Технология электрической сваркиОсновной металл, свариваемость, напряжения и деформации при сварке
Выбор основного металла
От правильного выбора металла для сварных конструкций в значительной мере зависят их эксплуатационная надежность и экономичность. В настоящее время сварные конструкции в основном изготовляют из углеродистых и низколегированных сталей, а также из алюминиевых и титановых сплавов. Ниже изложены краткие характеристики металлов различных классов и рекомендации по их выбору для изготовления сварных изделий.
Конструкционные стали выплавляют в мартеновских печах или конверторах. В зависимости от степени раскисления они могут быть кипящими, спокойными и полуспокойными.
Значительная часть мягких углеродистых сталей являются кипящими. При их разливке, вследствие быстрого охлаждения, у стенок изложницы образуется наружный слой (корка) почти чистого железа. В процессе охлаждения и дальнейшего затвердевания жидкого металла происходит выделение газов, приводящее к образованию пузырей под затвердевшей наружной коркой. В сердцевине такого слитка скапливаются ликвирующие примеси — фосфор, сера и углерод. После прокатки слитков кипящей стали отчетливо различаются чистая наружная зона и внутренняя ликвационная зона, в которой наблюдаются участки с повышенным содержанием серы и фосфора, так называемые сульфидные строчки.
Спокойные стали затвердевают без кипения, что обусловлено введением в их состав элементов-рас-кислителей.
Важной особенностью спокойной стали является ее однородное строение. Вредные примеси — сера и фосфор распределяются в ней более равномерно, Чем в кипящей стали. Вследствие раскисления и одновременного частичного связывания азота спокойные стали менее чувствительны к хрупкому излому, чем кипящие. Присадкой достаточного количества алюминия, который наряду с кислородом связывает также азот, удается значительно снизить их восприимчивость к старению. Образующиеся при этом мелкодисперсные нитриды приводят одновременно к уменьшению размера зерен и тем самым к уменьшению склонности стали к хладноломкости.
В полуспокойной стали добавлено такое количество раскисли-телей, при котором газов выделяется меньше, чем при затвердевании кипящей стали. Благодаря меньшей степени загрязнения ликвирующими примесями головной части слитка при полуспокойной стали обеспечивается несколько больший выход годного металла, чем при кипящей стали. Слитки полуспокойной стали имеют меньшую химическую неоднородность, чем кипящей.
В связи с этим следует расширять применение полуспокойных сталей. Исследования показали, что полуспокойную низкоуглеродистую сталь СтЗпс (группы Б и В по ГОСТ 380—71) в листовом, фасонном и полосовом прокате толщиной до 10 мм включительно и в сортовом (круг, квадрат, арматура) размером до 16 мм можно применять для сварных конструкций наравне со спокойной сталью без каких-либо ограничений по температурным условиям эксплуатации и виду нагрузок. Прокат больших толщин из полуспокойной стали рекомендуется использовать в сварных конструкциях при любых нагрузках, но с некоторыми ограничениями по температуре эксплуатации. С целью снятия этих ограничений взамен толстого проката из спокойной стали ВСтЗ следует применять сталь ВСтЗГпс (ГОСТ 380—71) с повышенным содержанием марганца (до 1,1%). Это обеспечивает высокие механические свойства и ударную вязкость сварных соединений.
Основное количество стали выплавляют мартеновским способом. В последнее время находят широкое применение конверторные стали. Конверторные процессы выплавки стали имеют несколько разновидностей. Бессемеровскую и томасовскую конверторные стали выплавляют с продувкой воздухом, они характеризуются повышенным содержанием азота (0,01—0,02%). В тома-совской стали также много фосфора (0,05—0,07%). Высокое содержание этих примесей отрицательно сказывается на стойкости металла против перехода в хрупкое состояние и стойкости против старения. Поэтому стали, выплавленные этими способами, не применяют для сварных конструкций. В настоящее время развивается производство сталей в конверторах с основной футеровкой и продувкой кислородом сверху. При этом содержание азота в готовом прокате не превышает 0,008%.
Низкоуглеродистые кислородно-конверторные стали в состоянии поставки практически равноценны выплавленным в мартеновских печах. По динамической (вибрационной и ударной) прочности сварные соединения из такой стали, выполненные под флюсом, 6 углекислом газе и штучными электродами, также не отличаютсй от изготовленных из мартенситной стали. Эти основные положительные показатели служебных свойств конверторных сталей позволяют рекомендовать их применение для сварных конструкций наравне с мартеновскими. В связи с этим в ГОСТ 380—71 способ выплавки сталей (мартеновский или конверторный) не указывается и решается металлургическими заводами в зависимости от производственных возможностей.
Состав и свойства низкоуглеродистых сталей регламентируются ГОСТ 380—71, 1050—60 и 6713—53 и подробно рассмотрены в гл. 9.
