Ультра звуковая сварка пластмасс и металловОсновные узлы оборудования для узс пластмасс и металлов
ВОЛНОВОДЫ
Технологическое оборудование для ультразвуковой сварки независимо от физико-механических свойств свариваемых материалов, которые являются непосредственными объектами интенсивного воздействия ультразвуковых колебаний, имеет одну структуру и состоит из следующих узлов: источника питания, аппаратуры управления сварочным циклом, механической колебательной системы и привода давления.
Важнейшим узлом, составляющим основу и специфику оборудования и технологии ультразвуковой сварки металлов и пластмасс, является механическая колебательная система. Эта система служит для преобразования электрической энергии в механическую, передачи этой энергии в зону сварки, согласования сопротивления нагрузки с внутренним сопротивлением системы и геометрических размеров зоны ввода энергии с размерами излучателя, концентрирования энергии и получения необходимой величины колебательной скорости излучателя. Система должна работать с максимальным КПД на резонанасной частоте назависимо от изменения сопротивления нагрузки.
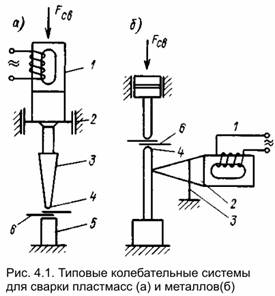
Типовая колебательная система (рис. 4.1) состоит из электромеханического преобразователя 1, волноводного звена 3 (трансформатора) — концентратора колебатель ной скорости, акустической развязки системы от корпуса машин 2, излучателя ультразвука — сварочного наконечника 4 и опоры 5, на которой расположены свариваемые детали 6.
Широко известны колебательные системы с использованием резонирующих стержней, работающих в режиме изгибных колебаний.
Электромеханические преобразователи 1 изготовляются из магнито - или электрострикционных материалов (никеля, пермендюра , титаната бария и др.). Под воздействием переменного электромагнитного поля в преобразователе возникают механические напряжения, которые вызывают упругие деформации материала. Таким образом, преобразователь является источником механических колебаний.
Волноводное звено 2 служит для передачи энергии сварочному наконечнику. Это звено должно обеспечивать необходимое увеличение амплитуды колебаний сварочного наконечника по сравнению с амплитудой исходных волн преобразователя, трансформировать сопротивление нагрузки и концентрировать энергию.
Сварочный наконечник 4 является элементом, посредством которого осуществляется отбор мощности, поглощаемой в зоне сварки. По существу, это звено, определяющее площадь и объем непосредственного источника ультразвук. Так как в процессе сварки наконечник внедряется в свариваемую деталь, то он является также и согласующим волноводным звеном между нагрузкой и колебательной системой.
В общем случае рассматриваемая система является системой с распределенными параметрами и, как следствие этого, она имеет бесконечное число степеней свободы и собственных частот. Система составлена из резонансных кратных полуволн звеньев.
в системе больше


Колебательную систему характеризуют следующие основные параметры:


— частота колебаний системы;
;


