Технология термической обработки металловХимическое действие нагревающей среды
Общие сведения. При нагреве деталей в печах металл взаимодействует с атмосферой печи. Результатом такого взаимодействия является окисление, ведущее к образованию окалины на поверхности нагреваемого металла, и обезуглероживание — частичное или полное выгорание углерода в поверхностных слоях стали.
Окисление приводит к потерям металла, усложняет обработку деталей, затрудняет получение высокой и равномерной твердости. Потери металла при нагреве составляют до 3% массы обрабатываемых деталей. В обезуглероженном слое появляются мягкие пятна и возникают растягивающие напряжения, что снижает прочность, износостойкость и предел выносливости, т. е. снижает срок службы деталей.
В состав печной газовой атмосферы входят кислород, окись углерода, двуокись углерода, водород, азот, метан, водяной пар. Действие этих газов на сталь различно. Водород обезуглероживает, окись углерода и метан науглероживают. Водяной пар, двуокись углерода и кислород окисляют и обезуглероживают.
Рассмотрим процесс окисления. Вначале происходит химическая реакция между металлом и окисляющим газом, в результате чего на поверхности металла образуется окисная пленка. Дальнейший процесс окисления — это диффузия атомов кислорода сквозь пленку (к металлу) с окислением на границе металл— пленка; диффузия атомов металла сквозь пленку на ее наружную поверхность с окислением на границе пленка—газ или встречная диффузия атомов кислорода и металла.
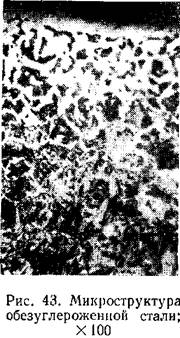
На интенсивность окисления влияют состав и строение окисной пленки. Если пленка пористая, окисление происходит интенсивно, если плотная, окисление замедляется или даже совершенно прекращается.
Процесс окисления есть диффузионный процесс; чем выше скорость диффузии, тем выше скорость окисления. С повышением температуры нагрева процесс диффузии резко ускоряется, поэтому и окисление будет происходить тем в большей степени, чем выше температура нагрева.
образуется менее плотный окисел РеО по следующим реакциям:
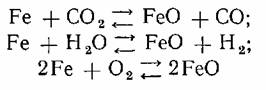
часть кислорода печной атмосферы находится в виде
окисление железа резко возрастает; при этом образуется слой окалины. Поэтому практически детали предохраняют от окисления при нагреве их до температур выше 500° С.
. Основные реакции обезуглероживания:
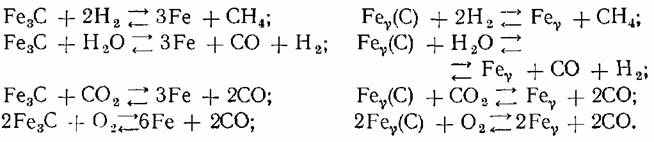
Обезуглероживание — скрытый дефект. Его можно обнаружить измерением твердости и по структуре стали (рис. 43). Степень обезуглероживающего действия печной атмосферы зависит от содержания в стали углерода и легирующих элементов; например, хром уменьшает, а кремний, вольфрам, молибден, ванадий увеличивают склонность к обезуглероживанию. На процесс обезуглероживания влияет и температура нагрева; чем выше температура, тем интенсивнее протекает обезуглероживание,
Для сохранения постоянства химического состава поверхности деталей при данном режиме нагрева и определенном химическом составе стали необходимо создать условия равновесия между металлом и печной атмосферой, т. е. иметь определенное соотношение окисляющих, обезуглероживающих, восстанавливающих и науглероживающих газов:
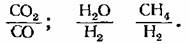
восстановление будут протекать в обе стороны с одинаковой скоростью, т. е. печная атмосфера будет нейтральной но отношению к нагреваемой детали.
должно быть не более 0,7, а отношение
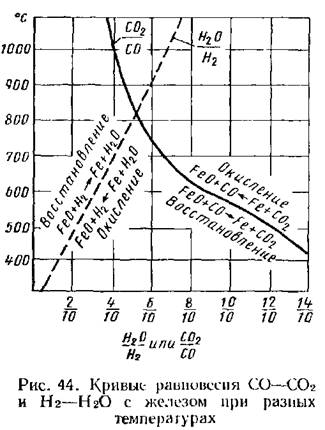
не более 0,4 (рис. 44).