Низколегированные стали повышенной прочности поставляются по ГОСТ 5058—65 и 5520—69, а также по различным техническим условиям. Повышение предела прочности и текучести углеродистой стали обеспечивается только увеличением концентрации углерода, что ухудшает свариваемость. Нередко в швах конструкций из стали с повышенным содержанием углерода (свыше 0,3%) возникают кристаллизационные трещины, которые в процессе эксплуатации могут развиваться и быть причиной разрушения.
В связи с этим вместо сталей с повышенным содержанием углерода ВСт4, БСт5, 30, 40 и других целесообразно во многих случаях применять низколегированные стали повышенной прочности с содержанием до 0,18—0,20% С. Требуемые высокие прочностные характеристики таких сталей обеспечиваются за счет их дополнительного легирования другими элементами. Стойкость против хрупкого разрушения сварных конструкций из сталей с повышенным содержанием углерода ниже, чем из низкоуглеродистых и низколегированных. Низколегированные стали целесообразно применять в строительных конструкциях, краностроении, вагоностроении, локомотивостроении, судостроении и т. п.
Забиваем Сайты В ТОП КУВАЛДОЙ - Уникальные возможности от SeoHammer
Каждая ссылка анализируется по трем пакетам оценки: SEO, Трафик и SMM.
SeoHammer делает продвижение сайта прозрачным и простым занятием.
Ссылки, вечные ссылки, статьи, упоминания, пресс-релизы - используйте по максимуму потенциал SeoHammer для продвижения вашего сайта.
Что умеет делать SeoHammer
— Продвижение в один клик, интеллектуальный подбор запросов, покупка самых лучших ссылок с высокой степенью качества у лучших бирж ссылок.
— Регулярная проверка качества ссылок по более чем 100 показателям и ежедневный пересчет показателей качества проекта.
— Все известные форматы ссылок: арендные ссылки, вечные ссылки, публикации (упоминания, мнения, отзывы, статьи, пресс-релизы).
— SeoHammer покажет, где рост или падение, а также запросы, на которые нужно обратить внимание.
SeoHammer еще предоставляет технологию Буст, она ускоряет продвижение в десятки раз,
а первые результаты появляются уже в течение первых 7 дней.
Зарегистрироваться и Начать продвижение
Для ответственных сварных конструкций, эксплуатирующихся в районах, где температура может быть ниже —40° С, следует рекомендовать легкосвариваемые низколегированные стали 09Г2С, 14Г2АФ, 16Г2АФ, 15Г2АФДпс, 18Г2АФпс, 09Г2, 10Г2Б, 16Г2Б, 15ХСНД и 16ГС, а для конструкций, работающих при более высоких температурах,— 10ХСНД, 14Г2, 15ГС, 14ХГС и др. Временное сопротивление этих сталей для толщин до 60 мм составляет 45—55 кгс/мм2, а предел текучести 30—40 кгс/мм2. Напомним, что предел текучести стали ВСтЗ составляет всего 23—24 кгс/мм2. Низколегированные стали должны удовлетворять специальным требованиям по ударной вязкости при нормальной и низких температурах, зависящим от условий эксплуатации.
В последние годы все более широкое применение находят стали с пределом текучести свыше 60 кгс/мм2 и временным сопротивлением до 100 кгс/мм2. Они характеризуются повышенной концентрацией марганца, содержат молибден (до 0,6%) и бор (0,002— 0,006%). Как правило, эти стали имеют бейнитную структуру и поставляются в термообработанном состоянии (закалка и отпуск).
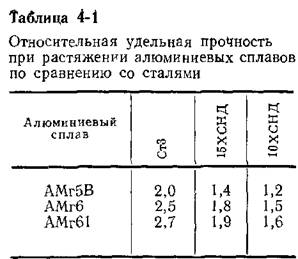
Конструкции из бейнитнЫХ сталей весьма стойки против хрупкого разрушения. В Советском Союзе к этому типу принадлежат стали 14ХМНДФР и 14Х2ГМР. Разработана технология их ручной дуговой, полуавтоматической и автоматической сварки. Эти стали находят применение в экскаваторах, шахтных подъемниках, резервуарах для хранения горючих веществ, напорных гидроприводах и т. п. Алюминиевые сплавы все шире применяют в качестве заменителя стали благодаря следующим преимуществам (табл. 4-1): более высокой удельной прочности (отношение временного сопротивления к объемной массе); высоким механическим свойствам, в частности ударной вязкости при низких и весьма низких температурах; более высокой стойкости против коррозии.
Удельная прочность алюминиевых сплавов значительно выше, чем сталей, и особенно низкоуглеродистой стали СтЗ. Весьма важной особенностью алюминиевых сплавов является их высокая технологичность при обработке прессованием, прокаткой и ковкой. При проектировании имеется возможность выбирать наиболее эффективные и рациональные профили проката (рис. 4-1), обеспечивающие дополнительную экономию металла и снижение трудоемкости. При этом резко сокращаются объем сварочных работ и количество наплавленного металла.

