Ультра звуковая сварка пластмасс и металловМетоды и аппаратура для измерения параметров электромеханических систем
При анализе работы системы генератор — механическая система возникает необходимость измерения силы тока, напряжения, соответствующих фазовых соотношений, мощности, частоты колебаний электрического тока, питающего преобразователь, а также амплитуды, частоты смещения сварочного наконечника и энергии, поглощаемой в зоне сварки.
Для измерения параметров генераторов, амплитудно-фазовых и частотных характеристик, круговых диаграмм, колебательных величин акустических систем в современных лабораториях используются измерительные комплексы, которые содержат блоки автоматической обработки некоторых данных. Расчеты производятся, как правило, с использованием вычислительной техники. Графическая обработка полученных данных производится графопостроителями.
В лабораторно-заводской практике, когда нет соответствующих отечественных и импортных средств измерения, напряжение на выходе генератора определяется посредством широко распространенных электростатических и электронных вольтметров и осциллографов обычными приемами. Перечень приборов для измерения различных электрических и механических величин дан в табл. 4.5.
Для измерения силы тока высокой частоты используются амперметры с термопреобразователями , например, типов Т-14 и Т-18. Для измерения электрической мощности в ряде лабораторий разработаны схемы ваттметров, работа которых основана на использовании нелинейных характеристик некоторых преобразователей. В качестве преобразователей используются диоды, вакуумные термопреобразователи и т. п. Такие преобразователи использованы в ваттметрах типов ЭВ-1, ВУЧ-2, Т-141 и др. (Ваттметр типа Т-141 имеет значительную инерционность и не позволяет выявить потребление энергии преобразователем в процессе сварки.) Схема измерения мощности типовым ваттметром показана на рис. 4.27.
При синусоидальной форме напряжения и тока на преобразователе и незначительной мощности колебательной системы (до 50—100 Вт) допускается измерение потребляемой мощности методом трех вольтметров. Активное сопротивление /?, включенное последовательно с нагрузкой, должно быть того же порядка, что и величина модуля полного сопротивления преобразователя. Мощность вычисляется по формуле

— напряжения на выходе генератора, на сопротивлении
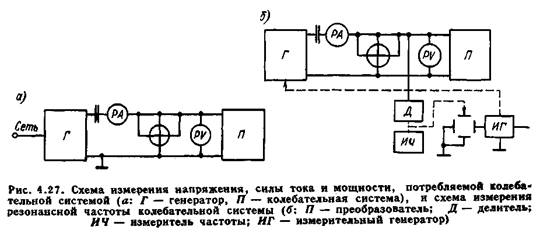
R и преобразователе. Мощность, потребляемая преобразователем, приближенно может быть определена посредством калориметрирования
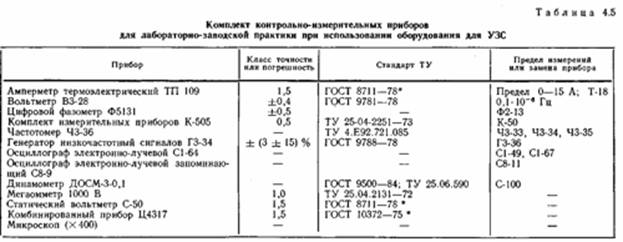
Преобразователь при этом погружают в ограниченный объем воды и измеряют изменение температуры за время его работы. Тогда

— масса воды и материала сосуда.
Известны методы ка-лориметрирования , основанные на сравнении выделяющейся теплоты, создаваемой преобразователем и эквивалентным нагревательным элементом.
Резонансная частота преобразователя определяется по максимальной потребляемой мощности при работе под нагрузкой и неизменном значении выходного напряжения генератора. Частота может быть определена цифровыми частотомерами типов 43-35, 43-28, 43-4. Применение цифровых частотомеров рационально. Они существенно упрощают процесс определения частоты и обмера резонансных кривых колебательной системы, поскольку дают непосредственное и точное значение частоты на световом цифровом индикаторе. Приближенную оценку частоты тока, питающего преобразователь, можно произвести прибором типа ИЧ-6. Схема измерения резонансной частоты приведена на рис. 4.27, б. Точное значение частоты можно получить и по шкале измерительного генератора при условии, что он использован в качестве задающего генератора источника питания.
Резонансная частота колебательной системы определяется по ее амплитудно-частотной характеристике. Резонансные характеристики целесообразно определять при номинальной мощности преобразователя.