.
Расчет волноводов продольных волн. Волноводы продольных волн служат для передачи энергии от преобразователя как первичного излучателя ультразвука непосредственно в зону сварки или к резонирующим элементам в виде стержней или дисков, работающих в режиме изгибных колебаний. Из ряда параметров, характеризующих его свойства, важнейшими в конечном счете являются колебательная скорость, напряжение, мощность, которые сварочный наконечник способен передать в зону сварки. Методика их расчета обусловлена энергетикой процесса и особенностями технологии сварки. В зависимости от теплофизических, механических и акустических свойств и состояния поверхности свариваемых материалов производится расчет энергии, необходимой для образования сварного соединения, мощности колебательной системы и, как следствие этого, амплитуды колебаний сварочного наконечника.
По упрощенной методике расчета, когда задано ориентировочное значение амплитуды колебательной скорости сварочного наконечника, все сводится к определению резонансной длины волновода, входной и выходной площади, формы и места его крепления. Формулы для расчета волноводов получены из решения дифференциального уравнения (2.1). Уравнение описывает процесс при условии, что колебания носят гармонический характер, волна плоская и распространяется вдоль оси волновода без потерь.
Практическое применение нашли конический, ступенчатый и экспоненциальный волноводы (концентраторы), возможно также использование параболического, гиперболического, катеноидального
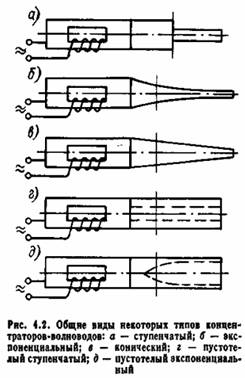
и т. п. Общие виды некоторых типов волноводов приведены на рис. 4.2.
Опуская преобразования, получаем следующие основные формулы для расчета волноводов: для ступенчатого длина резонансная

где / — резонансная частота волновода, которая обычно задается;
положение узловой плоскости — места крепления волновода

Коэффициент усиления амплитуды смещения

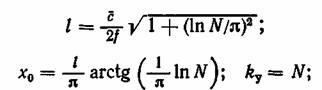
изменение формы
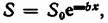
— исходная и текущая площади поперечного сечения
волновода соответственно; х — текущая координата;

