Практическая вибродиагностика и монтиторингТипичный цикл мониторинга оборудования.
Обычно первый шаг при построении системы вибромониторинга оборудования предприятия состоит в создании компьютерной базы данных по обслуживаемому оборудованию, содержащей детальное описание всех обслуживаемых агрегатов, их измерительных точек, измеряемые параметры для каждой измерительной точки и предварительные предельно допустимые уровни измеряемых параметров (в дальнейшем записи базы данных могут быть расширены, удалены или модифицированы). Затем создаются маршруты обходов оборудования (установок, агрегатов, измерительных точек), по которым будут следовать техники и производить сбор данных по каждой измерительной точке маршрута. Маршрут определяет последовательность сбора данных (какой агрегат, какой его компонент, какая точка и в какой последовательности должны быть обследованы проводящим измерения техником).
Техник со сборщиком данных в соответствии с Регламентом предприятия проводит периодические измерения вибрации и технологических параметров для оценки состояния оборудования, для чего маршрут обхода оборудования предварительно загружается в сборщик данных.
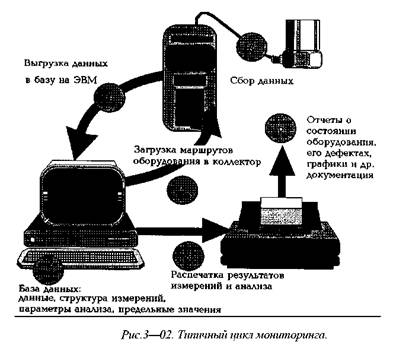
В процессе проведения измерений и обследований на экране сборщика данных индицируются штатные измерительные точки агрегата, на которых необходимо установить датчик для проведения измерений. Обычно на измерение параметров вибрации среднестатистической контрольной точки затрачивается около 5 секунд (на агрегате примерно 10...20 точек и более). Далее, после проведения всех запланированных измерений на маршруте, собранные в сборщике данные "разгружаются" в компьютер для анализа. Опыт показывает, что целесообразно построить работу на маршрутах таким образом, чтобы в течение рабочего дня техник мог охватить измерениями максимальное количество измерительных точек, число которых может составлять от 200 до 600 и более.
Специалист по диагностике, применяя программное обеспечение на компьютере и используя последовательности управляемых с помощью меню операций, производит анализ собранных данных с целью определения (распознавания) состояния обследованных агрегатов. В рамках вибромониторинга возможны два (применяемых в большинстве случаев совместно) метода, при помощи которых производится оценка состояния оборудования:
анализирующее программное обеспечение под управлением специалиста, имеющее встроенные программируемые автоматические модули, в автоматизированном режиме сравнивает текущие уровни контролируемых параметров (вибрации, температуры и др.) с предельными, и, в случае достижения текущим уровнем контролируемого параметра предельного уровня, предупреждает о точках агрегата (агрегатов), параметры которых превышают нормы, принятые в промышленности, или рекомендуемые заводом — изготовителем оборудования, или установленные экспертом по вибродиагностике;
анализирующее программное обеспечение строит тренды параметров и прогнозирует состояние агрегата, автоматически предупреждая о том, на каком оборудовании имеются тенденции к опасному постоянному возрастанию измеряемых параметров; параметры, используемые для оценки состояния оборудования, могут изменяться в соответствии с индивидуальными особенностями конкретного агрегата.
В случае, если требуется проведение виброанализа, инженер, имеющий квалификацию в области вибродиагностики, при помощи программного обеспечения производит анализ измеряемых параметров вибрации (форм сигналов, спектров и др.) оборудования и выдает заключение о возможности дальнейшей его эксплуатации и ТО (кроме того, имеются экспертные программные пакеты, т.н. искусственный интеллект в области вибрации, работающие в автоматизированном режиме и проводящие "черновой" предварительный анализ, что, с одной стороны, экономит время, а с другой — обеспечивает доступ к накопленным знаниям и опыту большинства авторитетных специалистов в виброанализе и позволяет пополнить собственные представления и опыт основами накопленного знания). По данным анализа планируются сроки проведения ТО. Программное обеспечение в автоматическом режиме может генерировать различные формы отчетной документации.
Особый интерес представляют архив и отчеты об истории проведения работ по ТО агрегатов, обнаруженным дефектам, затратам на ремонт и экономии средств. Именно они служат доказательством эффективности ОФС и позволяют расширять применение различных технологий мониторинга на предприятии.
Хотя даже первое измерение обычно позволяет провести оценку состояния агрегата, для построения трендов и прогнозирования изменений параметров вибрации требуется несколько замеров. По мере накопления данных уточняются предельные значения параметров вибрации и повышается вероятность достоверного прогнозирования изменений вибрации агрегата. Обычно первый замер показывает, что 10...40% оборудования нуждается в немедленном техобслуживании.
|