Определение активного, реактивного и полного сопротивлений преобразователя на резонансной частоте осуществляется по формуле
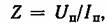
— сила тока и напряжение на преобразователе. Коэффициент мощности

— активная электрическая мощность, потребляемая преобразователем.
Активное сопротивление
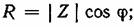
реактивное сопротивление
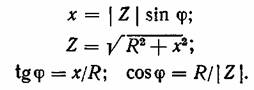
вычисляется по формуле
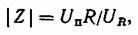
а коэффициент

Угол сдвига фаз между током и напряжением можно определить непосредственно, используя электронные фазометры.
Измерение механических параметров, характеризующих работу механической колебательной системы, предназначенной для сварки, в ряде случаев затруднено. Например, практически трудно напрямую измерить амплитуду смещений сварочного наконечника при сварке пластмасс, поскольку его колебания направлены нормально к плоскости свариваемых деталей.
Основным и наиболее надежным методом определения амплитуды колебаний сварочного наконечника является оптический метод, где измерения производятся посредством микроскопа. Этот метод позволяет достаточно просто определить амплитуду колебаний в любой точке системы, в которой распространяются продольные волны. Микроскоп должен иметь комплект сменной оптики с увеличением в пределах 100—500, осветители, окуляр с сеткой, эталон, по которому определяется цена деления сетки.
Измерение амплитуд колебаний производится следующим образом. При отсутствии колебаний в поле микроскопа замечается произвольная, наиболее характерная риска. После включения ультразвука эта риска вытягивается в линию. Длина этой линии равна удвоенной амплитуде колебательного смещения рассматриваемой точки. Измерения целесообразно производить в непосредственной близости от торца концентратора. Этот метод является единственным, который позволяет произвести градуирование любых других известных средств измерения. Но он имеет свои недостатки. Так, практически в режиме сварки очень трудно измерить амплитуды смещений на уровне 1—2 мкм. Доступ к зоне сварочного наконечника ограничен и т. п.
Измерение амплитуды механических колебаний возможно при условии использования электромеханического преобразователя с помощью специальных схем, позволяющих выделять составляющую тока, питающего преобразователь, величина которой пропорциональна величине механических колебаний электромеханической системы. Например, с этой целью применяется мостовая схема с дифференциальным трансформатором тока (см. рис. 4.18, б).
Забиваем Сайты В ТОП КУВАЛДОЙ - Уникальные возможности от SeoHammer
Каждая ссылка анализируется по трем пакетам оценки: SEO, Трафик и SMM.
SeoHammer делает продвижение сайта прозрачным и простым занятием.
Ссылки, вечные ссылки, статьи, упоминания, пресс-релизы - используйте по максимуму потенциал SeoHammer для продвижения вашего сайта.
Что умеет делать SeoHammer
— Продвижение в один клик, интеллектуальный подбор запросов, покупка самых лучших ссылок с высокой степенью качества у лучших бирж ссылок.
— Регулярная проверка качества ссылок по более чем 100 показателям и ежедневный пересчет показателей качества проекта.
— Все известные форматы ссылок: арендные ссылки, вечные ссылки, публикации (упоминания, мнения, отзывы, статьи, пресс-релизы).
— SeoHammer покажет, где рост или падение, а также запросы, на которые нужно обратить внимание.
SeoHammer еще предоставляет технологию Буст, она ускоряет продвижение в десятки раз,
а первые результаты появляются уже в течение первых 7 дней.
Зарегистрироваться и Начать продвижение
Наиболее приемлемым прибором для измерения колебаний является бесконтактный виброметр типа УБВ-2 с пределами измерений от 0,5 до 100 мкм (диапазон частот 8—40 кГц). Виброметр обеспечивает измерения с точностью ±5 %. Некоторым ограничением применения этих приборов является требование относительно большого диаметра вибрирующей площади (0 6 мм). Для измерения колебательных смещений могут быть использованы индуктивные и емкостные датчики, о чем было сказано выше.
Известны различные устройства для измерения амплитуды смещения сварочного наконечника. Например, в одном из устройств в качестве датчика использован магнитоэлектрический измерительный преобразователь (ИП). Принципиальная электрическая схема его содержит усилитель тока, усилитель напряжения и детектор [20 ].
При испытаниях прибора было установлено, что расхождение между его показаниями и измеренными оптическим методом (с помощью микроскопа МИР-2) не превышает 2 %. Полярный выходной сигнал может быть использован для индикации, а также для управления процессом сварки.