Применение защитных атмосфер. Для предохранения деталей от окисления и обезуглероживания при высоких температурах в рабочее пространство печи искусственно вводят защитную газовую среду, называемую защитной или контролируемой атмосферой. Применяемая контролируемая атмосфера должна иметь низкую стоимость, быть простой в приготовлении, не должна образовывать излишних количеств сажи и кокса, не окислять и не обезуглероживать поверхность деталей при термической обработке.
Для защиты от окисления могут применяться инертные
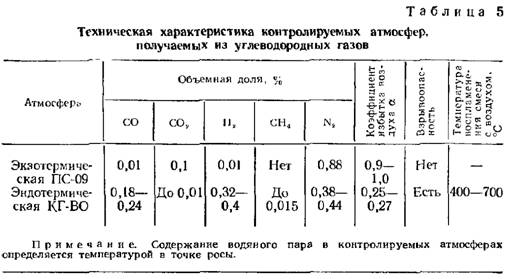
газы — аргон, неон и чистый азот, не содержащие даже следов кислорода, а также продукты диссоциации аммиака. Указанные газы требуют дополнительной очистки от агрессивных примесей и осушки, что повышает стоимость защитного газа в 2—3 раза. В связи с этим чистые газы применяются для защитных атмосфер ограниченно.
В современном машиностроительном производстве применяют контролируемые атмосферы двух типов: 1) экзотермическую — нейтральную при температуре ниже 700° С; 2) эндотермическую — универсальную, нейтральную при температуре выше 700° С (ниже 700° С она взрывоопасна).
Нейтральные контролируемые атмосферы получают путем сжигания углеводородных газов с коэффициентами избытка воздуха от 0,22 до 0,95. Данные о нейтральных атмосферах приведены в табл. 5. Для получения контролируемых атмосфер необходимы специальные установки.
Наиболее широкое применение находит эндотермическая атмосфера (эндогаз), которая применима как для безокислительного нагрева, так и для цементации. Характерной особенностью эндотермической атмосферы является то, что результаты ее взаимодействия с нагретой сталью зависят только от содержания влаги, количество которой контролируется определением температуры точки росы г. Следовательно, по температуре точки росы контролируется содержание углерода на поверхности стальной детали (углеродный потенциал) в момент установления равновесия с атмосферой данного состава.
Схема автоматического регулирования состава печной атмосферы на заданный углеродный потенциал в равновесных процессах
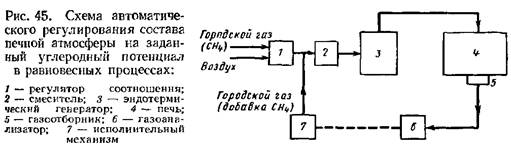
приведена на рис. 45. Углеродный потенциал атмосферы регулируется только соответствующим изменением состава газа, получаемого в газоприготовительной установке, обычно по температуре точки росы. Контролируемый газ отбирается из печи (газоотборник 5, устанавливаемый на стороне печи, противоположной газовводам) и подается в газоанализатор 6. При отклонении контролируемого газа от заданного состава поступает сигнал (штриховая линия на рис. 45) в исполнительный механизм 7, регулирующий добавку городского газа в смеситель 2 эндотермического генератора 3. Следовательно, добавка городского газа, изменяющая соотношение воздуха и природного газа, подаваемых в генератор, является основным фактором, определяющим качество автоматического регулирования состава печной атмосферы.
Забиваем Сайты В ТОП КУВАЛДОЙ - Уникальные возможности от SeoHammer
Каждая ссылка анализируется по трем пакетам оценки: SEO, Трафик и SMM.
SeoHammer делает продвижение сайта прозрачным и простым занятием.
Ссылки, вечные ссылки, статьи, упоминания, пресс-релизы - используйте по максимуму потенциал SeoHammer для продвижения вашего сайта.
Что умеет делать SeoHammer
— Продвижение в один клик, интеллектуальный подбор запросов, покупка самых лучших ссылок с высокой степенью качества у лучших бирж ссылок.
— Регулярная проверка качества ссылок по более чем 100 показателям и ежедневный пересчет показателей качества проекта.
— Все известные форматы ссылок: арендные ссылки, вечные ссылки, публикации (упоминания, мнения, отзывы, статьи, пресс-релизы).
— SeoHammer покажет, где рост или падение, а также запросы, на которые нужно обратить внимание.
SeoHammer еще предоставляет технологию Буст, она ускоряет продвижение в десятки раз,
а первые результаты появляются уже в течение первых 7 дней.
