Технология термической обработки металловПредварительная термическая обработка измерительного инструмента
Для исправления дефектов структуры (крупное зерно, цементитная сетка, пластинчатый перлит), снижения твердости (после ковки, штамповки, накатки резьбы и др.) и подготовки к окончательной термической обработке измерительный инструмент подвергают отжигу, улучшению и высокому отпуску.
690—710° С) применяют для доэвтектоидных сталей. Высокий отпуск проводят для снятия внутренних напряжений после обработки на металлорежущих станках и обработки давлением, а также перед повторной закалкой. Нормализацию применяют для исправления структуры сильно перегретой стали, устранения цементитной сетки и подготовки к закалке.
Для уменьшения деформации инструмента при закалке на мартенсит отожженные заготовки после предварительной обработки на металлорежущих станках подвергают улучшению — закалке в воде (для углеродистых сталей) или масле (для легированных сталей) с последующим высоким отпуском (650—680° С). В результате улучшения получается структура сорбита, наличие которой уменьшает деформацию при последующей закалке на мертенсит вследствие меньшей разницы в объемах между мартенситом и сорбитом, чем между мартенситом и перлитом. Кроме того, структура сорбита обеспечивает малую шероховатость поверхности после обработки на металлорежущих станках. После улучшения инструмент подвергают окончательной обработке резанием с оставлением припуска на шлифование.
Окончательная термическая обработка измерительного инструмента
Для получения требуемых свойств и структуры измерительный инструмент из высокоуглеродистых заэвтектоидных сталей подвергают термической обработке.
Закалка обеспечивает высокую твердость и стойкость в процессе работы. Этим требованиям удовлетворяет структура мартенсита скрытокристаллического или мелкоигольчатого строения с включением карбидов. Строение и состав мартенсита, форма и распределение карбидов, а также твердость определяют износостойкость инструмента. Твердость после закалки HRC 56—64. Наиболее широко при закалке используют нагрев в соляных печах-ваннах и нагрев с помощью т. в. ч.
); масло применяют для охлаждения крупного инструмента из легированной стали. Измерительный инструмент повышенной точности целесообразно после закалки подвергать обработке холодом при температурах минус 70° С (для легированных сталей).
Обработка холодом повышает твердость и стабилизирует размеры тем в большей степени, чем полнее происходит распад остаточного аустенита. Обработку холодом проводят в интервале между закалкой и отпуском (рис. 188). Температура обработки холодом некоторых инструментальных сталей приведена в табл. 29.
Отпуск уменьшает хрупкость, повышает вязкость, уменьшает внутренние напряжения при сохранении высокой твердости измерительного инструмента. Режим отпуска определяется классом точности инструмента, требуемой твердостью и маркой стали. Отпуск рекомендуется проводить в жидких средах (масло, селитра, щелочь) непосредственно после закалки (или обработки холодом) во избежание стабилизации аустенита и образования микротрещин. Отпуск инструмента пониженных классов точности проводят при более высоких температурах (150—180° С в течение 2—3 ч), а высоких классов точности — при 115—130° С с длительной выдержкой
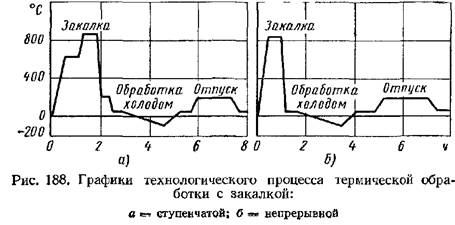
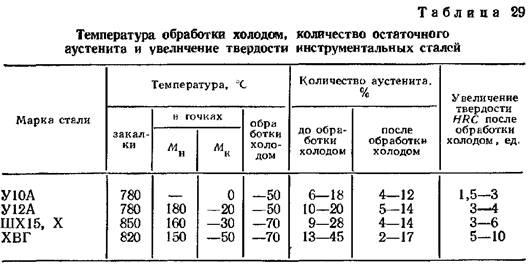
Зависимость твердости и количества остаточного аустенита от температуры отпуска для различных сталей приведена на рис. 189. Для полной стабилизации размеров (без обработки холодом) проводят отпуск при температурах выше 250° С. Инструмент высокой точности после предварительного шлифования подвергают старению.