В ГДР разработан оптико-электронный метод измерения амплитуды смещения сварочного наконечника [20].
Как показали результаты экспериментальных работ, погрешность измерений не превышает ±5 %. С использованием точных методов комбинирования точность измерений может быть повышена до ±1,5 %.
Можно отметить преимущества такого метода измерений: способ измерения бесконтактный; практически независим от процесса УЗС; конструкция измерительного преобразователя имеет очень небольшие габаритные размеры и массу; широкий диапазон измерений; место измерений находится в непосредственной близости от зоны сварки; сигнал дает текущее значение амплитуды в процессе сварки; принцип образования сигнала позволяет автоматизировать обработку сигнала и использовать его для управления процессом сварки.
Безусловным недостатком является чрезмерная чувствительность к постороннему свету и необходимость тщательной юстировки при наладке.
В ПНР проведен комплекс работ по созданию измерителя энергии, выделяющейся в зоне сварки и т. п. [20].
Конечной целью всего технологического цикла сварки является получение соединения, отвечающего, в конечном счете, требованиям технических условий на изделие. В зависимости от назначения изделия эти условия могут быть существенно различными. В одном случае требуется получение сварного соединения, обеспечивающего, например, прочность на уровне 0,1 ±0,2 от прочности основного материала, в другом — не менее прочности основного. Вне зависимости от этого одним из основных технических требований к оборудованию для УЗС является обеспечение заданных технологических параметров режима сварки. Кроме того, учитывая особенности процесса формирования сварного соединения, весьма сложный механизм преобразования энергии, элементы физико-механической неоднородности поверхностных слоев свариваемых материалов, получаем необходимость разработки средств управления процессом УЗС и контроля качества сварных соединений, тем более что эти средства упрощают организацию сварочных работ в целом.
В настоящее время известно достаточно много работ, в которых анализируется возможность управления процессом УЗС, разработаны методы аппаратуры, даны рекомендации для их ис-^ пользования в промышленности. Судить о результативности их использования практически нельзя, так как нет статистических данных, которые позволили бы сделать однозначный вывод. Ограничимся краткой систематизацией опубликованного материала.
Для управления процессом УЗС использовались, в основном, амплитуда колебаний сварочного наконечника, программированное сварочное усилие, деформирование свариваемых материалов, коэффициент бегущей волны в системе, кинематические характеристики процесса сварки, энергетика системы в целом, время сварки и др.
Управление процессом УЗС посредством изменения амплитуды колебаний сварочного наконечника проводилось следующими методами, например:
в процессе сварки снижалась амплитуда до 0,25 от исходной;
оценивалась энергетика процесса;

ступенчато снижалась амплитуда сварочного наконечника;
проводилось программированное изменение амплитуды смещения сварочного наконечника в процессе УЗС и т. д.
может дать более существенные результаты.
Известны работы [1, 2] по исследованию возможности управления процессом УЗС посредством программирования сварочного усилия. При этом основная цель работ состояла в выделении явлений пластического течения металла в поверхностных слоях, элементов внешнего трения, регулирования его уровня, кинетики изменений в процессе сварки. Исследования проведены с помощью специально разработанных устройств, позволяющих изменять сварочное усилие в процессе формирования соединения, производить импульсное нагружение с различной частотой. Установлено, что программирование уменьшения сварочного усилия способствует интенсификации образования зон схватывания (алюминий + керамика). Это обусловлено увеличением скорости деформации и коэффициента деформационного упрочнения на активной стадии нагружения, более полным протеканием релаксационных процессов и т. п. В любом случае сварочное усилие при заданной скорости сварочного наконечника формирует в зоне сварки колебательные напряжения и сопротивление нагрузки. Разработка устройств управления колебательными силами и скоростью наконечника предопределит решение проблемы управления процессом УЗС.
Большое внимание было уделено исследованиям возможности управления процессом УЗС металлов и пластмасс посредством регулирования величины деформирования свариваемых материалов— величины осадки [6].
Основные методы управления процессом сварки следующие:
по заданному времени сварки;
при достижении заранее заданной деформации, т. е. с так называемым фиксированным зазором;
при условии записи величины деформации в память, сравнения ее с текущей величиной и достижения заданного значения деформации;
при контроле величины осадки сварочного наконечника по кинетической характеристике процесса УЗС;
по фиксированной деформации, заданной соответствующим профилем контактирующих материалов, например У-образной разделкой кромок;
Сервис онлайн-записи на собственном Telegram-боте
Попробуйте сервис онлайн-записи VisitTime на основе вашего собственного Telegram-бота:
— Разгрузит мастера, специалиста или компанию;
— Позволит гибко управлять расписанием и загрузкой;
— Разошлет оповещения о новых услугах или акциях;
— Позволит принять оплату на карту/кошелек/счет;
— Позволит записываться на групповые и персональные посещения;
— Поможет получить от клиента отзывы о визите к вам;
— Включает в себя сервис чаевых.