Зарегистрироваться и Начать продвижение
Недостатками схемы являются: 1) трудность регулирования печной атмосферы нескольких печей, работающих от одной газоприготовительной установки; 2) ограничение допустимого соотношения газа и воздуха, поступающих в газоприготовительную установку, в связи с выделением сажи, которая разрушает катализатор эндотермического генератора, снижает его активность и увеличивает сопротивление трубопроводов.
Применение расплавленных солей. Предохранение деталей от окисления и обезуглероживания осуществляется также нагревом в хорошо раскисленных расплавленных солях. Расплавленные соли или их смеси являются распространенными средами для нагрева.
Широкое применение при термической обработке соляных ванн объясняется тем, что расплавленные соли по сравнению с другими нагревающими (газовыми, воздушными) и охлаждающими (вода, масло, воздух) средами обладают большими преимуществами. Основные преимущества соляных ванн следующие: более быстрый и равномерный нагрев, более высокая производительность, меньший рост зерна при нагреве, удобство местного нагрева, уменьшение коробления стержневых деталей, возможность нагрева деталей в вертикальном положении, меньшие внутренние напряжения и деформация, исключение возможности образования трещин (при охлаждении в расплавленных солях), предохранение от окисления и обезуглероживания при нагреве и при переносе деталей из ванны в закалочный бак (детали покрыты тонкой пленкой соли).
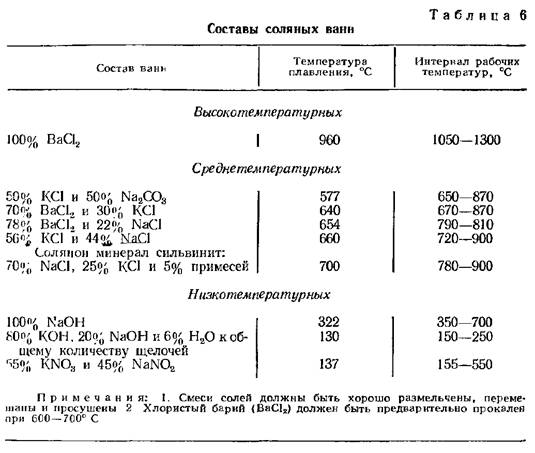
В зависимости от интервала рабочих температур соляные ванны условно подразделяют на высоко-, средне- и низкотемпературные. Некоторые составы соляных ванн приведены в табл. 6. Требования к солям, применяемым для термической обработки, следующие: хорошая растворимость в воде и малая гигроскопичность в твердом состоянии; высокая электропроводность; высокая жидко-текучесть; малая летучесть при рабочих температурах и инертность по отношению к нагреваемому металлу; простота состава и низкая стоимость.
Достаточная жидкотекучесть расплавов солей обеспечивается в том случае, если температура их плавления на 70—100° С ниже рабочей температуры ванны. Хорошую жидкотек учесть расплавам солей обеспечивает хлористый калий. В его присутствии получается светлая поверхность. Однако содержание хлористого калия в расплавах ограничивают (не более 30%) в связи с повышенной обезуглероживающей способностью.
Общим недостатком расплавов солей, как нагревающих сред, является их обезуглероживающее действие. Во избежание обезуглероживания деталей при нагреве в соляных ваннах необходимо периодически производить раскисление ванн. Раскисление высокотемпературных соляных ванн (с хлористым барием) обычно производится молотым 75%-ным ферросилицием, который добавляется в расплавленную соль 1—2 раза в смену в количестве 150—200 г за один прием, а также бурой. Раскисление среднетем-пературных соляных ванн производится: бурой — через каждые 4 ч работы добавляется 200—300 г буры; желтой кровяной солью в количестве 1—2% массы солей; древесным углем, для чего на дно ванны опускают на 10—15 мин ковш с отверстиями, наполненный углем. Происходящее вначале бурление ванны с появлением значительного количества языков пламени постепенно уменьшается и затем прекращается, что и указывает на конец раскисления. Раскисление низкотемпературных соляных ванн не производят.
Применение защитных покрытий. Новое в безокислительной термической обработке — применение защитных покрытий — стекловидных эмалей. Для таких покрытий применяют механические смеси тонких порошков стекол с огнеупорными наполнителями. В процессе нагрева происходит плавление легкоплавких, а затем тугоплавких составляющих смеси, и тем самым обеспечивается получение стекловидной расплавленной пленки, изолирующей металл от печной атмосферы.
при 500—550° С. Применять эмали целесообразно в условиях мелкосерийного производства.
|