для конического волновода
где kl — корни уравнения,
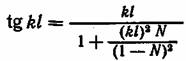
— волновое число;
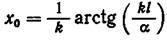
— коэффициент наклона образующей конического волновода к его продольной оси;
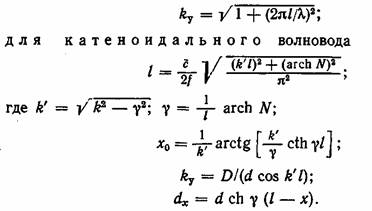
В работах [6, 10 и др.]. можно найти уравнения для расчета и других типов волноводов, однако теоретический анализ эффективности передачи энергии в зону сварки и практика использования сварочных машин показывают, что можно построить достаточно работоспособные системы с использованием указанных типов или их сочетаний.
при заданном сопротивлении нагрузки. Зависимости имеют экстремальный характер со сдвигом максимумов коэффициента усиления в область инерционных сопротивлений нагрузки. Сопротивление нагрузки в значительной степени влияет на коэффициент усиления волновода.
Забиваем Сайты В ТОП КУВАЛДОЙ - Уникальные возможности от SeoHammer
Каждая ссылка анализируется по трем пакетам оценки: SEO, Трафик и SMM.
SeoHammer делает продвижение сайта прозрачным и простым занятием.
Ссылки, вечные ссылки, статьи, упоминания, пресс-релизы - используйте по максимуму потенциал SeoHammer для продвижения вашего сайта.
Что умеет делать SeoHammer
— Продвижение в один клик, интеллектуальный подбор запросов, покупка самых лучших ссылок с высокой степенью качества у лучших бирж ссылок.
— Регулярная проверка качества ссылок по более чем 100 показателям и ежедневный пересчет показателей качества проекта.
— Все известные форматы ссылок: арендные ссылки, вечные ссылки, публикации (упоминания, мнения, отзывы, статьи, пресс-релизы).
— SeoHammer покажет, где рост или падение, а также запросы, на которые нужно обратить внимание.
SeoHammer еще предоставляет технологию Буст, она ускоряет продвижение в десятки раз,
а первые результаты появляются уже в течение первых 7 дней.
Зарегистрироваться и Начать продвижение
Для УЗС металлов целесообразно производить преобразование продольных волн в изгибные и использовать при этом так называемую продольно-поперечную систему волноводов. Основные колебания сварочного наконечника относительно плоскости свариваемых материалов происходят тангенциально. Эти волноводные звенья позволяют существенно увеличить технологические возможности машины: стабильность ее работы и диапазон форм свариваемых деталей.
Для расчета собственной частоты однородного стержня используется уравнение собственных колебаний стержня (2.6), уравнения для расчета собственных частот стержня при различных граничных условиях (2.10)—(2.13).
Для шовной УЗС целесообразно использование колебательных систем, в которых волноводом, передающим энергию ультразвука сварочному ролику может быть концентратор любой из рассмотренных форм. Известно использование составных волноводов в сочетаниях, например, ступенчатого с коническим, экспоненциальным и т. п. Исходное уравнение колебаний сварочного ролика постоянной толщины можно взять в виде:
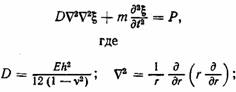
| — смещение ролика; т — масса ролика, отнесенная к единице площади ролика; Р — возбуждающая сила, отнесенная к единице площади; Е — модуль Юнга; к — толщина ролика; V — коэффифициент Пуассона.
Исследовательские работы по созданию оборудования для шовной УЗС металлов показали эффективность акустических систем со сварочными роликами [13 и др.].
Волноводы при передаче энергии ультразвука находятся в весьма сложном, термомеханическом состоянии. Оно заключается в знакопеременном характере нагружения, значительных механических переменных нагрузках, высоких температурах, особенно на поверхности сварного наконечника. Кроме того, материалы волноводов должны обладать минимальными коэффициентами потерь, минимумом изменения своих линейных размеров при температурах до 400—600 °С; должны хорошо обрабатываться и быть сравнительно недорогими.
Таким образом, рекомендации по выбору материалов и методов соединений волноводов сводятся к следующему.
Материал волновода и всех волноводных звеньев должен обладать достаточно высокой усталостной прочностью, малыми потерями, хорошо паяться твердыми припоями, а при необходимости и свариваться. Формой волновода определяется распределение амплитуд колебательного напряжения и смещения по его длине. Для колебательных систем с такими выходными параметрами выбор материала волновода является актуальной и довольно сложной задачей. Физико-механические свойства для некоторых материалов приведены в табл. 4.1.
Минимальными потерями обладают титановые сплавы. Они обеспечивают наиболее высокую амплитуду колебаний инструмента. Экспериментально показано, что амплитуда на торце волноводов из титанового сплава, например ВТ5, в 2 раза больше амплитуды волноводов из стали 45. К положительным качествам волноводов из титана можно отнести также их сравнительно высокую усталостную прочность. Таким образом, при сравнении
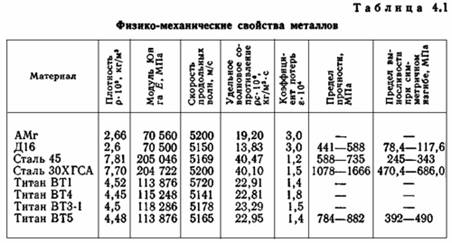
сталей и титановых сплавов для изготовления волноводов преимущество титановых сплавов очевидно. Но соединения титана непосредственно с никелем и другими магнитострикционными материалами крайне затруднено. Используются они, как правило, в качестве вторых ступеней.