Для новых пользователей первый месяц бесплатно.
Зарегистрироваться в сервисе
по изменению знака ускорения деформирования, зоны сварки и т. п.
Все методы управления дают технологический результат, но необходимо сделать три замечания (по п. 2).
Надежность этих методов в значительной мере определяется точностью измерения осадки сварочного наконечника. В частности, есть рекомендации о необходимости измерения ее величины на уровне ±0,01 мм.
Осадка будет различной в зависимости от свойств свариваемых материалов (алюминий—сталь, полистирол—полиэтилен).
Величина осадки не гарантирует необходимой прочности сварных соединений. Ситуации, когда деформация материала есть, а сварки нет, на практике является весьма частым явлением. Это касается сварки пластмасс и металлов.
В любом случае разработка методов управления процессом УЗС посредством выявления закономерностей деформирования свариваемых материалов и создания необходимых комплектов контрольно-измерительной аппаратуры представляется весьма перспективной. Тем более, что деформирование непосредственно отражает процесс энерговыделения в зоне сварки.
Для управления процессом УЗС целесообразно использовать способы, основанные на изменении коэффициента бегущей волны — к$ в колебательной системе. Он рационален прежде всего потому, что несет наиболее объективную информацию о передаче энергии в зону сварки в зависимости от формирующегося сопротивления нагрузки. Известны методы определения энергии, переносимой в зону сварки при условии измерения к$ в нулевой плоскости продольного волновода с соответствующими уравнениями для расчета Рсв ; при наличии специального измерительного звена как составной части продольного волновода [191 и при измерении кб в изгибно-колеблющемся стержне в непосредственной близости от сварочного наконечника [20].
При условии использования колебательных систем, стабильная работа которых обеспечена недостаточно известными средствами:
на высших гармониках в зависимости от механической добротности исходной узкополосной колебательной системы. Показана возможность увеличения полосы пропускания до 8—10 %, или до 8—9 кГц, но при этом потребляемая мощность на границах частотного диапазона возрастает в несколько раз. Электрические методы обеспечивают расширение полосы только в области первой (одной) гармоники механического резонанса.
Для расширения полосы пропускания частот колебательной системы разработан ряд конструктивных решений. Расширение полосы пропускания до 15—20 % от резонансной производилось за счет изменения геометрического размера излучающей стороны пьезопластин по линейному или синусоидальному законам, разнесения резонансных частот и пьезоизлучателей , использования нелинейных электромеханических явлений твердых тел и т. п.
Известны также методы контроля качества сварки и управления процессом сварки по электрическим характеристикам контакта свариваемых материалов. Показано, что величина контактного переходного электросопротивления свариваемых изделий коррелирует с прочностью сварного соединения. Сопротивление при этом измеряют посредством двойного места.
Одним из методов, позволяющих следить за процессом образования сварного соединения, является контроль качества по отраженным эхо-сигналам и плотности шумового спектра. Сущность метода заключается в том, что в зону сварки вводят дополнительные колебания с длиной волны, равной или меньше размера ожидаемого дефекта в сварном соединении, а затем улавливают отражение колебаний от этих дефектов.
Можно осуществлять контроль качества и управления процессом сварки по импедансу зоны сварки посредством бесконтактных электромагнитно-акустических датчиков; системы автоматического поддержания резонанса и амплитуды колебаний САПРА [4] и т. п.
В заключение отметим, что в основе решения проблем стабилизации процесса УЗС пластмасс и металлов лежит правильная оценка дестабилизирующих факторов и энергетики процесса. Использование акустических систем при условии, что изменение колебательных величин носит случайный характер, нерационально. Это приводит к необходимости разработки весьма дорогостоящих средств управления, которые с большим трудом исправляют эту ошибку (использование микропроцессоров, мини-ЭВМ и т. п.).

Оснащение сварочных машин элементами вычислительной техники и средствами управления в целом ряде случаев является избыточным и приводит к снижению экономической эффективности УЗС из-за чрезмерно высокой стоимости оборудования.
|