Искусственное старение закаленного инструмента приводит к изменению тетрагональности мартенсита и стабилизации размеров. Температура старения от 120—130° С до 150—160° С, продолжительность 5—24 ч; режимы старения приведены в табл. 30. Для более полной стабилизации можно проводить обработку холодом повторно после отпуска (рис. 190).
При старении с нагревом в термостате продолжительность выдержки увеличивается для инструмента диаметром меньше 50 мм на 2 ч, для инструмента диаметром больше 50 мм — на 1 ч.
Вспомогательными операциями, применяемыми в процессе термической обработки измерительного инструмента, являются промывка, пассивирование, гидроочистка.
По приведенной схеме проводят термическую обработку измерительных плиток из стали X. В зависимости от длины плиток
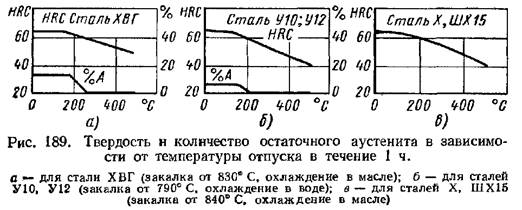

используют различные варианты термической обработки для получения высокой твердости и стабилизации размеров.
Размеры плиток длиной 3—5 мм мало изменяются в процессе старения. Поэтому после обработки на металлорежущих станках и высокого отпуска (650° С) их подвергают закалке без обработки холодом; отпуск проводят при 130—135° С в течение 24 ч.
Плитки длиной 5—100 мм перед закалкой подвергают нормализации. Далее проводят закалку с охлаждением в масле (40— 60° С). Охлаждение в горячих средах (ступенчатая и изотермическая закалка) приводит к увеличению количества остаточного аустенита. После закалки плитки охлаждают до минус 70° С (обработка холодом) и подвергают отпуску при 11О—130° С в течение 24—48 ч (для сохранения высокой твердости). Такой отпуск не изменяет количества остаточного аустенита и может вызвать увеличение длины в процессе эксплуатации. Поэтому плитки длиной более 50 мм после первой обработки холодом отпускают при 120— 125° С (2—3 ч), затем повторно охлаждают до минус 70° С и отпускают при 120—125° С в течение 2—3 ч. Рекомендуется обработку холодом и отпуск повторить 2—3 раза, в некоторых случаях до 6 раз.
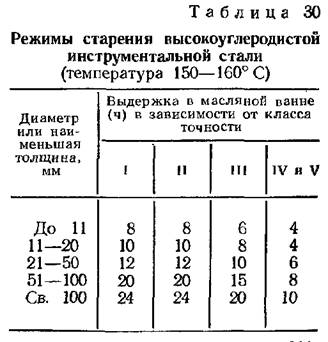
Суммарная продолжительность всех отпусков должна быть равна продолжительности однократного отпуска (24—48 ч). После шлифования для снятия напряжений и повышения качества доводки плитки вторично отпускают (старение) при 120— 135° С в течение 4—10 ч. Твердость плиток после термической обработки HRC 63—65.
Забиваем Сайты В ТОП КУВАЛДОЙ - Уникальные возможности от SeoHammer
Каждая ссылка анализируется по трем пакетам оценки: SEO, Трафик и SMM.
SeoHammer делает продвижение сайта прозрачным и простым занятием.
Ссылки, вечные ссылки, статьи, упоминания, пресс-релизы - используйте по максимуму потенциал SeoHammer для продвижения вашего сайта.
Что умеет делать SeoHammer
— Продвижение в один клик, интеллектуальный подбор запросов, покупка самых лучших ссылок с высокой степенью качества у лучших бирж ссылок.