Коэффициент потерь алюминиевых сплавов имеет ту же величину, что и для сталей, но его прочностные показатели уступают всем вышеперечисленным материалам. Для изготовления волноводов при ультразвуковой сварке пластмасс наиболее пригодными оказались алюминиевые сплавы (Д16, АМг , АМц ). Они успешно конкурируют с титановыми сплавами. Эта особенность волноводов из алюминиевых сплавов объясняется более рациональным сопряжением их волновых сопротивлений и свариваемого материала.
Как показал опыт эксплуатации оборудования для УЗС в промышленности, волноводные звенья можно делать и из углеродистых сталей 40, 45. Эти стали недефицитны, обладают достаточной усталостной прочностью и хорошо паяются твердыми припоями.
Эффективность работы механической колебательной системы в значительной мере зависит от качества соединения преобразователя с волноводом (концентратором). В колебательных системах/ используемых в машинах для ультразвуковой сварки, получил распространение единственный метод соединений — пайка. Другие способы (склеивание и сварка) практического распространения не получили (за исключением колебательных систем для микросварки). Не исключена целесообразность использования акустически прозрачного клея.
Качество пайки является фактором, определяющим возможность переноса энергии механических колебаний от преобразователя в зону сварки. Наиболее рационально применение твердых припоев марок ПСр40, ПСр45. При изготовлении колебательных систем малой мощности допустимо использование мягких припоев, например ПОС40, ПОС60.
Как известно, при изготовлении преобразователей из ферритов и керамики для их соединения с элементами волноводных звеньев используется клей; керамика может стягиваться посредством накладок и стяжных болтов.
При изготовлении колебательных систем со сменными волно-водными звеньями, с резонирующими стержнями, работающими в режиме изгибных колебаний, возникает необходимость сопряжения этих звеньев. Это возможно (при малых мощностях) посредством применения мелких и качественных резьб . При изготовлении акустических узлов преобразователи должны быть присоединены к волноводам. Это соединение должно прежде всего обеспечивать надежный акустический контакт.
Так как волновод и преобразователь являются резонансными звеньями, то механическое сопротивление в плоскости их соединения мало и определяется только эквивалентным сопротивлением потерь в концентраторе, поэтому механические усилия, которые могли бы вызвать разрушение, сравнительно невелики. (Правда, они растут с возрастанием энергии, переносимой в зону сварки, с уходом от резонансной частоты и т. п.). Наиболее рациональным способом соединения этих звеньев явяется пайка серебряными припоями. При этом сопрягаемые поверхности шлифуются, обезжириваются, при пайке оловом предварительно облужи-ваются . Преобразователи из пермендюра со сталью лучше паять припоями ПСр45 в печи, с флюсом № 302. При этом тонкая пластинка припоя толщиной 0,1—0,2 мм вырезается в размер площади преобразователя, посыпается слоем флюса и собирается в кондукторе с концентратором.
Сервис онлайн-записи на собственном Telegram-боте
Попробуйте сервис онлайн-записи VisitTime на основе вашего собственного Telegram-бота:
— Разгрузит мастера, специалиста или компанию;
— Позволит гибко управлять расписанием и загрузкой;
— Разошлет оповещения о новых услугах или акциях;
— Позволит принять оплату на карту/кошелек/счет;
— Позволит записываться на групповые и персональные посещения;
— Поможет получить от клиента отзывы о визите к вам;
— Включает в себя сервис чаевых.
Для новых пользователей первый месяц бесплатно.
Зарегистрироваться в сервисе
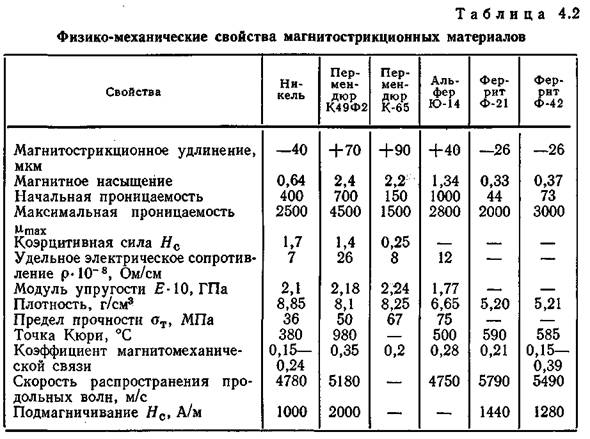
применение находят никель, пермендюр , ферриты. Никель обладает сравнительно небольшой, недостаточно интенсивной магнито-стрикцией , хорошими антикоррозионными свойствами, пластичностью и прочностью. Очень важно, что никель хорошо паяется оловом и серебром со сталями.
Наиболее рациональным материалом для изготовления преобразователя является пермендюр (К49Ф2). Он отличается сильно выраженным магнитострикционным эффектом, т. е. позволяет получать весьма значительные мощности при относительно небольших размерах вибратора. Однако по сравнению, например, с никелем он обладает недостаточной механической прочностью и антикоррозионной стойкостью. При использовании железоалю-миниевых сплавов, несмотря на неплохие характеристики, соединение их со сталями вызывает серьезные затруднения.
определяет положение рабочей точки на кривой магнитострикции и, как следствие этого, значение коэффициента магнитострикции (рис. 4.4, точка /С).
выбирают исходя из статической характеристики кривой магнитострикции. Рабочий участок на этой кривой целесообразно выбирать с максимальной крутизной, наибольшим перепадом максимального и минимального значений магнитострикции.
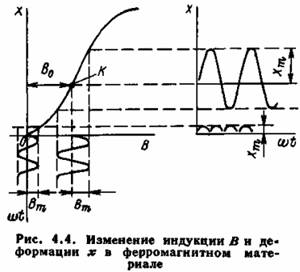
,
— напряженность
При этом окончательное число ампер-витков определяется экспериментально.
активные потери крайне малы. Опуская элементы преобразования, получаем

