивают режимы кратковременного отпуска при более высоких температурах до 600° С (с выдержкой 10—15 мин) с одновременным сокращением количества отпусков. Но кратковременный отпуск рекомендован для ограниченного промышленного применения в случае встраивания отпускных ванн в автоматизированные агрегаты с загрузкой инструментов в специальные приспособления в связи с возможностью понижения их твердости. Необходимым условием проведения кратковременного отпуска является контроль режима отпуска. Рекомендуемые режимы кратковременного отпуска приведены в табл. 23.
Цельный и сварной инструмент, имеющий хвостовик (HRC 30—45), для обеспечения требуемой твердости рабочей и хвостовой части подвергают различным вариантам термической обработки.
Для цельного инструмента с коротким хвостовиком применяют: а) закалку рабочей и хвостовой части (целиком), отпуск; кратковременный местный отпуск хвостовика при 500—550° С в течение 10—15 мин; б) закалку целиком с нагревом в соляной ванне в приспособлении, которое обеспечивает нагрев хвостовика до -более низких температур (неполная закалка) и отпуск.
Для цельного и сварного инструмента с длинным хвостовиком с целью уменьшения деформации производят отдельную закалку и отпуск рабочей и хвостовой части.
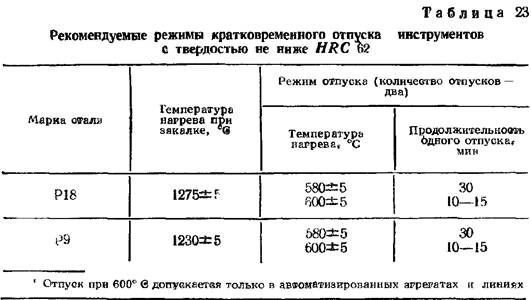

на 1 л воды)] при 15—20° С в течение 15—30 мин под давлением 5—6 кгс/см2; абразивная суспензия поступает по шлангу в форсунку, а из форсунки подается на обрабатываемый инструмент; эту операцию можно производить вручную на гидрополировальных аппаратах или на механизированных гидрополировальных установках; 2) в промывке холодной водой (15—20° С) в течение 2—3 мин; 3) в пассивировании.
Для устранения коробления инструмента, получающегося при термической обработке, его подвергают правке. В производственных условиях применяют следующие основные методы правки; 1) после закалки и отпуска в холодном состоянии; 2) после закалки и отпуска с подогревом (местным или общим) до температуры 150— 600° С; 3) в горячем состоянии в процессе охлаждения; 4) релак сационную в процессе закалки и отпуска (в штампах, зажимных устройствах и т. д.).
Кривизну и биение проверяют перед началом правки, в процессе правки (кроме последнего метода) и после ее окончания. Холодной правке подвергают инструмент, имеющий или невысокую твердость (после отжига), или небольшое коробление после закалки и отпуска.
Инструмент, имеющий значительную деформацию, подвергают горячей правке с подогревом, причем температура подогрева должна быть ниже температуры отпуска стали, из которой изготовлен инструмент. Целесообразно проводить горячую правку при ступенчатой закалке или закалке в горячем масле (для сталей с низкой критической скоростью закалки). При проведении правки в штампах инструмент нагревают до температур закалки, зажимают в штампах и интенсивно охлаждают в среде, применяемой для данной стали. Можно осуществлять правку в штампах и в процессе отпуска, причем охлаждение до температуры 20° С необходимо проводить также в штампах. Для правки применяют специальное оборудование — ручные и механические прессы.
|