Технология термической обработки металловСтали для измерительного инструмента
Измерительный инструмент служит для проверки размеров изготовляемых деталей. При измерении поверхность инструмента непосредственно соприкасается с поверхностью проверяемой детали и изнашивается. Поэтому поверхность измерительного инструмента должна быть твердой и износостойкой для сохранения размеров и формы в процессе работы. Для измерительного инструмента (особенно высоких классов точности) большое значение имеет сохранение постоянства линейных размеров и формы закаленного инструмента в течение длительного времени. Постепенное изменение размеров и формы закаленного инструмента связано с уменьшением тетрагональности решетки мартенсита, мартенситным превращением остаточного аустенита, уменьшением и перераспределением внутренних напряжений (естественным старением). Хотя это изменение и невелико, однако недопустимо для инструмента высокой точности. Процессы старения протекают медленно; результаты старения становятся заметны через 3—6 месяцев и значительно возрастают через 10—12 месяцев после проведения термической обработки. Поэтому при термической обработке измерительного инструмента большое внимание уделяется стабилизации напряженного состояния, мартенсита и остаточного аустенита, что достигается соответствующим режимом низкотемпературного отпуска (называемого искусственным старением) и обработкой при температурах ниже нуля.
Для получения правильного, точного профиля и размера измерительного инструмента после термической обработки необходимо обеспечить минимальное его коробление при закалке.
Калибры и плитки высоких классов точности изготовляют из сталей X, ХВГ, ШХ15 (рис. 187), калибры простой формы и

пониженных классов точности — из сталей У10А, УПА, У12А, ИХ; лекала сложной формы — из стали X; плоские скобы, угольники и шаблоны — из сталей 15, 20, 15Х, 20Х; плоские линейки, угольники — из сталей 50, 50Х, 55; инструменты, стойкие против коррозии, — из стали 40X13. Химический состав некоторых сталей для измерительного инструмента приведен в табл. 28.
Сталь X легирована только хромом — элементом, увеличивающим закаливаемость и прокаливаемость. Заготовки из стали X прокаливаются в масле в сечении до 20—22 мм (твердость в сердцевине не ниже НЯС 60) теплостойкость 200° С. Сталь X отжигается при 770—790° С с замедленным охлаждением (50° С/ч) до 600—700° С, далее на воздухе (НВ 181—229); закаливается от температуры 830—860° С в масле или горячих средах (160—170° С). Отпуск проводят при температуре 120—200° С и выше. Твердость колеблется в пределах НЯС 58—65.
Сталь ИХ легирована хромом и марганцем для увеличения прокаливаемости. Имеет более высокую твердость после отжига (по сравнению с углеродистыми сталями) и несколько хуже обрабатывается давлением и резанием. Ее применяют для изготовления мелкого инструмента вместо углеродистых сталей. Отжигается с температуры 750—770° С (охлаждение с печью 50° С/ч до 600° С, далее на воздухе) до твердости НВ 179—217; закаливается от 780—810° С в масле или горячих средах (можно охлаждать в воде или водных растворах.) Отпуск проводят при 130— 250° С; твердость НЯС 56—65.
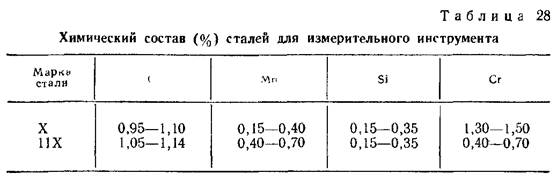
Марку стали для режущего инструмента определяют по искре (от 2 до 100% в зависимости от диаметра штанг) или на стилоскопе (один-два прутка от партии), а твердость — на прессе Бринелля (5% от партии); путем внешнего осмотра выявляют плены, закаты, трещины и другие наружные дефекты.
|