Уравнение позволяет определить резонансную частоту преобразователя при заданных его размерах а, Ь, с, & и др.
Аналогичные результаты можно получить, используя уравнение
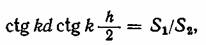
— площадь поперечного сечения стержня.
Длина стержня без накладок может быть предварительно определена так:
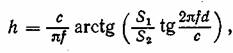
где / — заданная частота колебаний преобразователя.
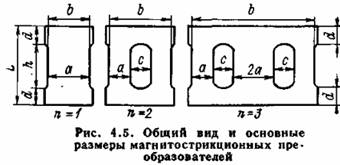
Для определения резонансной частоты трех-стержневого преобразователя (рис. 4.5) можно воепользоваться весьма простой формулой, которая дает вполне удовлетворительные результаты,
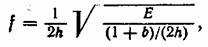
где Ь — толщина пакета; h — полная высота пакета с накладками; толщина боковых стержней равна b /8, а толщина центрального стержня b /4.
Для оценки энергетических показателей преобразователя можно использовать экспериментально-расчетные величины и, в частности, скорость, волновое сопротивление, относительное удлинение и добротность.
Уравнение, по которому рекомендовано определять удельную механическую мощность одностержневого преобразователя, имеет вид

амплитуда относительного удлинения.
Добротность Q может быть определена экспериментально из резонансной кривой, получаемой при возбуждении продольных колебаний преобразователя,


Принимая, что
(Но так
то использование предложенного уравнения всегда
дает завышенное значение.)
Как правило, конструкция МСП доводится экспериментально. В МСП основными видами потерь являются потери на гистерезис и вихревые токи. Потери от вихревых токов растут пропорционально квадрату частоты, а от гистерезиса — пропорционально частоте. Потери на гистерезис можно уменьшить только соответствующим выбором материала. Потери на вихревые токи можно уменьшить повышением электрического сопротивления материала преобразователя, изготовлением его из возможно более тонких пластин (целесообразно использовать пластины не толще 0,2 мм).
Электрический расчет преобразователя производится после того, как определены его резонансная частота, размеры, приближенное значение механической мощности и, принимая табличное значение его КПД, электрическая мощность.