— Регулярная проверка качества ссылок по более чем 100 показателям и ежедневный пересчет показателей качества проекта.
— Все известные форматы ссылок: арендные ссылки, вечные ссылки, публикации (упоминания, мнения, отзывы, статьи, пресс-релизы).
— SeoHammer покажет, где рост или падение, а также запросы, на которые нужно обратить внимание.
SeoHammer еще предоставляет технологию Буст, она ускоряет продвижение в десятки раз,
а первые результаты появляются уже в течение первых 7 дней.
Зарегистрироваться и Начать продвижение
Размеры плиток длиной более 100 мм в процессе эксплуатации изменяются значительно. Для них рекомендуется следующая обработка: закалка, отпуск при 270—290° С (для полного превращения аустенита) с получением твердости HRC 56—58; далее проводят
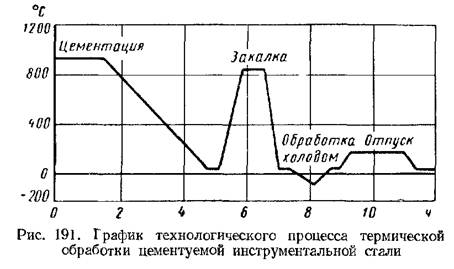
местную закалку торцов с нагревом в соляной ванне (2—2,5 мин) и охлаждением в воде и повторный отпуск при 120— 130° С в течение 24 ч.
Измерительный инструмент (скобы, шаблоны), изготовленный из низкоуглеродистых цементуемых сталей (15, 20, 20Х и др.), подвергают цементации на толщину 0,3—1,5 мм (в зависимости от толщины детали). Отношение толщины нецементованной зоны к толщине цементованного слоя должно быть не менее 2. Цементацию проводят при температуре 900—930° С. После цементации инструмент закаливают от 780—800° С с охлаждением в воде (сталь 20) или в масле (сталь 20Х). Для предотвращения образования трещин и снижения деформации проводят ступенчатую закалку в горячих средах (инструмент из углеродистых сталей сечением до 8 мм, инструмент из легированных сталей сечением до 12—18 мм).
Для улучшения структуры сердцевины рекомендуется двойная обработка: первая закалка (нормализация) от 850—880° С, вторая закалка от 780—800° С.
Для уменьшения количества остаточного аустенита в цементованном слое инструментов повышенной точности рекомендуется проводить обработку холодом при температуре минус 50° С (рис. 191). Отпуск цементованного измерительного инструмента проводят при 150—180° С в течение 1—3 ч; далее (после шлифования) старение при 120—130° С в течение 6—9 ч. Искривление инструментов, возникающее при цементации и последующей термической обработке, устраняют при шлифовании или правкой (рихтовкой).
и отпуску при 160—180° С с выдержкой 1,0—2,0 ч (HRC 50—54). Старение проводят при 120—130° С в течение 7—9 ч. Износившийся инструмент (например, калибры из легированной стали) можно восстановить отпуском при 210—230° С в течение 2—5 ч вследствие распада остаточного аустенита.
Дефекты, возникающие при термической обработке измерительного инструмента: недостаточная твердость (недогрев и низкая скорость охлаждения при закалке, перегрев при отпуске), хрупкость (перегрев при закалке, недогрев при отпуске), мягкие пятна (неравномерный нагрев и охлаждение, загрязнение неметаллическими включениями), разъедание инструмента (недостаточная очистка соляных ванн от продуктов раскисления, охлаждение в загрязненных расплавах селитры, плохая промывка инструмента перед отпуском), образование трещин в результате обезуглероживания, окисления и при шлифовании, искривление (поводка) и др.
Основным условием предупреждения брака при термической обработке измерительного инструмента является соблюдение режимов термической обработки, проверка готовности оборудования и оснастки к выполнению технологии термической обработки, своевременная очистка и раскисление соляных ванн, контроль ванн охлаждения, предварительный контроль отдельных параметров инструмента и т. д.
|