Для ответственных сварных конструкций могут быть рекомендованы алюминиево-магниевые сплавы АМг, АМгЗ, АМг5В, АМгб, АМг61 с пределом прочности соответственно 14, 20, 26, 32 и 34 кгс/мм2. При сварке этих сплавов околошовная зона практически не разупрочняется. Более прочные дюралюминиевые термо-обрабатываемые сплавы для сварных конструкций применять пока нецелесообразно, так как при сварке прочность околошовной зоны снижается. Восстановить полностью прочность путем естественного старения не удается. К недостаткам алюминиевых сплавов можно отнести сравнительно низкий модуль упругости (в 3 раза меньше, чем у стали) и более высокий коэффициент температурного расширения. Этим обусловлены большие деформации при сварке.

На рис. 4-2 приведены кривые значения ударной вязкости, полученные при испытании алюминиевого сплава АМгб, низкоуглеродистой стали ВСтЗкп и низколегированной стали 15ГФ. Характерно, что с понижением температуры ударная вязкость алюминия почти не снижается.
Исследования статической прочности различных типов сварных соединений из алюминиевого сплава АМгб показали, что несмотря на значительную концентрацию напряжений, вызываемую накладками, статическая прочность сварных соединений с понижением температуры до —60° С не отличается от прочности при нормальной температуре. Приближения предела текучести к пределу прочности с понижением температуры практически не наблюдается, что свидетельствует о малой склонности сплава к переходу в хрупкое состояние. Испытания сварных соединений на ударную прочность при различных температурах также подтвердили преимущества алюминиевого сплава перед низкоуглеродистой и низколегированными сталями.
При усталостных испытаниях сварных соединений установлена повышенная чувствительность алюминиевых сплавов к концентрации напряжений. Однако при обеспечении плавного перехода от шва к основному металлу прочность сварных соединений при переменных нагрузках практически такая же, как и самого сплава.
Из изложенного видны значительные преимущества алюми-ниево-магниевых сплавов перед низкоуглеродистой сталью и сталями повышенной прочности. Меньший эффект получается при применении алюминиевых сплавов в конструкциях вместо сталей высокой прочности с пределом текучести 50—60 кгс/мм2 и более. Однако эти стали пока еще очень мало используются. Таким образом, имеются все основания широко применять алюминиевые сплавы для сварных конструкций, в частности, эксплуатирующихся в северных районах, где температура может быть ниже —50° С.
Титан и его сплавы среди новых конструкционных материалов занимают значительное место. Титан и его сплавы обладают сравнительно малой плотностью и поэтому могут быть отнесены к числу легких металлов.
Чистый титан не находит широкого применения, так как обладает небольшой прочностью — около 25 кгс/мм2. В отличие от чистого технический титан содержит ряд примесей, из которых важнейшими являются азот, кислород, водород, а также углерод. Эти примеси повышают прочность, однако несколько снижают пластичность металла. Такой титан с временным сопротивлением 40—55 кгс/мм2 и относительным удлинением 20—30% находит применение в качестве конструкционного материала. При повышенных температурах прочность технического титана падает, однако даже при температуре 500° С все еще достигает 30 кгс/мм2.
Холодная обработка оказывает большое влияние на механические свойства титана: она снижает пластичность и повышает прочность и твердость металла. Так, 10%-ное обжатие приводит к повышению временного сопротивления на 20—25% и снижению относительного удлинения при разрыве на 25—30%.
Титан и его сплавы обладают замечательными свойствами. Они сочетают большую прочность при нормальной и высоких температурах с весьма большой коррозионной стойкостью. Благодаря этому они являются ценнейшим конструкционным материалом в авиационной промышленности, судостроении, химическом машиностроении и других отраслях промышленности.
Сервис онлайн-записи на собственном Telegram-боте
Попробуйте сервис онлайн-записи VisitTime на основе вашего собственного Telegram-бота:
— Разгрузит мастера, специалиста или компанию;
— Позволит гибко управлять расписанием и загрузкой;
— Разошлет оповещения о новых услугах или акциях;
— Позволит принять оплату на карту/кошелек/счет;
— Позволит записываться на групповые и персональные посещения;
— Поможет получить от клиента отзывы о визите к вам;
— Включает в себя сервис чаевых.
Для новых пользователей первый месяц бесплатно.
Зарегистрироваться в сервисе
Титан, так же как и алюминий, весьма чувствителен к концентрации напряжений. Поэтому при работе сварной конструкции в условиях переменных нагрузок следует обеспечивать плавный переход от шва к основному металлу. Это достигается путем механической обработки либо оплавления кромок аргоно-дуговой горелкой.
|