— средняя длина пути магнитного потока в отдельной магнитной цепи.
Число витков на каждом стержне равно

где / — переменная составляющая тока, которая задается.
= 0,5, определяем приближенное значение его электрической мощности
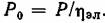
Тогда полное активное сопротивление, эквивалентное всем потерям в преобразователе, равно
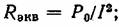
в обмотке


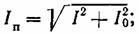
магнитное сопротивление отдельной магнитной цепи

— эффективное значение магнитной проницаемости магнитопровода ; S — площадь поперечного сечения магнитопро-вода среднего стержня (в случае трехстержневого МСП).
Индуктивность преобразователя при последовательной намотке на стержни


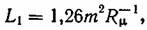
— индуктивность одной обмотки на крайнем стержне.
Номинальное напряжение на преобразователе U выбирается исходя из его электрической мощности и требований ГОСТ 9865—76 и 13952—83.
получаем

необходимо возвратиться к исходным значениям ампер-витков и переменной составляющей тока. Реальность выбора переменной составляющей проверяется условием


Если это условие не соблюдается, необходимо увеличить Р или уменьшить /.
При выборе сечения провода обмоток исходят из мощности потерь и условий охлаждения. Для охлаждения преобразователей из никеля и пермендюра , используемых в сварочных машинах, используется, как правило, проточная вода технического назначения.
При условии, что определено сечение провода, его марка (обычно используется БПВЛ), т. е. его полный диаметр, и известно число витков на стержне, рассчитывается заполнение окна преобразователя. Если оказывается, что окно по своим размерам недостаточно для размещения обмоток, необходимо снова произвести перерасчет ампер-витков, т. е. принять большее значение тока, уменьшить число витков, а может быть, учитывая интенсивное охлаждение обмоток, взять меньшее сечение провода. При слишком большом окне становится очевидной нерациональность размеров преобразователя (лучше увеличить сечение стержней), т. е. необходимо пересчитать геометрические размеры преобразователя, его резонансную частоту и элементы электрической цепи.
Практически для изготовления преобразователя используется, например, листовой никель или пермендюр толщиной 0,05— 0,15 мм, которые штампуются в размер, подвергаются термообработке и собираются в пакеты по специальной технологии.
В качестве магнитострикционных материалов можно использовать специально разработанную керамику, обладающую сильно выраженными магнитострикционными свойствами, — ферриты. По своим механическим свойствам и технологии изготовления они близки к пьезокерамике , но не требуют дефицитных исходных материалов. Основным преимуществом ферритов по сравнению с магнитострикционными металлами является отсутствие потерь на токи Фуко. Электрическое сопротивление ферритов в 108— 1011 раз больше, чем в металлах. Ферриты обладают высоким электроакустическим КПД — до 87 %, который сохраняется в широком диапазоне частот. Они не требуют высокого напряжения, не чувствительны к воздействию внешней среды, могут работать даже в агрессивных средах. Технология их изготовления позволяет получать необходимые формы преобразователей. Однако ферриты имеют и существенные недостатки. Амплитуда колебаний .и интенсивность излучения у преобразователей, изготовленных из ферритов, ограничиваются нелинейными свойствами и низкой механической прочностью ферритов. Экспериментальные работы показали, что предельная интенсивность феррйтовых преобразователей составляет 5—3,5 Вт/см2.
Вместе с тем применение преобразователей из ферритов, особенно в маломощных установках (5—50 Вт), для сварки микротолщин металлов и полимеров при условии серийного выпуска преобразователей возможно.
Для расчета преобразователей из ферритов используются величины, характеризующие свойства магнитострикционных материалов (см. табл. 4.2). Для оценки КПД излучателя надо знать величину электромеханической связи и потери в материале. Электроакустический КПД ферритов достигает 74 %. Амплитуда колебаний и интенсивность излучения феррйтовых преобразователей ограничиваются их нелинейными свойствами и механической прочностью.
Экспериментальные исследования показывают, что промышленное использование керамики возможно только при интенсив-ностях 2,5—3 Вт/см2 и амплитуде колебаний до 3 мкм. В маломощных установках для УЗС, например до 50 Вт, использование магнитострикционных преобразователей из ферритов вполне оправдано.
Преобразование электрических колебаний в механические связано также с использованием пьезоэлектрического эффекта. Установлено, что при растяжении и сжатии некоторых кристаллов (кварца, титаната бария, цирконата свинца и других материалов) на их поверхностях возникают электрические заряды. Внесение пьезоэлектрического кристалла в электрическое поле, силовые линии которого совпадают с направлением его пьезоэлектрической оси, вызывает растяжение или сжатие кристалла (обратный пьезоэффект ). Условие резонанса пьезоэлектрического преобразователя определяется уравнением
где с — скорость звука в материале преобразователя.
Практически чаще используются преобразователи, состоящие из пластин пьезоэлемента , пьезоэлемента и металла, многослойных пластин (рис. 4.6). В многослойном преобразователе размеры отдельных элементов с накладками одинаковой толщины связаны с частотой собственных колебаний соотношением

