Технология электрической сваркиСварка алюминиевых сплавов
Присутствие поверхностных тугоплавких окисных пленок затрудняет получение хорошего сварного соединения на сплавах алюминия. Хорошие результаты дает применение для сварки алюминия и его сплавов импульсно-модулированного по амплитуде пучка электронов. В процессе импульсной сварки теплота выделяется во внутренних слоях металла под поверхностным слоем окислов, вследствие чего внутренние слои металла быстро расплавляются и частично испаряются. Этот процесс действует подобно взрыву — окисные пленки металла не препятствуют сплавлению кромок.
Из всех источников сварочного нагрева плавлением только электронный луч позволяет получать соединения термически упрочняемых и нагартованных сплавов систем Al—Mg, A1—Zn— Mg—Си, Al—Си—Мп без существенного разупрочнения околошовной зоны. Коэффициент прочности сварных соединений на сплаве АМгб 0,95—1,00; на сплавах АЦМ, Д20 и В95 0,75—0,85, что на 15—-25% выше соответствующих значений для дуговых способов сварки.
При подборе режимов сварки необходимо учитывать, что при наличии легирующих элементов с высокой упругостью паров (цинка, магния) наблюдается резкое повышение глубины проплавления по сравнению со швами на сплавах алюминия с медью и марганцем.
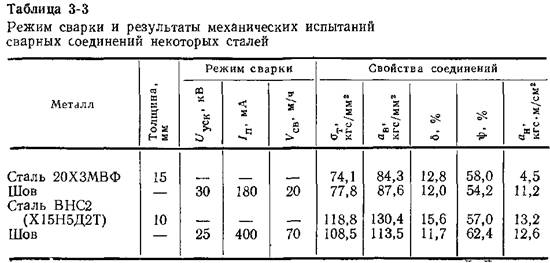

Для уменьшения пористости швов свариваемые кромки необходимо подвергать химическому полированию или химическому травлению с последующим шабрением. Химически полированные поверхности менее склонны к дальнейшему окислению и гидратации, что позволяет выдерживать их более длительное время от момента обработки до сварки. Присадочную проволоку также следует подвергать химическому полированию.
Сварку алюминиевых сплавов необходимо выполнять на высокой скорости (60—-90 м/ч), что повышает плотность соединения и снижает потери легколетучих легирующих элементов (табл. 3-4).
Основные типы сварных соединений и техника их выполнения. Для электроннолучевой сварки характерны как обычные типы соединений, так и принципиально новые. Общее требование ко всем типам соединений — точная сборка деталей перед сваркой. Обычно отклонение оси пучка электронов от сварного стыка в процессе сварки не должно превышать 0,2—0,3 мм. При толщине свариваемых пластин до 5 мм допустимая величина зазора, как правило, не превышает 0,05—0,07 мм. При увеличении толщины пластин до 20 мм допустимая величина зазора возрастает до 0,1 мм, но не более.
При увеличении зазоров свыше указанных пределов получить удовлетворительное формирование стыковых швов без подрезов практически невозможно. Наиболее эффективным способом устранения подрезов является подача присадочной проволоки или же сварка по технологическим буртикам, оставляемым при механической обработке стыков. Сварка с присадочной проволокой позволяет увеличить допустимый зазор в стыке до 0,5 мм, кроме того, становится возможным металлургическое вмешательство с целью предупреждения возникновения трещин. При сварке без зазоров доля проволоки в металле шва при толщине основного металла до 20 мм составляет около 25%. Изменяя величину зазора в стыке и скорость подачи проволоки, можно довести долю присадочного металла до 50%.
Электроннолучевую сварку с отбортовкой кромок на телах вращения применяют преимущественно в радиоэлектронике и приборостроении. В торцовых и стыковых соединениях с отбортовкой кромок допустимы зазоры до 0,5—0,7 мм и превышение кромок до 1—2 мм. Однако в этом случае для обеспечения удовлетворительного формирования шва диаметр пятна на изделии должен несколько превышать величину зазора.
Сварку металлов, значительно отличающихся по толщине (например, приварка мембраны к корпусу и т. п.), выполняют с предварительной разделкой кромок металла большей толщины для выравнивания теплового поля в соединяемых деталях и достижения симметричного проплавления.
Импульсную электроннолучевую сварку благодаря малому тепловложению применяют при наличии в непосредственной близости от места сварки спаев металла со стеклом или керамикой. Она способствует получению определенной ориентации кристаллитов металлов сварного шва, обеспечивающей вакуумную плотность сварных соединений в течение длительного времени эксплуатации. При тех же погонной энергии и скорости сварки проплав-ление в импульсном режиме глубже, чем в непрерывном, особенно для тонколистовых материалов.
Сварка в узких разделках и труднодоступных местах (рис. 3-12, а) является одним из преимуществ электроннолучевой сварки перед известными способами сварки плавлением и возможна благодаря малым размерам пучка в сечении, его

длиннофокусности и автономности по отношению к свариваемому материалу. Однопроходную сварку расположенных на различной высоте стыков проникающим пучком (рис. 3-12, б) выполняют в редких случаях, так как она не обеспечивает достаточно стабильного формирования швов. В некоторых конструкциях теплообменников (рис. 3-12, в) сварку выполняют внедренным пучком через ребро жесткости. Для исключения концентраторов напряжения в корне проплавления, предотвращения дефектов в нем, а также для выхода парогазовой фазы при вварке заглушек необходимо подготовлять соединения в соответствии с рис. 3-12, г.
|