Технология термической обработки металловПрактика термической обработки стали
Время нагрева
Чем больше в стали углерода и специальных примесей, тем менее она теплопроводна и медленнее должен быть ее нагрев. Поверхностные слои металла, нагретые до более высокой температуры, стремятся расшириться. Этому расширению препятствуют
внутренние, менее нагретые слои. В результате поверхностные слои будут испытывать напряжения сжатия, а внутренние — напряжения растяжения (рис. 40). Величина напряжений зависит от времени (скорости) нагрева: чем больше скорость нагрева, тем больше разность температур между поверхностью и сердцевиной и, следовательно, тем выше напряжения.
Величина возникающих напряжений не должна превосходить допустимую, так как в металле могут образоваться трещины. Наиболее опасно возникновение внутренних напряжений при нагреве до температур 500—800° С когда металл обладает малой пластичностью. При более высоких температурах возникновение внутренних напряжений неопасно, так как металл становится пластичным.
При термической обработке (в печах) возможны три способа нагрева (рис. 41): 1) детали загружают в холодную или разогретую до невысокой температуры печь (рис. 41, а); печь нагревают с деталями до заданной температуры; время нагрева большое, по разность температур по сечению небольшая; этот способ применяют при нагреве деталей из высоколегированных сталей и сложной формы, 2) летали загружают в печь, имеющую постоянную заданную
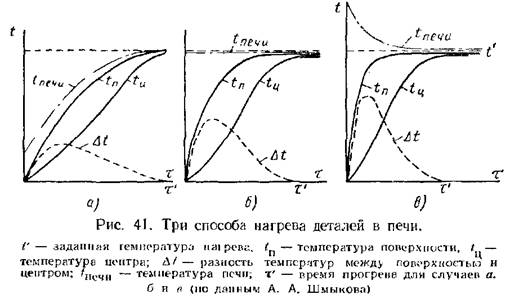
температуру (рис. 41, 6):
Время выдержки при заданной температуре может быть принято равным 1 мин для углеродистых сталей и 1,5—2 мин для легированных сталей.
Время нагрева до заданной температуры может быть определено несколькими способами.
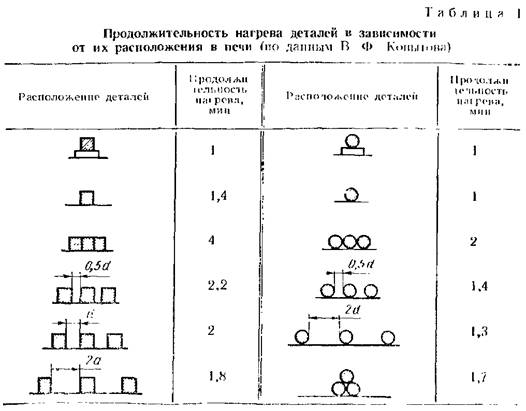

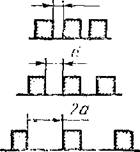

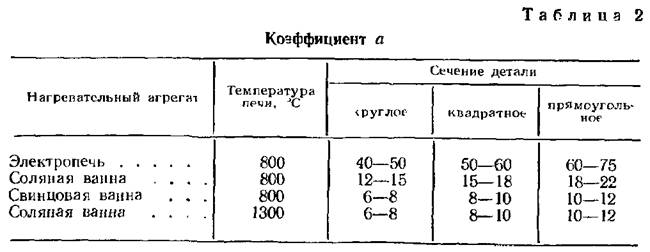

— коэффициент, определяемый экспериментально, с/мм;
следует использовать толщину Н детали. Значение коэффициента а в зависимости от условий нагрева и формы детали приведено в табл. 2.
Если нагревают несколько деталей, различно расположенных на поду печи, то результат, полученный по формуле (2), надо умножить на коэффициент равномерности нагрева (см. табл. 1). Этот способ определения времени нагрева наиболее простой и распространенный, но недостаточно точный, так как не учитывает влияние нагрева с торцов и соотношения длины и диаметра (толщины) детали.
2. Для деталей сложной формы значительной длины время нагрева

— диаметр шара, мм;
— время сквозного прогрева шара, мин. Время нагрева деталей разной формы в различных средах с учетом их расположения в печи