— плотность соответственно керамики и накладок;
— площадь пластин керамики и накладок.

В более сложном варианте многослойного преобразователя с частотопонижающими накладками, толщины которых неодинаковы, его размеры связаны, как следует из работы, уравнением

— волновые сопротивления пьезокерамики , излучающей и отражающей накладок.
Выражение для определения излучаемой удельной механической мощности ультразвуковых колебаний четверть- и полуволнового преобразователя в режиме одностороннего излучения имеет вид
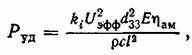
рс — волновое сопротивление среды.
Для многослойного преобразователя

— напряженность электрического поля.
Для изготовления преобразователей применительно к механическим колебательным системам для УЗС используются в настоящее время ЦТС. Пьезокерамика обладает высоким пьезомодулем (табл. 4.3), значительной диэлектрической проницаемостью, сравнительно большой механической прочностью, невысоким входным электрическим сопротивлением и относительно небольшой стоимостью.
Уход собственной частоты пьезоэлемента в диапазоне от О до 50 °С примерно в 10—15 раз меньше, чем у титаната бария и т. д. Титанат бария имеет существенные недостатки: малую теплопроводность, низкое значение точки Кюри (120 °С, потеря пьезо-эффекта ), значительные диэлектрические потери, зависимость физических свойств керамики от температуры. Это вызывает большое изменение собственной частоты преобразователя.
Исходной величиной для расчета пьезоэлектрического преобразователя является мощность, которую необходимо ввести в зону сварки. Зная основные свойства (табл. 4.2) и удельную мощность излучения пьезоматериала , находим суммарную площадь излучения 5. Эффективное напряжение возбуждения для полуволнового преобразователя

Амплитуда колебаний пьезоэлемента находится в зависимости от пьезомодуля и приложенного напряжения:

сопротивление потерь в пьезокерамике

сопротивление излучения

равно

емкостное сопротивление

где с — емкость преобразователя.
Полное сопротивление преобразователя
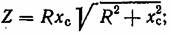
эффективное значение силы тока


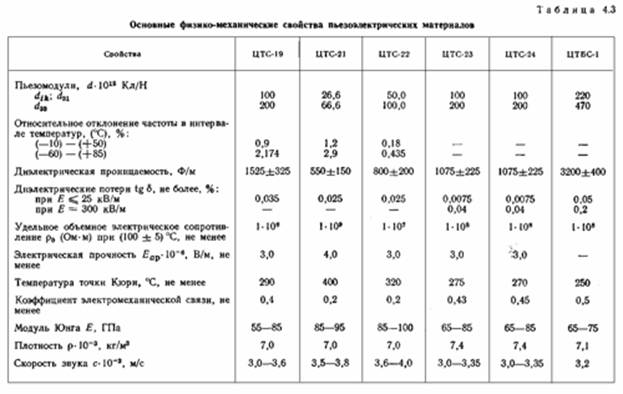
Эффективное значение переменного напряжения на резонансной частоте

а — коэффициент, равный примерно уд-
— коэффициент преобразования.
Механическое сопротивление преобразователя на резонансной частоте

Полное активное сопротивление преобразователя, приведенное к параллельной схеме,

— сопротивление электрических потерь.
—частота колебаний при резонансе).
|