Кузнечно-штамповочное оборудованиеПрессы-автоматы для прессования деталей из металлических порошков
Некоторые детали машин должны обладать настолько специфическими свойствами, что для их изготовления непригодны монолитные металлы. Например, детали должны быть пористыми или содержать компоненты, не образующие сплавов с железом, медью и т. п. В таком случае детали изготовляют из металлических порошков или их смесей (шихты) с другими компонентами на специальных прессах-автоматах.
В зависимости от типа привода различают механические (кривошипные) и гидравлические прессы-автоматы. Механические прессы-автоматы имеют более сложное устройство и довольно дорогие, их выпускают с номинальным усилием до 1,6 МН. Гидравлический привод позволяет упростить конструкцию, но производительность таких прессов-автоматов ниже, чем механических.
Отличительные особенности прессов-автоматов для изготовления деталей из металлических порошков обусловлены свойствами исходной сыпучей заготовки и характером процесса деформации. Так называемый насыпной объем заготовки намного превышает объем детали. Поэтому в процессе деформации заготовку равномерно уплотняют по всему объему до заданной плотности. Для этого в инструменте необходимо предусмотреть независимость движения его отдельных частей - верхних и нижних пуансонов, матрицы, стержня выталкивателя - с использованием соответствующих механизмов.
Отпрессованная из шихты заготовка - это еще не готовая деталь, поскольку сцепление деформированных частиц порошка остается слабым. Поэтому ее подвергают химико-термической обработке - спеканию в специальных печах. В ходе спекания полностью протекают адгезионные процессы и заготовка становится прочной. Однако спекание сопровождается изменением размеров заготовки, и поэтому необходима калибровка спеченной заготовки. Только после этого изготовление детали с требуемыми свойствами и размерами закончено.
Механические прессы-автоматы для прессования металлических порошков выполняют с нижним приводом. Станины прессов сварные, коробчатой формы. Подвижную верхнюю траверсу называют прессующей головкой. Возвратно-поступательное движение головки (при рабочем ходе сверху вниз) осуществляют посредством кривошипно-ползунного механизма подобно тому, как это делают на листоштамповочных прессах-автоматах с нижним приводом (см. рис. 1.11). В системе привода пресса-автомата предусмотрены коробка скоростей (до 6 ступеней) или вариатор для регулирования скорости прессования.
Силу прессования регулируют посредством эталонирования давления воздуха в пневматическом мультипликаторе гидравлического цилиндра (гидроподушки), установленного в прессующей головке. Рабочие части инструмента закреплены на плите плунжера гидравлического цилиндра. Поэтому плунжер при достижении заданного усилия прекращает свое движение, несмотря на продолжающееся перемещение прессующей головки (по аналогии с прижимом в прессе тройного действия для чистовой вырубки, см. § 1.6). Поддержание силы постоянной в течение некоторого времени предохраняет пресс от перегрузок при неправильном ведении технологического процесса, например при излишней засыпке шихты в матрицу.
Механизм для прессования выполняют в виде съемного прессующего блока (рис. 1.30). Верхнюю плиту 1 блока с верхним пуансоном крепят к плунжеру гидравлического цилиндра прессующей головки. Плита 2 матрицы снизу прижата штоками двух цилиндров подпора к регулируемым упорам станины и таким образом зафиксирована в крайнем верхнем положении. Нижняя плита 3 - плита выталкивателя или нижнего пуансона - имеет свой привод от кулачка на главном валу. Как показано на рис. 1.30, во избежание попадания абразивных частиц шихты колонки блока, по которым передвигаются плиты 1 и 3, закрыты телескопическими ограждениями. Снизу плиты 3 расположен шток 4 пневмопривода центрального стержня выталкивателя.
Схематично процесс прессования детали типа втулки показан на рис. 1.31. На стадии а в полость матрицы 4 при помощи автоматического питателя 5 засыпают шихту. Затем следует рабочий ход головки и верхнего пуансона 6. Уплотнение шихты на стадии б начинается у торца пуансона и распространяется по мере его продвижения по высоте засыпки. Однако силы трения ограничивают зону активной деформации и нижняя часть засыпки 3 может оставаться неуплотненной, какую бы большую силу ни развивал верхний пуансон при неподвижной матрице.

Чтобы получить равномерное уплотнение, применяют двустороннее прессование. Для этого матрицу выполняют плавающей, т. е. она может смещаться вниз вместе с плитой (позиция г на рис. 1.31). На стадии в верхний пуансон и матрица перемещаются вниз относительно нижнего пуансона 2, плита которого покоится на неподвижных упорах. В результате такого движения инструмента происходит равномерное уплотнение по всей высоте засыпки. На стадии г верхний пуансон (от прессующей головки), нижний пуансон (от кулачкового механизма) и центральный стержень 1 (от пневмопривода), формирующий внутреннее отверстие втулки, начинают совместное движение вверх, извлекая заготовку из полости матрицы. При этом матрица также поднимается со своей плитой до упоров. Наконец, на стадии д центральный стержень совершает ход вниз, верхний пуансон - вверх до крайнего верхнего положения, а освобожденная
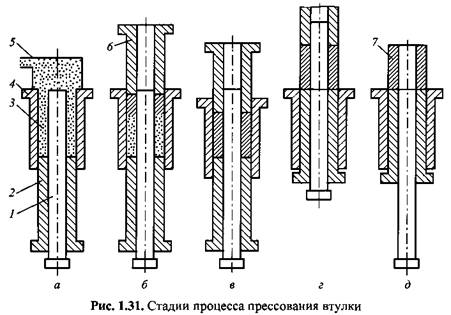
заготовка 7 ходом питателя сталкивается по лотку в тару или на транспортер. После этого нижний пуансон опускается до упора, и все части инструмента занимают исходное положение.
регламентированы ГОСТ 10480.
Конструкция прессов усложняется при усложнении формы и увеличении размеров прессуемых деталей. Например, для изготовления деталей с буртами необходимо иметь два нижних пуансона с независимым приводом. Калибровку спеченных заготовок проводят на прессах-автоматах, подобных автоматам для прессования.
|