— коэффициент формы, он имеет следующие значения: 1 — для шара; 2— для цилиндра; 2,5 — для параллелепипеда; 4 — для пластины ;
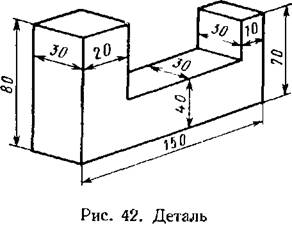
— коэффициент среды (для нагрева: 1—в соли, 0,5 — в свинце, 2 — в газовой среде);
— коэффициент равно мерности нагрева.
Для детали, показанной на рис. 42, сечением 30x40 мм
= 30 мм.
Этот способ определения времени нагрева является достаточно точным и наиболее удобным для практического применения.

— время нагрева, мин; V — объем тела, см3; Р — поверхность тела, см2; К — суммарный физический фактор нагрева, мин/см.
называется геометрическим показателем тела:

в формулу (5) получим

Геометрические параметры различных тел вычисляют по следующим формулам. Для шара
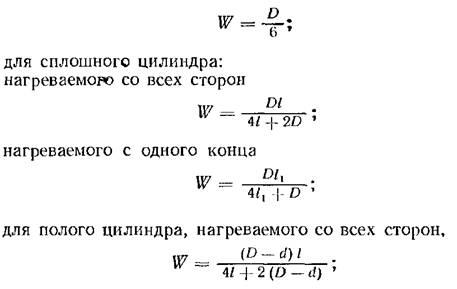
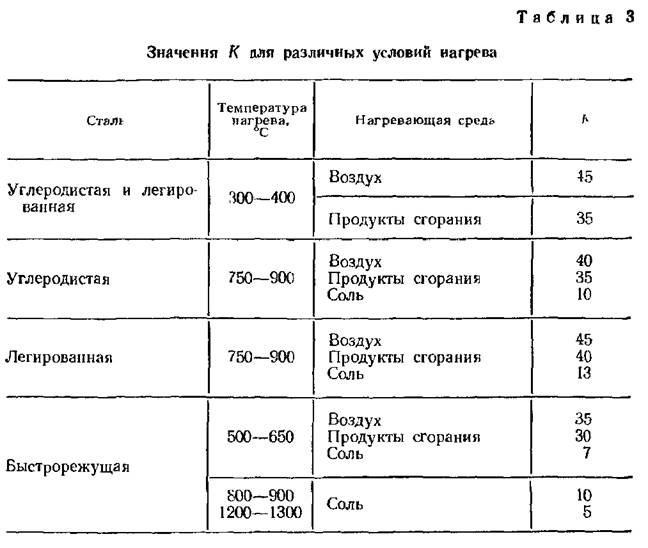
для прямоугольной пластины, нагреваемой со всех сторон,
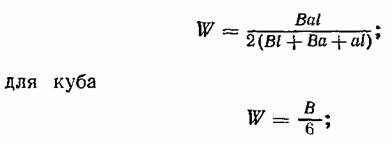
для призмы с основанием в виде квадрата, треугольника или правильного шестиугольника
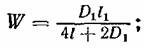
— внутренний диаметр, см;
— длина нагреваемой части, см; В — ребро куба, толщина пластины, см; а — ширина пластины, см.
Значения коэффициента К приведены в табл. 3.
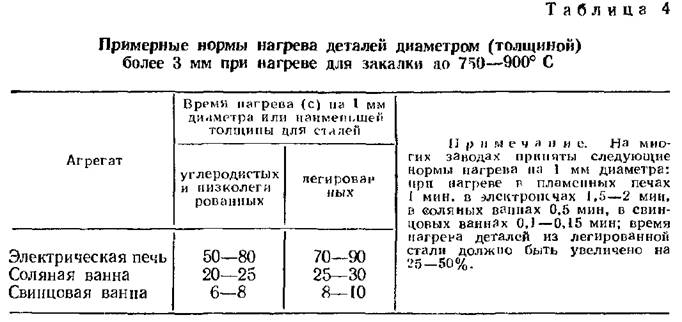
Все три приведенных способа применимы для определения времени нагрева деталей диаметром (стороной квадрата) 3—100 мм. Рекомендуемая продолжительность выдержки в камерных печах и ваннах приведена в табл. 4,
|